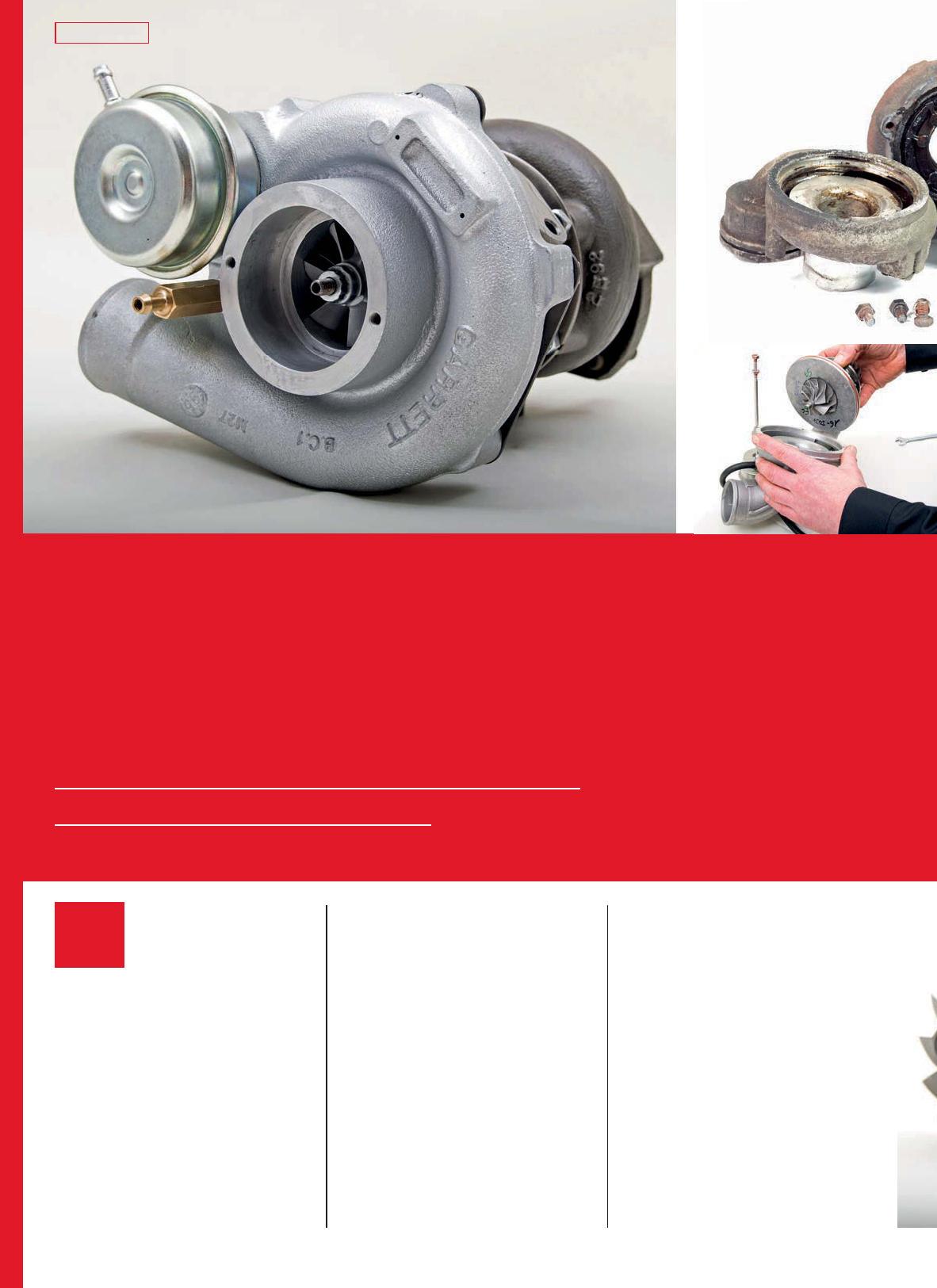
12 minute read
TURBO FAILURES
Are you doing this to your turbo?
