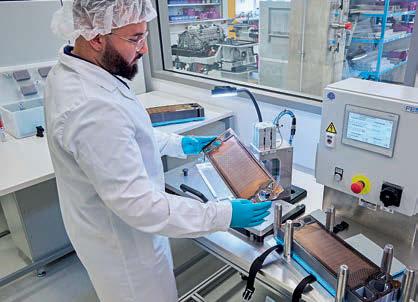
26 minute read
News
BMWNews
HYDROGEN X5 ENTERS PRODUCTION
Advertisement
BMW is continuing to test hydrogen as an option for electric drivetrains, now the iX5 Hydrogen has entered small series production.
BMW is continuing its exploration of hydrogen technology with the small series production of the iX5 Hydrogen. Fuel cell system production at the company’s competence centre for hydrogen in Munich got underway recently, the iX5 Hydrogen cars produced will enter service around the world from the end of this year for test and demonstration purposes.
BMW has been exploring hydrogen technology since 2013, and prides itself on playing a pioneering role in its use. For many industry insiders, fuel cell technology makes the most amount of sense for the future of mobility. And, since the BMW 5 Series GT Hydrogen Cell of 2015, fuel cell technology has been steadily refined.
“As a versatile energy source, hydrogen has a key role to play on the road to climate neutrality. And it will also gain substantially in importance as far as personal mobility is concerned. We think hydrogen-powered vehicles are ideally placed technologically to fit alongside battery-electric vehicles and complete the electric mobility picture, said Oliver Zipse, Chairman of the Board of Management of BMW AG. “By commencing small-scale production of fuel cells today, we are demonstrating the technical maturity of this type of drive system and underscoring its potential for the future.
“Our many years of research and development work have enabled us to get the very most out of hydrogen technology,” added Frank Weber, Member of the Board of Management of BMW AG, Development. “We have managed to more than double the fuel cell’s continuous output in the secondgeneration fuel cell in the iX5 Hydrogen, while weight and size have both decreased drastically.”
The technology in the iX5 Hydrogen generates a high continuous output of 125kW/170hp. It teams-up with an electric motor and a high-performance battery developed specially for the vehicle, this enables the powertrain to deliver 275kW/374hp. The system comprises two hydrogen tanks, fuel cell and an electric motor, this is integrated into the existing X5 platform enabling the small production run. The iX5 Hydrogen already underwent extreme weather testing in icy Sweden at the start of this year.
Now, you might be wondering how it all works. Inn essence a chemical reaction takes place in the fuel cell between hydrogen from the tanks and oxygen from the air. a n i i a steady supply of both elements f cell’s membrane is of crucial importance for drive system efficiency. In addition to the technological equivalents of features found on combustion engines, such as charge air coolers, air filters, control units and sensors, BMW has developed special hydrogen


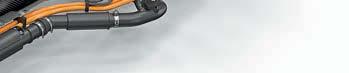
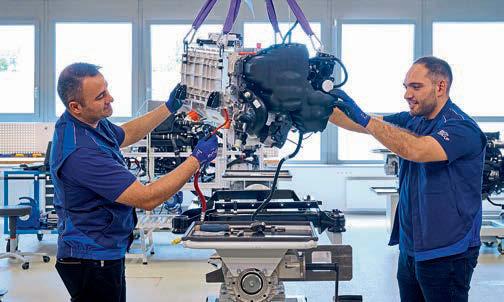
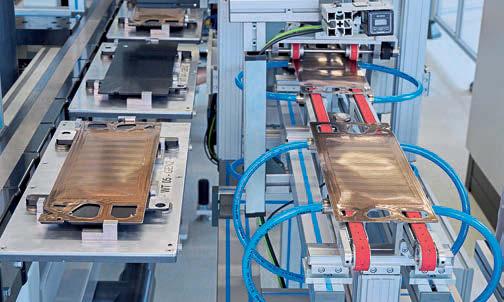


components for its new fuel cell system. These include the high-speed compressor with turbine and high-voltage coolant pump, for instance.
BMW sources the individual fuel cells themselves from Toyota. The two companies have enjoyed a partnership since 2013, collaborating on fuel cell drive system developments. Fuel cell systems are manufactured in two main steps. The individual fuel cells are first assembled into a fuel cell stack. The next step involves fitting all the other components to produce a complete fuel cell system.
Stacking of the fuel cells is a fully automated process. Once the individual components have been inspected for any damage, the stack is compressed by machine with a force of five tonnes and placed in a housing. The stack housing is manufactured in the light metal foundry at BMW's Plant Landshut using a sand casting technique. For this, molten aluminium is poured into a mould made from compacted sand mixed with resin in a process specially designed for this latest small-series vehicle. The pressure plate, which delivers hydrogen and oxygen to the fuel cell stack, is made from cast plastic parts and light-alloy castings, also from the Landshut plant. The pressure plate forms a gas-tight and watertight seal around the stack housing.
Final assembly of the fuel cell stacks includes a voltage test along with extensive testing of the chemical reaction within the cells. Finally, all of the different components are fitted together in the assembly area to produce the complete system. During this system assembly stage, further components are fitted, such as the compressor, the anode and cathode, the high-voltage coolant pump and the wiring harness. Whether or not BMW will roll out this technology on a larger scale remains to be seen.
LMDH TESTING CONTINUES
The BMW M Hybrid V8 has entered the next phase of testing in the USA.
Following initial shakedown runs in Italy and Spain, BMW's next Le Mans challenger, the BMW M Hybrid V8, has entered further intensive testing in the USA. Ahead of its debut at the IMSA WeatherTech SportsCar Championship season opener at Daytona next year, the new racer will test at various racetracks in the US where BMW's focus will shift from climate analysis, day and night running, to sheer performance and reliability.
BMW reports that there have not yet been any fundamental teething troubles, works drivers Connor De Phillippi, Sheldon van der Linde, Marco Wittmann, Augusto Farfus, Briton Nick Yelloly and Philipp Eng have all had outings behind the wheel. So too, the BMW Junior Team of Dan Harper, Max Hesse and Neil Verhagen, new signing René Rast has also completed a number of laps in the new car.
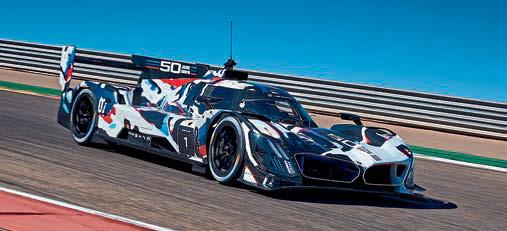
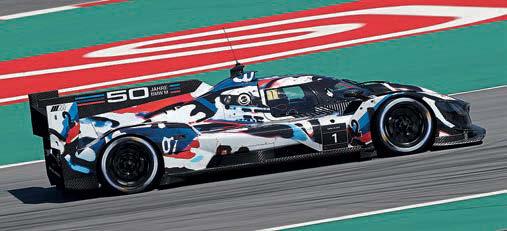
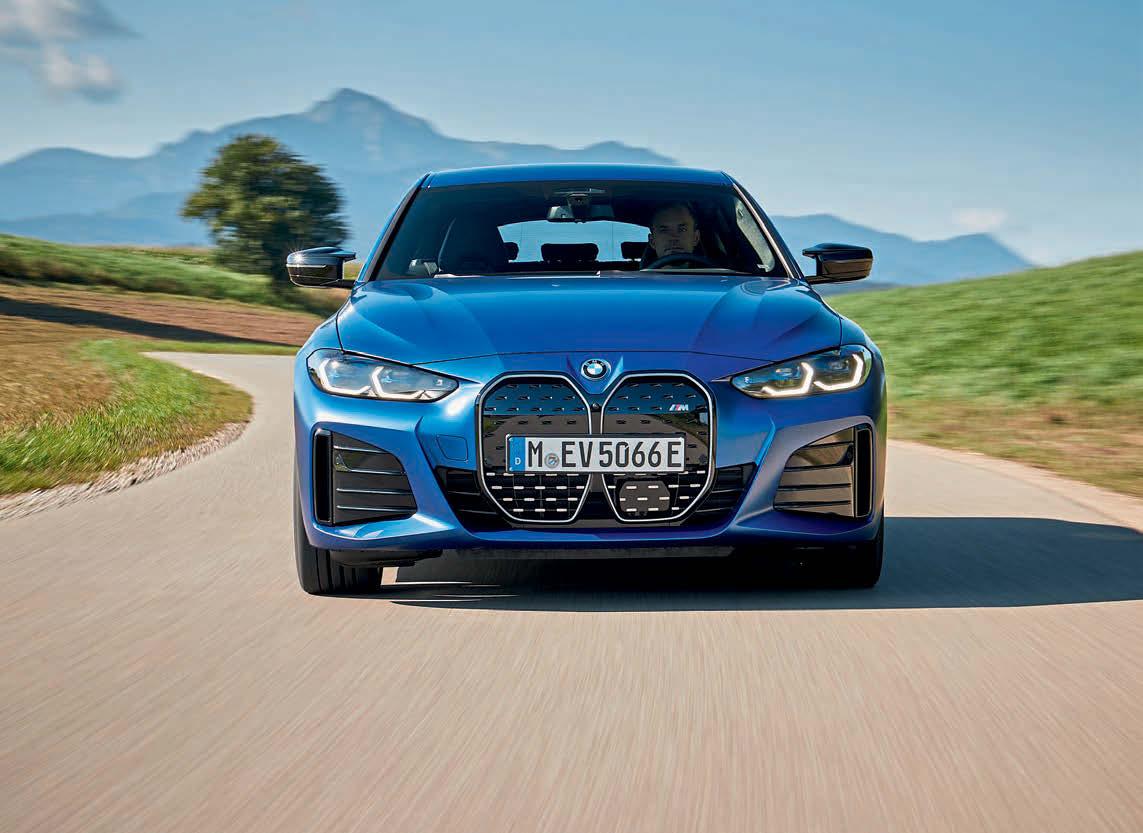
ALL-ELECTRIC
Testing for the next chapter of BMW M's transformation to electric mobility is well underway.
