
5 minute read
Construction robots
Robotics automate manual processes.
Although lagging other industries, construction is making strides in automation of certain jobsite functions to increase productivity and minimize the amount of time skilled workers have to spend on repetitive and/or lower skilled tasks. Here are recent additions and updates to robotic technology intended to take some of the manual labor out of the construction process.
Advertisement
HILTI ADDS TO ROBOT DRILLING CAPABILITIES When Hilti launched its Jaibot semiautonomous mobile drilling device in late 2020, it combined building information modeling (BIM) data with reference data from a robotic total station to drill overhead holes automatically. Now, Hilti has added features that enable it to drill even more complex ceiling types while enhancing ease of use and accuracy.
According to Hilti, the Jaibot can now identify and map installed profiles of corrugated sheet metal deck structures, align with the digital plans and automatically adapt planned drill holes to pre-defined installation zones. It is able to detect existing installations or structural elements and adjust its working area and arm movements to avoid them.
In addition, the robot can now drill and mark holes in vertical concrete walls at heights from roughly 3 to 18 ft. The integration of a new sensor system improves hole drilling depth accuracy and distance measuring. As in the past, the robot executes drilling tasks automatically, while an intuitive remote control user interface enables the operator to ensure optimal placement and control.
To automate the jobsite, users upload BIM data from Autocad or Revit to the Hilti cloud application, import the job file via the PLC 400 rugged field tablet for layout applications and locate the jobsite with the Hilti PLT 300 total station. This data is used by Jaibot to drill all holes
PHOTO: DUSTY ROBOTICS
FieldPrinter uses existing BIM designs to print digital building models onto the jobsite floor.
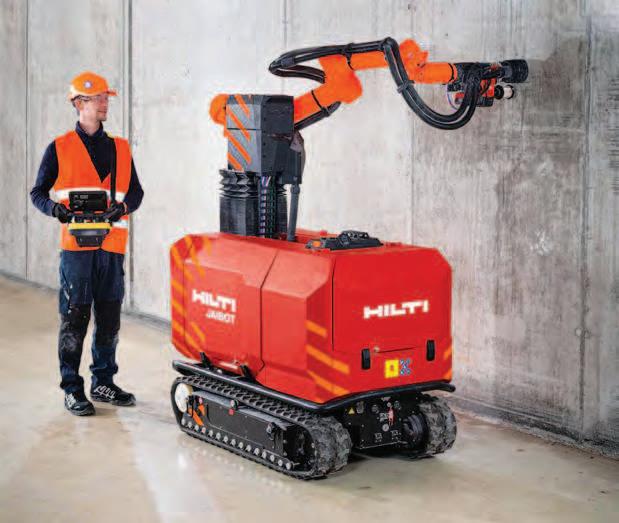
The Jaibot
can now be used to drill holes in sheet metal deck
structures and in vertical
concrete walls at heights from about 3 to 18 ft.
PHOTO: HILTI within its range autonomously according to the digital drilling plan.
New 2D structural floor or installation plan upload options allow for increased background information, improved user management and filtering by diameter to establish a drilling path and plan execution, as well as enhanced reporting with features like Field-to-BIM data and drilling progress. An option to export data and print a 2D plan for potential field rework is also available.
The cordless Jaibot can work for up to eight hours between charges.
FIELDPRINTER AUTOMATES LAYOUT According to Dusty Robotics, its FieldPrinter autonomous robotic solution can lay out floor plans on jobsites up to 10 times faster than traditional manual crews with an accuracy up to 1/16 in.
FieldPrinter utilizes existing BIM designs to print digital building models directly onto a jobsite floor, instructing crews exactly what to build and where. The system requires a control point file, >
which signifies where in 2D space the system is operating. From there, model information is added that can be printed on the floor in DWG or CSV format. Any combination of points, text and lines are printed directly from a CAD file and linework styles can be customized to display layer information, such as wall types or plumbing types. The layout can be completed on flat surfaces including concrete, plywood subfloor, wood formwork and asphalt.
FieldPrinter comes in a customized hard case housing and the rest of the system includes a tripod, total station and ruggedized tablet. Using the tablet interface, the operator has full control over the layout. Once the job is completed, the report generator provides the user with a digital report of the completed work and productivity rates.
Recent advances added to the FieldPrinter technology include: ■ the ability to print around reshores or on congested sites using automatic obstacle detection and avoidance; ■ QR code printing to enable instant access to construction documents; ■ fast, efficient printing including singlepass printing of intersection points; ■ and real-time progress monitoring.