A wellbuilt turbo should last the life of the engine
Advertisement
TURBO FAILURES ARE YOU KILLING YOUR TURBO?
We take a closer look at what could be killing your turbo, and how to prevent it
Words DAN SHERWOOD & JAMIE / Photos JAMIE & FAST FORD ARCHIVES
Awise turbo specialist once said, “Turbos don’t die; they’re killed.” And they were right. Turbochargers get a bad rep for being temperamental old things that like to play up in anything other than 100 per cent perfect conditions, but that’s not really fair.
Turbos must put up with some of the harshest conditions your engine dishes out – those immense heat cycles would put an enormous strain on any piece of hardware, but a well-cared-for turbo will happily cope. Looked after properly, a good turbo can last the lifetime of your car, even on a tuned engine. But they’re not indestructible. They rely heavily on other component parts of your engine – not to mention your mapping settings – being in tip-top condition too. That’s why we’ve complied this guide to the most common causes of turbo failure, what caused them, and how to prevent it from happening.
OIL STARVATION
Without question, the most common cause of turbo failure is oil starvation. A turbocharger’s turbine shaft runs at speeds of over 150,000rpm and at temperatures exceeding 900C, and it can do so almost endlessly – but only when lubricated as it was designed to be.
To work effectively, a turbo needs a constant flow and pressure of clean, good quality oil. This not only works to lubricate the thrust and journal bearings, it also helps to stabilise the rotating shaft and journal bearings, as well as acting as a coolant. This requirement is intensified as the turbocharger speed and engine load increases. Even a small reduction in oil pressure can be enough to kill your turbo in seconds, and can be identified by blueing on the turbo shaft or seized bearings. The main causes of oil starvation range from oil pump failure to low oil levels; or dirty oil to broken or blocked oil feed pipes.
HOW TO PREVENT OIL STARVATION
Use a good-quality oil and filter and change them sooner than your manufacturerrecommended intervals. Keep an eye on your oil pressure too – ideally via an aftermarket gauge reading directly from the oil feed union to the turbo – as any drop in pressure can destroy a turbo very quickly.
OIL CONTAMINATION
