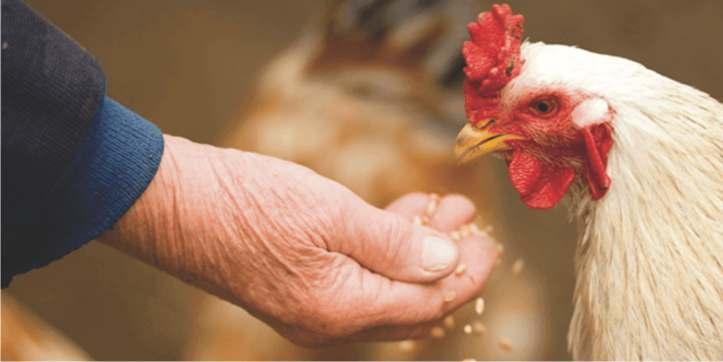
15 minute read
Modifying Performance in poultry through Enzymes when used alternative raw materials in feed
Dr. Milind D. Rainchwar, Novus Animal Nutrition India
Dr. Milind D. Rainchwar
Advertisement
With the advent and modifications in poultry genetics, varied strains are being produced to yield optimum performance in terms of Body weight, FCR, EEF, Egg production, Uniformity, Reduction in mortality, etc. Genetic potential is an inherent property of a bird that has undergone huge changes over the past few decades. The genetics is closely associated with the nutrition being provided to the birds during their lifetime to achieve optimum performance and exploit the genetic potential. The thumb rule is that the phenotype (physical expression-performance) of birds is determined by a combination of its genotype (Genetics) and environment (Nutrition, Management, etc.). Provided the genotype is being taken care of by Breeding companies, utmost emphasis should be placed on the type of nutrition to be provided to achieve the required target performance of birds. Feed is an important and expensive input that contributes almost 70-75 percent of total cost of production. Like the famous notion of-GARBAGE IN=GARBAGE OUT, the raw material quality indicates directly the quality of finished feed being produced, of course considering other parameters such as feed milling, etc. Hence, the quality of raw materials should be given due emphasis to produce an optimal feed to achieve target performance.
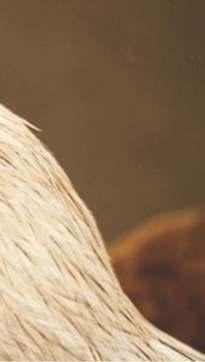
Feed is perfect balanced combination of energy, protein, fat, minerals, vitamins, different feed additives and supplements that help to optimize performance potential of bird through feed under standard management conditions. A good quality feed coupled with optimal environment and disease management plays a major role in influencing bird's performance. List of factors responsible for good quality feed production includes-
Purchase of Feed
Ingredients/Raw materials
Quality control of feed ingredients/Raw materials
Storage of raw materials
Feed formulation
Processing of Raw materials
Batching
Grinding
Mixing
Quality control of
Finished Feed
Feed mill Maintenance
Energy Sources
Energy sources accounts for the major proportion of feed and amounts almost 35-45% of overall feed cost. The sources of energy in poultry diet being the carbohydrates and fat/oil portion, due emphasis needs to be placed on these ingredients when procured. The source of carbohydrates comprises of grains while fat/oil sources comprises of vegetable oils and animal fat/oils. Maize is the prime source of energy used by many poultry farmers and feed millers. Owing to its better digestibility, easy availability and higher metabolizable Energy (AME) maize still ranks first choice (though it is on lose competition with Broken rice and Bajra) amongst the various available grain sources. We witness in general the use of other grain sources mainly Bajra, broken rice and Wheat when the prices of Maize gone high and supply is limited. At the same time, these raw materials are used abundantly due to price impact in the areas where harvesting of these crops is more. Apart from these grains, some by-products of these are also used as moderate source of energy like Rice Polish, etc.
