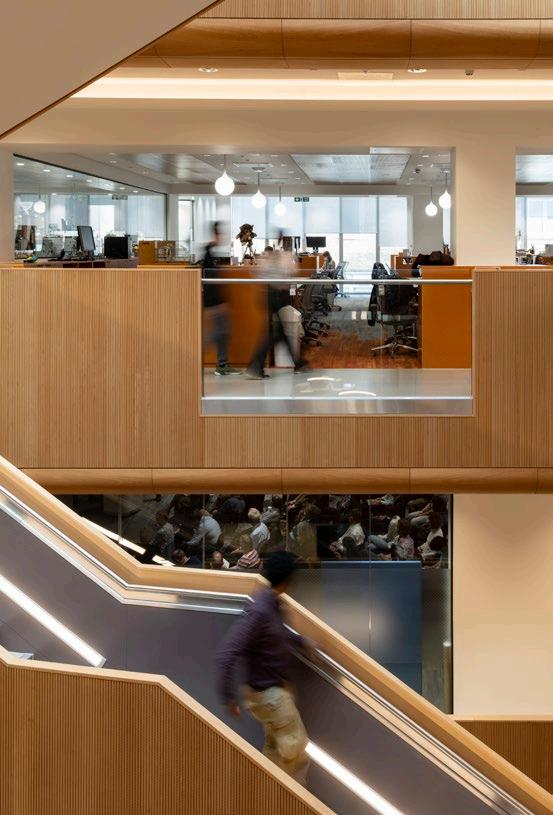
8 minute read
MATERIAL CHOICES
A Whole-life design approach at Hawkins\ Brown
Louisa Bowles was a student at the Mackintosh School of Architecture from 2002-2004. She is now a Partner and Sustainability Lead at Hawkins\Brown. Since joining Hawkins\ Brown in 2004, she has led several complex architectural projects from concept to completion in a range of sectors including education, science, research, commercial and civic. She led the co-funded research with a UCL EngD that resulted in the concept for H\B:ERT, the in-house Whole Life Carbon design tool and subsequently led the launch and ongoing development of the tool. She has worked full time in her sustainability focused role since 2019 and was the AJ 2022 Sustainability Champion and is a Mayor’s Design Advocate.
Advertisement
Hawkins\Brown is an internationally renowned practice of architects, designers and researchers, based in London, Manchester, Edinburgh, Dublin and LA. We work across a range of different sectors and at a variety of different scales from school pavilions to large city-wide infrastructure projects and masterplans. This has meant our approach to sustainable design needs to respond to a range of different clients, context and scales.
However, what unites our range of projects can be filtered down into a simple concept that is flexible enough to apply to all sectors, scales and easy for people with little specific training to explain. Reducing carbon, improving society. This is an evidence-based design approach to ensure our buildings enhance the lives of the future generation.
To embed these principles across the practice Hawkins\ Brown created the Specialist Design Studio to spread best practice expertise from people with all kinds of specialist skills including digital design, BIM, visualisation, technical and delivery skills. Sustainability sits within this group and the power of this is the ability to spread the knowledge, approaches and milestone checkpoints among a greater number of people, so having more impact.
One of the questions we are regularly asked is how did the HB Sustainability team and effort start or evolve. Formal staffing started late 2017 and the size of the team and the range of in-house skills has been gradually increasing. This has been as a result of a number of external stimuli including various industry initiatives, regulation and an awareness that the situation is getting more complex with increasing client, media and planning demands. We believe Architects have a real place in leading this as we are often the Lead Consultant or Designer, so the more we can do in-house the smoother our processes will be.
It’s always good to remind ourselves why we are concerned with sustainable design and specifically carbon emissions and material specifications. Globally, we need to limit the average increase of temperatures to 1.5deg. Nationally we have legal commitments to be Net Zero Carbon by 2050 with a 78% reduction by 2035. If we keep spending our carbon budget to 2050 at the current rate we will run out many years before this. The UKGBC roadmap to Net Zero project indicated the work required and policies required to maintain the reduction trajectory required to meet the 2050 target.
To support, we have standard resources, support networks and data collection processes to track performance. These have evolved and been updated and expanded on numerous occasions to improve them and as new people enter the team. The more we learn on one project the more we can transfer to another within tight programmes.
