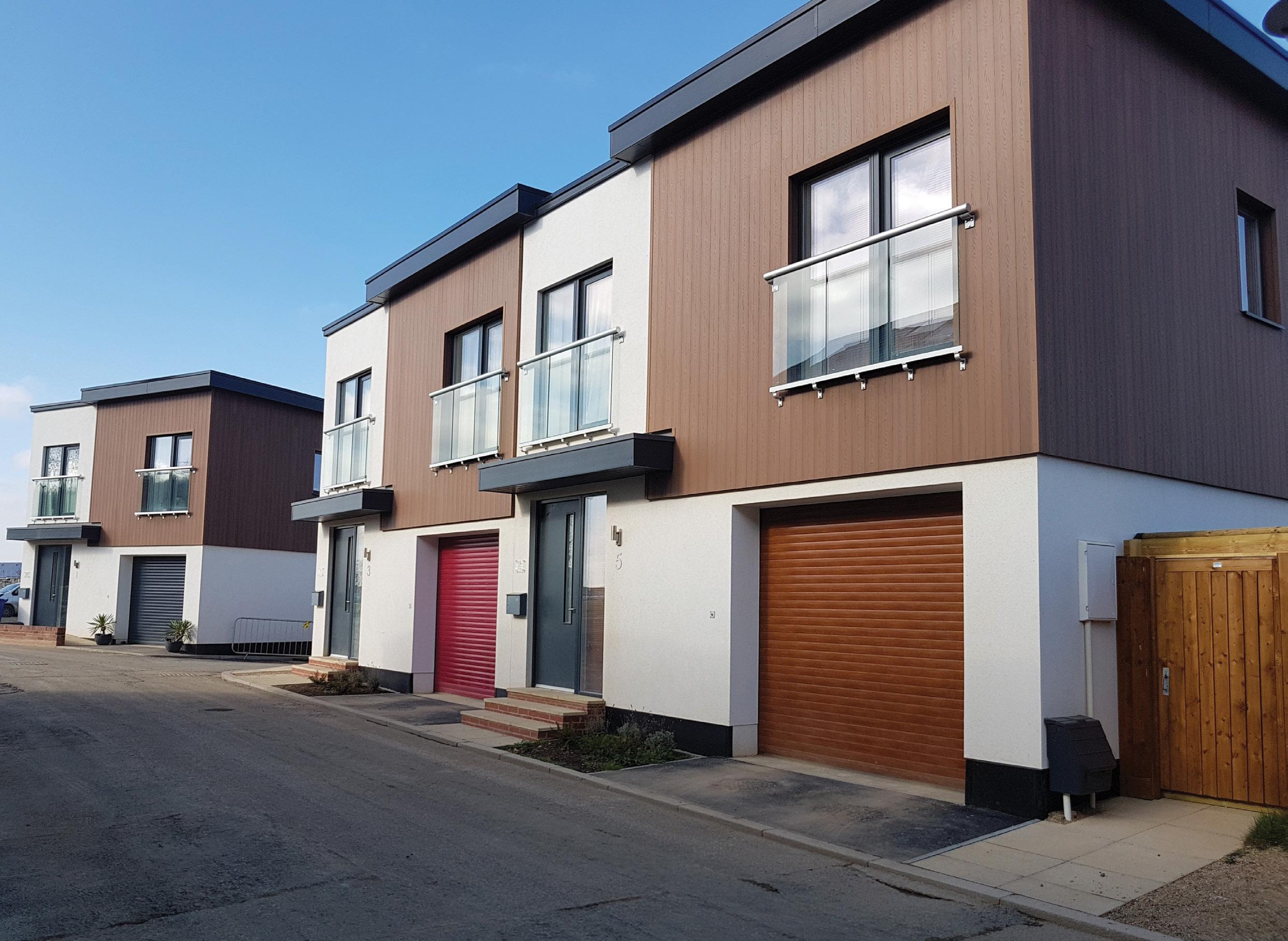
12 minute read
Focusing on the Future
Low Carbon Living
With Beattie Passive having long been an exponent of Passivhaus design in the UK, we asked them a few questions about the importance of the standard to the future of sustainable homes in the UK.
assivhaus is a fabric first approach to construction. By P combining a highly insulated structure with limited to no thermal bridges, triple-glazed, gas filled Passivhaus windows and heat recovery ventilation, a very thermally efficient and high-performance home is delivered. With a fabric first approach it is very simple and achievable to reach net zero emissions with the addition of 2.5kw PVs and air source heat pumps for hot water.
