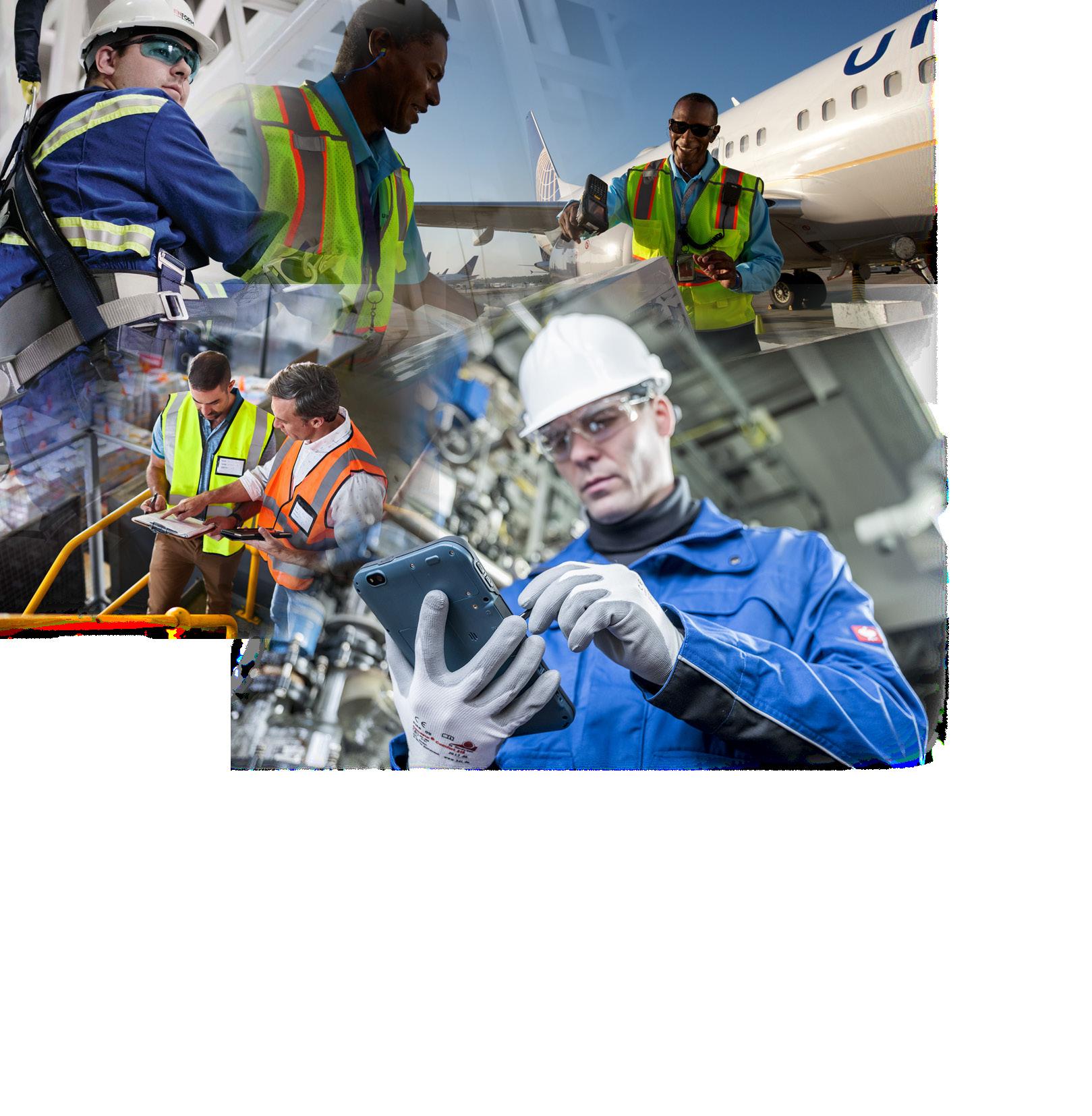
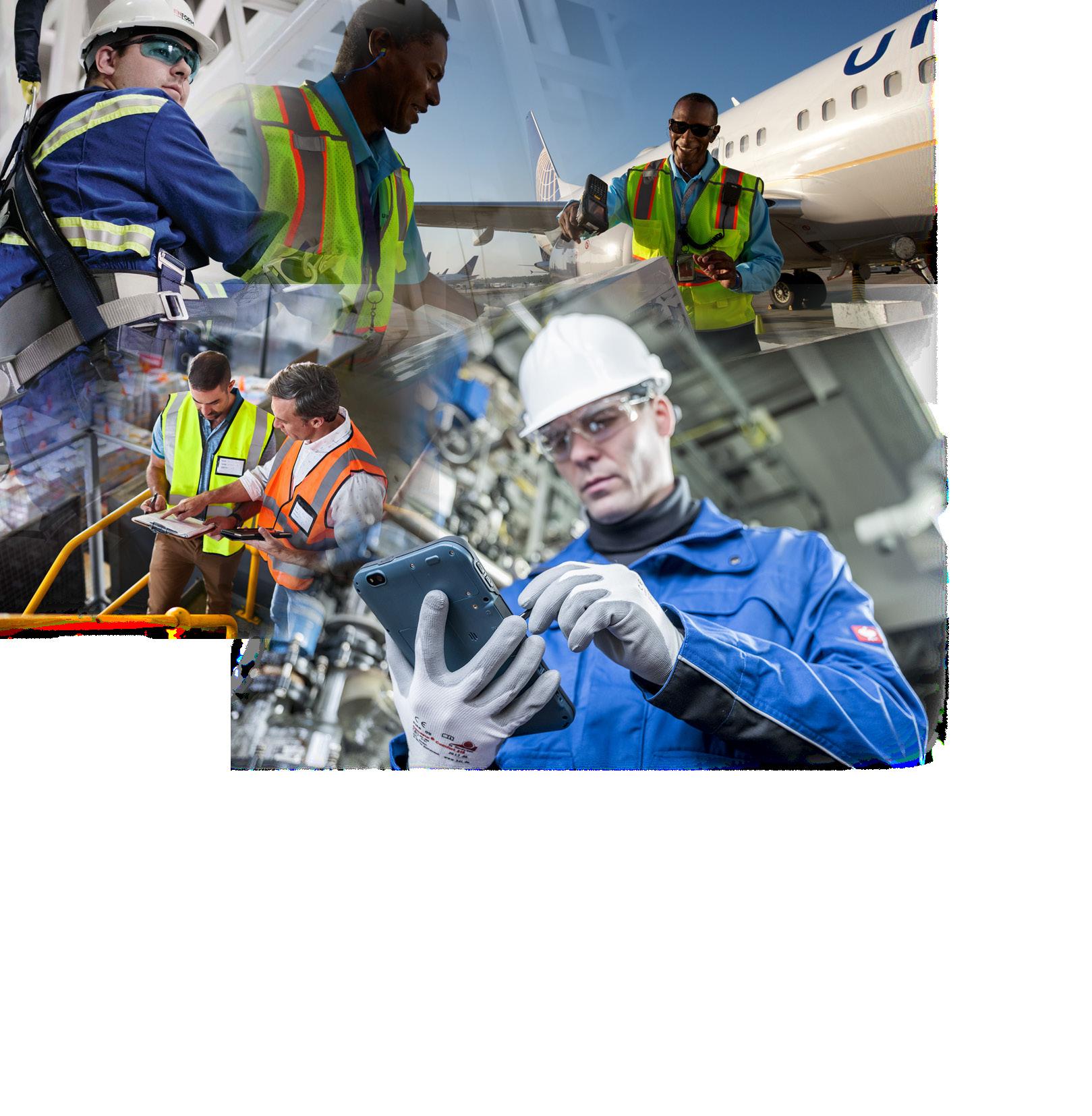
How good is your Safety performance at the workplace?
Is your HSEQ performance cycle complete, or you are missing some steps? Read more, give answer to a few questions, and find out if you and your company are on the right way!
It is crucial for any organization to have a transparent process that everyone in the organization can recognize and can navigate through the HSEQ cycle so that the desired effect is truly achieved.
Steps required for optimal HSEQ performance cycle are:
1. Inform
2. Observe
3. Discuss
4. Implement
5. Evaluate
By going through and repeating the entire process, sustainable behavior changes and lasting increases in knowledge can be achieved, resulting in a safer workplace and a Safety Culture where communication among individuals is fostered to enhance and maintain the safety and health of employees in the workplace.
The Significance of Workplace Safety Awareness*
Workplace safety awareness refers to the collective consciousness and understanding of potential hazards and safety protocols within a work setting. It empowers employees to identify, mitigate, and report risks, thereby creating an environment that prioritizes their welfare. A solid safety culture contributes to reduced accidents, fewer workplace injuries, and increased employee morale.
SOURCE: * Occupational Safety and Health Administration (OSHA). (2021). "Why Safety and Health is Important."
5. evaluate
1. inform
cyclE/ proceSs communicating > m a iger>egdelwonkniatni s tering >
4. implement
2. observe
3. discuss
LEMACORE method (Learning, Maintaining, Communicating, Registering) underline the significance of not avoiding any of the abovementioned steps if your company aims for optimal HSEQ performance.
Curious to discover how good is your Safety Performance at the workplace?
