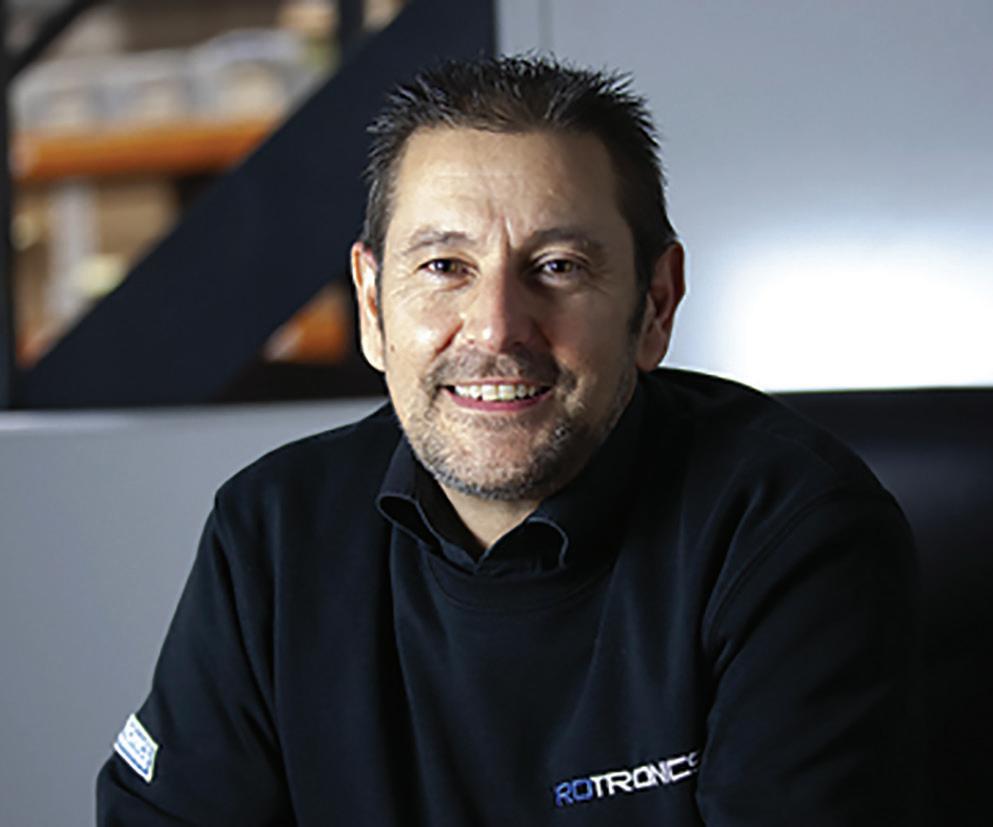
3 minute read
IT’S ELECTRIFYING!
Each time we put pen to paper about electrification in the automotive sector, processes have changed, more information is known, and the skills of technicians have grown.
“We are working with a lot of vehicle manufacturers, and they are working much smarter in relation to the 12V battery and the EV pack,” says Ken Clark, Managing Director at Rotronics. “There’s a growing recognition that the health of the 12V battery remains central to an electric vehicle. Some manufacturers have Flying Doctors, a specialist team sent out to fix problems at dealer level, while others choose to have dedicated specialist EV-enabled dealers. Some even have full-blown EV capability across all dealers.”
In the aftermarket, EVs are being supported by improved specialist teams, who are being trained to solve a number of electrification issues. However, there is still limited capability, and today’s technology supports an ‘all-makes’ solution. We must also recognise that many EVs remain under manufacturer warranty and won’t come into the aftermarket for some time.
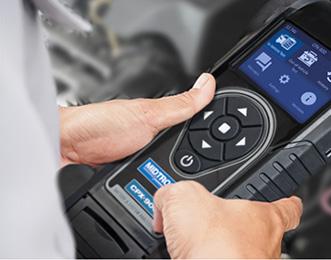
“We know with our recent customer problem-solving that the most simple and realistic issue to solve remains the 12V battery,” says Clark. “This is worked on by everyone, not just specialist teams. Every workshop has to be able to manage the 12V battery in the best possible way. Even in an EV, the 12V battery remains at the very heart of the vehicle and its systems, and unlike the EV pack itself, is often only provided with a two-year warranty. This makes it a good fit and an opportunity for any aftermarket workshop to maintain and replace.”