BMW M has started test drive programmes for a next generation of electric cars. M engineers have begun putting innovative drive and chassis control systems to the test, the hardware and software solutions are designed for future fully electric high-performance M cars. The testing focuses on a four-wheel drive system featuring four electric motors and an integrated driving dynamics control system, together these are said to provide an unprecedented level of performance and experience. With this completely new drive concept, BMW M is aiming to transfer the essence of its current crop of M cars into the world of emission-free mobility.
This anniversary year, marking 50 years of M, has already seen the market launch of the all-electric i4 M50 (pictured) performance car and the iX M60. The i7 M70, the first BMW M based on an all-electric sedan platform, will follow next year.
"On our anniversary, we are not only looking back, but above all also looking forward,” said Franciscus van Meel, Chairman of the Board of Management of BMW M GmbH. “Before the end of the year, production of the XM, our first high-performance car featuring a V8 M hybrid drive, will commence. Together with our fans all over the world, we are also looking forward to our entry into the LMDh category of the North American IMSA endurance racing series, in which we will also be competing with an eight-cylinder hybrid turbo engine in Daytona and at other events in 2023, as well as in the WEC racing series at Le Mans a year later.”
BMW M technicians have developed a test vehicle based on the i4 M50, it carries the appropriate kit to test the new drive and suspension technology. The mule features a modified body, with wide wheel arches, allowing for the integration of different front and rear axle designs. The front end features an adapted body strut taken from the M3 / M4, designed for particularly high torsional rigidity. The test mule also replicates the arrangement of the M car's radiator units.
The revolutionary high-performance drive system is described as an electric M xDrive four-wheel drive setup. The four wheels are each driven by an electric motor opening up new possibilities for infinitely variable, precise, and very fast, distribution of torque. Within milliseconds the power and torque of the electric motors can be sent precisely where required on a level that would be impossible using a convention system. This is said to give the driver an entirely new set of performance characteristics – M characteristics.
“Electrification opens up completely new degrees of freedom for us to create M-typical dynamics,” says Dirk Häcker, Head of Development at BMW M GmbH. “And we can already see that we can exploit this potential to the maximum, so that our highperformance sports cars will continue to offer the M-typical and incomparable combination of dynamics, agility and precision in the locally emission-free future.”
When it comes to the integrated control unit, the same levels of precision and speed are found. The electric M xDrive four-wheel drive system uses the four motors connected to a central, highly integrated, control unit that permanently monitors the driving condition and the driver's inputs. Accelerator pedal position, steering angle, longitudinal and lateral acceleration, wheel speeds and other parameters are monitored to ensure the correct level of power is transferred to the road. Signals are transmitted just as quickly and directly via a multi-plate clutch and differentials to the four motors.
Developed via intensive test phases, initially on virtual models and then on test benches, the concept is now being trialled on the road. Inside the four-door mule, extensive measuring technology can be found designed to analyse every driving situation. This allows for the theoretical results from the test laboratory to be compared with the realities of the real world.
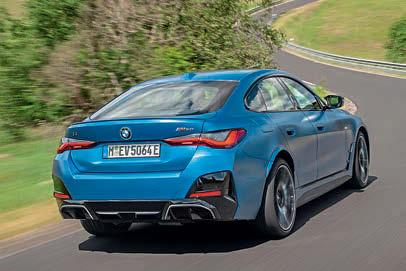
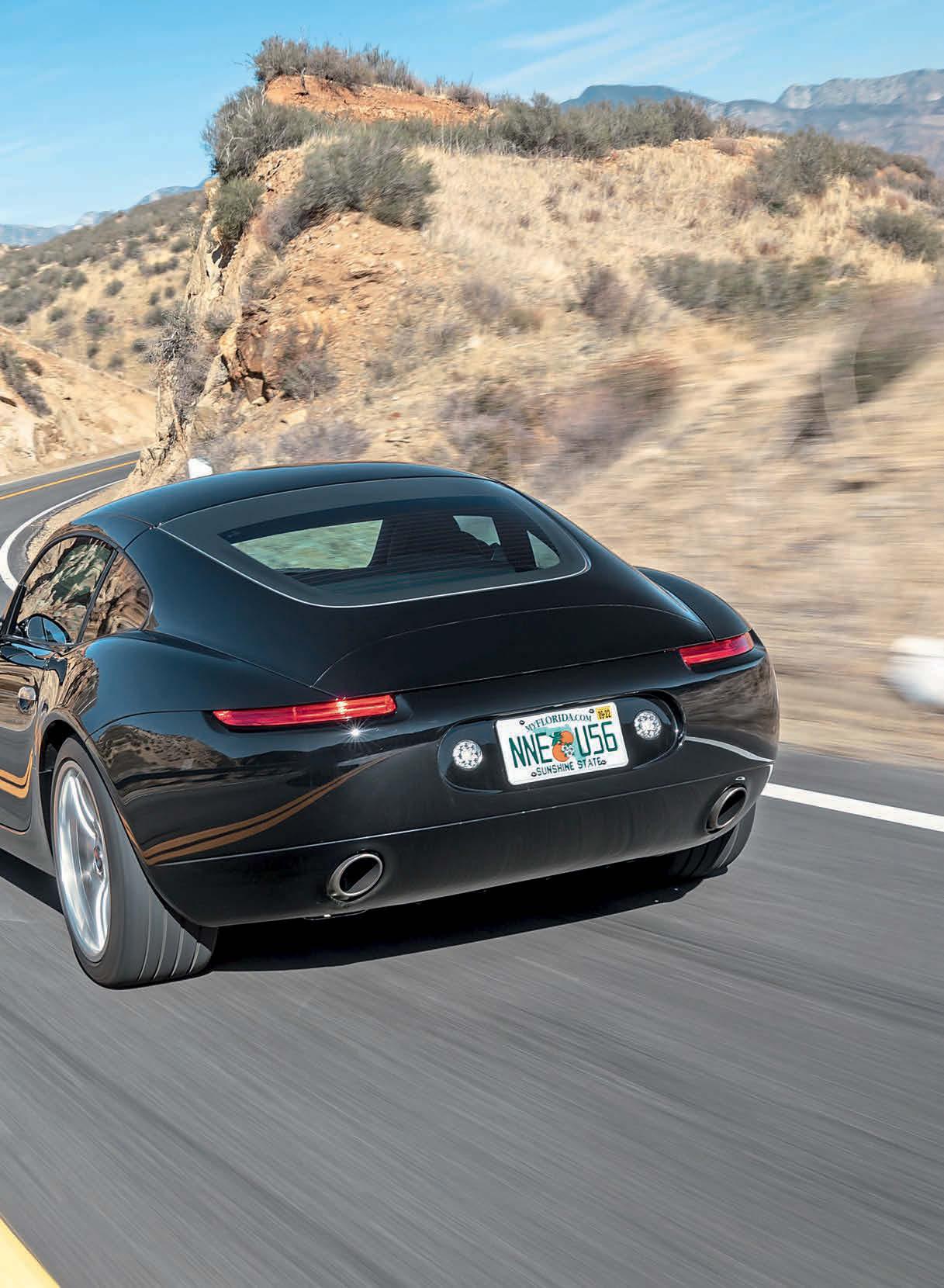
“ t’s the car we wish BMW had made,” admits Willem Smit, who’s
Ione half of Smit Vehicle Engineering. The other, his brother, Kaess, concurs, and the result of some discussions a few years previously is parked nearby as we grab a coffee. We’re on the canyon roads around Palm Springs, the brothers having driven up from San Diego, in their currently one-off, ‘prototype’ Oletha coupé. I can see it from where
I’m sitting, it’s captivating but understated at the same time, a shape that’s familiar but unique, it, say the brothers, is a homage to what a Z8 coupé could have been, and by extension, having 507 Roadster cues to its lines.
There’s no doubt the Smit brothers aren’t alone in dreaming up derivatives of existing products, likely you’ve all done so at some point, I know I have. The difference between them and myself, and, extrapolating here, you, is the capacity to actually do something about it.
Willem’s an automotive engineer, having worked with EV pioneers Tesla, and restomod royalty, in Porsche circles at least, Singer, while Kaess weighs in with some serious engineering nous based around a career in advanced aeronautical composites for a company that had Boeing and Lockheed among its clients. That’s strong engineering pedigree, then, which explains why when Willem had a small off and some panel damage at a track day in his E86 Z4 M Coupé an idea started to form.