Many people assume the oil filter will remove any dirty bits before the oil reaches the turbocharger. But this can be a costly mistake.
Impact damage will quickly kill a turbo
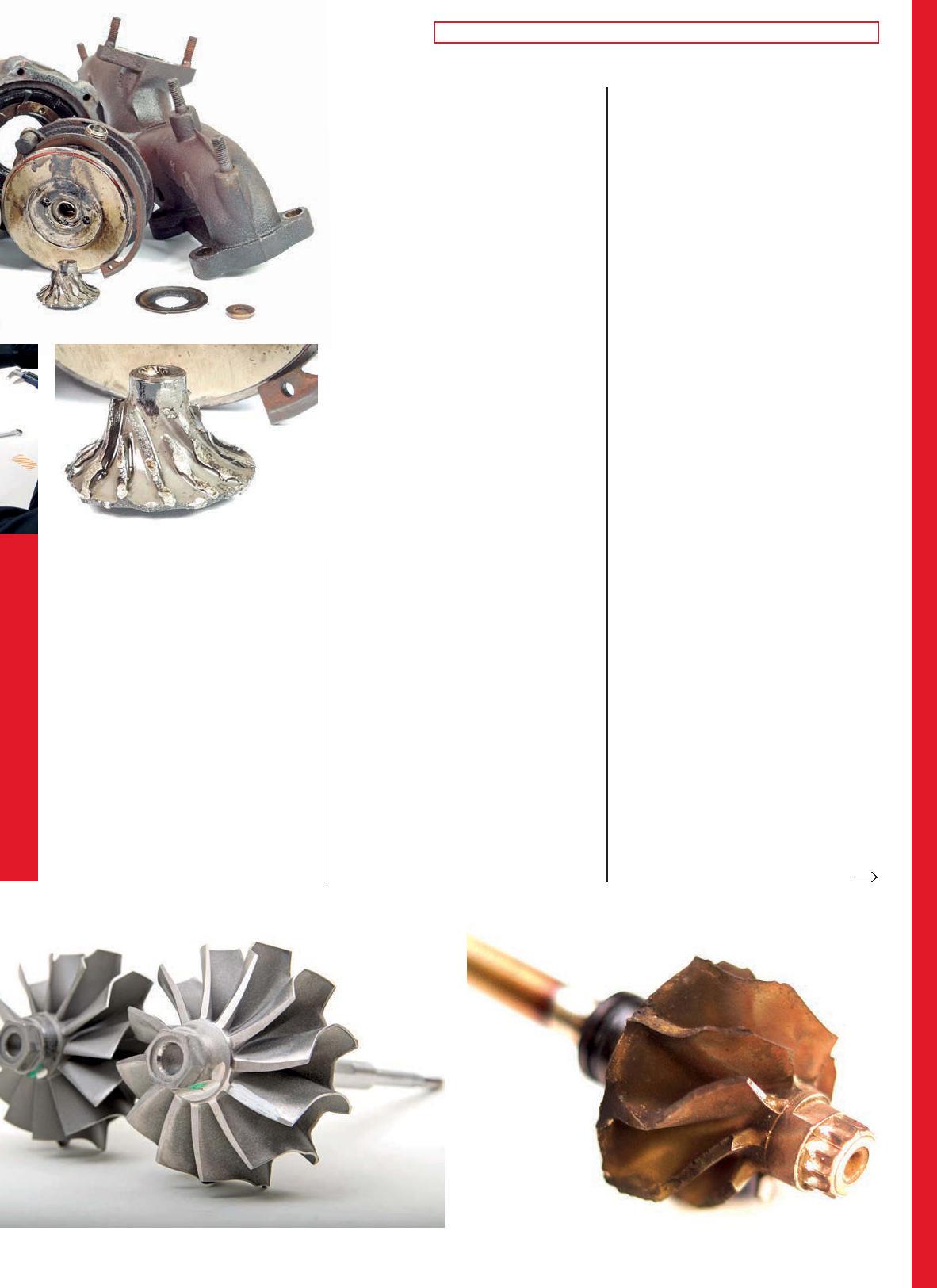
Just like having low oil is bad news for your blower, contaminated oil is also a sure-fire way to turbo failure. Any particles of debris floating around in the oil system (from the products of fuel combustion such as carbon deposits and soot, to tiny metal particles from general wear and tear of the engine) will eventually get past the oil filter and end up at the turbo, causing damage to the smooth surfaces of the bearings and shaft.
But it’s not just particles getting past the oil filter that can cause damage. Other engine problems that allow water or fuel to mix with the oil (such as head gasket failure) will prevent the oil from working as it should, reducing its supportive, cooling and lubricating capabilities.
And when this happens, it is always the turbo that fails first.
HOW TO PREVENT OIL CONTAMINATION
Good quality-oil and filter, changed well before the prescribed intervals, is essential. Adding an inline turbo pre-filter could also help catch any errant particles hell-bent on waging war on your turbo.
IMPACT DAMAGE AND TURBO FAILURE
The air filter prevents dust particles, small stones, dirt and leaves from reaching the turbo’s delicate compressor wheel. Running without an air filter, or even just using one that has rubbish levels of filtration, means more debris will find its way into the turbo. And, spinning at 150,000 rpm, it doesn’t take much of an imbalance to wreak havoc.
At best, the bearings will wear out prematurely because of the excess vibration, but often the imbalance is great enough to cause the compressor wheel to clip the inside of the compressor housing. When this happens, larger chucks of the blades can break off, making the whole thing even more out of balance, until eventually the compressor wheel destroys itself.
Although more likely – and easier to prevent – impact damage isn’t limited to the turbo’s compressor wheel; it can also happen to the turbine wheel caused by debris from inside the combustion chamber. This could be anything from lumps of carbon, injector tips or broken valve parts, to bits of weld or rust from the manifold. But whatever it is, anything hitting the turbine wheel will cause considerable amounts of damage.