It’s also worth noting that problems with the 12V battery remains the number one cause of roadside breakdowns –something that hasn’t changed despite more electric vehicles being on the road.
Back to college
Rotronics has been working with a UK-based training academy in the South West to find the best technology to support EVs, with a primary focus on the EV pack and the 12V battery. The training academy called in the Rotronics team to solve a problem with a malfunctioning vehicle. The EV pack appeared to be OK, but it took four days for the lecturers to work out that it was actually the 12V battery at fault.
“The 12V battery was flat but they had no test or charge technology,” explains Clark. “Worse still, they didn’t know they should have the technology because they thought the EV pack would solve any issues with the 12V battery.
“They have since invested in a CPX900 and GRX5100 to ensure they can look after the electric vehicles used for training in the academy. The GRX5100 offers an unrivalled ability to safely discharge and balance HEV and EV battery packs.”
Heavy support Rotronics has also been called in to provide assistance to electric truck manufacturers.
“Not surprisingly, the assistance we have been asked to provide is not only how to support and manage the EV packs, but also the technology required to sort out the 12V batteries as a matter of priority,” says Clark. “We have done that, and it’s been heartening to work with the team as they understand that the management of the 12V battery is the principal consideration.
“Without a 12V battery in the best condition, the EV trucks go nowhere. I may have sounded like a broken record for a while about battery management, but it’s great to see that
PLEASE CONTACT THE ROTRONICS TEAM FOR MORE INFORMATION ON AVAILABLE PRODUCTS AND THE BATTERY MANAGEMENT PROGRAMMES workshop managers and vehicle manufacturers are now really taking notice and seeking help. It’s saving them considerable sums of money.”
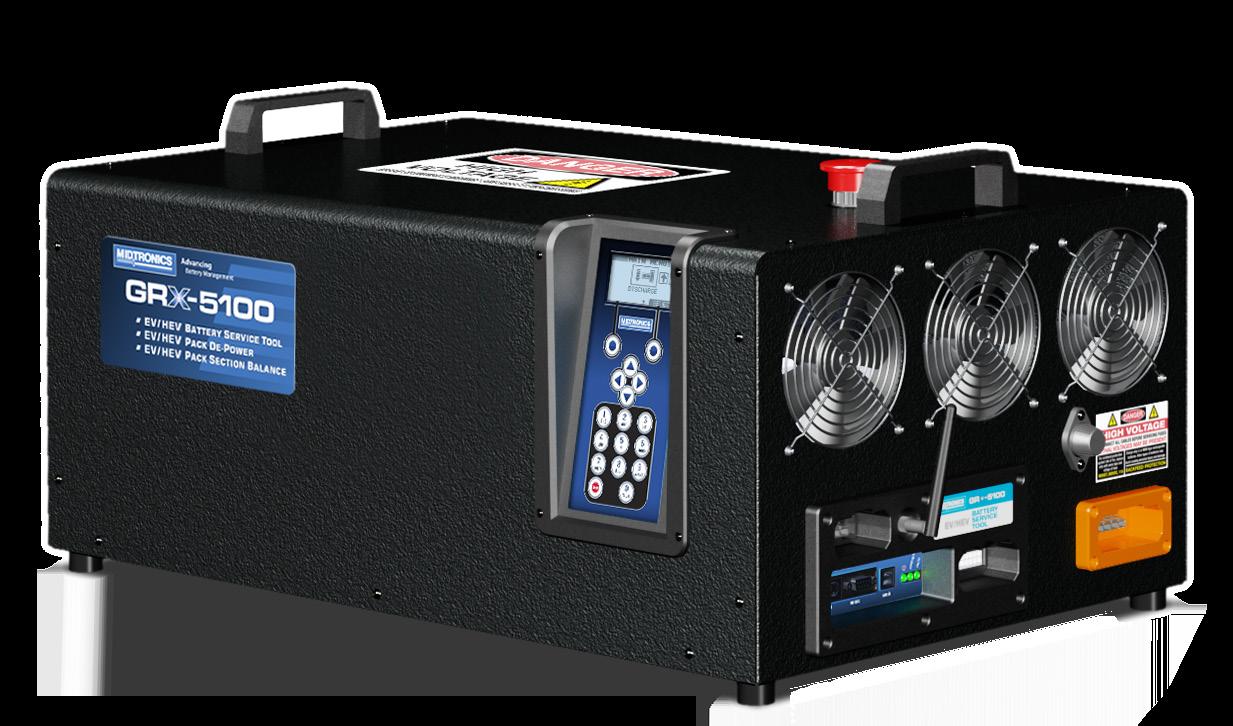
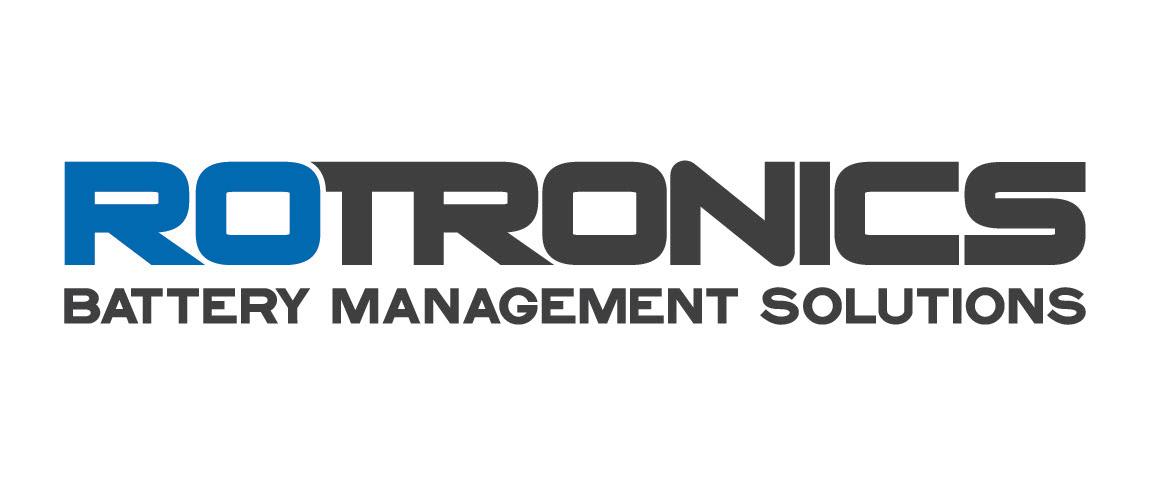
End of life
Another area of the automotive sector that’s coming forward to seek assistance for their electric vehicles are the end-of-life or reclamation and recycling teams. But they need to understand where to start by answering the following questions:
• What tools do you need?
• How do you communicate with the vehicle?
• Do modules need charging?
• How do you discharge down?
• How do you recycle the pack?
Rotronics is pleased to be in the development stages of working with end-of-life vehicle suppliers, finding better ways to recycle and recover EV packs for second-life applications. There is little consistency in the EV pack across vehicles or battery manufacturers, while there are multiple cables to attach the diagnostics to the pack.
The 12V and 24V battery sets in a passenger car or commercial vehicle in a BEV application remains one of the most important components that, if not maintained, will cause the vehicle to break down.