“I wrecked up in Sonoma and had to replace the entire side of the car. Doing so meant I knew the quarter panels bolted on and off, which was key, because with many modern cars they’re integral to the body side,” explains Willem. “Dimensionally, being a modern platform and robotically assembled means these cars are very consistent,” he adds, saying that the Oletha’s bodywork is attached to the original body mounting points. Obviously before they got to that stage, the brothers had sat down and worked things out properly, saying: “we started with a wire frame drawing, and asked if what we were considering doing was even remotely possible from a dimensions perspective.”
They admit to loving BMWs, and a family history littered with their own, and parents’ BMW and M cars underlines that, but they wanted to create something with elements of different models. A Z8 coupé, perhaps, the Z8 being a favourite of theirs, visually at least, but they wanted to make it a coupé, and more of a driver’s car than a gutsy cruiser. Using a Z8 as a basis was never going to happen, then, that due to availability, cost, as well as the chassis stiffness. The Z4’s more modern structure, allied to the coupé roof, means the Oletha’s around three times stiffer torsionally than BMW’s open Z8, which, usefully, suited the pair’s dynamic aims of the car more convincingly.
Willem’s eureka moment was a serendipitous result of not just that off, but the realisation that the Z4’s wheelbase was within 3mm of the Z8. Other elements, like the rake of the screen worked, and the drawings evolved into what I’m gawping at in the parking area. And it’s knee-weakeningly gorgeous.
“We had what I think most people would say looks like the car within a couple months and we spent probably the rest of the year refining that,” says Willem. They do concede that to finesse it they did seek out the skills of a digital modeller, who, due to other work must remain anonymous, but they describe that clandestine modeler beautifully as:
“like our hands, the sculptor’s hands,” admitting that they weren’t able to do the kinds of surfacing in CAD (Computer Aided Design) that he could, saying that while they had something that worked proportionally and aesthetically it needed that expert input to get it finished properly.
The result is genuinely stunning. The Oletha’s proportions are spot on, there’s a muscular tautness to its shape, it is elegant rather than aggressive, with some particularly neat detailing around things like the lights, door handles side vent with the integrated Smit roundel badge. Given the brothers describe it as a “prototype” the execution of the build is incredible, the panel fit super tight, the depth of their engineering prowess, and artistry in its execution evident everywhere.
Look at something as mundane as the mechanism and fit of the rear spoiler, which, while sourced from another manufacturer, went through a load-test cycle by Willem’s girlfriend doing 10,000 step ups on a rig mounting of it to make sure it’d work as intended in its application here.