The Passivhaus standard is still considered an expensive route to an energy efficient building – what can be changed to alter that perception?
“Whilst it used to be the case that building Passivhaus required a higher initial investment than traditional build, a recent report by Derek Gough Associates concluded that in some cases it is actually cheaper to build Passivhaus than it is to build a traditional build. It is critical to look at the long term benefits and the lifetime cost analysis to really compare the costs and benefits of building Passivhaus, not just considering energy savings but also the costs of maintenance and any future upgrade requirements of traditional build to achieve zero carbon.”
What has driven the recent Beattie Passive Norwich factory expansion and investment into Haus4?
“Our Haus4 range was initially designed as a high-quality, highly flexible solution to the UK’s homelessness problem. The worsening situation of UK homelessness combined with the greater impetus to get homeless people off the street in the wake of the Coronavirus pandemic, we have seen demand for our Haus4 range skyrocket. In order to facilitate this demand, we have expanded into significantly larger premises and taken on an additional 70+ staff and have immediately begun work on 150 modular pods for clients across the UK.
The Haus4 range delivers both the exceptional performance of Passivhaus and the quality of a Beattie Passive build. How is Haus4 different from a standard Beattie Passive house build?
None. Both the Haus4 product and a more ‘traditional’ Beattie Passive build are built to the same high standard using the same patented timber frame build system, and are tested just as stringently upon completion, so in that sense there is no difference in quality and performance. The difference comes in their purpose. The Haus4
range was developed in response to the demand from councils, housing associations and developers for fast, flexible, high quality and easily relocatable units. Services can be connected and be ready for occupation within an afternoon. We are now expanding our modular range
Passive House windows V entilation with heat recovery
Airtightness Factory on or close to their own site. The Flying Factory is highly flexible, able to be easily scaled up, scaled down, relocated or mothballed to align with a client’s needs, and no specialist equipment is required making it a very affordable option. By being able to set up a Flying Factory like this close
to apartments and houses. to site means Beattie clients
Passivhaus design Thermal insulation
typically involves very high levels of insulation and an airtight building envelope. How is the Haus4 range delivering Passivhaus performance?
5
Thermal bridge free desig ns can deliver studs and panels straight from manufacture to
The five basic principles of Passivhaus
site, reducing or avoiding logistical challenges and transport costs. It also provides an ideal base to support local supply chains and the training of
local people in the skills of carpentry and construction.
“The Beattie Passive build system was designed from the ground up to be a system that could deliver to the Passivhaus standard by default. Our patented construction method provides a continuous insulation layer around the core of a timber framed structure, delivering a complete build system
The Haus4 units are designed to be fully demountable. What does that mean and how can that respond to future changing housing needs?
“When the Haus4 home is needed elsewhere, it is a very simple
from foundation beams, ground floor, walls and roof. The Beattie Passive build system is deliberately simple so that it can apply to any size or shape of property, so that whether we are building a traditional home on-site, or a modular built Haus4 unit inside a factory, the Beattie Passive system delivers every time. The modular manufacturing process is exactly the same as our ‘traditional’ build process but has the advantage of being in a covered factory where efficiencies and processes can be maximised. The performance delivered is no different – we build to Passivhaus standard every time.”
Can Passivhaus housing be delivered at scale to improve the UK’s built environment generally?
“Beattie Passive was founded on the basis that we wanted to lift the standard of building across the building industry, and we believe matter to disconnect the services, load them up onto a lorry via crane, and then move them to where they are needed next, where they can once again be connected to services and made ready for habitation within hours. These units are highly relocatable – our partner Creating Enterprise has moved theirs more than 10 times so far with no structural damage – and relocatable housing like this is the perfect way to respond to changing housing needs, as these units can either be placed down as permanent homes in an area or can be placed down as temporary accommodation while other arrangements are made, and then moved on to where they are needed next. Our modular units can be completely re-purposed. So for example our apartments blocks have been designed with 1, 2 and 3-bedroom flats, but if the need arises these properties can easily be taken down, moved and repurposed into a 2 bedroom bungalows or house.
that partnering with organisations and enabling them to build our Passivhaus build system is the best way to truly deliver at scale. We are always on the lookout for partners from around the country to collaborate with and provide them with the skills and abilities to build their own Passivhaus standard homes. Through our Flying Factory partnership offering, we already have nine partners
Beattie Passive are currently supporting Cardiff Council to increase the supply of new, high-quality temporary accommodation to cater for homeless families in the city. How is the scheme progressing?
with their own Beattie Passive factories delivering Passivhaus homes. We believe that partnering with more organisations who share our vision and values will increase awareness of and raise the profile of Passivhaus.”