HOW TO PREVENT IMPACT DAMAGE
Always invest in a good-quality air filter with good filtration properties, as well as meeting the airflow requirements for your power level. And make sure you clean it regularly, according to the maker’s instructions.
Also, be sure to check the turbo for loose connections and debris, especially if fitting a turbo after a previous failure. If possible, check exhaust manifolds for signs of internal rust or loose weld spots too.
Cut-back blades help prevent the turbine wheel from clipping the inside of the housing and causing damage
BUILD QUALITY
OE turbos are built to meet stringent specifications and pass numerous quality checks and tests. That’s part of the reason they’re so expensive. A high-quality aftermarket turbo, built by a reputable specialist, will also have strict quality control, testing and development procedures, again adding to the costs.
Problems can arise when you try and cut costs with cheap turbos that perhaps haven’t gone through the same vigorous checks to ensure build quality. Although things may seem fine for a short time, the usable lifespan is often radically reduced, meaning the savings you make on the purchase price are lost through buying twice when your cheap turbo fails.
HOW TO PREVENT IT
Buy from a reputable specialist to ensure you’re getting a quality product, and that can provide backup in case of any problems and technical queries.
THRUST BEARING FAILURE
As the compressor wheel spins, it is effectively trying to pull the shaft out of the front of the turbo. It is prevented from doing so by the turbo’s thrust bearing, which holds the shaft in place and resists this axial force. On most standard applications with low boost levels, a 270-degree thrust bearing is sufficient to stop this from happening – it’s called a 270-degree bearing as there is a 90-degree cut-out that allows the bearing to slide over the shaft, making a turbo cheaper and easier to produce; a 360-degree bearing is made of three pieces, and assembled with the shaft running through it.
But increase the boost and the thrust bearing will struggle to contain it. This can lead to a reduction in lubrication and a
rapid increase in wear, identified by in-out play in the shaft and smoke from the exhaust.
HOW TO PREVENT THRUST BEARING FAILURE
Have your turbo checked over before you start increasing boost pressures. This could involve getting it refreshed by a turbo specialist with new or uprated bearings if you are planning on pushing things further.
STOPPING THE ENGINE WHEN THE TURBO IS HOT
A turbo is fed by hot exhaust gases, so unsurprisingly creates a lot of heat in the shaft and bearings, much of which is dissipated by the flow of oil. When allowed to slow down and cool over a reasonable period, this isn’t a problem. But by shutting off an engine immediately after being on boost, the flow of oil is halted and that heat is trapped inside the turbo. This heat can cause damage, including a warped shaft – due to turbine droop – as well as carbonising the oil and damaging the bearings. At this stage it’s all over, and turbo failure is imminent.
HOW TO PREVENT HOT STOP
It’s recommended that you end your journey at a more sedate pace or, once at your destination, simply leave the engine ticking over for a few minutes to allow the turbo to cool down before shutting it off. Turbo timers were popular back in the day, but just leaving the car running for a few minutes before you lock up and leave it does the same thing.
CLOGGED ENGINE BREATHER
The engine breather system is an important part of a turbocharged engine; it’s a oneway valve that allows high pressure blow-by gasses from the crankcase to pass through without causing excessive pressure in the oil system. If this gets clogged it will allow excessive pressure to build up in the engine. In turn, this will pressurise the turbo’s oil system, causing oil to force its way past the bearings, causing damage to the bearings and blue smoke to be emitted from the exhaust.
HOW TO PREVENT GETTING A CLOGGED ENGINE BREATHER
The standard PCV system should cope with moderate increases in power while continuing to control the emissions from the crankcase, but the system should be thoroughly checked (even on a relatively new car) and any suspect valves and hoses replaced. For highly-tuned applications, a remote catch tank is advised to vent excess pressure and collect oil vapour.