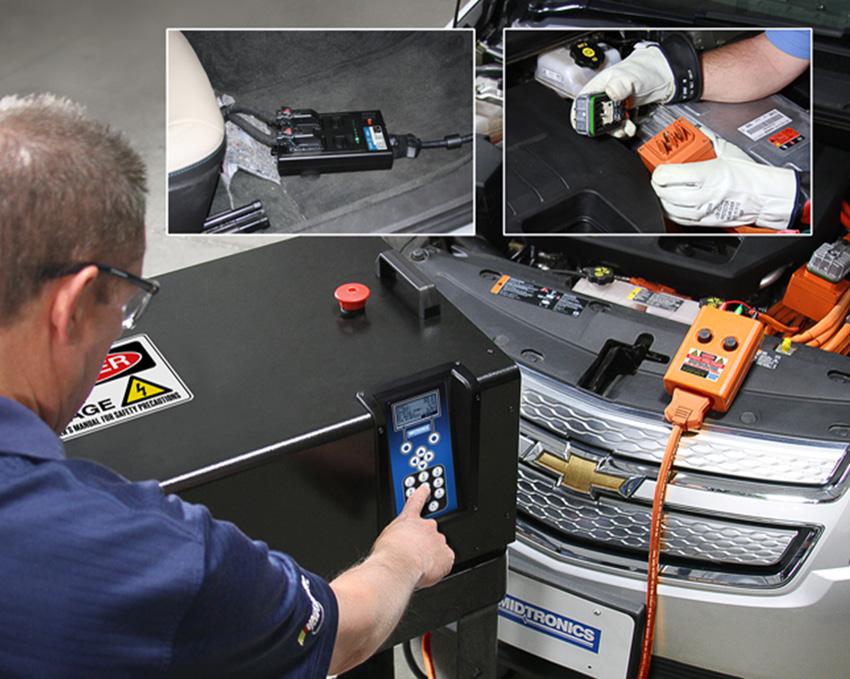
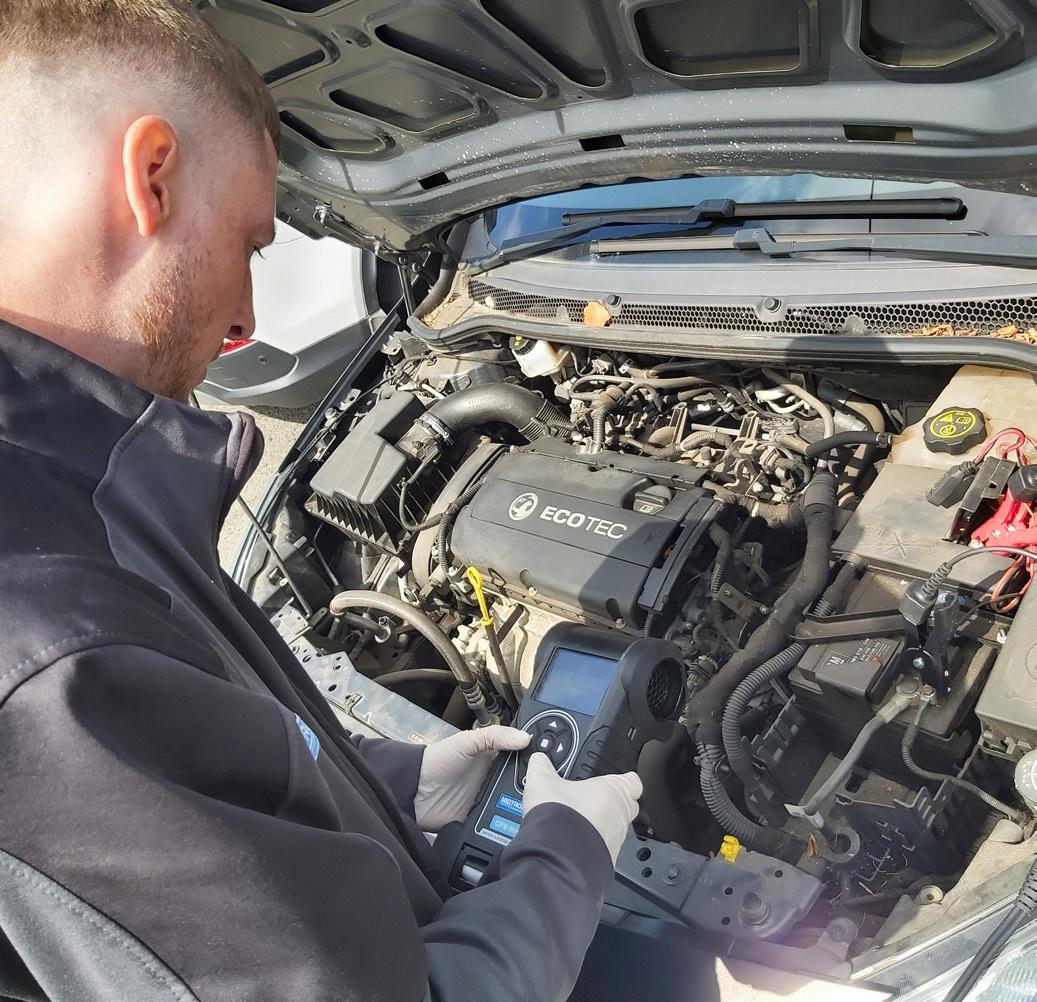
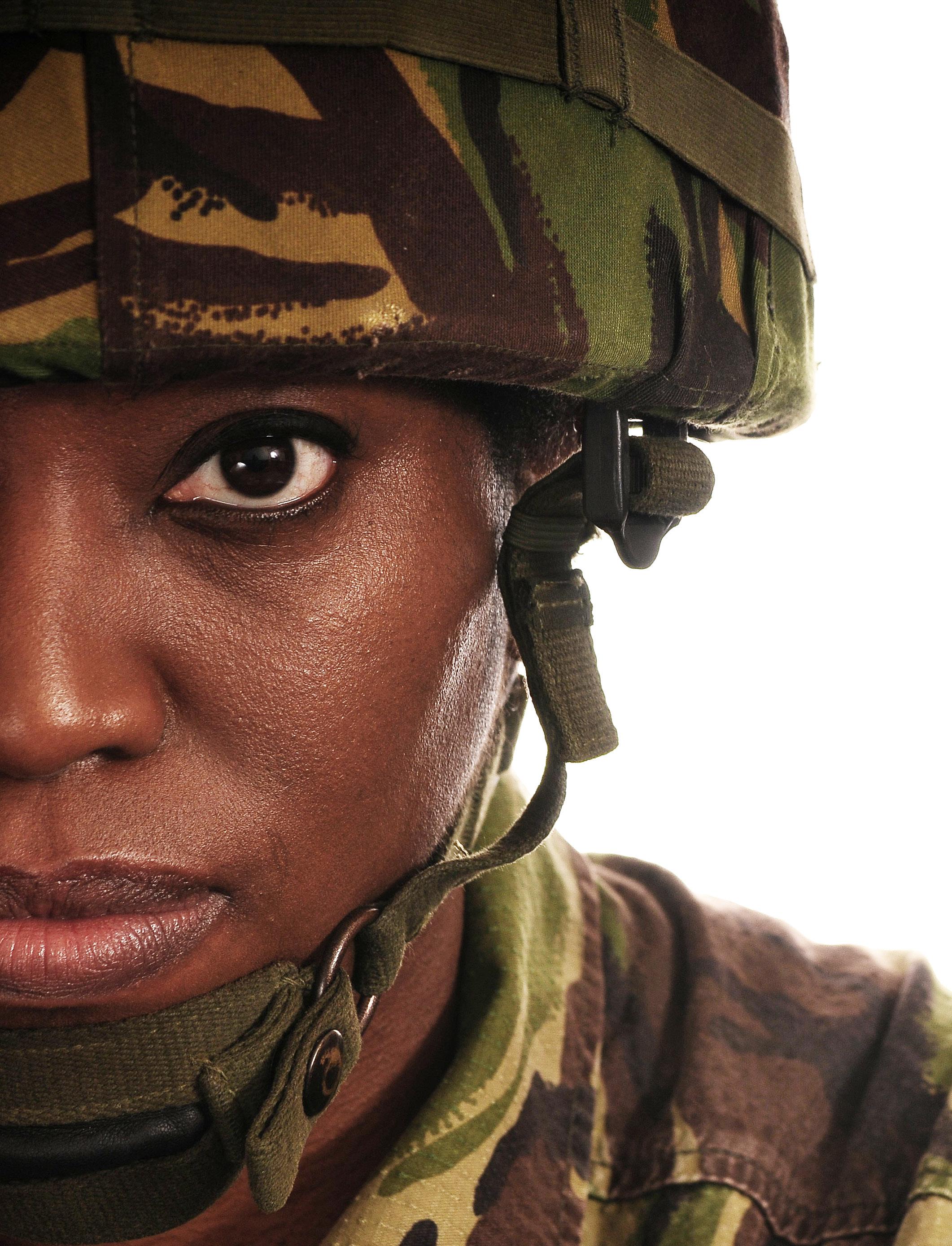
Automotive needs to bring in as much new talent as possible, and while the focus has traditionally been on exciting a new generation about the sector, it isn’t the only avenue.
There are a lot of people looking to change careers, shifting from what they know to a new challenge in automotive. But the road to the industry isn’t always clear, which is why the Mission Motorsport charity is helping with the transition.
