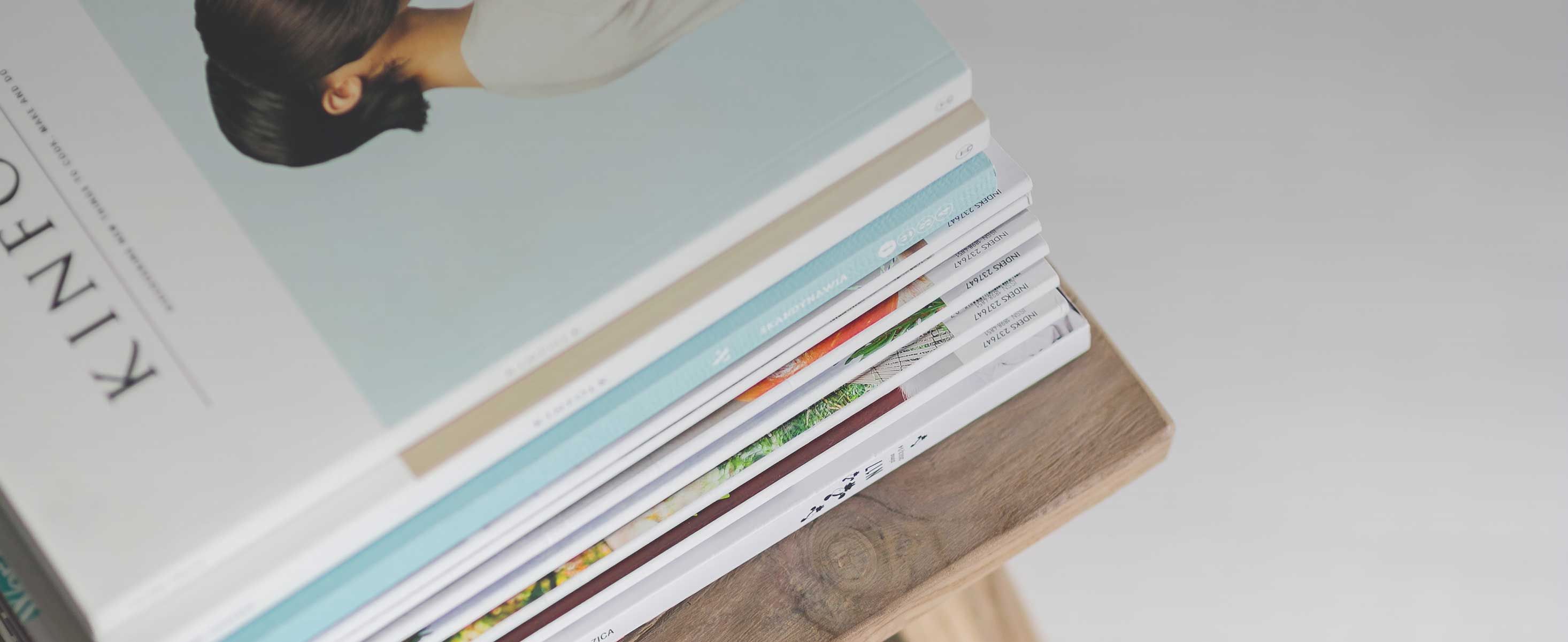
4 minute read
RESHORING AN INCREASINGLY POPULAR OPTION FOR MANY U.S. COMPANIES
as freIght expenses and overseas labor costs rise, it’s become obvious to some corporations that offshoring doesn’t hold the same appeal it once did.
Even as long ago as 2005, economic projections called for reshoring to become a trend worth investigating. Gasoline, for example, was a mere 69 cents per gallon in the 1990s but spiked to $3.50 per gallon in 2019 before settling at $3.19 in August 2021. Consider, too, foreign demand for better wages. In the past, manufacturers could make their products in Mexico for about 25 cents. Today, that cost is closer to $4, while labor costs remain mostly flat throughout the United States.
Now, factor in a global pandemic. Labor and material shortages following the initial shutdown are now resulting in extensive lead times. A full 36% of small businesses say they are experiencing domestic delays – particularly in the manufacturing, construction, and trade sectors, according to a U.S. Census Small Business Pulse survey. Experts do not have pre-pandemic data to compare it to, but believe these levels are considerably higher than in the past.