That committed, obsessive engineering-led approach is ever more obvious the more we discuss the car. The panels, all carbon fibre, are sourced in the UK, from a supplier based in Sussex, the Smits having tried numerous potential suppliers in the USA but not finding any able
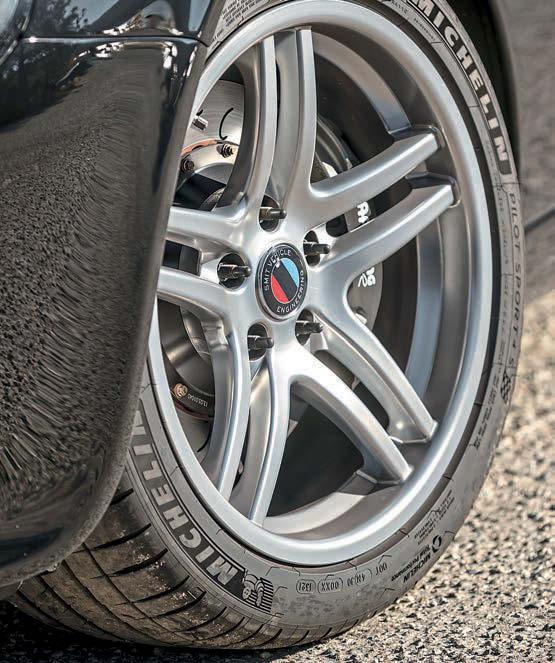
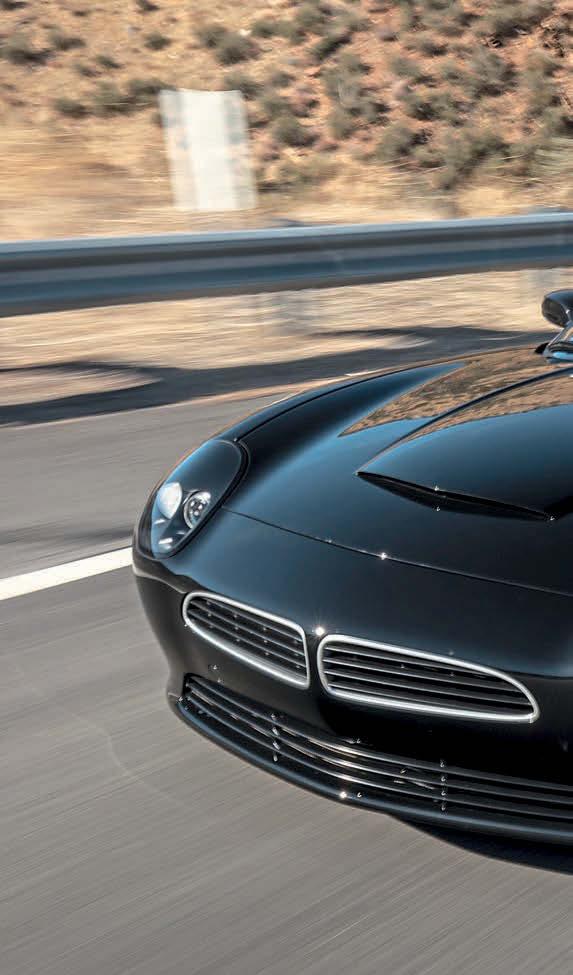
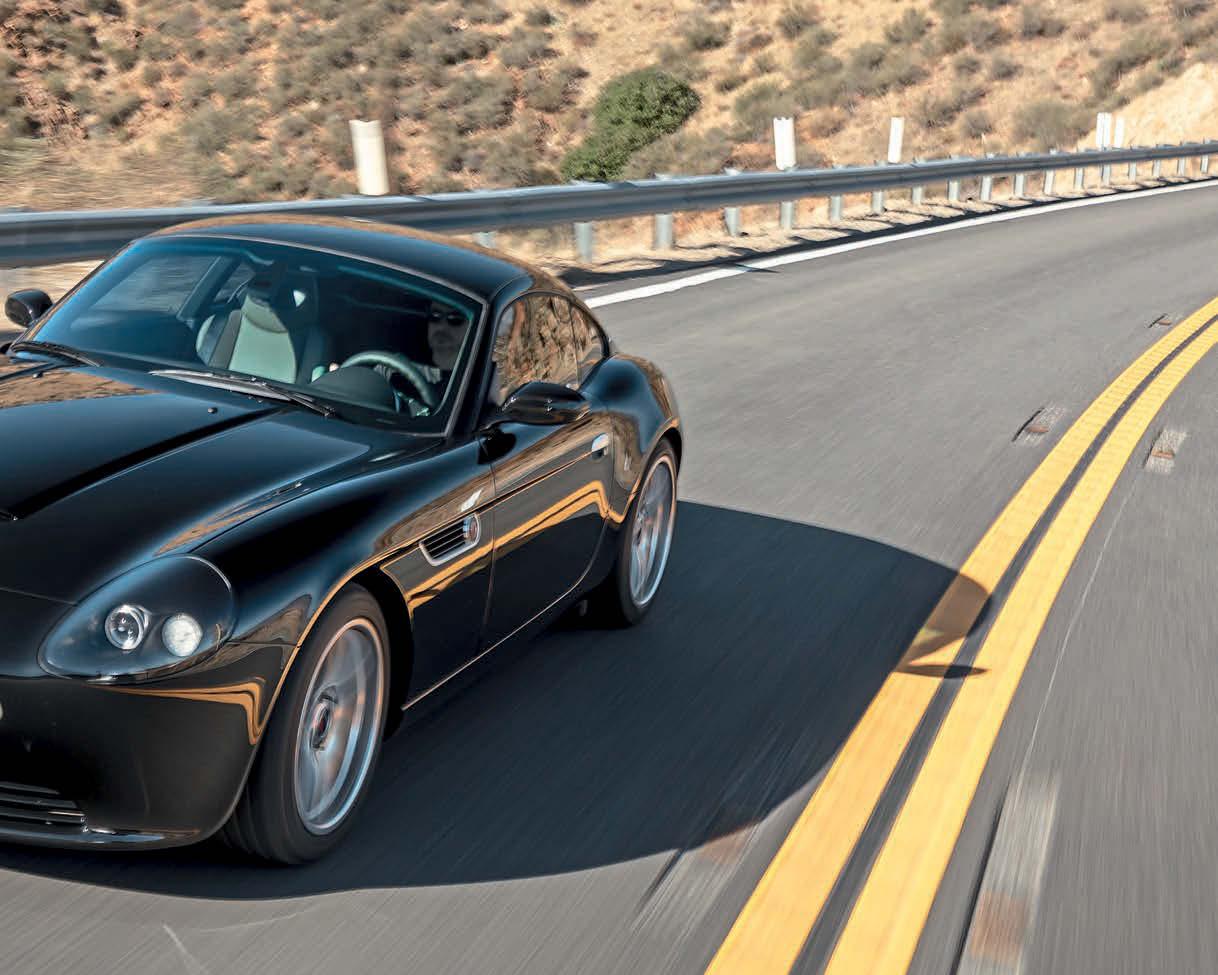
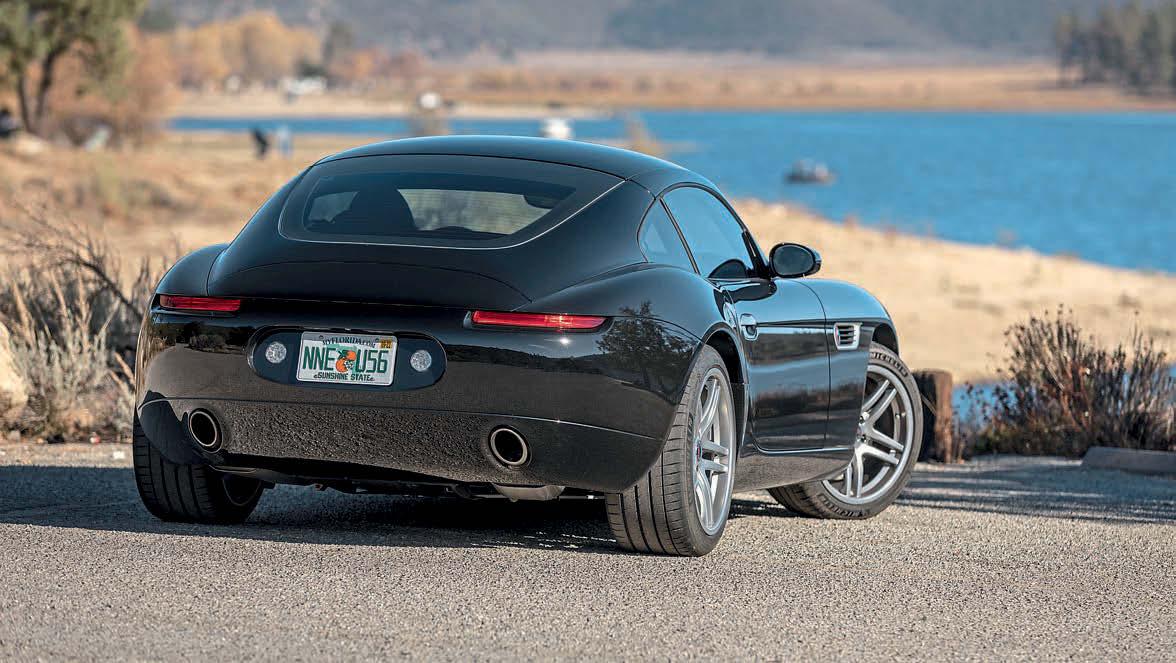
to manufacture the composites to a quality that they demanded. Those panels were designed specifically to utilise all the existing mounting locations and fasteners, their thickness being specific to the load and structural requirements. The glass is carried over entirely from the Z4. Aerodynamic testing revealed that the new body produced around 500lb of lift at the rear axle at 200mph, which explains that pop-up spoiler, it able to be raised manually, or coming up automatically at around 60mph.
They could have stopped with simply re-bodying it, but both brothers enjoy driving, and the thinking behind the Oletha wasn’t just to make it look sensational, but to up the stakes in driver appeal, too. The original goal was to create something similar in focus to a 911 (996) GT3, which leans towards more committed drivers, with a leaning towards occasional track use and some compromises as a result.
For that they needed more power, and while they’ll happily build you one keeping the E86’s S54 in-line six’, they’re also able to slot a S65B44 under the bonnet as here. Naturally it hasn’t been left stock, with the brothers rating their engine at 450+hp, it coming with an 8,500rpm redline, that being 200rpm more than the standard engine. To achieve that it comes with a forged crankshaft, pistons and conrods as well as uprated valve springs and a custom carbon fibre intake manifold.
Getting the electrics to work, admits the Smit brothers, was a bit of a nightmare, and here they sought out some expert help, from someone they found via internet forums. An ex-BMW engineer, who worked previously in research and development had been doing something along the lines of what Smit were after. He wasn’t the type of person to answer emails or talk to strangers, so they jumped on a plane to Germany to go and meet him in person. The result was an electrical kit designed specifically for their application, and crucially, one that uses the factory engine management, underlining that it wasn’t the work of a moment, Smit explains the entire process to get it all to work took two-years.
Naturally that engine is not a straight drop-in job, either, the tolerances under the bonnet are extremely restricted. The hood scoop isn’t just functional, then, it gives a bit of clearance, while the tight fit between the suspension towers meant that Smit tried 25 different manifold iterations to fit them without interference with the chassis. That limited space created knock-on issues with the steering column, and where to place it. Approaching that problem like the engineers they are,
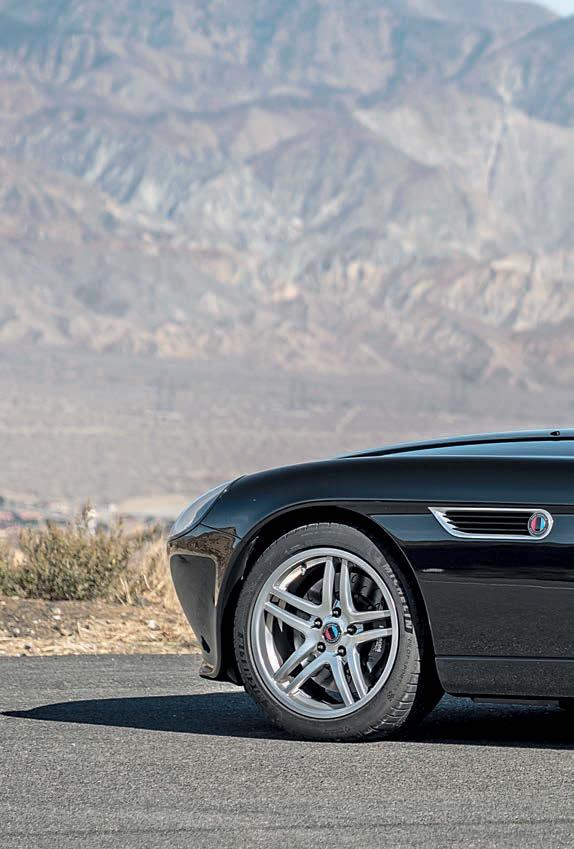
The original goal was to create something which leans towards more committed drivers
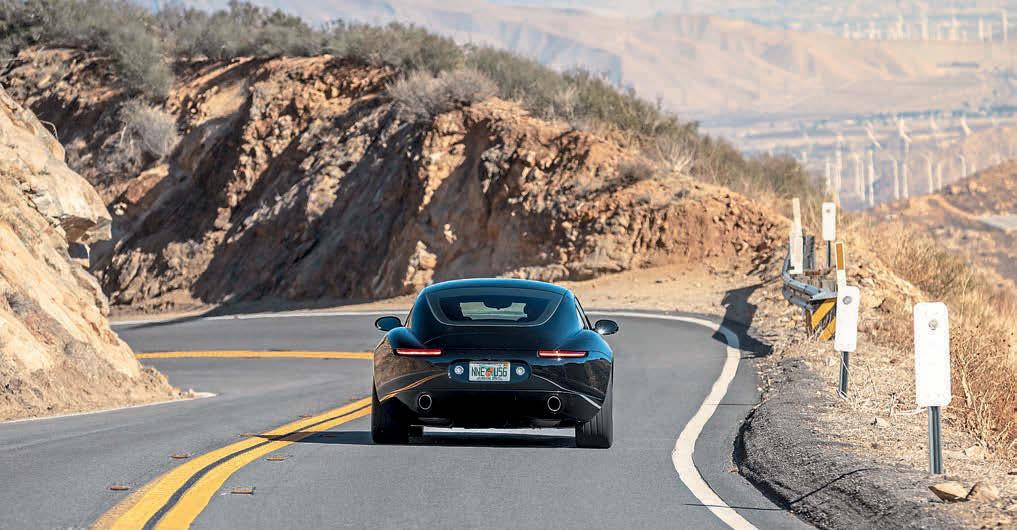
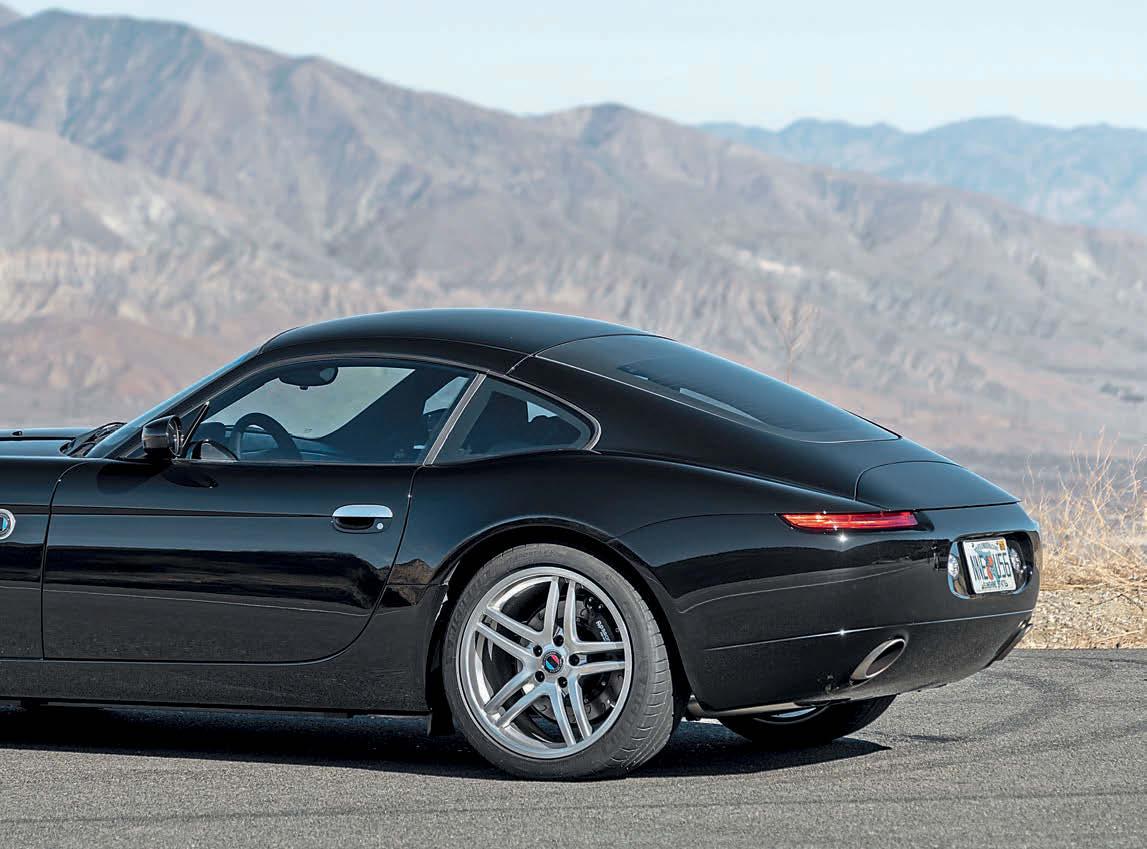
