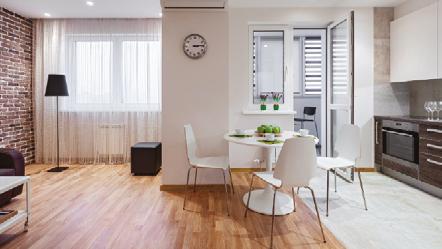
4 minute read
LVT Options
Flooring factsheet
Vinyl Flooring
Vinyl is a fast growing sector of the flooring market due to its durability at relatively low cost and huge range of designs
available. Sheet vinyl and cushion floor by the roll are popular but the sector is dominated by LVT. In reality, most of the products sold today are “LVP”, Luxury Vinyl Planks, as wood decors are more popular than ceramics and stone but the term LVT is still used to cover the whole non-sheet market.
Benefits
•Huge choice in terms of decors across wood, ceramic, stone and geometric designs • Impressive realism – not just in the design but infinishing techniques that allow for wood knots you can feel, tiles you can grout, etc. See appearance options. • Excellent performance in durability for high traffic areas, scratch resistance and cleanability. Vinyl also tends to be much more nonslip than natural materials. Some products are water resistant for bathrooms and kitchens. • Warm and soft to touch compared to ceramic and stone floors - and a good heat insulator anyhow, and suitable for use with underfloor heating systems. • Sound reduction – vinyl has neglible impact sound compared to the tap/click of laminate and transmits less sound and vibration compared to solid floor. • Considerably cheaper than the ‘real’ thing – both to buy and to fit – and tile/plank approach minimises wastage. Installation
Installation preparation
Vinyl requires a dry, sound, level subfloor as the relative thinness of vinyl and its light reflection performance will quickly reveal imperfections after installation as well as cause potential wear issues. Exisitng wooden/MDF floors may need a plywood underlay up to 6mm thick and then the joints will need to be skimmed or taped. Non-wood sub-floors will need a self-levelling screed to be laid to ensure a suitable base for the floor. A damp-proof membrane may be required depending on sub-floor moisture levels. However, new rigid core products are less flexible and can be laid more easily over existing floors – see Construction.
Product options
•Dry back – a sheet or tile that needs to be fixed to the sub-floor using an adhesive. • Self-adhesive – tiles with a peel-off backing paper to stick to the sub-floor. Some tiles have adhesive overlaps to stick to each other rather than the sub-floor. • Loose lay vinyl – tiles that simply drop onto the floor and rely on a high friction backing to keep them in place – they demand a very sound, level sub-floor but are the easiset type of tile to lay or replace. • Click – tiles that have a mechanical jointing system to attach to one another (like a locked tongue and groove system) and ‘float’ on the sub-floor without being glued down. There are many proprietary versions of the click system which offer fast, clean installation and stability.
Appearance options
Vinyl tiles and planks cover a hugh variety of sizes and shapes and can be mix-and-matched to achieve an infinite number of designs. Current fashions include extra wide and long planks for wood through to very small planks for wood. Border effects can be easy to achieve in LVT. Other notable options include: • Embossed – this is where the top clear layer of the tile has been embossed to create a realistic texture that matches the style of the stone of wood decor. Registered embossed is the most authentic – the texture matches the design so that, for example, a wood knot or hand-scraped element in the wood design can be felt on the surface of the flooring. • Grouting and grooving – vinyl tiles can be laid with grouting inlay strips or beads of vinyl for addewd realism – and there are acrylic grouts that can be applied. In wood decors, planks are available with v-grooves or bevelled edges between planks for added realism.
www.bramptonchase.co.uk
www.invictus.co.uk
www.karndean.com
www.myvictoria.co.uk
PVC Middle Layer(s)
Fibre Glass Layer(s) Top Coating
Wear Layer
Decor Layer
LVT construction
Top coating – A polyurethane or aluminium oxide coating provides protection against scratches and stains and gives enhances anti-slip.
Wear layer – This is a key layer - determining the performance and resilience of the product. A 0.3mm (12 mil) wear layer is a good for heavy wear areas. Commercial installations need 0.5mm wear layers or above with 0.7mm at the top end. The wear warranties and guarantees carried by products will be based on this thickness.
Decor layer – This is the decor itself - in essence it is a paper- or filmbased photographic inkjet print. (A few LVT floors have the image printed directly to the surface of the floor but this implies less image definition and different wear characteristics.) PVC and fibre glass layers – The construction ‘sandwich’ can vary between products but a combination of PVC (polyvinyl chloride) layers for strength and flexibility and fibre glass layers for structural stability may be used. Any click-system profile will be incorporated into these layers. Products often use a combination of recycled vinyl which is cheaper and virgin PVC which lasts longer and is more stable.
Rigid core LVT has a solid, less flexible PVC layer with maximum stability which means it can be laid over exisiting, less even flooring without showing imperfections and therefore avoiding wear problems. Base (or backing) layer – The final high density PVC layer varies according to the installation requirement and is designed for taking adhesive or as an ‘underlay’ for loose-lay and click installations.