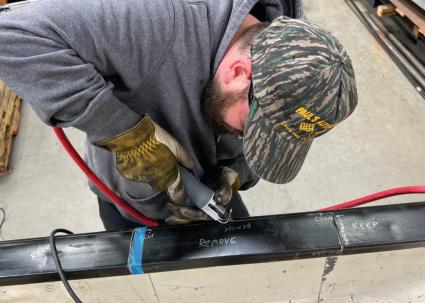
6 minute read
DENTSIDE
D E
2 Tech Gary Hardin used a pneumatic saw to accurately slice panels away from the stock bed of the F-100 in preparation for the shortening of the bed.
Advertisement
3 And so, it began. Here you can see a 16-inch panel that needed to be removed.
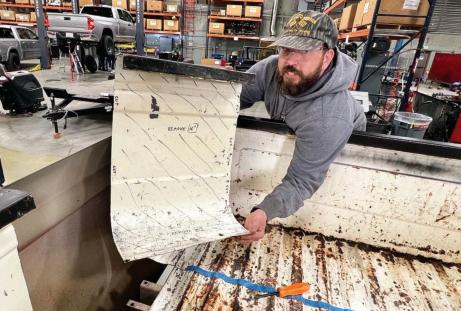
3
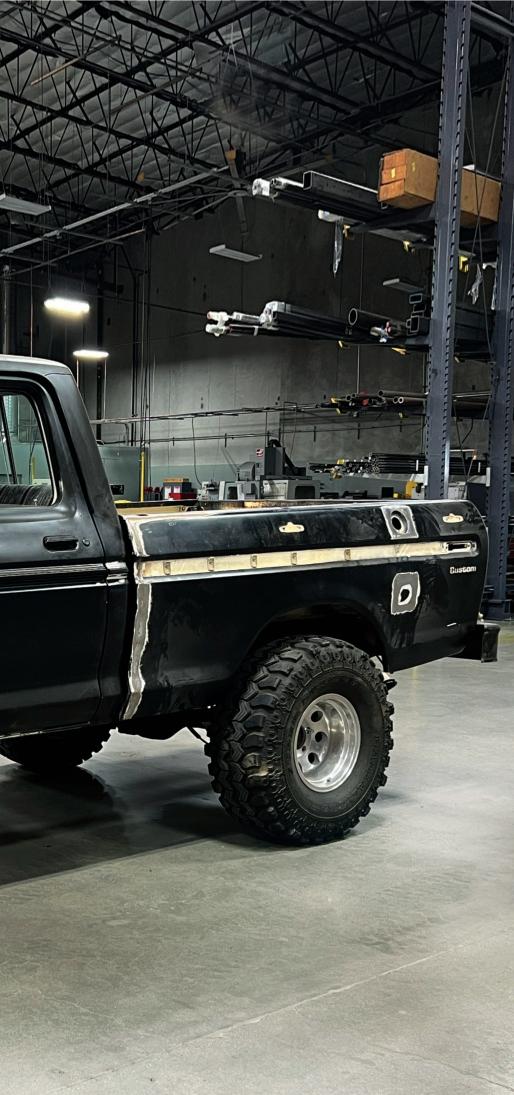
By Ryan Kennelly editor@fourwheeler.com Photos: Ryan Kennelly
In the August 2022 issue of Four Wheeler, we told the story of purchasing a vintage ’75 Ford F-100 Dentside in Reno, Nevada, and the adventure of driving it home to Southern California. In Part 2 (Sep. ’22) we detailed a series of upgrades to the classic Ford, including flooring, gauges, tires, wheels, and more. The result was significantly improved truck that was coming together nicely.
Unfortunately, as we noted at the end of Part 2, the truck was stolen from the owner’s shop. In an effort to recover the truck the owner immediately utilized social media to broadcast news of the theft. The owner reports that the post resulted in over 50,000 Instagram views and over 500 shares in 24 hours. Possibly due to the social media blitz, the truck was found four days later, vandalized, parked on a public street.
