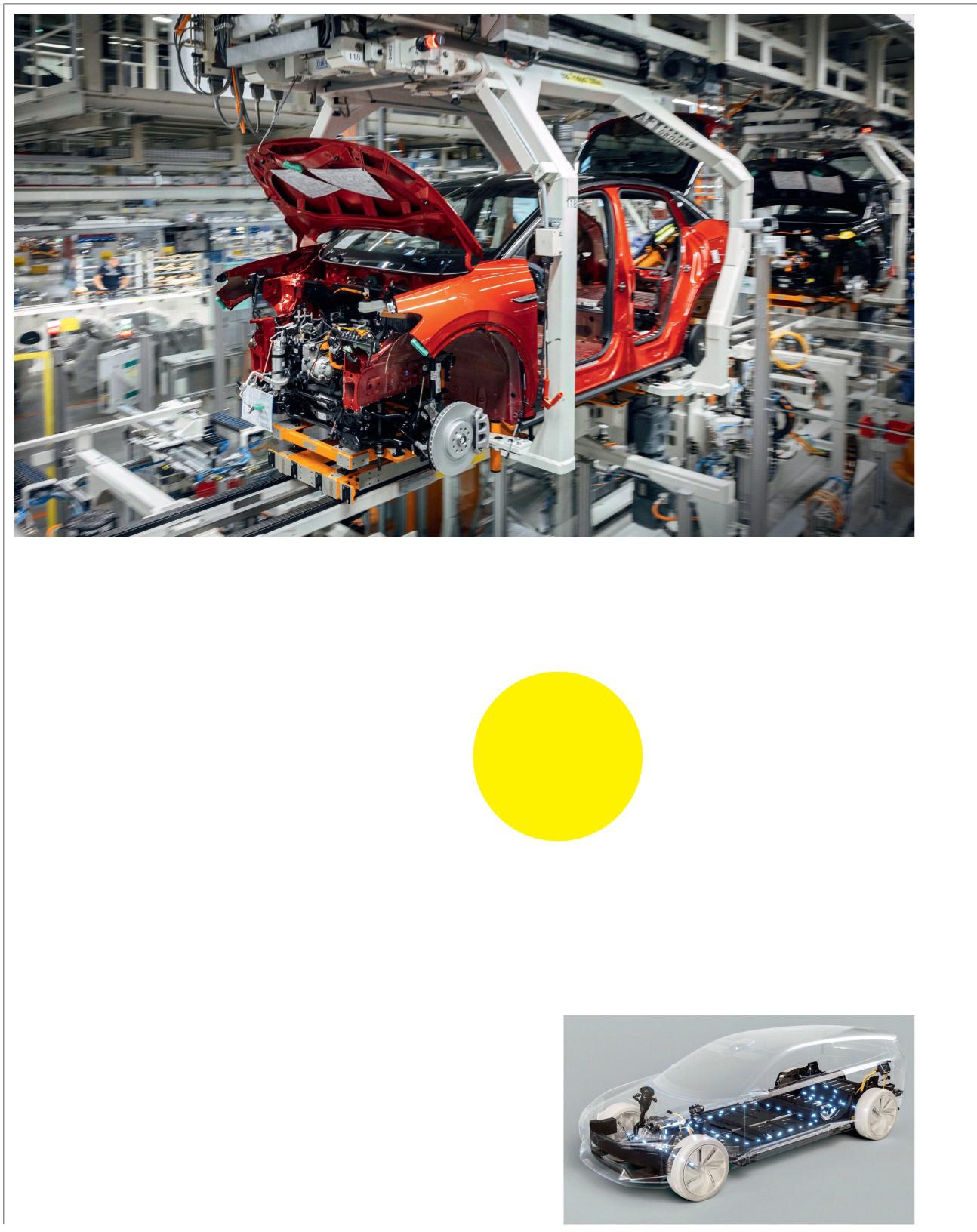
3 minute read
DIY car makers Building parts in-house is on the up
from sin46th magzus.org
by Thomas Swift
Assembly lines bring together parts sourced from numerous suppliers
Car firms eye in-house parts supply
Advertisement
AsindustrymovestoEVs,manufacturerswanttocontrolproductionofvitalparts
Car maker’ is a common term, but the truth is that today’s car companies are more assemblers of bought-in parts than actual manufacturers.
That was highlighted in a recent comment by Stellantis CEO Carlos Tavares, who said that the value of a car once it has emerged from the factory is “85% bolt-on parts” .
These parts are sourced from thousands of lesserknown suppliers, but as we shift from internal combustion engine cars to electric cars using ever-more sophisticated software, car makers are trying to recapture some of the value lost to suppliers.
The process of making parts in-house is called vertical integration, and car makers are going further down that route in specific areas – most notably batteries but also computer chips and software.
This is happening for a number of reasons: to keep some of the profit lost to suppliers, to ensure a good flow of limited supply and even to work out exactly what the CO2 costs of the components are.
Some manufacturers have always leaned towards
‘vertical integrati Volkswagen. But recent years has on, notably the trend in been to farm out more work to suppliers. This keeps capital investments to produce the parts off the car maker’s books and, if the parts supplier is large enough, can actually work out cheaper. The rapid pace of technology change is forcing a rethink, however. Car makers will focus on parts very specific to EVs –power electronics, batteries and the raw materials for those batteries – and not just take over the jobs of the tier-one suppliers (those that sell parts directly to the car maker, rather than to other parts suppliers). “The traditional tier-one and tier-two go-to-market model has evolved, ” said Enrico Salvatori, president of Qualcomm Europe. The new vertical integration approach is different from the old model, whereby car makers would forge cylinder blocks themselves. They don’t have or want the capability to make chips or refine battery materials, but they do want to secure the supply long before they need it, and that means investing in or partnering specialists.
Volkswagen has partnered Chinese company Gotion for a new battery cell plant in Salzgitter, Germany, to start in 2025. Both Volkswagen and Volvo have invested in Swedish battery company Northvolt to create partnerships that will secure them cell production. Stellantis and Mercedes-Benz each have a stake in French battery company ACC, while Renault has put its own money into battery maker Verkor.
As ever in the modern car industry, they are generally following the lead of Tesla, which showed the way with its battery tie-up with Panasonic. Tesla has also moved to secure raw materials via deals with BHP for nickel and Glencore for cobalt. Jeremy Wrathall, boss of British mining startup Cornish Lithium, said: “We’ve had various approaches by auto makers. No one has made us an offer to buy us, but the mood music is hotting up. ”
One other big advantage of going direct to the source of raw materials is that you know exactly its provenance and probably also its CO2 footprint.
“It’s important that you 70% know your CO2 intensity of your input materials, ” said Jon Regnart, automotive trend strategist at the UK
Proportion of electric government’s Advanced motors that will be made Propulsion Centre. in-house in the future, He cites Volkswagen’s up from 33% now investigation of lithium mining (Source: IHS Markit) in Chile as an example. Cars will continue to be largely made from bought-in parts, but makers’ targeted dives into the supply chain should yield better visibility of parts bottlenecks and better understanding of what goes into the final product. Neither of those things is a given right now, due to the often opaque sources of parts within parts. NICK GIBBS
Volvo will make EVs with batteries from a firm it part-owns