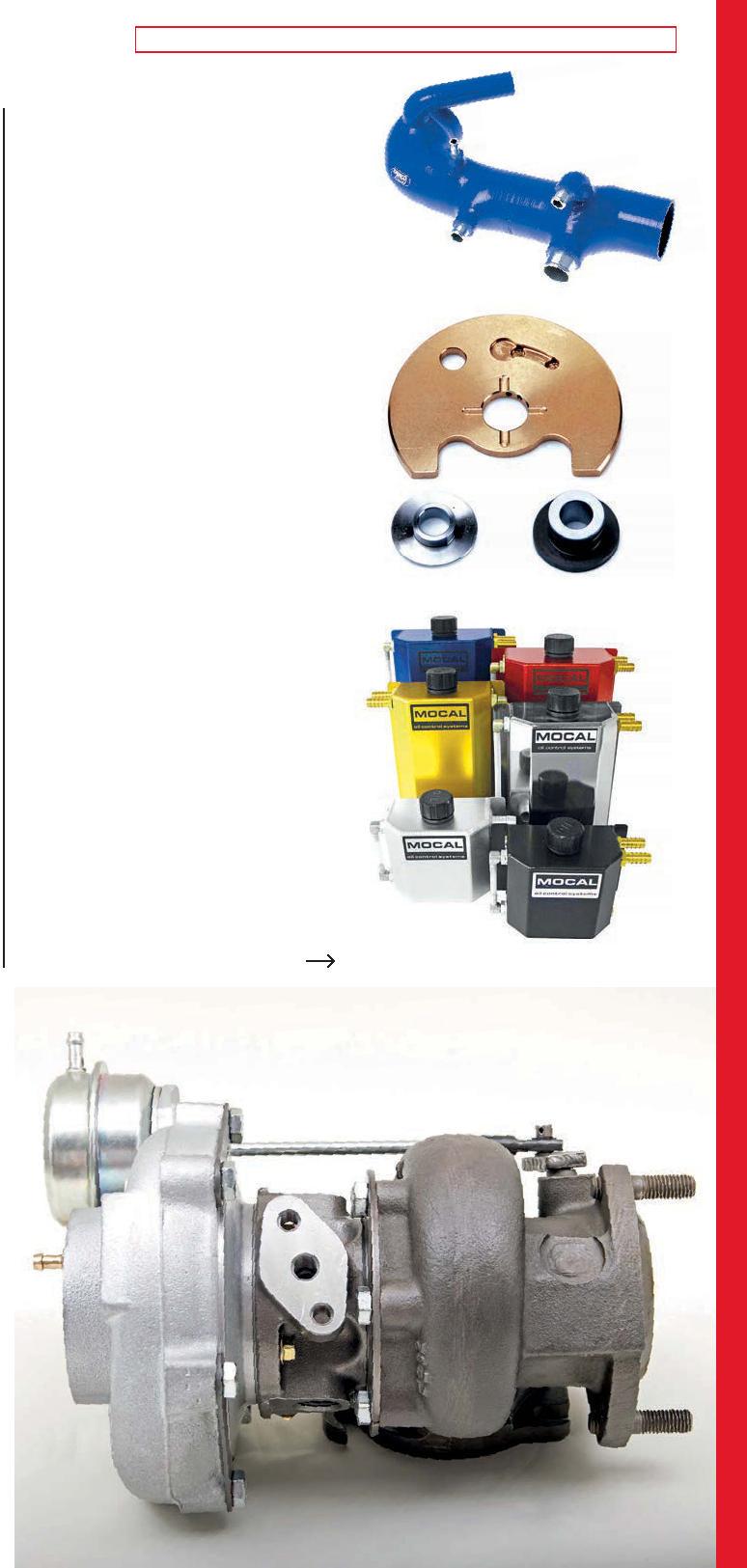
CARBON BUILD-UP
As well as damage and wear to the bearings and shaft, running old and dirty oil can lead to a build-up of sludge in the engine’s oil galleries and the turbo oil-feed pipework. Any restrictions or blockages here can prove fatal for your turbo. Some cars seem to suffer from carbon build-up and excess sludge more than others, and there is not much you can do about it other than keeping an eye on your oil condition when checking levels; thick black oil needs changing fast.
