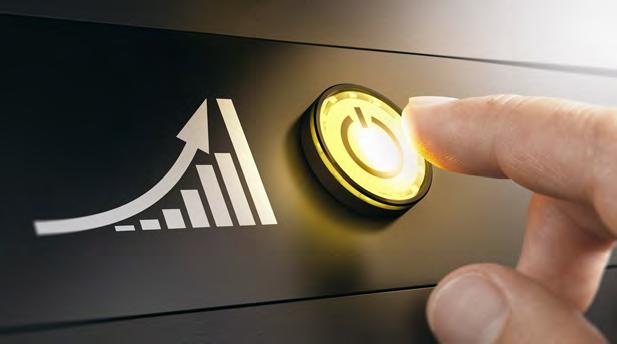
3 minute read
BOOST YOUR BUSINESS WITH SMART BATTERY MANAGEMENT
Ken Clark, managing director of Rotronics Battery Management Solutions, explains how data can generate cost savings and increase revenue for workshops, dealers and fleet managers through well-maintained 12V batteries
Why is battery management so important?
Whatever type of vehicle we discuss, the 12V battery is always the beating heart. If the battery is not in optimal condition, the vehicle won’t move – that’s why it’s so important.
All good battery management programmes should start at the beginning, whether that’s with the PDI, the dealership or importer, independent workshop or compound. It’s staggering to discover that less than 50% of vehicles entering workshops across all industry segments have batteries in a good state of charge.
As part of a proactive inspection process, technicians should be testing every vehicle entering the workshop as soon as it arrives. This gives maximum charging time should the battery need it. Allowing vehicles to run idle in an attempt to charge the battery will achieve nothing more than a surface charging of the battery, which can lead to a false battery test diagnosis if the surface charge hasn’t been removed during the testing process.
Do workshops take battery management seriously?
In general, workshops don’t regard the battery to be as important as other vehicle components, with an attitude that the battery either works or it doesn’t. But we know that if a battery is maintained well then it will last for longer and perform better, saving the vehicle owner time and money.
If I was in a workshop, the first thing I’d do is test the vehicle battery and find out the maximum time required to fully recharge it. To avoid any downtime, I’d do this first, while carrying out the routine maintenance or service process. I’d use ROBIS, our web-based dashboard and reporting system to look at performance opportunities and examine my team’s test and charge activities. What gets measured gets managed, which means saving money through managing actions that arise through constant monitoring. If I need to generate revenue, I could also see what my opportunities and conversion rates are.
How does Rotronics demonstrate battery health?
Through our industry-first online battery reporting system ROBIS and 5.4 million battery tests across a vast range of vehicle types, industry segments and workshops, we have gained an incredible amount of knowledge about vehicle battery health.
The ROBIS system can tell us which workshops are properly managing their batteries and whether their tests are improving. For independent workshops, we can see if technicians are recording the data correctly and carrying out the tester’s instructions, as well as any revenue-generating opportunities there may be.
We also work with CV/Fleet managers and owners, as well as independent workshop and main dealers, to look at the considerable cost savings and opportunities gained from the data, ensuring that the batteries last longer and perform better.
What does the future hold for batteries?
The future of automotive is electrification and hydrogen. That pathway is already set, and cars and vans have a 2025 deadline to reduce their CO2 emissions by 15% from the 2021 baseline. By 2030, the target increases to 37.5% for cars and 31% for vans.
With electrification, workshop behaviours and general service processes will have to change. The 12V battery will become a real focus during electrification as it’s the one component that remains constant in the maintenance programme. The application of batteries may change, but the management of the 12V and 24V battery set will be unchanged for commercial and passenger vehicles. Electrification will certainly not alter the need for continued battery management across all vehicle types and industry sectors.
What can industries do to prime early-career mindsets for a future of proactive battery maintenance?
Get on board with the importance of battery management – just because you can’t see what’s going on inside the box doesn’t mean that it’s not essential – and understand what the latest battery management technology and data gathering can do.
This smart technology can save or even make money for you, so looking seriously at the potential cost savings and the revenuegenerating opportunities is vital.
The applications of vehicles are changing, and we are now looking at endurance rather than cranking as a primary function of testing a battery. We need to ensure it remains at the forefront of any service programme and becomes a natural part of everyday workshop practice.
FOR MORE INFORMATION ON ROTRONICS BATTERY MANAGEMENT PROGRAMMES, CALL KEN CLARK ON 0121 514 0605 OR EMAIL INFO@ROTRONICSBMS.COM