
6 minute read
Before Blasting
Before Blasting Away
Pre-sandblasting tips
Advertisement
BY JOHN GUNNELL
Dave Wallendal had to install new rubber blast gloves in the Trinco cabinet.
Media blasting cabinets can be purchased from any number of brick-and-mortar retailers, swap meet vendors or catalog houses. They are impressive-looking devices with holes in the front for attaching rubber gloves, doors on the side (and sometimes liftup fronts), large glass windows to see inside, air pressure gauges, hoses to get compressed air to the proper places, foot pedals that are stomped on for air pressure, and large dust collectors with lter bags inside to catch debris.
The media blasting concept is simple. Fill the cabinet with blast media ranging from gentle glass beads to more aggressive aluminum oxide, and the compressed air forced through the hoses and blasting gun directs the media against the parts in the cabinet, stripping them of rust, dirt, paint, primer and body ller to get a clean part. Depending upon the roughness of the media, the part may end up with a smooth, shiny surface (with glass beads), or a gray color and slightly rough texture (with other media).
Chances are good that the rst time you blasted with a brand-new cabinet, you were amazed by how fast the metal became clean. You watched the media virtually erase unsightly debris from old parts. The view through the inspection window was clear, and you could see where the most blasting was needed. It was a positive experience.
Later, you noticed that it was getting harder to see through the inspection window. Then, you realized that your “eraser” wasn’t doing the job it once did. Some parts wound up with hard black grease residues that the blast media didn’t seem to remove. You could no longer see a steady stream of media ying out of the gun. Later, you could sense that some really rusty spots on the parts weren’t cleaning up as well as they once did.
A drop in blasting ef ciency can get noticeable after a while, and several hobbyists have reacted with some creative solutions. One man, who had worked all his life as an engineer, cut a hole in the back of his media blasting cabinet and mounted a sandblasting tank in the opening. It works great. Another British car
Wallendal drilled a hole in front of the white cabinet to install a pickup bracket. The white cabinet is the older, extra-large Eastwood model that needed service work. The gray Trinco cabinet is sold by Metal Finishing Supply Co.
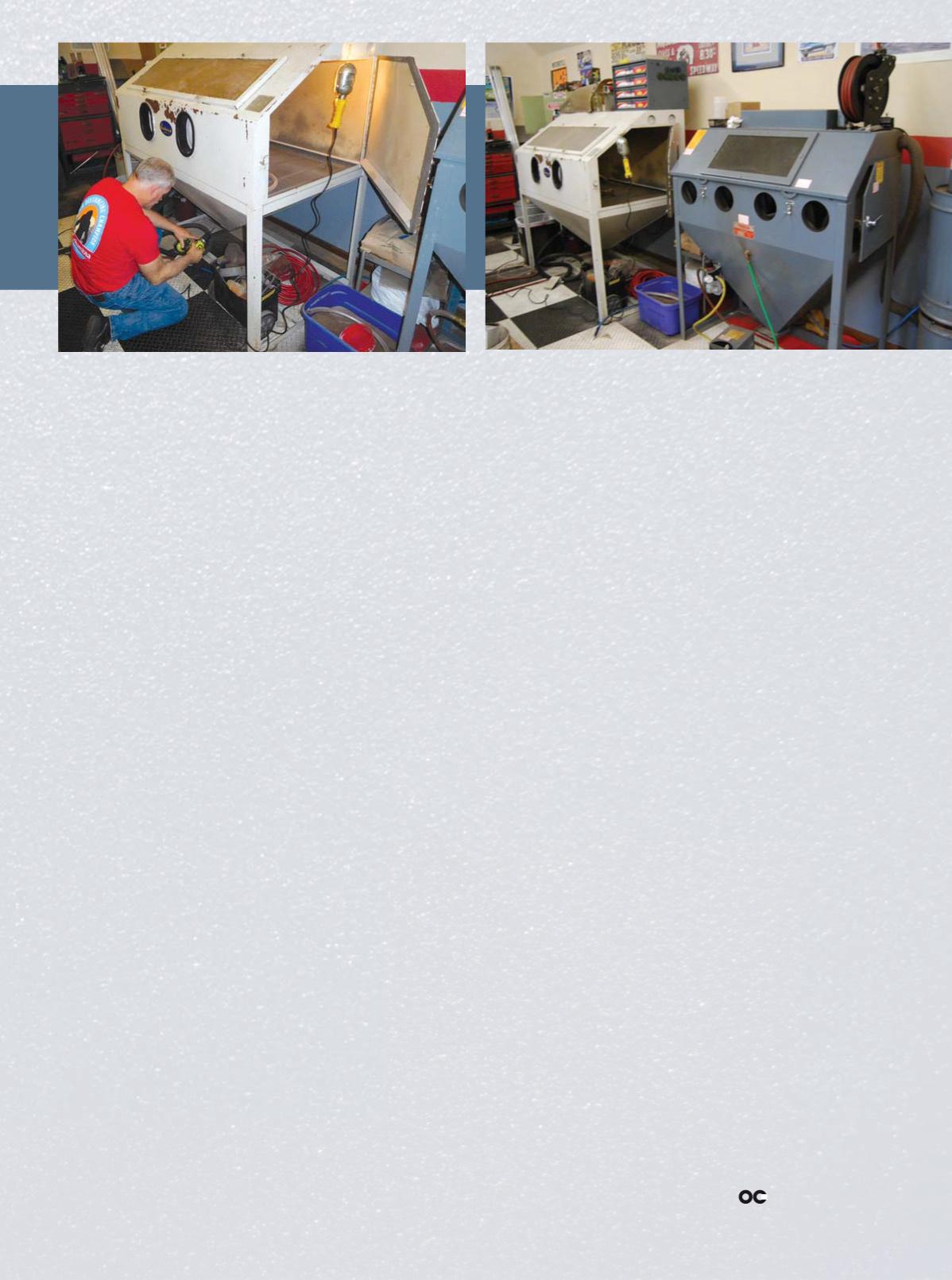
hobbyist devised an elaborate “self-cleaning” dust-collection system to automatically deposit debris into a plastic bucket. Tips for tip-top operation
Blasting ef ciency decreases, because media blasting cabinets need regular service to maintain top performance. After many sessions of bombarding steel and cast-iron parts, all media starts to break down. It becomes more of a powder than an abrasive, and it needs to be replaced. A trap door at the bottom of the cabinet can be opened to release the old media. Be certain to close the door before adding new media. And don’t add too much media. You need just enough to cover the pickup tube or hose, but not so much that the media load gets so heavy that the media doesn’t blow around inside the cabinet. A clear view
You want the media blowing around a bit, but when it does, it will scratch the glass inspection window if the glass is unprotected. This is done with protective plastic sheets that are heavy enough to tolerate the media (for a while). Of course, these sheets will also eventually get scratched, so plan on replacing them on a regular basis.