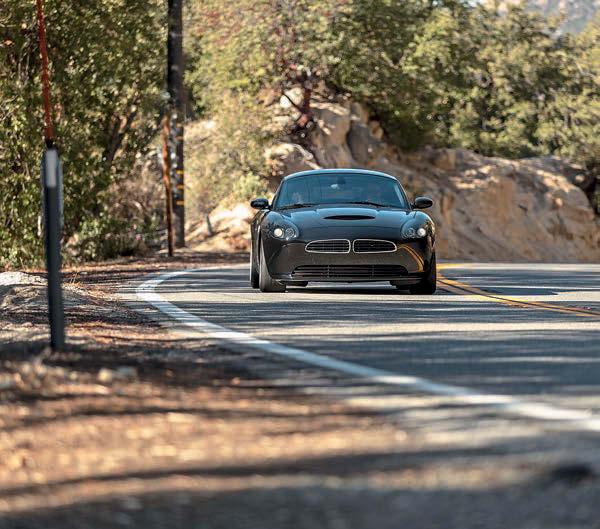
the Smit brother’s solution was to have the column pass through the manifolds, the duo even going to the trouble to engineer it in such a manner that should a buyer want a RHD car, that can be produced, too. Just about everywhere you look under the bonnet, there’s innovative, methodical and tested engineering, with the Oletha featuring over 100 3D printed components, including things like unique engine mounts. Smit is the first company on this scale I’ve visited who’ve shown me CFD (Computational Fluid Dynamics) schematics and have openly discussed things like NVH (Noise Vibration Harshness). That underlines their admirable, obsessive OEM engineering approach to building their car, Willem saying that the while the engine mounts are unique, the bushings are original BMW specification to ensure that the Oletha doesn’t produce any harsh sounds or resonance under the bonnet. The ZF six-speed manual transmission, also pinched from the E92 M3, drives the rear wheels via a mechanical limited slip differential, the suspension being a KW adjustable set up, with the brakes being AP racing items, with six piston callipers up front, and four piston ones at the rear. Those callipers sit behind bespoke, forged and machined monoblock aluminium wheels of 18x9 ET30 front and 19x10 ET20 rear with Michelin Pilot Sport 4S tyres of 255/40/R18 front and 275/35/R19 rear. After the exterior, and under the bonnet the Oletha reveals its Z4 origins and a degree of ‘it works’ pragmatism from the Smit brothers. The cockpit is all but identical to the production car. There is the option of carbon fibre touring or sports seat choices, while there’ll be some re-trimming in finer materials, but otherwise the changes are minimal. That’s not necessarily a complaint, because, in front are BMW’s simple c5789ddb-a5df-4b46-9e84-c56e1e8ad27f c5789ddb-a5df-4b46-9e84-c56e1e8ad27f
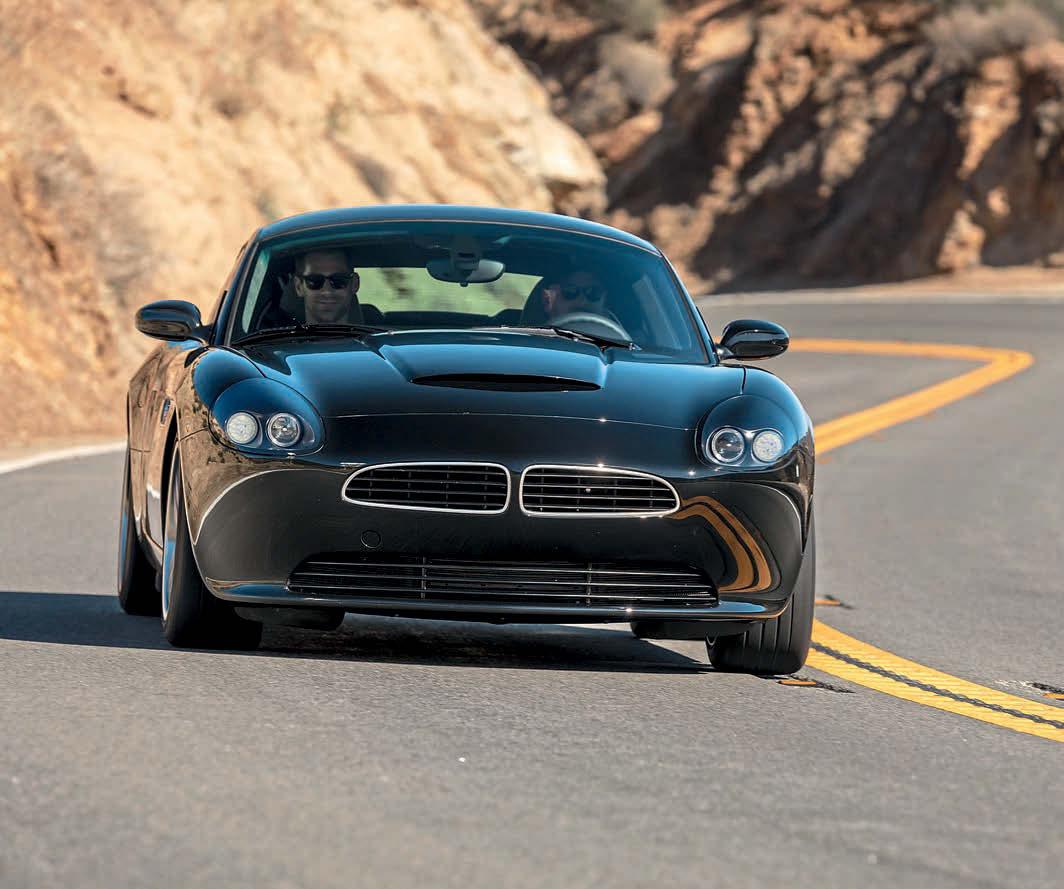
analogue white on black instruments nestled deep in some cowled covers. There are no screens, no distractions, which, these days, is very much a good thing.
As is the sound when it starts. The V8’s note is bassy and loud, not obnoxiously so, but there’s a hint of American muscle over the usual Bavarian culture, and it’s not out of place. Despite Smit’s goal of the Oletha being something to rival something like a 996 GT3, it feels different than that, more like a muscular, but agile, classic GT than a precision, track-biased car. Really, it’s all the better for it, with fewer compromises as a result. Numbers, if you care, suggest a 0-60mph time of around four-seconds, and the top speed should comfortably exceed 180mph. And price? About US $450,000, depending on how you spec it. And do you know what? It feels worth it, too. Before you start doing the maths suggesting you could have a Z8 and more for that, the sort of buyers who’ll be adding an Oletha to their garage are the kind who’ll already own those, and much more besides. The Oletha transcends rational observation and comparison, too, its uniqueness, and the ability to have them build you exactly the car you want being key to its appeal.
