
7 minute read
Toggle Switch
Toggle Switch
HOW THE PENECHAR BROTHERS BECAME THE WIZARDS BEHIND FOUNTAIN CITY GUITARWORKS AND SEÜF GUITARS
By Nick Spacek
When I get to Fountain City Guitarworks’ location in the Squier park neighborhood of Kansas City, I am not quite sure I’m where I’m supposed to be. Located on a quiet residential street between Troost and 71 Highway, the business looks just like another house. I spend a solid minute double-checking things on my phone until I see a man carrying a guitar case confidently walk to the front door and ring the bell. I scurry up behind him and enter the front room.
The entire ground floor of this stately old house is outfitted with a drill press, belt sander, bandsaw, and innumerable hand tools. There’s a faint smell of paint and lacquer mixed with sawdust. After introductions all around, we pull some stools into a corner of the shop, and I sit down with the co-owners of Fountain City Guitarworks, twin brothers Mark and Shaun Penechar. I immediately mention how when that front door opens, it is not what you expect.
“It’s a pretty magical thing,” says Mark. “It’s like walking into Narnia.”
Fountain City is the Penechar brothers’ business, born out of the pair taking over Dave Seüferling’s Seüf Guitars when the luthier retired in 2016. Two years later, they started a new repair business with a third partner, no longer with the company, and the two businesses have been running sideby-side ever since.
“Instead of just being Seüf Guitars, we just married the two, but I always wanted to have a separation between builds and repairs,” Mark says. “That’s born of necessity, but before, Seüf was also the repair shop that you were taking guitars to. Now it’s Fountain City Guitarworks, but we’re still making Seüf guitars because they had an established brand.”
Seüf’s iconic blend of custom creation married with a vintage look has made them very highly regarded in the music world, but Fountain City Guitarworks doesn’t have a specific clientele.
“It’s top to bottom,” says Mark. “All walks. From touring musicians—we just got a bunch of guitars ready for a touring band yesterday—and then a lot of local folks who play six, seven nights a week.”
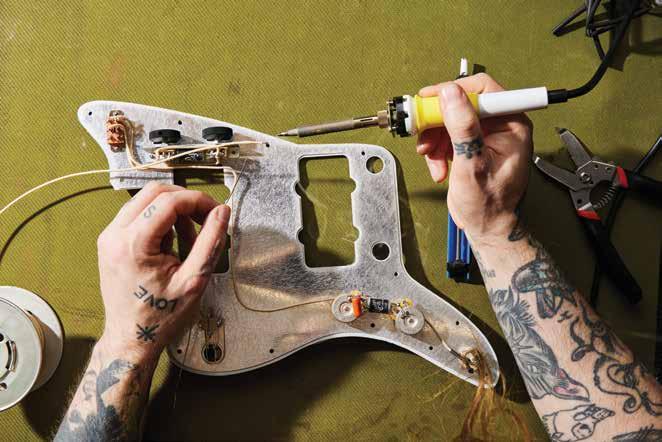
From hobbyists to blues lawyers, Fountain City fixes guitars for everyone: young, old, acoustic, electric, short, and tall, the pair joke. Their Seüf clientele skews the same, although they do mention the fact that they’ve made one for Kevin Morby. Phoebe Bridgers’ bass player plays a Seüf bass, and there’s a guitar sitting by the front door waiting to ship out for a member of Mild High Club.
On the repair side, right now, Mark is working on a restoration of a 1955 Stratocaster for writer Dan Erlewine, whose seminal books like Guitar Player’s Repair Guide, Guitar Finishing Step by Step, and Trade Secrets grace several shelves in the workshop.
“The guy that wrote all the books over there,” says Mark while pointing at the bookcase. “Getting to work for your idol and the fact that he asked? That’s pretty cool. I’m gonna refret the neck, and the neck pickup needs to be rewound. It’s gonna be really fun for me to get to do that, and it’s very rare. We get a lot of vintage adjustments in, but not a lot of second-year Stratocasters.”
It’s an interesting career for two guys who, less than 15 years prior, had no woodworking experience whatsoever. Mark started doing finish sanding at Seüf back in 2011 and, from there, worked his way up to running that shop during the week. Shaun came on in 2014 and started doing the same thing Mark was doing and then worked his way up, as well. The brothers have been playing music since they were 12 and currently do time in the bands Bolinas and Doubledrag, but as to how they came to be making some of the finest custom guitars in the Midwest—that’s a little less direct.
“Well, you have to start off with a crappy pizza job or be a bar back or something like that,” jokes Mark. “Then, you luck into it. And then basically, you learn how to use a router, planers, bandsaws, and all that.”
I took a shop class in middle school, but I don’t remember anything. I might’ve made a birdhouse or something.
“I took a shop class in middle school, but I don’t remember anything,” Shaun says. “I might’ve made a birdhouse or something.”
“I’d never used a drill before I started,” Mark admits, making what the pair and their team do all the more impressive. To go from knowing nothing to building whole-ass, very well-respected guitars in 13 years is mind-boggling. That’s a steep learning curve, but thanks to the pair being in their twenties when they started this, they had the time, energy, and passion to commit themselves to the craft.
“I dropped outta college and had a lot of free time,” Mark says. “School and I didn’t resonate very well, but as soon as I got into it, I was like, ‘Man, I really, really love doing this,’ so I spent all of my nights doing my homework, research, and practice and then finally just gelled.”
It’s paid off for both of them, and their knowledge is apparent when Shaun offers up opinions on the various considerations to be made when selecting wood for their guitars. The big four that Seüf uses are alder, swamp ash, tempered pine, and mahogany.
“The tempered pine’s actually kind of a new thing,” Shaun says. It’s pine that’s kilndried in a vacuum chamber so that you can heat it beyond its smoke point. It basically fossilizes the cell, and it apparently was supposed to sound like old wood. I love working with it. I love the sound of it. It’s fairly unique in its tonal qualities beyond that.”
In the construction of Seüf guitars, the division of labor is fairly stark due to how busy the company gets. It’s clear at the end of our interview when Mark and Shaun show me around the rest of the house. Every square foot is packed with guitars or guitarsin-the-making. There’s a room upstairs with dozens of instruments waiting for repairs and another across the hall with necks and bodies hanging as the paint cures on them. The pair break down just who does what.
“Shaun does stuff that I haven’t done in years, and I do stuff that Shaun hasn’t done in years,” Mark says.
“I’ve never wound a pickup,” Shaun says.
“I make 30 pickups a month,” says Mark. Shaun does most of the woodworking and finishing, along with sanding and painting, and is just generally in charge of the way they look. Mark will be threading necks, making sure fingerboards and necks are straight, along with the wiring—and the aforementioned pickups—with the brothers splitting the final setup and assembly. The Penechars also added two full-time employees on the Fountain City side and one parttime worker who’s currently being trained to help with builds, which has helped the two immensely.
The job does bleed over into the Penechars’ lives outside the shop, despite the pair trying to keep their time within the space at 40 hours a week. As Mark puts it, you don’t go to a dive bar and not run into a musician who needs some work done.
“Everywhere we go, we run into somebody that is a client or a potential client or something,” says Mark. “It’s weird. People come up to me like, ‘You’re that guy!’ and like, I am.”
Fountain City Guitarworks’ Guitar maintenance Advice
• Change your strings more often. “You gotta change your strings more often than you do, everybody,” the pair immediately tell me.
• Clean your frets. “When you change your strings, it’ll make your strings last longer,” Shaun advises.
• Humidify in winter. Low humidity can result in cracks in the body or the bridge lifting and/or totally separating.