Fats and Oils as Energy Sources
Crude Vegetable oils of Soybean and Rice Bran are widely used as an energy source from oils. While using these as Energy sources, utmost care to be considered for their purity in terms of presence of less contaminants, which would otherwise drastically reduce energy availability from respective oil. Fish oil serves as a good source of energy provided extra precautions are taken for its handling as well the oil is prone for oxidation if stored for long duration. So, enough quantity of antioxidant is required to control Free fatty acids level. Animal fats such as tallow should be avoided in poultry diets due to their poor digestibility. It can be included to certain extent in finisher diet if it is of supreme quality.
Protein Sources
In the major raw materials used for poultry feed production, protein sources contribute almost 45-55% of total feed cost. In current scenario, it may go even higher as the Protein sources prices are gone record high. So, keeping in view of this, strict quality control measures with
respect to procurement and management of protein sources of raw materials is utmost important. Till date, Soybean meal is by far the best and widely used source of protein in poultry feed. This is then followed by other protein sources like Meat and Bone Meal, Groundnut cake, Rapeseed meal, Mustard De oiled cake, Full Fat Soybean, Maize Gluten meal, Rice Gluten, Dried Distiller Grain Solubles (DDGS), Poultry By-Product meal, Sunflower meal, Guar Korma, Cotton Seed meal, Blood meal, Fish Meal, etc. Protein sources must be procured from reliable sources. Vendor/Supplier establishment is a crucial step to document required ingredient specification. Regular vendor reviews need to be carried out to have strict vigilance on incoming raw material quality. Physical, chemical and microbiological quality control measures for protein sources need to be adopted depending on the type of raw material. As far as possible, 50% of the total incoming lot must be sampled for the various quality control tests. Physical tests such as odor, colour, texture, presence of insects, pests, etc. need to carry out as soon as material is received at the plant/farm. For other tests, in house lab set up is always a best option. If not, laboratory providing these testing solutions should be identified to get the clear picture of the raw material quality.
Antinutritional Factors in Ingredient Sources
Antinutritional factors (ANF) are hard to analyse. But we can have an idea of their presence in various ingredients and decide on their inclusion levels. Non-Starch polysaccharides (NSP) and phytates are present in all grains, which entrap essential nutrients thereby reducing bioavailability. NSPs are also present in all protein sources including soybean. To address these issues, an optimal combination of good quality NSP enzyme, Phytase and Protease enzyme is very much essential to explore the potential of raw material and to improve digestibility and thus, bioavailability. Table 2 showing commonly endogenous toxic materials/ Antinutritional factors in different protein sources.
Role of Enzymes to Encounter Antinutritional Factors and improve Performance
Enzymes acts like catalysts and helps to improve the digestibility and Bioavailability of raw materials and Nutrients and thus, helps to improve performance of Birds. In fact, Enzymes are probably the only ingredient in feed formulation which when added, reduces the feed cost
Table 1. Protein Sources and their inclusions in general in Poultry Feed Protein Source Max Inclusion % in Feed Practiced in General for Poultry Diets
Soybean Meal
40 Groundnut Cake 10 Rapeseed Meal DDGS 3-5 5-15
Rice Gluten 3-10
Mustard Cake
3-5 Cotton Seed DOC 3-5 Guar Korma Sunflower Meal 2-4 3-8 Maize Gluten Meal 2-5 Full Fat Soya 2-8 Meat and Bone Meal 2-5 Poultry By-product Meal 1-2.5 Fish Meal 2-8 Blood meal 1-3 Shrimp Head Meal 2-4
(Source: Brazillian Tables, Commercial Poultry Nutrition)
when considered its matrix in a better way. Common enzymes used in feed formulations are broadly categorized in three groups- NSPase, Protease and Phytases. While general consideration is that, NSPase will help to reduce the impact of NSPs present in the feed and thus, helps to release energy which is otherwise not available for Absorption. Carbohydrates are added in the feed as a source of energy but it's not completely absorbed as certain amount is non or less digestible due to presence of less digestible Carbohydrates which are otherwise called NSPs. To counter that, NSPase are added which then effectively neutralize their impact and release certain amount of energy which is made available to birds. Good quality Enzymes can release