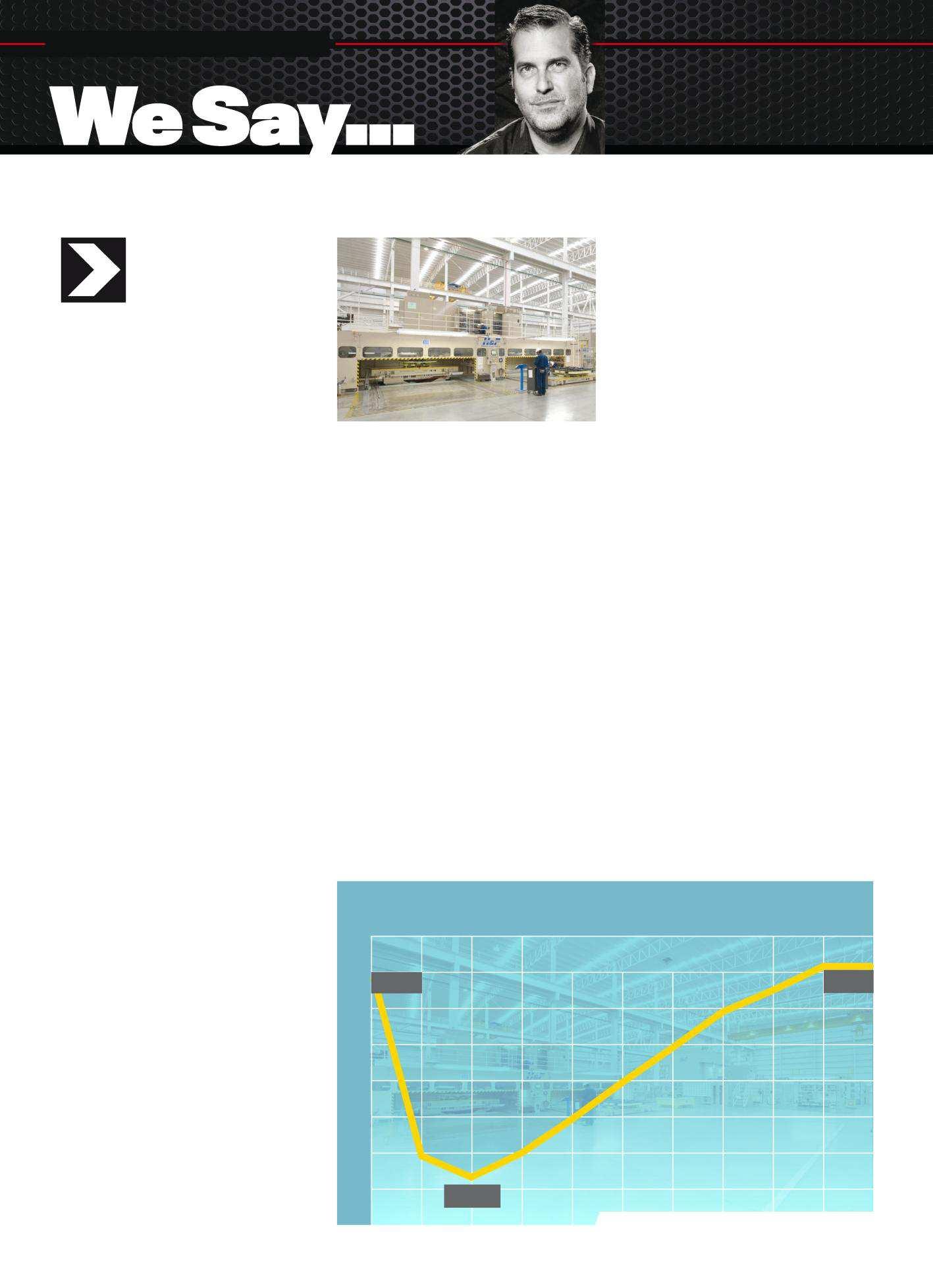
3 minute read
Mark Rechtin REFERENCE MARK Jobs Jobs Jobs But where are the workers?
from 5t67
by Thomas Swift
“Build it where you sell it” used to be the motivation for foreign automakers to bring plants to America—as well as to avoid transport costs, to achieve quicker-to-market timing, and as a hedge against currency-exchange fluctuations.
But today, it’s simply cheaper to build cars here than it is in South Korea or Germany or Sweden.
Advertisement
Automakers might have taken a breather during the devastating recession of 2008–2010, laying off hundreds of thousands of auto workers as vehicle sales plummeted and the need for second and third production shifts waned. But auto factory employment is now at a higher level than before the last sales peak—just before the economy collapsed in 2008, according to the Bureau of Labor Statistics (see chart below).
It’s good news for American workers that there is a new Toyota-Mazda plant in Alabama, a new Volvo plant in South Carolina, and an expansion of Daimler’s operations in Alabama. In fact, in some auto sectors there are more jobs open than there are qualified workers to fill them. Why? Put simply: poor skills and low wages.
Auto manufacturing expert Mike Robinet, managing director for data giant IHS Markit, says some automakers have had to delay production or miss a third shift because they (or their suppliers) couldn’t find enough trained or trainable people and thus suffered shortages of labor or critical parts. He cites Denso’s new $1 billion plant in Maryville, Tennessee, which will build battery inverters and power supplies, as having to “import” people from outside the Knoxville area to fill the 1,000 jobs that will staff the plant.
A Denso spokesperson responded that the company “is not ‘importing ’ workers,” merely “adding new strategies to reach a larger radius or market than in the past.”
Tomayto. Tomahto.
As early as 2014, there were signs that America might lack the skilled and semi-skilled laborers needed to fill its available auto jobs. That year, I attended a gathering of the Japan-America Society of Indiana, where executives from three major automotive suppliers—Aisin Seiki, NTN Driveshaft, and Enkei America—said they couldn’t fill key positions at their southern Indiana operations because there weren’t enough qualified applicants.
Well, sort of.
It used to be that, back in the golden age of manufacturing, skilled workers on the assembly line received a respectable blue-collar wage, owned a home, and sent their kids to college. But recent recessiondriven labor contracts (or lack of labor influence altogether) have allowed automakers to drive wages down— especially for newcomers to the factory.
New plants are good news for U.S. workers. In fact, in some sectors there are more jobs than qualified workers to fill them.
The average hourly wage for an autoworker in America was $22.09 in 2008, a number that has inched to $22.39 over the past decade, according to the Bureau of Labor Statistics. But if wages had merely kept pace with inflation, they should average $25.94 an hour today.
Remember, this is an average. Lots of grandfathered workers with seniority make well more than this amount. But many of the new auto jobs being created are actually in the $9 to $15 per hour range, according to a recent piece of investigative reporting by Bloomberg Businessweek. That’s not much incentive for a skilled job seeker seeking to support a family. And lowering the bar for new employees willing to accept those wages means the industry has to deal with less qualified candidates, higher absenteeism, and failed drug tests, Robinet says.
Of course, certain economic supplyand-demand theories contend that with 4 percent unemployment and jobs going begging, automakers and suppliers might have to sweeten the pot a little to bring in new hires.
What’s good for GM (and Ford and Toyota) is good for America. But more to the point, what is good for American workers is good for America, too. They should be treated accordingly, both by training and by what they earn. It’s great that auto jobs are back. Now wages need to follow suit. Q
EMPLOYEES U.S. motor vehicle and parts manufacturing
1000
950
946.5 In thousands, seasonally adjusted
955.1
900
850
800
750
700
650