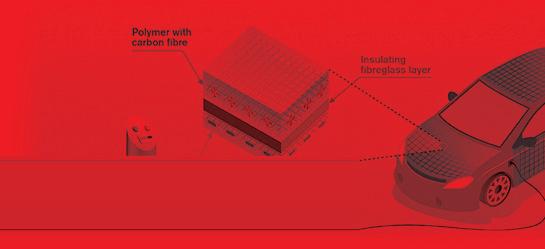
4 minute read
Technologue Structural battery components look to revolutionize EV energy storage.
from sin46th magzud.org
by Thomas Swift
Frank Markus Technologue
Structural battery composite promises “massless” energy storage.
Advertisement

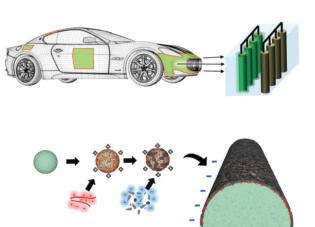
’ve covered various technologies that promise to Ilower the mass and/or increase the energy density of electric vehicle batteries, so my interest was keenly piqued when I recently learned of research out of Chalmers University of Technology in Gothenburg, Sweden, on a concept for “massless” energy storage. Sounds even lighter than lithium air!
The first thing to know about the “structural battery” is that it is not actually weightless. Rather, as the name implies, it can be used to replace various mono-tasking structural panels in use today with structures that can also store energy. They’re part of a new class of multifunctional composites called structural power composites, capable of storing electrical energy in a capacitor or battery.
Airbus aims to launch an all-electric 100-passenger regional aircraft by 2050, but replacing the 60 pounds of jet fuel per passenger with batteries would require almost 37 times as much weight. Such a plane could never get off the ground, but what if it featured a slightly thicker structural battery composite (SBC) fuselage that also functioned as its energy storage? Or what if those 100 seat frames on board were made of SBC?
Raw, uncoated carbon-fiber strands are great electrical conductors, and because they typically include tiny voids that can easily accept lithium ions, they function well as a battery’s negative electrode. The carbon fibers do grow slightly during lithiation, however, so that expansion must be factored into any design.
Employing electrophoretic deposition to apply a lithium-iron-phosphate/grapheneoxide coating onto carbon-fiber filaments allows them to serve as a structural cathode. Voilà! Now all that’s needed is an electrolyte that can also function as a structural resin, and the Swedish gang has identified a polymer electrolyte with a cross-linking monomer that enhances the material’s structural rigidity while still conducting lithium ions.
In the current research state, Chalmers’ structural battery stores about 24 watt-hours per kilogram, but the team expects to hit 75 Wh/kg by 2023—still about a third the density of the best lithium-ion cells. That lower energy density means the SBC materials are less likely to experience thermal runaway, but there remains a concern that they could give off toxic fumes if they catch fire.
The strongest carbon fibers don’t store energy well, so today the SBC version of the material has about one-third the static tensile and compressive strength of an aluminum panel of equivalent thickness. But by next year, the team expects its SBC to reach structural parity with aluminum while equaling the yield strength of steel. Chalmers professor Leif Asp says that although SBC material can be curved and shaped like other composite materials, sharp bends increase the risk of short-circuiting the cell.