almost 2-4% of Energy from the ration. Commonly used NSP enzymes includes Xylanase, B Glucanase, Amylase, Cellulase, etc. Protein inclusion cost is the second highest cost in the feed after Energy (includes Carbohydrates and Oil). Soya DOC is conventionally the most used protein source used in poultry diets because of its better protein digestibility and better amino acid profile than others. Ideally its digestibility is in the range of 84-91%. But it has many antinutritional factors such as Trypsin inhibitor, Glycinin, B conglycinin and Lectins. Many of these are allergens proteins and can cause digestive disturbance. Trypsin plays major role in protein digestion but due to Trypsin inhibitor protein digestion gets hampered resulting more
Table 2. Commonly endogenous toxic materials/ Antinutritional factors in different protein sources Feedstuffs Antinutritional Factors
Soybean and its meal Trypsin inhibitor, phytohaemagglutinins, Lipoxygenase, Goitrogen, Saponins, Oligosaccharides. Groundnut and Its meal Trypsin inhibitor, Goitrogen, Tannins, Oligosaccharides and Lectins. Mustard and its meal Goitorgens (Thioglucosides or Glucosinolates), Tannic acid, Erucic Acid, Sinapine, pectins and oligosaccharides. Sunflower seed and its meal Chlorogenic, Quinic Acid and Fibre (Tannin Like Compounds) Cotton Seed and its meals Gossypol (Phenol like compound), cyclopropenoid fatty acids, Tannins.
Fish meal Gizzerosine and Histamine ( Biogenic Amines).
consideration of its matrix, helps to reduce the feed cost as well. Due to current situation, many poultry farmers have shifted to alternative/nonconventional protein sources such as Rapeseed meal, Mustard DOC, Groundnut cake, Meat and Bone meal, Poultry meal, Guar Meal, Maize Gluten meal, cotton seed DOC, etc. There is huge variation in digestibility of protein and amino acids of these sources when added in the diet even though crude protein is higher or equally matching. In other way,
undigestible protein available as a food for bad pathogens in hind gut bacteria. Protease can be effective in managing these problems and reduce the antinutritional factors in Soya DOC. Research has shown that addition of mono component protease enzyme in the poultry diet can help to reduce Glycinin and B conglycinin by more than 90 percent while it helps to neutralize Trypsin Inhibitor in the Soya DOC as well making it more bioavailable. Effective use of protease not only help to improve the digestibility of Soya DOC but
more undigestible amino acid is available at post absorption site which is a food for pathogens. This undigestible portion is a substrate for Protease enzyme and it acts on that portion to make it more digestible at the site of absorption. This results in lesser undigested amino acids resulting in better performance of birds. Hence, use of Protease enzyme become critical. Use of mono component protease enzyme can be more effective comparatively and it can be helpful to consider higher matrix basis the feed formulation and substrate available in the formulation. So in present scenario, use of mono component Protease enzyme can prove beneficial to reduce feed cost by approximate Rs 1500-2000 per ton feed depending on raw material sources and feed formulation in Broilers. Below is the sample formulation for broilers showing the Cost Benefit of protease enzyme (as per current scenario).
Conclusion
Feed contributes almost 70% of poultry production cost. Due to sharp rise in raw materials particularly protein sources, it is imperative to use alternate sources which are available, but they have their own issues when used without proper knowledge as they contain antinutritional factors which damage the performance if not considered during formulation. Also, the inclusion levels matter most for many reasons. Enzyme play critical role in maintaining the performance by reducing feed cost. Ideal selection of Good enzymes not only reduces the feed cost but also improves production cost as well. Protease enzyme when used in the diet containing alternate protein sources can be very much helpful. It enhances the protein digestibility, supports bird's performance and reduces feed cost. Its inclusion in the diet improves digestion of protein in feed ingredients, thereby allowing lower protein inclusion of total protein when formulating diets. Also, it helps to neutralize antinutritional factors. Effective use of Protease can help to reduce feed cost from Rs 15002000 per ton Feed with current raw material prices in Broiler Diets while in layers it can be significant savings up to Rs 1000-1500 Per MT Feed. In Breeders, when used, Significant difference in hatchability improvement can be observed provided formulation is balanced.