As part of the MoD’s Career Transition Partnership, the charity helps those leaving the military to find employment in the automotive industry. An IMI training provider, Mission Motorsport delivers a range of qualifications up to and including Level 3 Diploma courses and full apprenticeships to enable service leavers to bridge the gap between military service and a second career as a civilian.
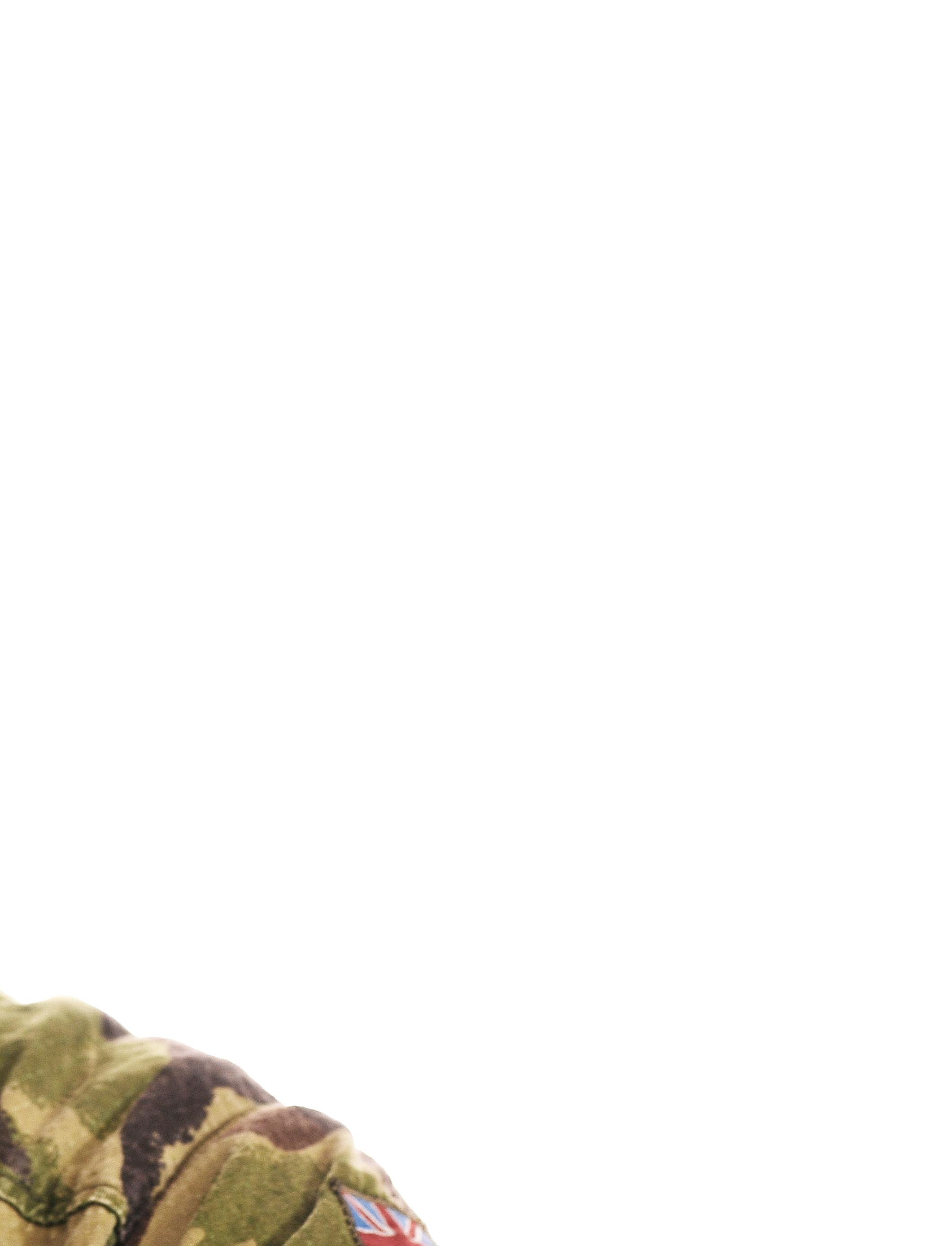
MotorPro Editor James Scoltock chats with David Guilfoyle, technical training manager at Mission Motorsport, and ex-student James Eaton to talk about how to make the move from military service to automotive a success.