Chat over and coffees downed, and on the road what’s apparent is there’s more to it than merely its beauty. There’s a physicality about driving it that’s wonderfully immersive, the Oletha’s throttle response being super crisp, the gearshift perfectly weighted and precise – thanks to some Smit developments in the linkage to improve the stiffness and accuracy – its short throw being quick, it eased by a clutch that’s light but feelsome under foot. There’s clarity in the steering, too, the nose quick to react, again, it delivering faithful turn in via a set up that’s loaded with the sort of detailed feel and confidence-inspiring weighting that’s uncommon these days. The chassis delivers a similarly appealing balance of accuracy blended with sophisticated control, the wheel and body control very well managed. That allows the Oletha to ride convincingly, yet not do so without feeling out of its depth or losing its composure when you raise the bar and start really pressing on.
You really enjoy it without doing so, but the neat trick with the Oletha is the duality it delivers. This is a car that’s able to cover ground quickly and hugely entertainingly with an effortlessness that underlines its integrity. Ask more from it and it just keeps getting better, exploring the upper reaches of the engine’s rev range, above the 5,000-6,000rpm where it feels natural to upshift normally, and where it’s already hauling along at a decent lick, and things get even more interesting and exciting. It sounds phenomenal, too.
Up here the Oletha’s potency subtly changes its character into something even more boisterous and immersive, and something, which crucially, reveals a chassis that’s up to the job of matching the searing performance. It’s that which impresses the most, that, and the fact that this car, the product from the talented minds of a pair of ambitious, hugely qualified and committed driving brothers, is a first attempt. It would be an incredible car if BMW had built it, and it’s even more remarkable because Smit Vehicle Engineering has...
100-year ars of Plant Muni nich
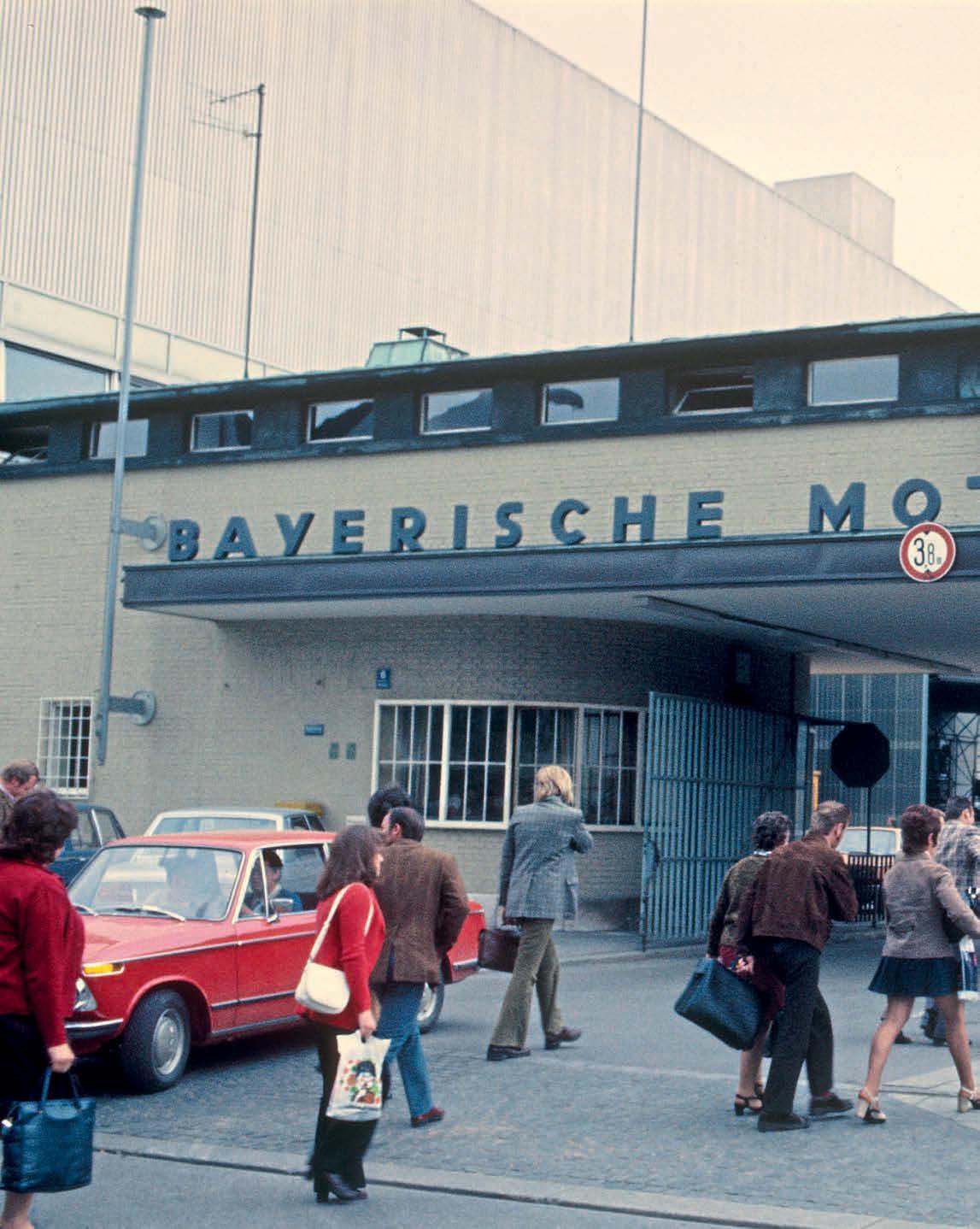
BMW has been building cars at its famed Munich plant since 1922. Now the birthplace of the 3 Series is celebrating a milestone anniversary.
Words: Simon Jackson Photography: BMW Archive
MW is celebrating the
B100th anniversary of its Munich plant. Products stamped with ‘Bayerische Motoren Werke’ have been born at the site in Munich’s
Milbertshofen district since 1922, since then BMW’s most iconic models have rolled off the production lines – ranging from the Isetta to 3 Series and M3.
In recent times the place has been transformed into what BMW calls its
‘iFactory’, by next year half of what it produces will be battery electric vehicles.
In the beginning, aircraft engines and motorcycles were the order of the day.
Just prior to the second world war, the
Munich facility celebrated the creation of its 100,000 BMW motorcycle. Between those dark years of 1938 and 1945 production of both bikes and planes continued, now staffed by forced labour.
Come the end of the war most of the buildings were either completed destroyed or beyond use. Occupied by
American troops, the plant was quickly brought back to life, tasked with the repair of US army vehicles, a permit to restart production of motorcycles and agricultural vehicles soon followed.