Table 3. Value Proposition of Mono Component Protease enzyme in broilers Prestarter Starter
Finisher Ingredients Control Mono Component Mono Component Mono Component Protease Enzyme Control Protease Enzyme Control Protease Enzyme
Maize 583.69 613.74 605.74 636.21 643.46 673.93
Soya DOC 46% 340.84 316.96 MBM 45% 25.00 25.00
Blend Oil
17.56 10.55 Limestone Powder 8.75 8.82 Feed Additives 24.00 24.00 310.59 286.11 32.13 32.64 27.69 20.54 7.50 7.53 18.00 18.00 269.38 244.91 27.70 28.22 37.08 29.93 7.51 7.54 16.00 16.00
Mono Component Protease Enzyme - Added Added - Added
Formula Cost (INR) 40,587.82 38,750.85 40,142.63 38,281.59 38,598.97 36,737.92 Cost Savings (INR) 1,836.97 1,861.04 1,861.05
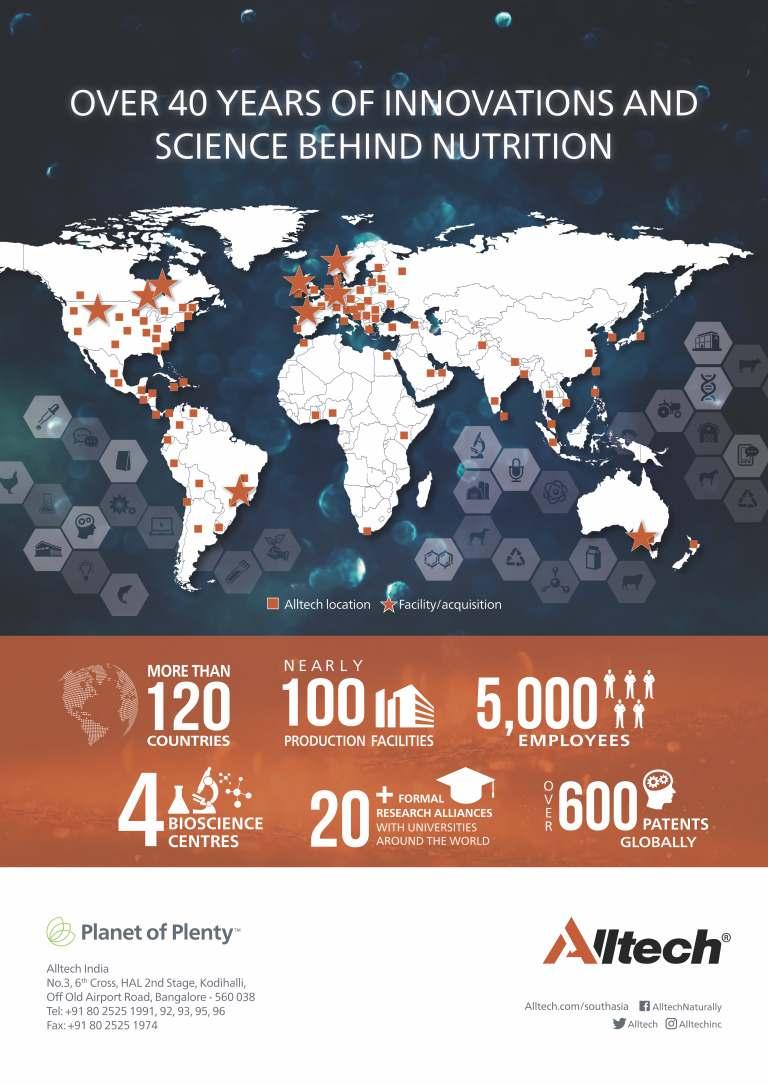
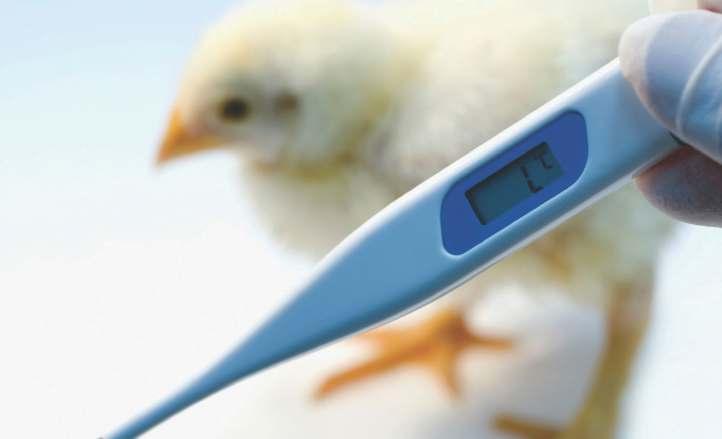
Why we need a comprehensive strategy for heat stress management?
Dr. Rahul Mittal and Dr. Chandrasekar S, Kemin Industries
Temperature and humidity play a critical role in poultry production. Often, in tropical countries like India and Bangladesh, the temperature regularly reaches upwards of 40⁰C which is unfavorable for profitable poultry production. Heat stress is a negative balance between the net energy flowing from animal's body to surroundings and net energy (heat) produced by the bird (Lucas J. Lara, animals, 2013). Heat stress is one of the most important stressors challenging poultry industry. The negative effects of heat stress lead to reduced growth, reduced egg production and makes birds prone to viral challenges. It is manifested in birds' behavioral changes, hormonal changes, and immunological changes. Understanding the complex heat stress problem is crucial to control and manage profitable poultry production.
Heat stress is a complex problem
Modern poultry seems to be more prone to negative impacts of heat stress as there's a higher amount of metabolic activity. There are many changes that may occur when bird is constantly exposed to temperatures above 27⁰C i.e. above the comfort zone