Those factors have led companies to find that the cost of keeping business in the United States is preferable to overseas transportation and labor costs. The result? A scramble for industrial space within American borders. Industrial vacancy rates remain at an all-time low, despite high levels of investment in new facilities. Industrial developers report twice the level of interest they are accustomed to. Throughout the country, there simply is not enough warehousing space available to meet this spike in demand.
For companies contemplating a move toward reshoring, the considerations are extensive. Minimizing downtime and supply chain disruption is a top priority, and those things can be achieved when you plan in advance. Consider these factors:
ERIC VOYLES eric.voyles@texamericascenter.com
Eric Voyles is the Executive Vice President & Chief Economic Development Officer at TexAmericas Center.
EXISTING OR NEW BUILD?
Determine first whether you would be best served by purchasing an existing building or a new facility designed to suit you. Don’t expect to catch a price break either way. While sky-high steel prices are lending toward more expensive building costs right now, the lack of availability on the market has existing buildings selling at premium prices.
Size Considerations
What is the smallest building you can handle? On the contrary, what is the most amount of space you expect to utilize? Begin your property search by looking for options within those parameters.
Key Amenities
How many dock doors do you need? Which ceiling height? How much acreage? Do you need to be located near rail access? Don’t pay a premium for amenities that simply aren’t useful to your core business needs.
LOCATION, LOCATION, LOCATION
If you have multiple trucks entering and leaving your facility daily, you may need to be within two miles of the interstate. If you don’t ship nearly as much product, you can opt for a less expensive building that’s further away. Just be sure there are 80,000-pound truck routes leading all the way to the interstate.
Once you’ve narrowed down your possibilities of properties, look more closely at your top candidates:
GET THIRD-PARTY VALIDATION ON THE CONDITION OF THE GROUND
If a property is truly development-ready, you can begin construction much sooner. You don’t experience a lengthy delay while the infrastructure, utilities, and transportation requirements are put into place.
Err On The Bigger Side
If you’re debating between two properties and one is a bit tight while the other is a tad large – go big. Factor in your 5 - 10-year growth potential. Once you are already established in your building, you don’t want to be so landlocked that you need to move again. The cost to move machinery and the disruption to production down the line is too high.
Look For Flexibility
Many developers will negotiate with tenants to give them access to additional acreage for several years, with the option to decline or accept that land later.
Consider New Avenues
If you’re a heavy truck user, it might be worth considering a location with rail access so you can eventually make the switch. Trains can carry four times the volume that trucks can, and they can do it for less. The downside is that rail is slower than trucks. Factor in your lead time and whether that’s a reasonable trade-off.
Identify Nearby Social Amenities
Restaurants, hotels, and nightlife might not seem critical to industrial builds, but consider that your employees will want to go out to lunch. Clients will need a place to stay for site visits. Traveling executives will look for evening entertainment after their meetings.
Ultimately, companies find that reshoring gives them stability in the crucial areas of labor costs and logistics. It is a viable, longterm solution for many companies looking to better manage costs while enjoying the benefits of doing business in America. There is value in doing business on U.S. soil. n athens, the CapItal of Greece and the birthplace of democracy, is renowned for some of the world's greatest cultural monuments like the /01/ Parthenon (built on the sacred Acropolis Hill, built in 448 BC on the site of an ancient sanctuary of goddess Athena), the enduring symbol of Ancient Greek beauty. It is one of the few temples that was entirely constructed of marble and the only one with Doric order, the oldest form in Greek architecture. In 1687 AD, the Venetians troops besieged the Turks (who were in the Parthenon) with a bomb that destroyed a great part of the masterpiece. (Parthenon means the apartment of the virgin and Athena was the goddess of wisdom, war and was also a virgin.)
/02/ The Temple of the Olympian Zeus is a half-ruined temple dedicated to Zeus, the chief of the Olympian Gods. Its construction dates to the 6th century and it is very close to other monuments of Athens.
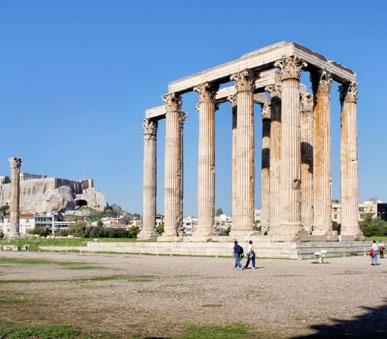