The Flying Factory is essentially a mini Passivhaus factory that allows Beattie’s partners to become self-sufficient in delivering their own Passivhaus-standard homes. After training on how the system works and how to build it, Beattie helps their partners set up their own Flying “We are so far on track to deliver 58 new modular homes ranging from studios to 1, 2 and 3-bedroom flats to provide temporary homes while a more permanent housing solution for these families is found. All these units will meet the Passivhaus standard and are built for a 60+ year lifespan. Our first scheme recently left the factory and the next batch of these units is under construction in our factory and will be ready to be shipped out in February 2021.
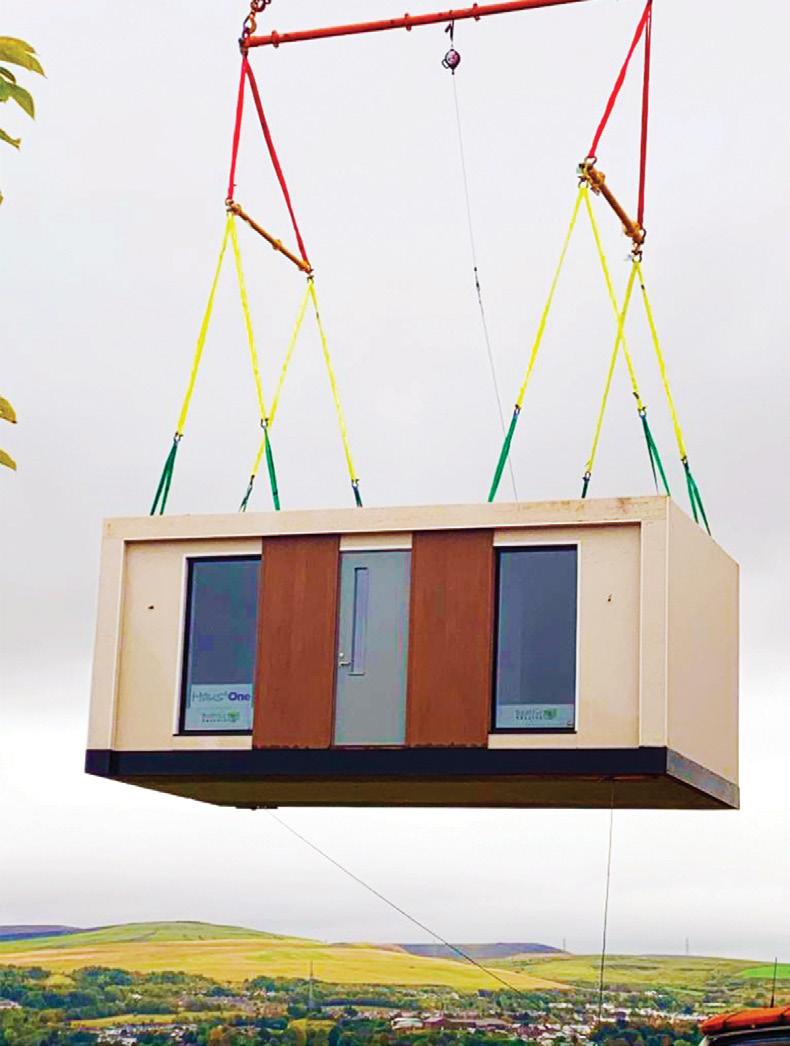
Wraptite® airtightness solution provides huge benefits for Anglesey modular homes Now is the Time For Timber
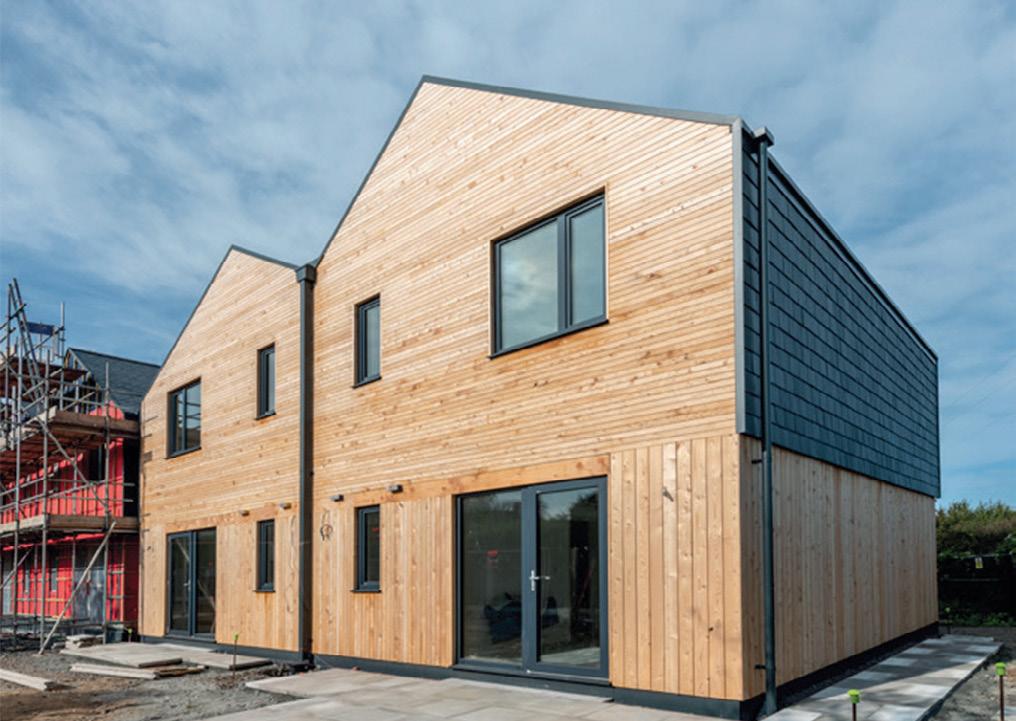
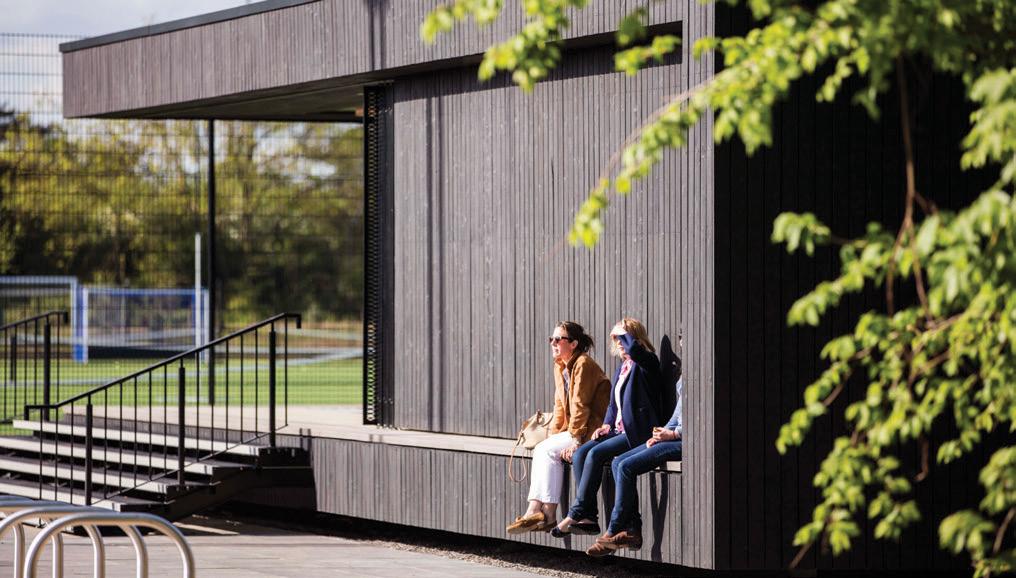
The superior airtightness performance of the Wraptite membrane from the A. Proctor Group is delivering huge benefits to both the in-factory and on-site construction of a series of new modular social housing for Anglesey Council. Wraptite is the only self-adhering vapour permeable air barrier certified by the BBA. Applied externally on the outside of the structural frame, Wraptite simplifies the process of maintaining the envelope’s integrity, as there are less building services and structural penetrations to be sealed. The high vapour permeability of Wraptite allows the substrate beneath to dry quickly and moisture vapour to escape, and reduces the likelihood of mould, mildew, condensation, timber distortion and metal corrosion. The self-adhesive nature of Wraptite means that it is easy to apply together with Wraptite Corners and the fact there is no requirement for mechanical fixings. Specialist contractor Kenton Jones was commissioned by the Isle of Anglesey County Council to construct the new homes using a high-performance timber frame system. Managing Director, Kenton Jones explains how Wraptite was key to achieving a quality airtightness solution which was suited to modular build. “After 10 years of building an open panel high-performance timber frame system, we moved to a factory insulated closed panel system which had the airtightness and VCL applied in the factory and simply taped on-site. This worked well when the airtightness layer was fully accessible before services were installed on site. “In 2019 we built a new module factory and delivered our first set of modules early 2020, it was then we realised internal airtightness was going to be a difficult detail. When building modules that are fully factory finished internally but need to be craned together on-site to form the same dwelling both in a vertical and horizontal joint, we identified that there would be areas of the building which would remain inaccessible after installation on site. “