Behavioral changes in birds
To maintain homeostasis, birds tend to reduce body temperature by
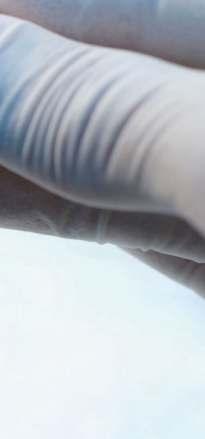
manifesting peculiar behavioral signs like reduced feed intake, drinking more water, increased panting, wings raised up and minimum movement with more time spent on resting. While panting is an efficient way for thermoregulation but increased panting leads to respiratory alkalosis which lead to increased CO2 levels and high blood pH which subsequently hinders bicarbonate availability and reduced calcium in blood for eggshell mineralization in layer and breeder birds.
Physiological changes
Increased plasma corticosterone due to neuroendocrinal
Physiological Changes Ÿ Hyperglycemia Ÿ Immunosuppression Ÿ Respiratory Alkalosis
Ÿ Reduced ADG Ÿ Reduced egg production Ÿ Increased mortality
Reduced Profitability Complex Heat Stress
Behavioral Changes Ÿ Reduced feed intake Ÿ Increased panting Ÿ Raised wings
changes may lead to multiple effects like hyperglycemia and immunosuppression which ultimately lead to lower feed intake and increasedvulnerability to viral challenges. Multiple studies have shown immunosuppressing effect of heat stress on broiler, laying hens and breeder birds. Lower weight of thymus and spleen, lower levels of antibodies IgG and IgM are common findings in heat stressed birds (Aengwanich, J. Vet. Sci. 2008). Under chronic heat stress, bird's body tend to show increase in levels of reactive oxygen species (ROS) which leads to oxidative stress and further damage the production possibilities. (Droge, W, Physiol., 2002) Dehydration and electrolyte imbalance: There's a high amount of water and electrolyte (Na+ , K+ , Cl- ) loss in heat stressed birds. Decreased cell permeability and reduced ATP synthesis leads to cellular apoptosis.