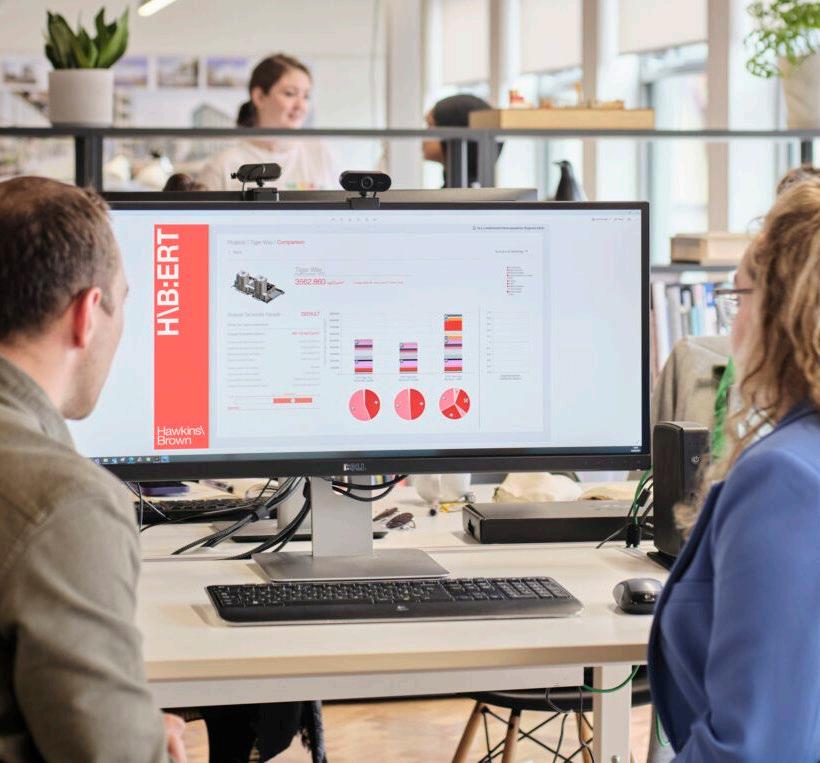
We advocate for Whole Life Carbon to be integrated into the design process where possible. Starting with benchmarking, a rough idea of the aspirations, outline material palette and project abnormals will usually indicate whether it will be possible to meet the most onerous performance or not. We can then optioneer to prove this and track through whole building analysis at key milestones.
We recognize that there are always more drivers than carbon so we often group information on material choices into matrices so carbon, cost, aesthetic, buildability and other factors can be weighted. It is rare there is one perfect answer. And we know from our own analysis and industry benchmarking etc that the structure and facade are often the key indicators of meeting one target over another in regards embodied carbon.
So in regards to structure there are three key material options, concrete, steel and timber or a hybrid of the two. A decision will most likely be made based on function, clear span, material efficiency and hence cost, speed of construction and potentially embodied carbon. However, as you can see here many of our projects expose the chosen material where we can, for joint aesthetic and efficiency reasons. The IStructE guidance has had a huge influence over the recent years and we are seeing more attention to optimization before specification changes, but this is still a key lever to reducing.
In regards facades the situation is more complex as a case study later will show. We have almost infinite finishes and window configurations but also need to adhere to noncombustibility and thermal performance requirements. Broadly there are some rules of thumb we propose to our teams early on as much of the embodied carbon is still in the sub-framing on most buildings at scale. So, reduce the cladding weight, reduce the use of metals. Where you can use recycled products. And in regards the finish itself, review the replacement cycle and really consider how that will be done.
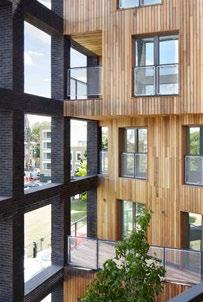
Case Study 1: TEDI CAMPUS
Our first case study looks at re-use, modular construction and design for deconstruction. TEDI-London, is an HE engineering enterprise, cofounded by three global universities: King’s College London, Arizona State University and UNSW Sydney. Phase 1 is now complete at British Land’s Canada Water development, constructed from volumetric modules and is designed to be deconstructed at the end of life for further re-use. Phase 2 has used preloved modular frames.