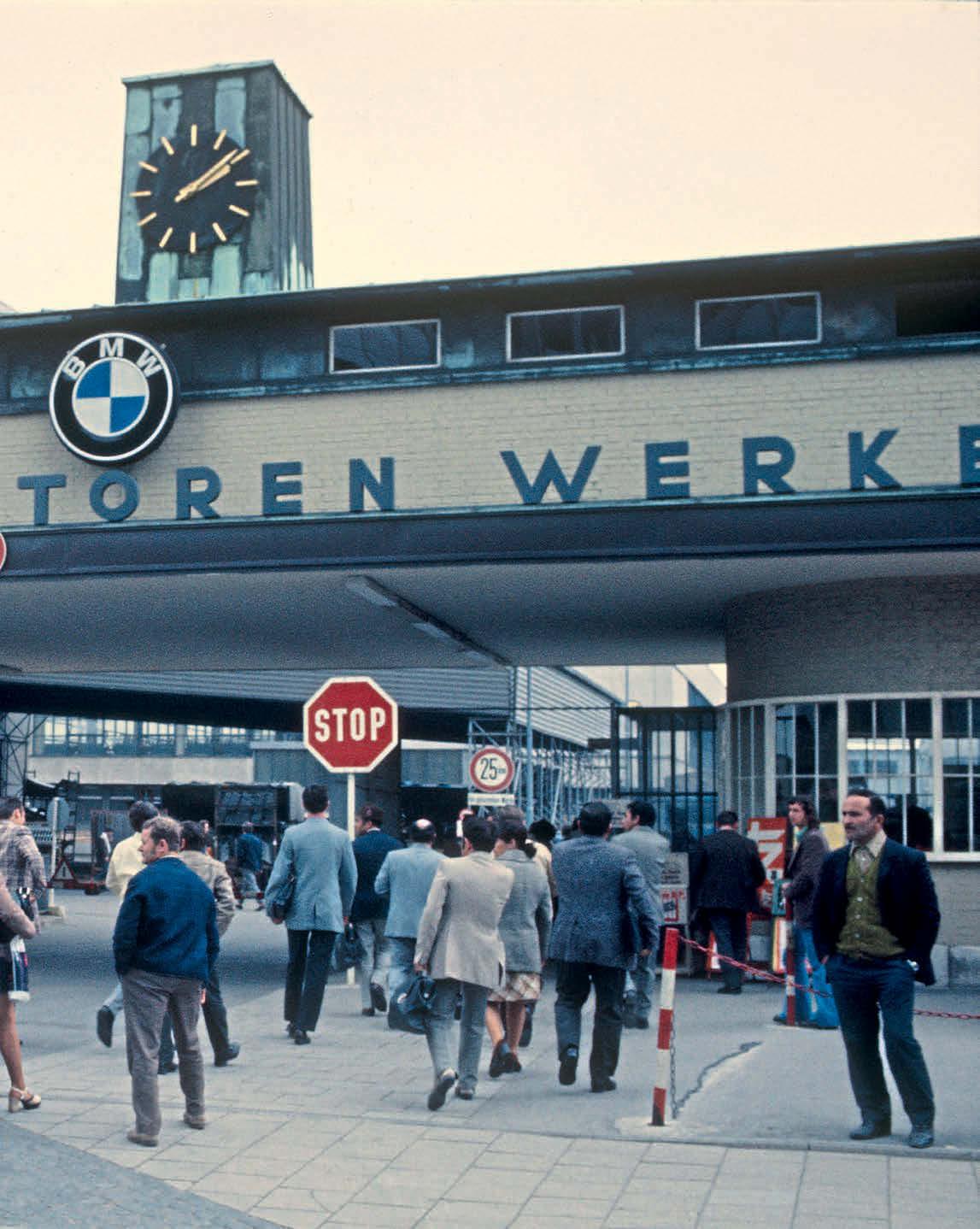
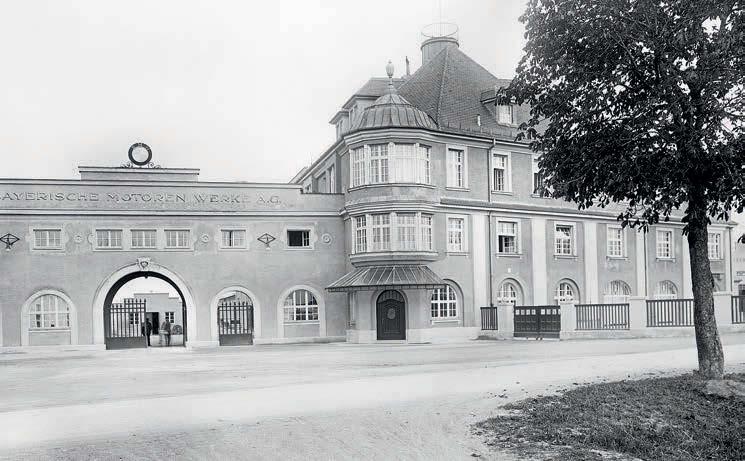
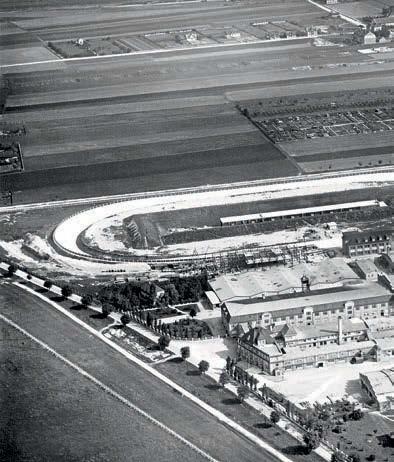
Here: Aerial shot of the facility in the 1930s
In 1952 the first cars were built. The 501 was based heavily on the pre-war 326, perhaps a natural combination of its past, the Isetta ‘motorcoupé’ arrives in 1955 – built under license from ISO in Milan, securing the future of the plant. The Neue Klasse – the BMW 1500 – enters production in 1962 and within three years some 100,000 have been built. At the end of the 1960s motorcycle production ends after 46-years, leaving the Munich site dedicated to building cars.
In 1975 the 3 Series arrives, the plant is reconfigured for the job at hand, and twoyears later it is building the engines for the entire BMW range – 3 Series included. In November 1978, the 500,000th 3 Series leaves the premises. Towards the end of the 1970s things change pretty drastically, old buildings are converted, new ones are constructed and the site’s South Gate on Dostlerstrasse – built in 1934 – is torn down. This lays the groundwork for even larger alterations, in 1981 Building 11, the original structure built in 1913, makes way for further development work.
During the 1990s production is heavily automated, partly to meet demand, partly as a consideration for the plant’s location right in the centre of the Munich neighbourhood. In 2000 a new engine storage facility, IMOLA, arrives. The sophisticated engine logistics setup streamlines engine production for the brand. Just four years later, the plane celebrates the building of its 7-millionth car, make that its 8-millionth by summer 2009. The 2010s see a continual evolution of cars and machinery, in 2014 all-electric trucks begin supplying parts. In 2016, the 10-millionth BMW built on the Munich assembly lines is celebrated. One year later a new paint shop is opened, the state-of-the-art facility is one of the finest in the industry. At the end of the decade comes a new direction. In 2019 the plant produced its highest output yet, some 230,000 cars were built in the calendar year, and following that came the start of another reinvention – this time tooling for i4 production with an investment of 200 million euros.
For 2020 engine production is relocated to sites in Austria and the UK, Munich is set to
The Munich plant has been home to 3 Series production since 1975...
Milestones at Plant Munich
1922: Munich site becomes the home of BMW. 1923: R 32 – BMW’s first motorcycle, is produced. 1934: First large radial aircraft engine is built. 1940: BMW 801 double-radial engine is developed and built. 1945: US troops occupy Milbertshofen plant. 1948: R 24 single-cylinder motorcycle arrives limited by the Allies to 250cc. 1952: The first cars are built, the BMW 501 is an evolution of the 326. 1955: Isetta production starts in April. 1962: BMW 1500 ‘Neue Klasse’ goes into production. 1975: Munich plant is reconfigured for the first 3 Series. 1979: South Gate, built in 1934, is torn down. 1981: The original building, 11, makes way for change. 2000: IMOLA engine storage concept implemented. 2015: Foundation stone for next paint shop is laid. 2019: Buildings and facilities are prepared for the arrival of the i4. 2020: Engine operations moved, new facility is built for electrified vehicles. 2022: Plant Munich celebrates its 100th anniversary.
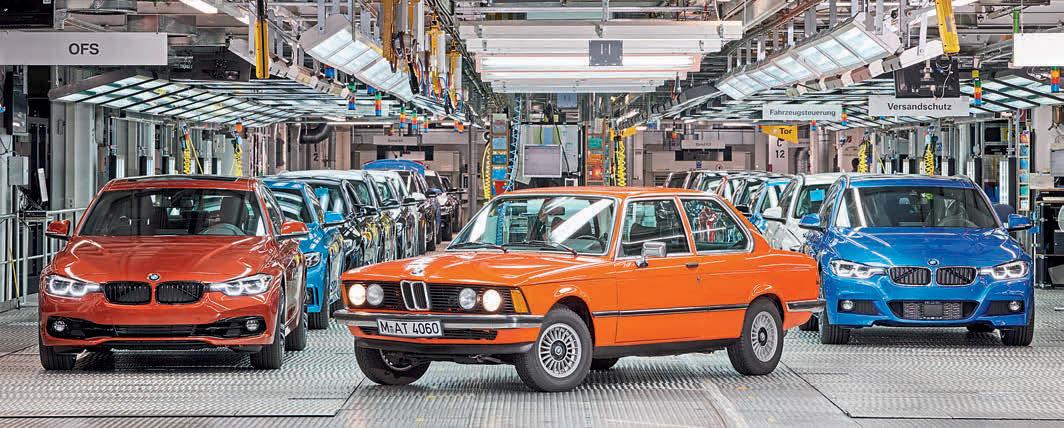
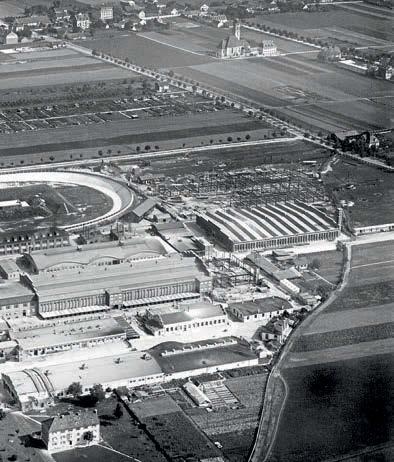
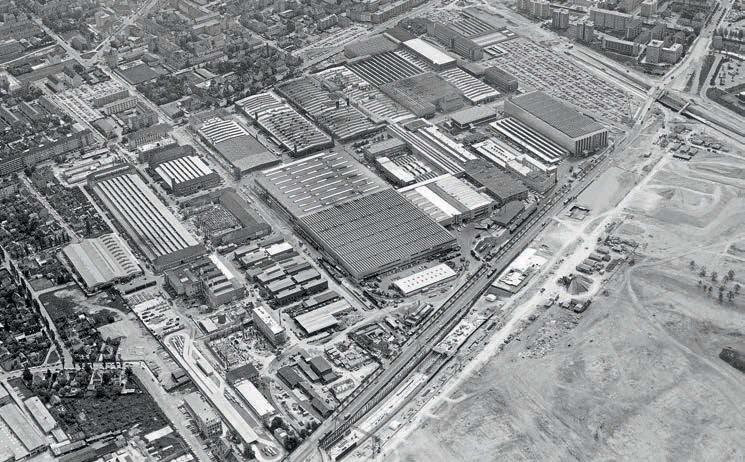
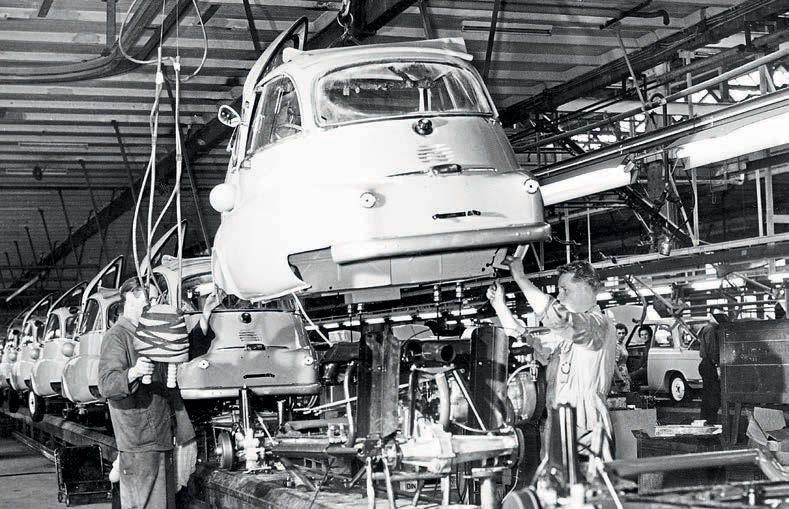
1955 and largely saved the plant from failure.