Replacement plastic sheets should be the same dimensions as the glass inspection window. The glass is usually held to the opening by a metal frame that ts around it. The frame has a couple of holes drilled in it, and these are lowered over threaded studs that stick up from the cabinet and hold the glass in the proper position. Drop the frame over the studs and reinstall the wing nuts that are used to secure the frame. Dust the dust collector
Some media blaster makers recommend taking the twopiece dust collector (actually a large plastic or metal canister) apart and cleaning it every time the media blaster is used. Most shops probably don’t clean the dust collector that frequently, but the job should still be done about once a month if you blast fairly often. The lter bag inside should be cleaned on a regular schedule, too, and probably replaced yearly or sooner. (Follow the guidelines provided by the cabinet manufacturer.) Keep a clean gun
eventually turn the round opening in the barrel into an irregular shape, affecting the ow of media. Usually, the barrel is held in place by little screws that can be loosened or tightened with an Allen wrench. Every few weeks, loosen the screws and slightly rotate the barrel so it lasts longer.
Clogs in the pickup tube, hoses and gun are another problem that can arise. Maybe you blasted a part that had fabric or rubber remnants attached to it. These can clog passages and can also contaminate the media. Avoid blasting such items; nd a way to remove the fabric or rubber remnants before blasting the metal part. Any foreign matter attached to a part — including dirt and grease — can contaminate the media. Use a wire brush attachment on a die grinder, cut-off tool or rotary tool to remove those “petri ed” black grease spots before placing the part in the media blaster.
Dave Wallendal of Metal Finishing Supply Co., Inc. in Waukesha, Wis., (www.metal nishingsupply.biz) is a vendor at the Jefferson Swap Meet and Car Show in Jefferson, Wis. He makes sales and service calls at shops around the Badger state.
Wallendal was asked to check out an older, very large cabinet blaster that had been purchased from Eastwood (www.Eastwood.com) about 12 years ago. A large cabinet is nice to have, because large parts t in it. But the blasting ef ciency of this cabinet had dramatically dropped. Wallendal determined that the pickup tube and hoses were opping around in the cabinet and not properly sucking up media. He fabricated a bracket to hold the pickup tube in a better position in the media.
The Eastwood cabinet was loaded with glass bead media. Wallendal said this was a great media to use when working on car restorations, because threaded parts can be blasted without ruining the threads. Glass beads will also leave a smooth, shiny nish. However, they won’t remove material that is harder than the beads themselves. Glass bead media will also break down to powder faster than aluminum oxide or other media .
In addition to sales and service work, Wallendal sells blast cabinets and parts and supplies for them. But, even if you have a cabinet in your shop that’s of a brand Wallendal does not sell, he can supply various media, lter bags, guns and barrels, hoses, air pressure gauges and inspection window protectors. He’ll make your “eraser” erase again.