The deconstruction is a planned for event as the campus will only be here for up to 7 years but effort was also spent ensuring an overall enhancement of the site and student experience. All materials can be stripped off and separated for use elsewhere. Built in the UK, the building itself took just six weeks to construct once the modular components had arrived on the site, minimising disruption to the local area. Each module uses lightweight steel frame boxes clad with insulation and requires no deep piles or concrete.
Case study 2: 55 Great Suffolk Street
This project was featured in the recent RIBA Exhibition; Long Life, Low Energy: Designing for a Circular Economy. The original brief from Fabrix for the refurbishment of 55 Great Suffolk Street included the need for steel re-use and circular economy strategies.

What struck the whole team was how beautiful and raw the original building was so that design concept was always to retain as much material as possible but the means of access was tricky to provide without damaging the existing integrity. What transpired was a weather-protected circulation core that sat outside of the main building volume.
The inspiration for the materilaty of this key addition was the refence to the original warehouse as storage for paper and resulting exploration of pattern generated from
corrugations.
However, it is the steel reuse that has been of primary interest so far on the project due to the current rarity, but increasing interest and need, of this occurring. We have just undergone RIBA Stage 4 including a lot of detailed collaborative work together with Fabrix, Cleveland Steel and our structural engineers Symmetrys. Part of the building has been designed to work with existing steels from another site. This required some reciprocal work up front. Instead of choosing sections from a catalogue, an inspection was taken of what was available. The spec of the steel was generated, a testing regime for the sections deemed most suitable was devised and then the results compared to the spec. Adjustments made where required or alternates found.
Case study 3: Two science and research buildings compared
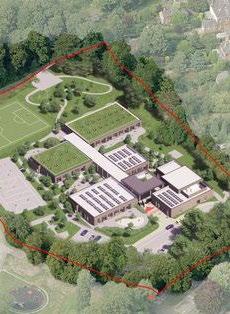
A few quick observations about how all can sometimes not be what it seems with embodied carbon and material choices. We compared two of our recently completed life sciences buildings; IBRB at the University of Warwick and the Dorothy Crowfoot Hodgkin Building for the University of Oxford. The material choices were carefully considered based on the scientific requirements, long term flexibility, construction methodology and health and wellbeing but not in regards embodied carbon per se at the time. Both of these were designed around 2015.