For more information contact www.proctorgroup.com Soprema Urges Specifiers to Upgrade from Greener to Greenest With Green Homes Grant
Insulation and waterproofing specialist, Soprema, is urging specifiers to consider the sustainability of the materials they select for housing upgrade projects carried out under the Government’s Green Homes Grant scheme. The scheme allows home owners and landlords to apply for a grant of up to £5,000 per property to cover up to two thirds of the cost of home improvements that reduce energy consumption and carbon emissions. Those on certain benefits can claim up to £10,000 to cover the entire cost of improvements. The scheme, which applies to home improvements completed by the end of March 2021, is expected to lead to a significant surge in uptake of internal wall insulation (IWI), roof insulation and external wall insulation (EWI) for solid wall properties. However, Soprema has raised concerns about the possibility that less green solutions will reduce the benefits of the initiative and result in additional environmental issues in the long term. Roland Jackson, commercial director of Soprema explains: “Any insulation installation will provide environmental benefits by improving thermal performance but the reality is that some of the materials commonly used are made from non-renewable and non-recyclable materials that continue a cycle specifiers and home owners need to consider the goals of the Green Homes Grant and choose renewable, recycled and recyclable insulation materials. These solutions provide all the environmental benefits of improved thermal performance, without any of the negative environmental side-effects.” Soprema advises that a woodfibre insulation system, such as the company’s Pavatex range, provides the ideal solution for IWI and roof void insulation upgrades. Manufactured from renewable timber and completely recyclable, Pavatex provides excellent thermal performance, with options for plasterboarding or rendering, and is also naturally breathable for a comfortable indoor environment all year round. For EWI insulation upgrades, Soprema recommends the company’s XPS 500 insulation, which is a BRE Green Guide A-rated system, thanks to its use of recycled materials and 100% recyclability benefits. There is just a short window of opportunity for home owners and landlords to take advantage of the Green Homes Grant but the impact of the scheme could last for generations. That’s why Soprema is urging specifiers to choose wisely by using insulation systems that will truly make properties greener.