Impact of heat stress on profitability
Multiple studies have shown the negative impact of heat stress on birds like reduced feed intake, reduced average daily gain, decrease in egg production, and increase in egg abnormalities. In one of the studies by Farnell, M.B.et al, 2001 showed that chronic heat stress may bring egg production down by 50%. In another study, Warriss et al demonstrated an increase in mortality rate by 3 times while N. R. StPierre et al, 1999 showed a drop of >50% in average daily gain and concluded that heat stress can cause up to 15% of total economic loss in poultry annually. A loss of 11 lakh is incurred if there is a drop in production of 5% for a 1 lakh bird layer farm (assuming age between 20 weeks to 32 weeks).
Comprehensive strategy to minimize losses in summer
Drop in feed intake, dehydration, and immunosuppression due to summer stress hits directly to the bottom line of farmer. To minimize these losses, a comprehensive strategy is required.
Farm management:
general summer management practices to reduce average temperature inside shed like using foggers, white lime paint, curtains, insulating the shed roof and water tank will provide cooling effect.
Providing proper ventilation is crucial.
Water management:
water is the most important nutrient. Birds consume 4 times more water at temperatures above 37⁰C. Maintain regular supply of cool and fresh water with additional water acidifiers and sanitizers.
Nutrition
Management: right nutritional changes for summer is paramount to tackle heat stress problem. Based on the geographical location and intensity of heat, common practices like m Optimizing energy levels through inclusion of fats.
The feed passage time decreases with additional fat diet, this will help in improving availability of nutrients for absorption. m There are many advantages of additional fats in summer like increased palatability to improve feed intake, provides a cooling effect to bird, improves egg weight and shell strength. m High protein content during heat stress will increase heat load.
Supplementing optimal protein quantity and improved amino acid balance is critical. This will help to reduce wastage and heat load due to nitrogen excretion and improved digestibility
Vitamins: Vitamin C plays a critical role in reducing body temperature, reduce corticosterone levels and works as an excellent antioxidant to reduce oxidative stress.
Vitamin C also improves immunity and reduces mortality in growing birds infected with IBD (G D Butcher and R D miles, 2011). Vitamin E is also used as an antioxidant and booster for immunity, Vitamin A and Vitamin D3 are also required in additional quantity for eggshell quality and immunity respectively.
Trace mineral
requirement is increased by 15-20% as there's an increase in excretion of minerals. Specific trace minerals like organic
Chromium supplementation play a critical role in improving both cell mediated and humoral immunity while also reducing glucose concentration in blood and better uptake of glucose by cells. (Ghazi et al, Biol. Trace Elem. Res. 2012) To prevent problems due to respiratory alkalosis due to excess panting, electrolyte and sodium bicarbonate addition is crucial to replace lost ions which improves feed intake and eggshell quality. Betaine HCl is an important inclusion for broilers and layers as it regulates the water balance inside cells and prevents dehydration related losses. Also, Betaine is studied to improve immunity in birds.
Conclusion:
Maintaining profitability during heat stress is a challenging task. This is because there are multiple physiological and behavioral changes that occur during high ambient temperature which ultimately lead to production losses. A comprehensive strategy which includes efficient nutrition, water and farm management will help in reducing signs of heat stress and bring down overall losses in the farm.
For any further information, you may contact the author at rahul.mittal@kemin.com