Answer all these questions truthfully and honestly to gain realistic insight of your situation. Download this pdf so you can tick the box of your choice. Good luck!
1. INFORM
Do you and/or your colleagues always have access to simple, to-the-point, essential HSEQ information?
YES SOMETIMES NO
2. OBSERVE
Does your company have a practical ‘workplace hazards identification & removal’ process in place?
3. DISCUSS
Does your company facilitate and encourage discussing the observed issues?
INFORMATION SOURCES:
Occupational Safety and Health Administration (OSHA). (2021). "Why Safety and Health is Important." Canadian Centre for Occupational Health and Safety. (2021). "The Benefits of Workplace Safety." Safety Science. ”Training for Safety: The Role of Repetition in a High-Risk Industry.”
4. IMPLEMENT
Does your company proceed with implementation of the solutions as discussed and agreed?
YES
SOMETIMES NO
5. EVALUATE
Are evaluation and feedback a standard procedure in your company?
YES
SOMETIMES NO
Now that you have checked all the boxes, you can see if your company is on the right way to create and maintain a safer and healthier workplace. If one (or more answers) is NO, it creates a gap in efficient CYCLE/PROCESS and can result in increased risk of incidents/accidents.
On the other hand, if you answered YES to majority of the questions, your company is on the right way to achieve Operational Excellence. Still, that doesn’t mean that certain areas can’t be improved. With the right tools & services your company can further optimize the efforts and continuously improve the way you work.
Improve your company’s Safety Performance, promote a strong Safety Culture and reduce substantially your HSEQ spending resulting in less incidents!
Would you like to find out more?
Read our brief INTRODUCTION or TOOLS & SERVICES presentation.