HOW TO PREVENT CARBON BUILD-UP
The use of good-quality oil and fuel will help limit potential build-up, as will regular oil and filter changes. Also, inspect the waste oil and filter for signs of build-up and to get an insight into what’s going on inside the engine.
OVER-BOOSTING
Also known as over-speeding, over-boosting is where the turbocharger is operating above its normal limits. Like any component that is working harder than it was designed to, this causes excess wear and eventually damage. This can damage the bearings, shaft and even the turbine and compressor wheels themselves (they effectively increase diameter under the huge centrifugal forces, and expand so much they can make contact with the inside of the housings). Overboosting can occur for various reasons, from incorrect ECU mapping to a faulty or undersized wastegate or actuator. It is more commonly down to a simple air leak in the turbo system. There are various places air can leak from, including broken gaskets, split hoses or punctured intercoolers – all of which force the turbo to work harder as it tries to reach the required boost pressure.
HOW TO PREVENT OVER-BOOSTING
Ensure that all the turbocharger pipework (and intercooler) is sound with no splits, cracks or leaking joints. Consider uprating
Silicone hoses can help cure boost leaks and prevent your turbo from over-boosting
360-degree thrust bearings are a good upgrade
Don’t under estimate the importance of a good breather system on a turbo’d engine
External wastegates can help with compressor surge
to silicone hoses, which will not perish over time and are capable of holding greater pressure. Also, ensure that the wastegate and actuator are operating correctly.
BAD MAPPING
The standard mapping will never cause your turbo to fail, but poor remaps can, and often do. Simply upping the boost levels or crudely turning everything up will cause all manner of performance and reliability issues, not least of which for your turbo. Incorrect AFRs can introduce excess carbon build-up, high EGTs can crack housings, too much boost can cause over-speeding, and when it all eventually blows up, the chunks of broken engine exiting via the exhaust will completely finish off your turbo just for good measure.