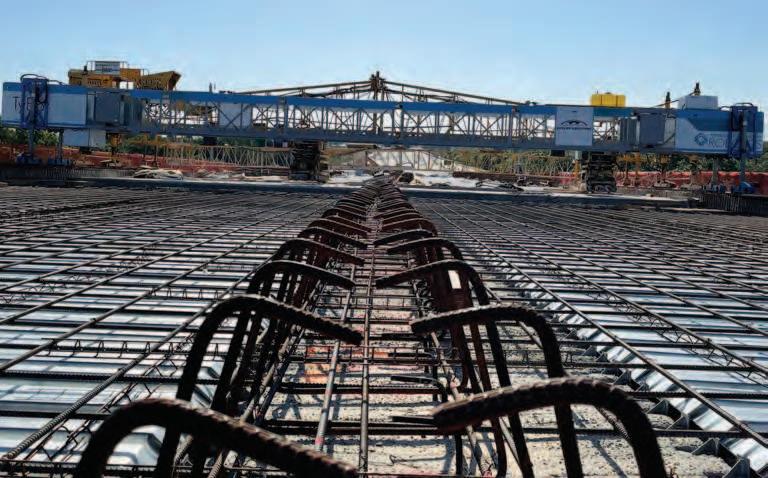
PHOTO: ADVANCED CONSTRUCTION ROBOTICS
SPOT ADDS FLEXIBILITY AND REPEATABILITY Boston Dynamics’ Spot mobile robot has seen a string of advancements since its launch in 2016, largely designed to make it friendlier for the company’s primary market of construction.
Spot is designed to navigate terrain to automate routine inspection tasks and serve as a dynamic sensor to collect data. It is controlled remotely via an intuitive tablet application and built-in stereo cameras, and can be programmed to conduct repeatable, autonomous missions for consistent data capture.
Spot Release 3.0 streamlines automated inspections for even more flexible autonomy and effective, repeatable data capture and processing. It adds new capabilities to Spot’s Autowalk system, including mission editing, mission planning, dynamic replanning around blocked paths and scheduled missions for unsupervised autonomous inspections. It also allows repeatable image capture and live review of computer vision models.
Other new features include the ability to remotely start payloads, configure payload parameters, etc.; remotely operate the optional Spot Arm via Spot CAM integration and split-screen view; and use configurable warning sounds to make bystanders aware of Spot’s movements.
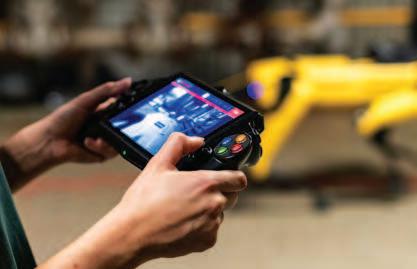
PHOTO: BOSTON DYNAMICS Combining the IronBot and TyBot (shown) on rebar projects will reportedly increase productivity by at least 250%.
IRONBOT TO TAKE ON HEAVY LIFTING Advanced Construction Robotics, maker of the TyBot rebar tying robot, is in the later stages of development on the IronBot, a rebar carrying and placing robot designed to self-place up to 5000 lb. bundles of transverse and longitudinal rebar in horizontal rebar applications. Built for quick assembly and deployment,
Release 3.0 adds capabilities to Spot’s Autowalk system for more flexible autonomy. it can integrate into any jobsite with screed rails, performing the heavy lifting, carrying and placing of rebar while enabling the crew to focus on other tasks.
The new robot will compliment the TyBot, which can self-locate, self-position and self-tie up to 1100 rebar intersections per hour, the company said. The TyBot uses a tram housing a dual camera system that self-identifies rebar intersections. The tram moves along a fully integrated track system to autonomously position the tie module, which ties rebar intersections at 50% or 100% coverage. Power is provided by a 5500 watt, 120/240 V/22.9 amp Cummins Onan generator with a continuous run time of over 12 hours.
When used in combination, the IronBot and TyBot will be able to increase productivity on rebar tying projects by at least 250%, the company asserted.
The IronBot is scheduled to be available in the latter part of 2022. DP
READ MORE ONLINE
■ What are the benefits of autonomy and robotics? - https://bit.ly/3Pjsnpw ■ New features for semi-autonomous mobile drilling robot - https://bit.ly/3JN0xAI ■ How is Spot the robot being used on construction sites? - https://bit.ly/3bJ2CkR ■ FieldPrinter autonomous robot automates jobsite layout - https://bit.ly/3zHpt8i ■ Autonomous robot used on US highway project - https://bit.ly/3Pf0SgI