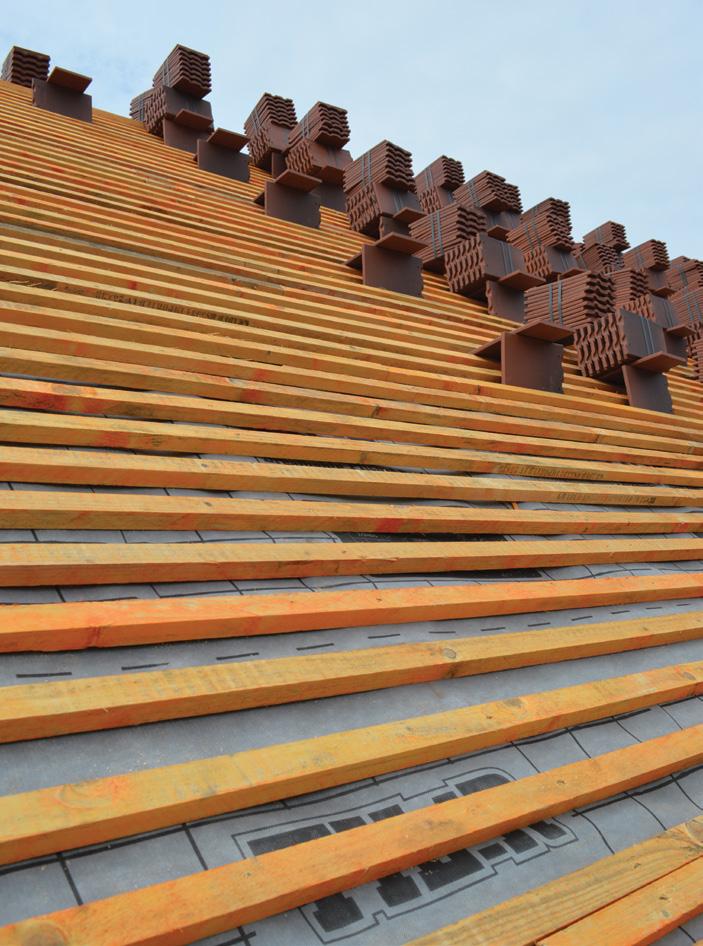
4 minute read
Long Term Market Pressures
Demand for timber and construction products is at record highs both in the UK and globally, with reports suggesting that shortages are set to continue throughout 2021.
A
ddressing some of these concerns, John Newcomb, CEO Builders Merchants Federation and Peter Caplehorn, CEO Construction Products Association, who cochairs of CLC Product Availability work group released a statement saying that the availability issues we are currently experiencing are likely to worsen before they improve.
“While supplies of plaster and plasterboard are much improved on last year, almost every other product group is experiencing longer lead times and, as a consequence, higher prices,” they said. “Imports of timber will be an issue for the foreseeable future. Not enough timber is being produced to meet world demand. Added to this, other countries are prepared to pay more to secure their supply, pushing the UK lower down the pecking order. All users should plan for increased demand and longer delays, keep open lines of communication with their suppliers and order early for future projects.”
The Office for National Statistics (ONS) also projected a rise of 7-8% in material prices this year, with increases for timber, expected to more than double. Travis Perkins – the UK’s biggest builders’ merchant also grabbed national headlines by warning customers of ‘considerable cost increases’ to raw materials amid the industry-wide shortage. Speaking to The Times, Travis Perkins said it had been informing customers in its stores, websites and by email of the price rises, with the price of bagged cement up by 15%, chipboard by 10% and paint by 5% at its UK outlets.
Leading voices from the UK roofing industry have also warned of ‘faltering availability and rapidly rising costs of basic materials such as timber roofing battens.’ The National Federation of Roofing Contractors (NFRC), Avonside Group (including Avonside Roofing), Marley and SR Timber said global timber shortages have put the UK housebuilding industry’s supply chain under enormous pressure with extremely low available stocks of European softwood
For roofing contractors, the biggest impacts are on cost and productivity. Delays in supplies of materials such as batten present a real and serious risk to housebuilders’ production schedules, the financial impact of which can be severe. Avonside Group’s CEO Eddie Stanton said: “The price of roofing batten is rising on a monthly basis, already in excess of 50% over the past six months, and supply lead times are getting longer.