HOW TO PREVENT IT
Choose a reputable specialist to map your car. It’s also worth doing a full health check before you look to increase the power levels, as any faults will need to be fixed first.
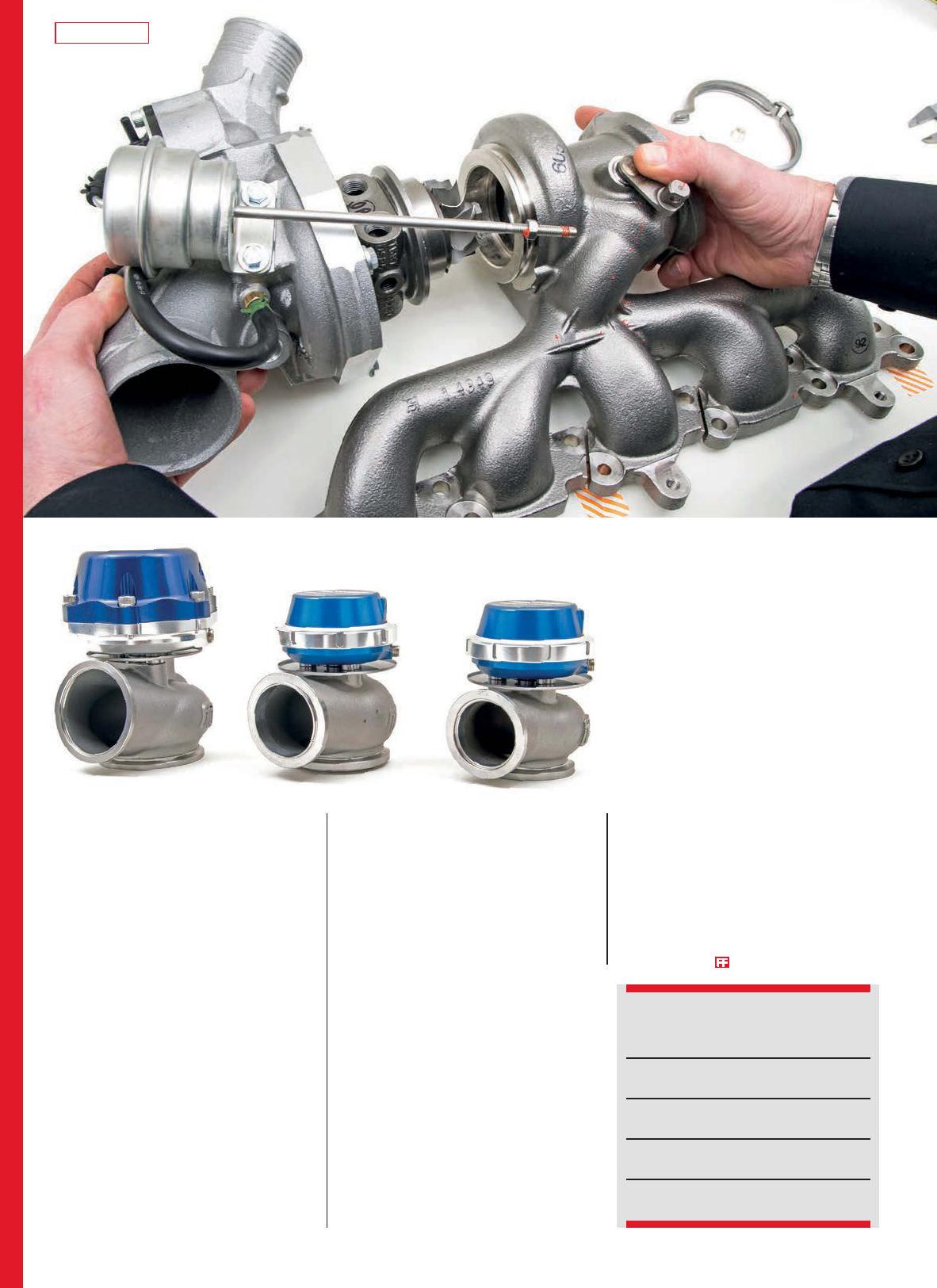
COMPRESSOR SURGE
Turbo cars make some great noises, especially when they are tuned, and that’s all part of the fun. But some noises can signal problems. One such sound that you don’t want to hear is the ‘flutter’ or ‘turkey gobble’ sound sometimes wrongly referred to as ‘wastegate chatter’. This noise is the sound of compressor surge.
It happens when the turbo is delivering more air than the engine can take in, which then backs up and eventually tries to force its way back out through the turbo the wrong way – the noise is this air hitting the still spinning compressor wheel blades. It may sound cool, but the added pressure on your turbo will cause accelerated bearing wear.
HOW TO PREVENT COMPRESSOR SURGE
Eliminating compressor surge can be achieved by fitting a suitable blow-off valve, but if you are experiencing surge at wide open throttle (when any BOV would be shut anyway) you need to look at other areas such as turbo sizing, wastegate and actuator function and mapping.
EXCESSIVE EXHAUST GAS TEMPERATURES
Turbos are built to take the high temperatures generated during normal operation, but if the temperature of the exhaust gases is too high, it can cause catastrophic damage. Typically, this damage is located around the turbocharger’s turbine, cracking the housing, causing excessive erosion and corrosion, all while causing collateral damage to other components like the wastegate.
HOW TO PREVENT IT
Excessive exhaust gas temperatures (EGT) can be caused by poor-quality oil, faults in the oil cooling system, incorrect mapping, bad tuning, poor maintenance and such like.
To ensure your car stays within a safe range, fit an EGT sensor, ideally one that feeds back to the ECU. That way, if the temperatures go up it can shut down the engine before any damage is done.
CONTACTS
TURBO ZENTRUM
www.turbozentrum.co.uk
TURBO PERFORMANCE
www.turboperformanceltd.com
TURBO TECHNICS
www.turbotechnics.com
AET TURBOS
aet-turbos.co.uk