For further information visit www.soprema.co.uk/en
With the threat of missing critical environmental targets a very real danger in the post COVID-19 economy, the Time for Timber campaign started 21 September, launching a new drive that directly targets the financial and insurance sectors – one of the biggest stumbling blocks in the path of sustainable development. With ambitious targets set for the UK to reach net zero by 2050, combined with an increasingly urbanised population, there is an urgent need to change how we build high density and single-family housing. The obvious solution is using renewable, sustainable and environmentally positive materials such as timber but, historically, the insurance industry has been unwilling to support such initiatives. Misconceptions around timber’s suitability as a major project construction material have meant that this versatile solution is considered a risk by many insurers and finance houses. This basic misunderstanding of the facts could be jeopardising the future of the economy and the environment. Bringing together leading voices from around the construction industry, the Time for Timber campaign has been founded with the express intention of challenging these misconceptions within the financial and insurance sectors. The campaign launches today with a major advertising campaign at Bank underground station, in the heart of London’s financial district. The bold move will see the hard-hitting campaign message dominating the advertising space within the station, in a bid to kick-start engagement with this important issue. A programme of webinars with financial sector media partners and a new whitepaper will follow, to begin strengthening the dialogue between the timber construction industry, insurers and investors. Underpinning the communication campaign is a groundswell of support that is building throughout the industry, which is showcased in a new Time for Timber documentary. The film features compelling interviews with figures such as: British Green Party economist, Molly Scott Cato; architect and Chair of the Good Homes Alliance, Lynne Sullivan; Technical and Innovation Director at Barratt Homes, Oliver Novakovic and Chief Executive of the UK Sustainable Investment and Finance Association, Simon Howard – among several other prominent names.