Image © SR Timber Image © SR Timber This is putting enormous pressure on the housebuilding supply chain, especially roofing contractors, in terms of what price increases they can absorb and what they have to pass on.” Reflecting on Marley’s position in respect of its JB Red timber brand, the company’s roof systems director Stuart Nicholson said: “The global/US pressure of increased demand for timber has exacerbated the supply issues caused by the pandemic and Brexit. Therefore, it remains extremely challenging to secure the raw materials needed to produce and supply finished products.” SR Timber’s trading director Shaun Revill says: “We’re in the very fortunate position of having our own dedicated sawmill in the Baltics, which means we have our own robust supply chain – but even that has been tested to the limit recently with Brexit and Covid-19, and we are not insulated from what’s going on globally. We have been very proactive and transparent with our customers and given them lots of information to explain the situation regarding stock availability – which currently has a lead time of around ten days – and price movements.” James Talman, chief executive of the NFRC, said: “We are currently seeing unprecedented shortages of roofing materials, in particular timber. This is due to a whole host of different reasons, from Covid-19 restrictions to the impact of low US timber supplies. Our data shows that two-thirds of roofing contractors saw material availability deteriorate in the first quarter of the year, and 89% reported price rises. Timber battens were the second-highest material shortage after roof tiles with a third of contractors reporting shortages. Whilst our supplier members are doing all they can to alleviate shortages, it will still be some time before we are back to steady levels of supply, and homebuilders therefore need to work collaboratively with roofing contractors to plan ahead, build in lead times, factor in price rises and ensure flexibility in contracts.”
It is now critical that everyone in the supply chain – customers, merchants and suppliers – to be planning material purchasing and supplies further and further in advance. This way everyone can better meet the forecasted timber volumes and increasing industry demands to reduce the stress on building completion and market pressures across the UK.
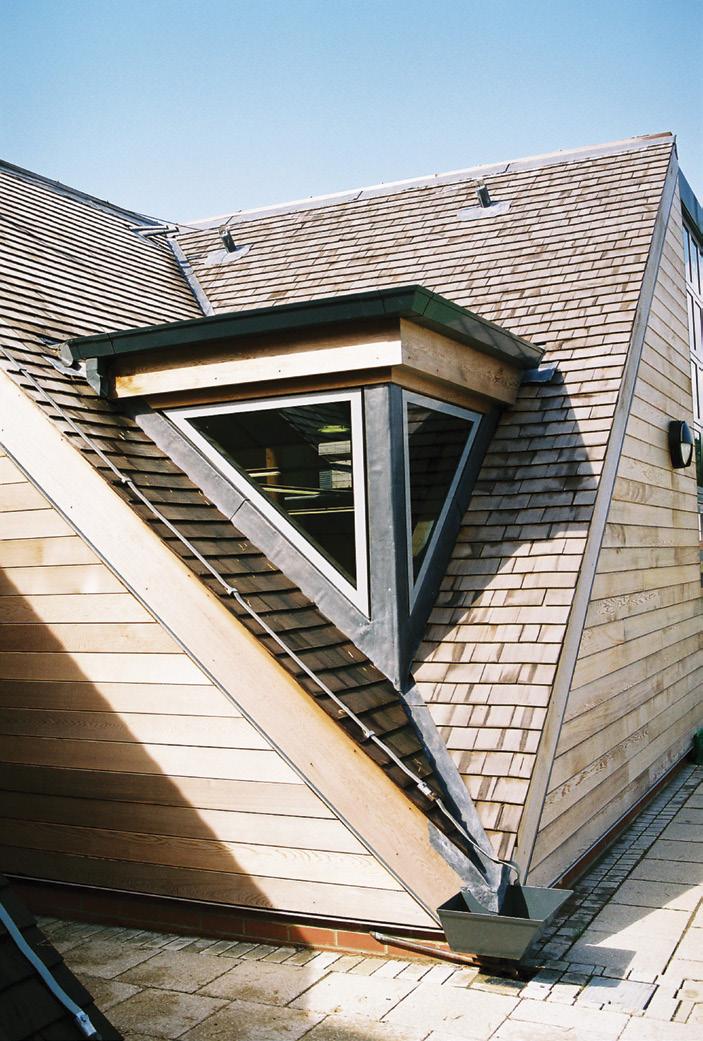
6118
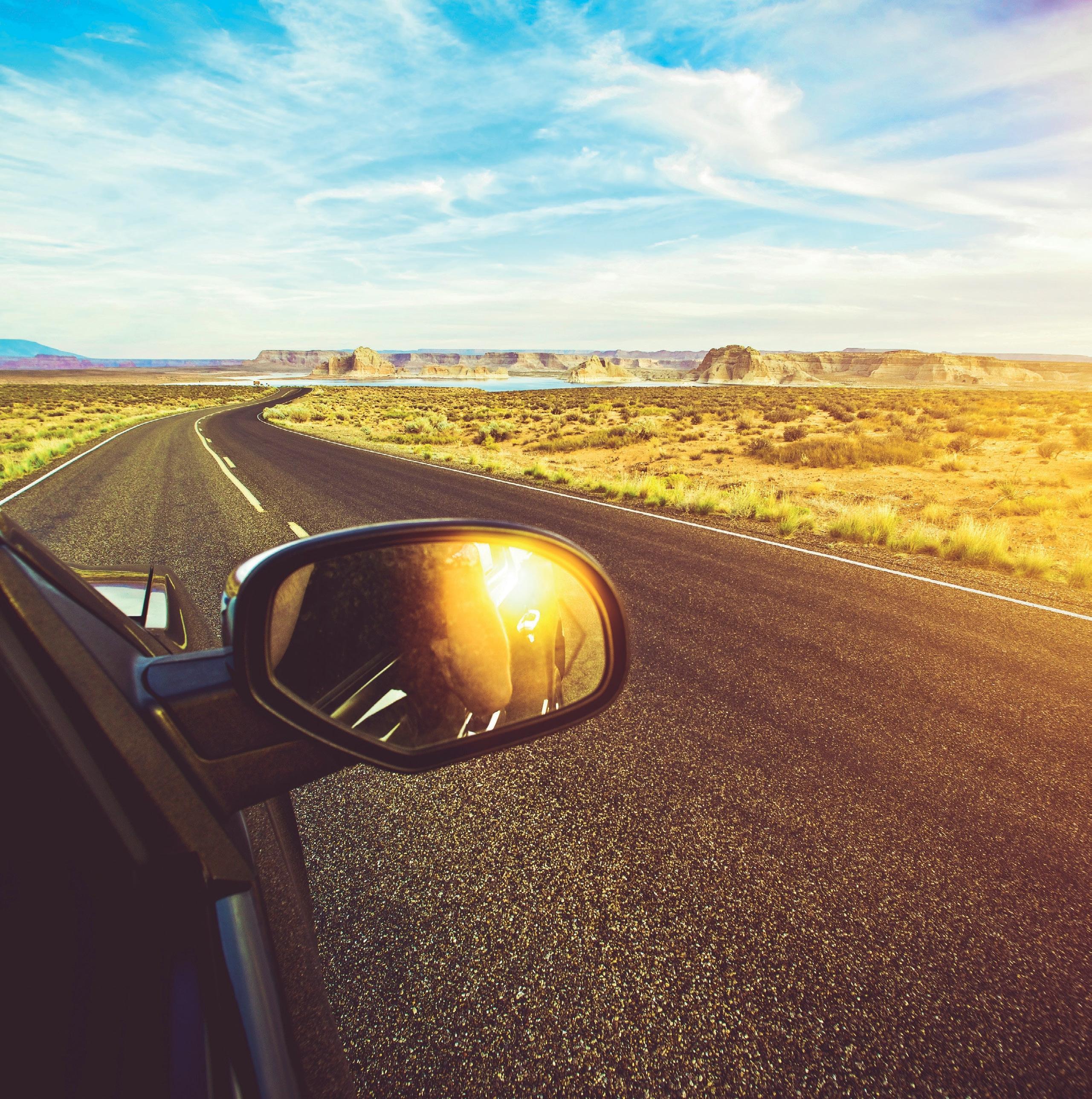