Our thought was that the timber structure used for 50% of the IBRB should have resulted in a figure that reflected a reduction. But in fact the DCHB came out lower. We have attributed this to a few factors including the steeply sloping IBRB site requiring far more piles than in Oxford where the ground conditions enabled a hybrid raft and piled solution. Both concrete structures were pre-fabricated and designed to similar loadings and spans but a higher % of cement replacement used in the DCHB. And the form factor on the DHBC was more efficient as the building is deeper plan with a central toplit atrium. So often factors other than pure material choice massively affect the carbon emissions.
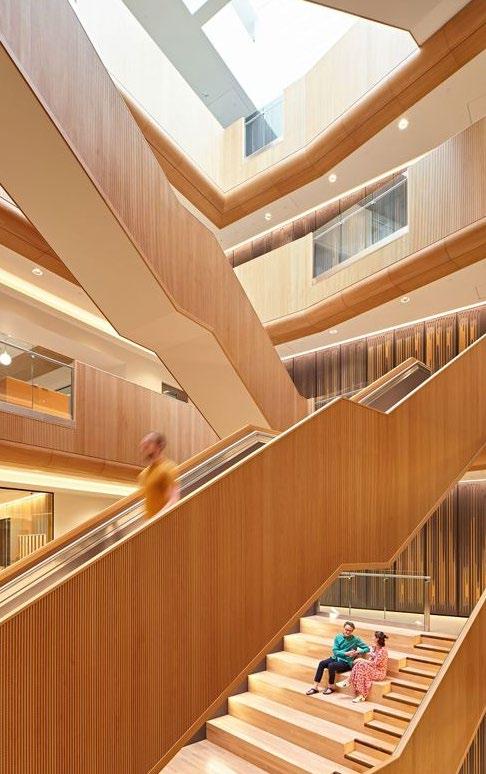
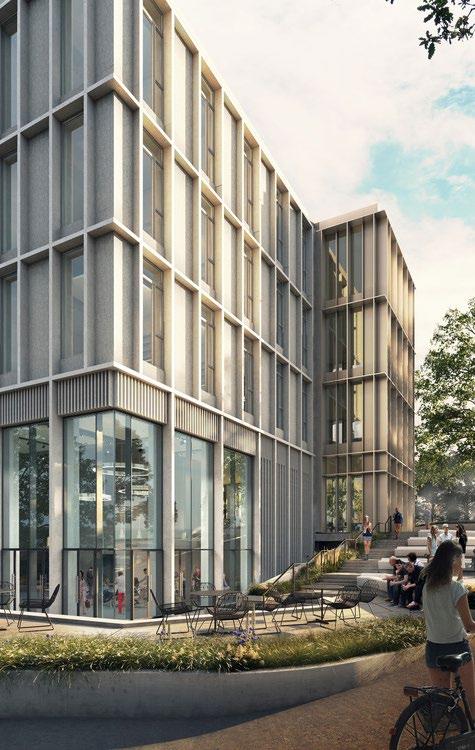
Case study 4: St Mary’ s Catholic Academy
And finally an example of a project that has focused on both embodied and operational carbon from the start. St Mary’s Catholic Academy in Derby is an example of a very low energy, low carbon proposal which we’ve been working on for the Department of Education based on their GenZero principles. The scale has enabled the use of primarily natural materials and modular SIPS panels. Biophilic design is really important here so every wing of the school looks out onto carefully crafted external spaces that create distinct characters through the seasons. Some are functional or productive or educational and some of them are obviously for play.
So the natural materials obviously help as you can see from the embodied carbon figures at around 440kgco2e/ sqm. This principle has been used for the majority of building elements except for the polished concrete floor aimed at ensuring thermal mass while reducing the embodied carbon of sheet floor finishes and short replacement cycles. But the timber is doing more than contributing to a nice number. It is embedded in the principle of providing supportive, calm, healthy learning environments with good air quality, acoustics and connections to external spaces.
So our conclusion - there is no right answer, we must think through our choices at each design stage and life cycle stage through a number of lenses. And we can advocate for Architects as Lead Consultants to take control of each design. Drive through passive design, fabric first and energy efficiency measures. And lead the conversation on materials. While the sub and super-structure is the largest proportion of embodied carbon in a building the Architect is still the curator of the design and has the widest influence over a holistic decision, balancing all factors. It also has to be recognised that there is no perfect answer – the lowest carbon option is not to build at all, but that is unlikely the full answer. So we build less by retrofitting and re-using and we are efficient with material by using the right thing for the right job. One of the focusses of the Environmental Audit Committee which resulted in the recommendation for a national policy on Whole Life Carbon reporting is that there is not much to be gained through demonising specific materials but that all materials need to be used efficiently and decarbonised versions made more available.
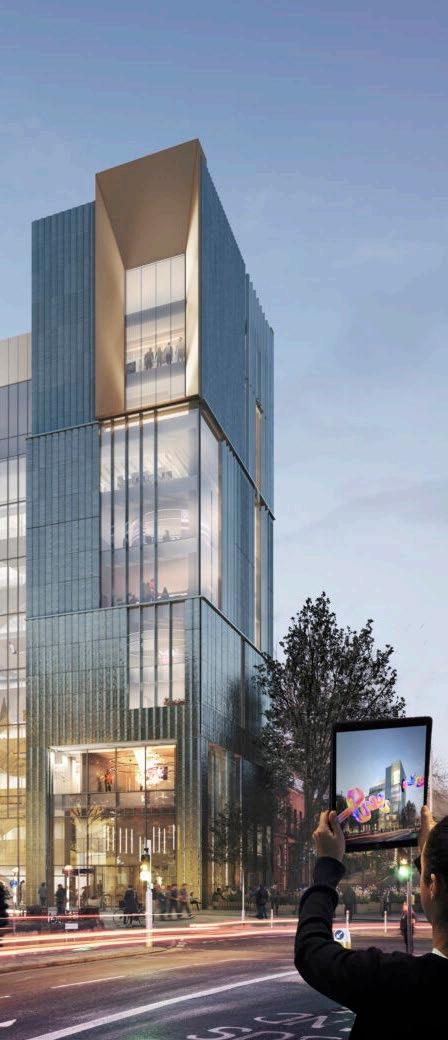