History Lost, But a New Direction
When dealing with old vehicles, the more original they are, the better they tell the story. So, we often seek out old trucks that have never been painted. Those beautiful patinas can tell you things like how much time the owner spent under the hood by the scratches on the fenders or the type of things hauled in the bed by the rock chips up high on the bedrails. We were bummed that the thieves had spray painted the whole truck flat black. The original patina was gone, buried under the shoddy spray paint. The loss of patina was one of the things that forced us to change our build plan for the F-100.
We Cut it in Half
At this point, nothing on the F-100 was safe from modification. We decided we were going to “shortbed” the 133-inch wheelbase down to 117 inches. The shorter wheelbase would be more fun off-road and a 6-foot, 8-inch bed would still be longer than most modern 1⁄2-ton trucks on the road today. In order to remove 16 inches from the truck we needed a plan of attack. Starting with the bed, we marked up the puzzle pieces so the feature lines would all come back together. We created a set of 16-inch calipers to lay out the cut lines. Once marked, we used an air-powered saw to disassemble the 8-foot bed. Each part was neatly set aside until the dissection was complete.
More Modifications
While the bed was apart, we decided to move the filler neck so California-compliant fuel pumps could quickly fuel up the highcapacity fuel tank. This meant removing the fill location, patching the holes, and reinstalling the fill location up higher to add some draft to the fill neck. This also meant we needed to create a new fill neck. The 2 1⁄4-inch stainless-steel mandrel-bent tubes would test our welding skill to create the new fill tube. F-100 shortbeds didn’t
4 Plug welds that were drilled out and relocated during the sheetmetal surgery needed to be filled in.

4 6 5 7
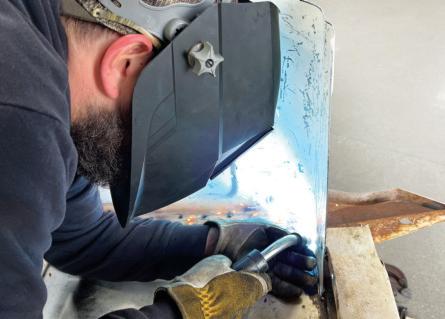
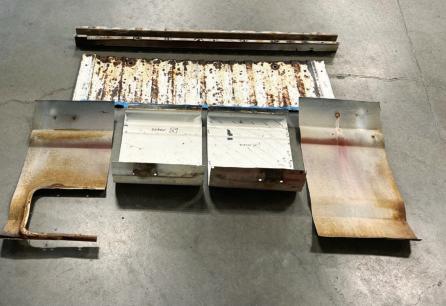
6 The new seams in the bed were trigger welded. 7 All total, 120 pounds of material was removed during the shortbed conversion.
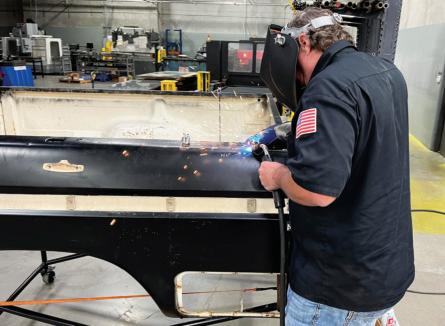
8 Custom tools were created to lay out the frame cut path.

9 A 1 1⁄4-inch hole saw was used to create the radius in the Z intersections.
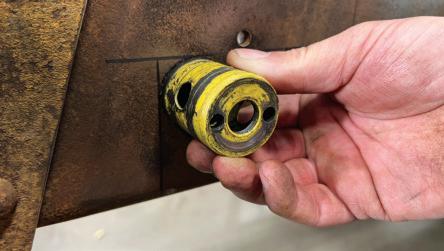
8 9
come with a side toolbox so we chose to keep that. This meant we would need to build the smaller door frame and shorten the door in two places to center the latch.
The Reassembly
With all our puzzle pieces dry fit, we used butt welding clamps to hold the front of the bed to the main assembly. All the feature lines aligned nearly perfect. The corrugated floor terminated at the front wall as if it was factory. With all parts tacked in place, a series of tacks commenced moving around the whole truck to avoid distortion from heat. Once all the voids were closed, the welds were carefully sanded. The bed was now 16 inches shorter, but we weren’t done yet. The frame needed to be shortened.