of CO2 emissions and waste. While these products are acceptable for use under the scheme, both
To find out more and to watch the Time for Timber film, visit www.timefortimber.org
Shed loads of help from Norbord
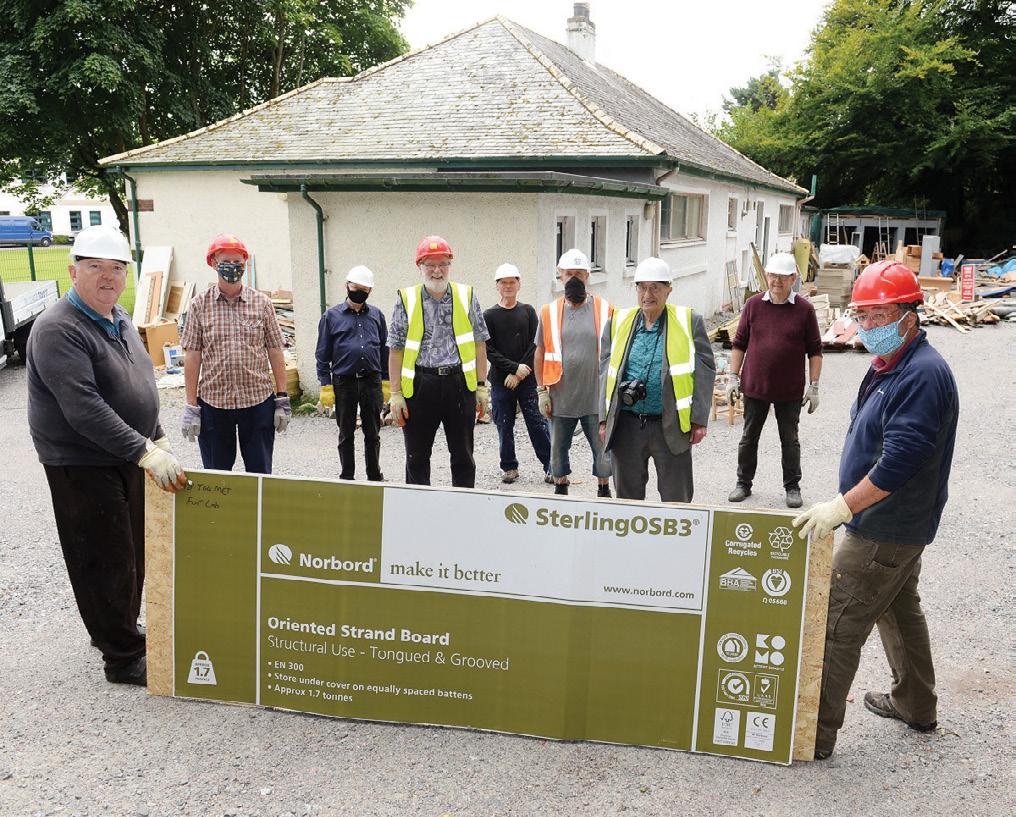
The Inverness branch of Men’s Shed has been busy restoring a former 1930’s pavilion in the grounds of Millburn Academy into a new home for the group. Fundraising for the £115,000 renovation project had been hampered by the pandemic, but a donation of SterlingOSB Zero by Norbord from the nearby plant in Inverness enabled the group to re-open and get back to work! The renovation task on the derelict pavilion was so big that the local group could work on different parts of the building while still observing social distancing. The Scottish Men’s Sheds Association and the UK Men’s Sheds Association create resources to look after the wellbeing, health and education of members and never has this been more vital than during the pandemic as part of the battle against social isolation. Norbord’s portfolio of OSB products is a development of the most popular brand in the building and interior design industries and comprises SterlingOSB Zero 3, SterlingOSB Zero Tongue and Groove, SterlingOSB Zero Fire Solutions and SterlingOSB Zero StrongFix. They are variants of the popular precision-engineered OSB3 board; BBA approved and designed for humid conditions, it contains zero added formaldehyde.