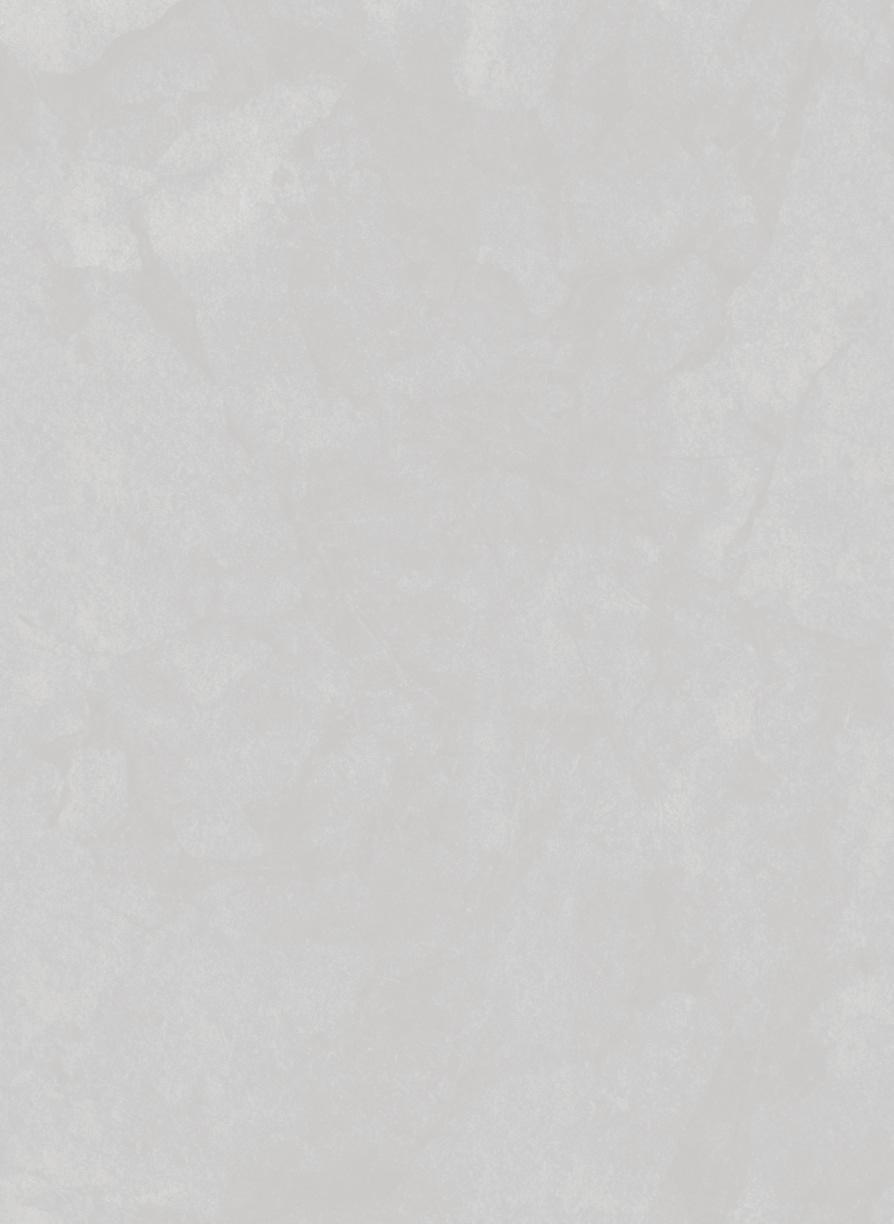
Carbon-Fiber-Composite Car Distributed Structural Batteries
LiFePO4 in DMF Electrostatic Self-Assembly Electrophoretic Deposition
PDDA in H2O EGO + CB in DMF Carbon Fiber
A paper published by Chalmers researchers looked at the effects of removing the battery packs and incorporating structural battery composite materials into a Tesla Model S (with an 85-kWh battery) and a BMW i3. By replacing roughly 70 percent of the interior and exterior panels and 60 percent of the body structure with SBC, the mass of these cars drops by 26 and 19 percent, respectively, while the predicted New European Driving Cycle–rated range drops by 36 and 17 percent. But doubling the thickness and mass of these SBC panels brings both cars back to mass parity while boosting range by 20 percent in the Tesla and 70 percent in the BMW (not to mention adding foot room by eliminating the space-hogging battery packs). Replacing a worn-out structural battery might sound more difficult than unbolting a battery box and swapping out cells, but then modern EV batteries seem to be lasting the life of the car anyway. Nevertheless, structural battery usage might best be restricted to easily replaceable items like seat frames, door panels, and perhaps the hood, roof, and floor panels, rather than integral structures like pillars and crash rails.
How soon might we see structural batteries enter production? Chalmers University’s Asp reckons SBC could arrive in laptops, phones, and toys within two years, with aerial drones following in 10 years and EV traction batteries sometime after that. Additional R&D is required to prove the long-term durability and capability of the SBC, not to mention issues related to scaling for manufacture, managing power and connectivity, and recycling. Predicting the cost relative to today’s battery and body structure costs is also difficult because of unknowns such as the price of solid-state batteries and other potential future battery chemistries that may lend themselves to structural battery integration.
We are rooting for structural battery composites and similar two-birds/one-stone tech that helps democratize electrification. Q