As If Ford Planned It
Looking closely at the frame while the bed was off, we noticed the fuel lines, brake lines, and e-brake cables all had junctions right where the frame was about to be shortened, as if Ford had planned for this to happen. The frame itself would be a bit harder. The framerails seemed to be uniform in shape, but the frame had a taper from front to back. This meant we would need to cut a wedge in each framerail and close the distance between them as they neared their new intersection. This made creating a “Z” shaped cut a bit trickier. The “Z Method” is the preferred cut to reduce fatigue at the heat affected areas during welding. After a series of complex cuts, bends, and additional plating, we had what we needed. Read on to see some random highlights of the latest mods to our F-100.
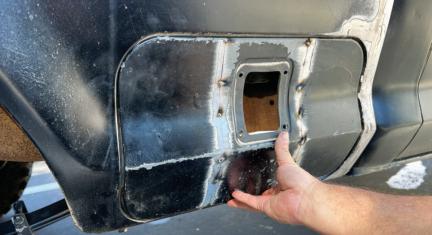
10 11
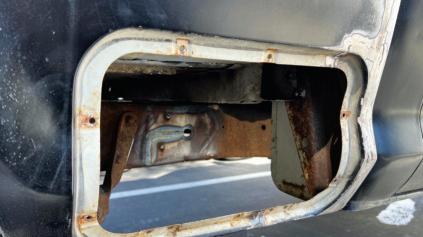
10 We wanted to keep the bedside toolbox, so we shrunk it to coincide with the shorter bedside. 11 The toolbox lid needed material removed before and after the latch to look correct.
12 After welding all the frame joints, a fish plate was added to the inside to increase strength.
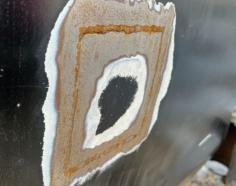
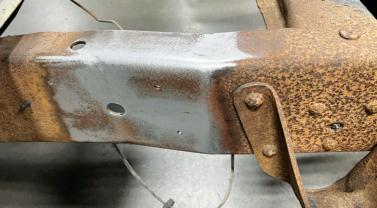
BEFORE
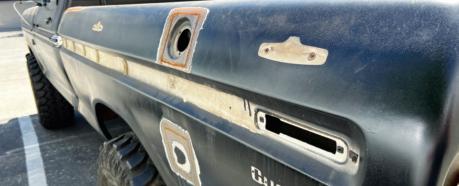
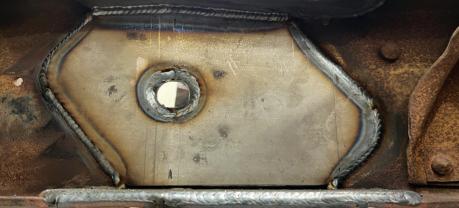
12
14
13 The outside surface of the framerails was sanded and polished to appear unmodified. 14 The fuel fill neck hole was relocated to promote easier filling when using California fuel pumps. 15 The bedside panels that were removed to install the fuel fill neck holes were repurposed into the original fuel fill location. 15


Before And After
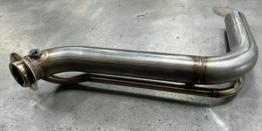

Here you can see a photo of the F-100 prior to being stolen and how it looked when it arrived on a flatbed after being recovered. Prior to it being stolen, several upgrades had been completed, including some new wiring, a new battery and mount, a new gauge cluster bezel and LED gauge lights, carpet, several suspension components, wheels, and tires. Among other things, the thieves absconded with the wheels and tires. And in an apparent effort to conceal the truck’s unique identity it was spray painted flat black.
16
17
16 A cover plate was fashioned from a bedside to close up the bed were the filler neck protruded through the inner bed. 17 The stainless-steel mandrel-bent fuel fill tubing tested our welding skills.
What’s Next? The new wheelbase looks great, but we are a long way from finished with our F-100. As much as we would like to finalize the cosmetics of the shortened Dentside, we need to attack the drivetrain. In preparation for that we’ve gathered tough aftermarket upgrades to build up the vintage axles. Keep an eye out for the next installment as we set up ring-and-pinions and install lockers and chromoly axleshafts. FW