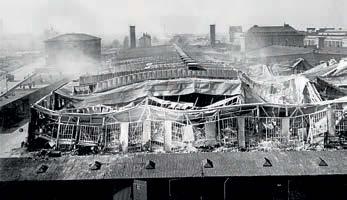
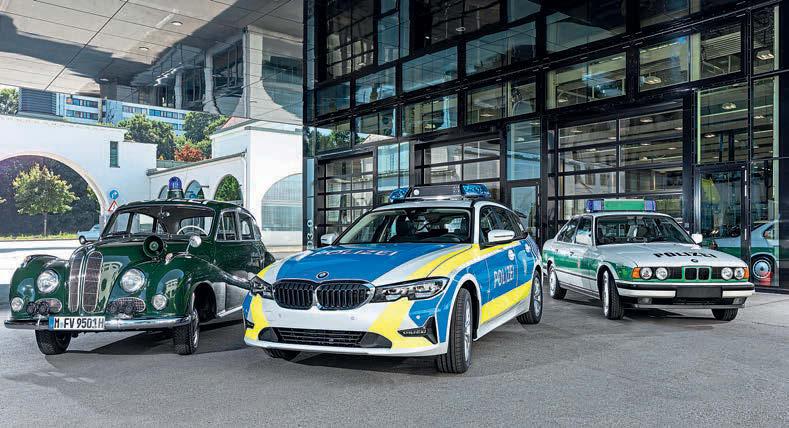
become the home of electrified BMWs and an ambitious schedule launches set to turn the facility on its head inside two years. The old paint shop is replaced by a new bodyshop while two new buildings are constructed to enable series production of a completely new electric vehicle from 2026. With the plan realised, by 2021 five different models are built in Munich, propelled by a mixture of internal combustion, plug-in hybrid and allelectric power units. That brings us full circle, when next month the workforce will celebrate the plant’s 100th anniversary with a special two-day party with members of their family. “Our roots are in Munich. This plant is our origin. And our future,” said Milan Nedeljkovic, Member of the Board of Management for Production at BMW AG: “It’s a high-tech production site. Around 900 top-quality BMWs leave this plant every day. Five different models with all types of drive. This proves c5789ddb-a5df-4b46-9e84-c56e1e8ad27f c5789ddb-a5df-4b46-9e84-c56e1e8ad27f
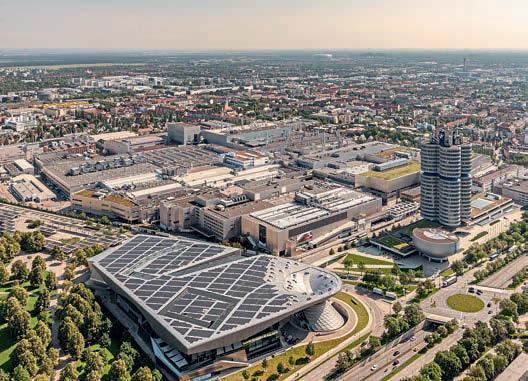
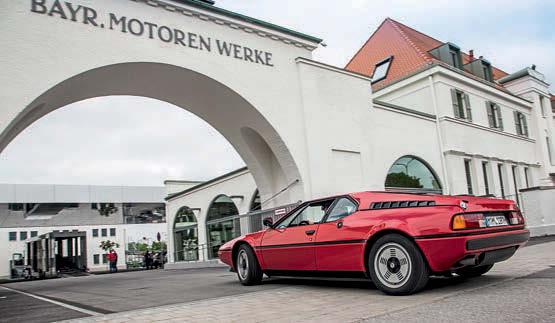
Left: This shot from 2019 shows how the plant sits in the Munich neighbourhood in modern times. Below Left to Right: R 32 motorcycle. The main entrance as it looks today. 1602 Electric hinted at the electric future of the facility.
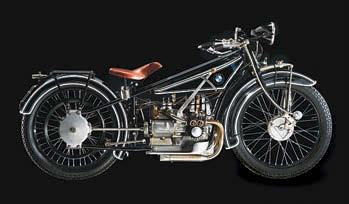
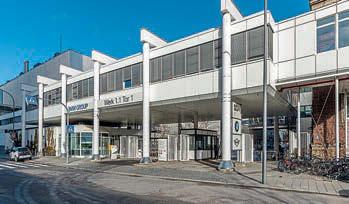
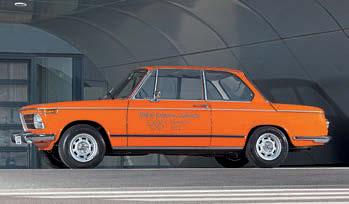
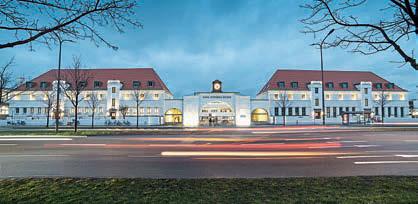
The site has also been home to BMW Group Classic since 2016.
the high flexibility, but also the vast breadth of experience and skills of the people who work here. They are the driving force behind everything that happens here.”
At an event to mark the anniversary, CEO Oliver Zipse said: “Our home plant – right in the heart of the metropolis that is Munich – has defied the elements of time. Because there have always been people who kept this site moving, always with the right instinct for the times and, above all, with a clear view to the future.”
In its 100th anniversary year, the Munich plant is demonstrating the leading role it plays in the age of electromobility. The allelectric i4 already makes up a quarter of the production volume – and rising: “The demand among our customers for the new i4 is enormous – so we’re ramping up production even further. Next year already, every second vehicle leaving the Munich plant will be fully electric. Going by current plans, that means more than 100,000 i4s from the heart of Munich for customers all over the world,” announced Zipse, Nedeljkovic added: “This means that, by 2023, our home plant will already have achieved the BMW Group’s global goal for 2030, namely to increase our proportion of BEVs to 50 percent”.
Innovation has sat at the centre of the Munich site’s philosophy, it has produced the first series of the fully electric MINI E, the iconic Z8, and the electric special edition of the 1602 for the Summer Olympics of 1972. Not to mention Project i, culminating in the revolutionary BMW i3, which also originated at the plant. The transformation into an ‘iFactory’ is designed to make it ‘lean’, ‘green’ and ‘digital’. BMW says that together, the principles ensure that this special site –BMW Group’s century-old plant – will have ‘maximum flexibility, excellent processes and outstanding integration capacities over the coming decades’. BMW and its Munich plant are seemingly inseparable
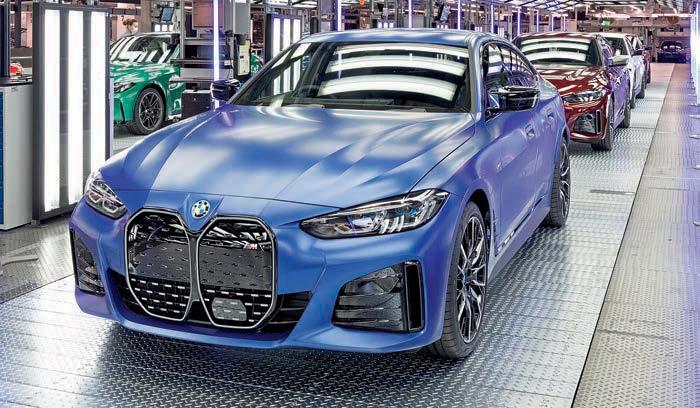
Below: The administration building and body shop at plant Munich in 2022.
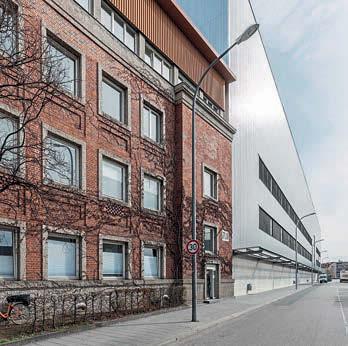