FOR MORE FANTASTIC IMI PODCASTS, HEAD TO OUR PODBEAN CHANNEL FOR THE LATEST CONTENT
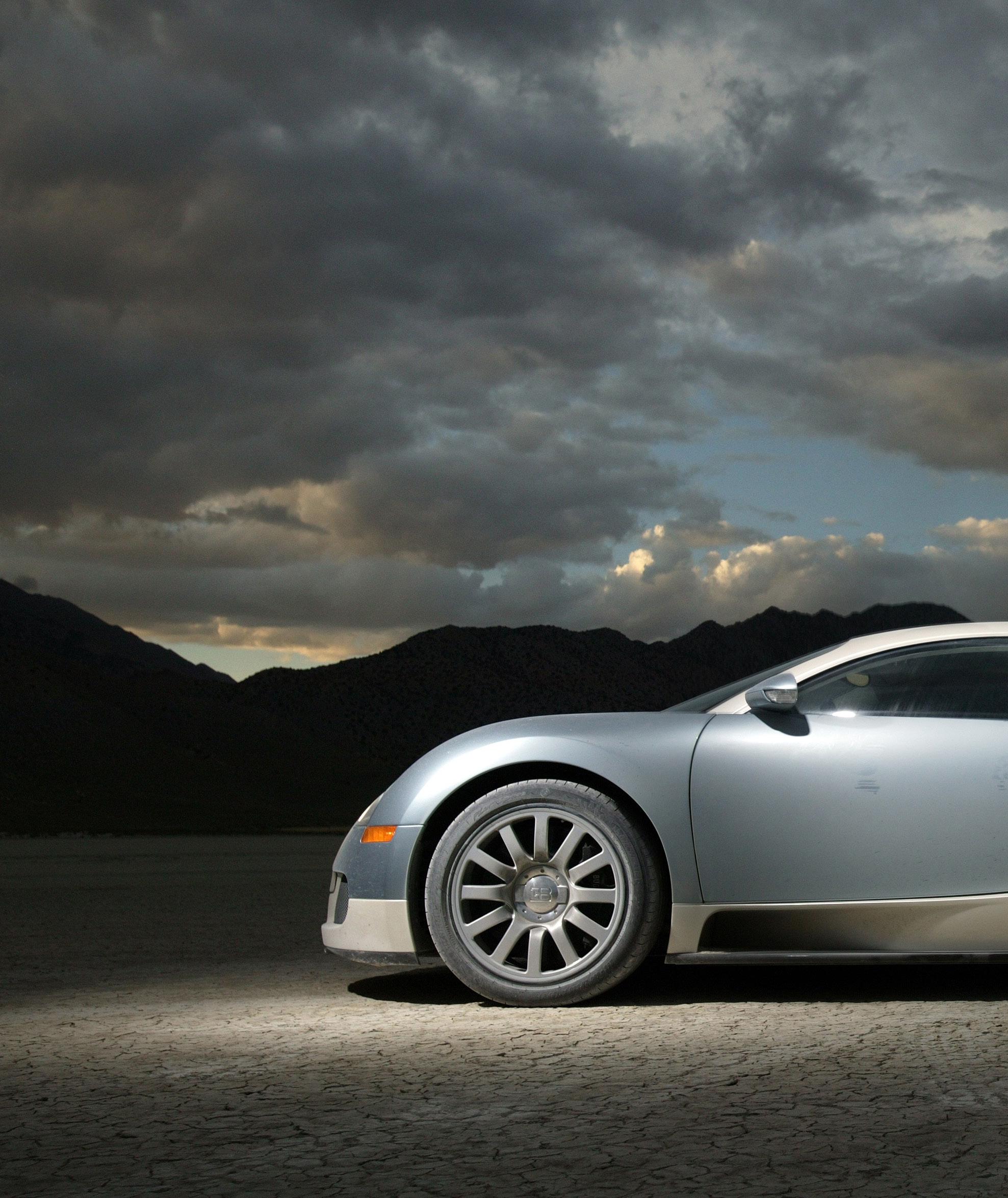