
6 minute read
The Effective Way to Build
Is timber frame and modern methods of construction (MMC) the answer to the UK’s many housing demands?
he Royal Institute of British Architects (RIBA) has called
Ton the government and local authorities for urgent investment in housing to meet the growing demand for social housing. Homeless charity Crisis recently calculated that 90,000 homes need to be built a year in order to meet this demand. Recent studies in the industry to calculate that if these houses were built using timber frame construction rather than traditional masonry methods, could save the government over £261 million.
Timber frame construction responds to the wider housing challenges. In fact, building with timber would see the government’s existing target of building 300,000 homes per annum reached far more effectively and sustainably, generating cost savings across the board and arguably moving towards bursting the current housing bubble. Building with timber is cost effective, with timber frame coming in at around a 2.8%* cost saving. It is also shortening construction time as Rider Levett Bucknall found in a study between the two methods. The build time for an average timber frame home was only 41 weeks compared to 49 weeks for masonry. The two months of saved time equates to further cost savings on labour most notably, as well as improve cash flow by completing projects sooner. The cost savings and efficiency aren’t the only benefit associate with timber frame. Timber is part of the circular economy, which is the most effective carbon store. When used instead of the more traditional building materials, a single cubic metre of timber will save around 0.8 tonnes of carbon dioxide emissions. When extended to the 90,000 homes a year – that can make a huge difference to the environment.
Importantly, timber is a renewable material, with up to 90% of the timber used in the UK coming from certified sustainable sources such as the FSC and PEFC. The majority of the remaining 10% comes from well managed sources in countries which do not practice certification. For every tree that is harvested, five are planted in its place which means that it is not only a sustainable method, but one that is integral to the governments Net Zero by 2050 initiative. Richard Swayne, Director of Paramount Timber Frame says: “The time has come for the industry to switch to timber frame more aggressively. The benefits for using timber instead of traditional masonry methods are tenfold. At Paramount Timber Frame, we know there is intense need for delivering high quality, good value housing and fast. Switching to timber frame is how we start to build for tomorrow. To not only alleviate the housing crises, but to evolve the industry to becoming more sustainable, for both the environment and society. Andrew Carpenter, Chief Executive of the Structural Timber Association says: “It’s no secret that Britain’s housing construction has faced numerous challenges over the decades, from planning restrictions, cost of materials and safety issues. Timber construction provides a glaringly obvious solution to many of these challenges whilst also meeting housing needs efficiently and net zero carbon by 2050 target. With timber construction we believe we can build back Britain, Better, Greener and Faster. Our Time for Timber campaign embodies this, bringing together the science, data and industry thought-leaders, echoing that the time to change our out-dated construction methods is now.”
Are you an engineering or architecture student and want to measure yourself against design professionals? Take part in the competition and design your timber multi-storey structure with our most innovative products! You can win a tour that will start from our Italian headquarters and will end with the participation in the Mass Timber Seminar and the prestigious Forum Holzbau in Innsbruck, two of the most important events in the world of timber construction.
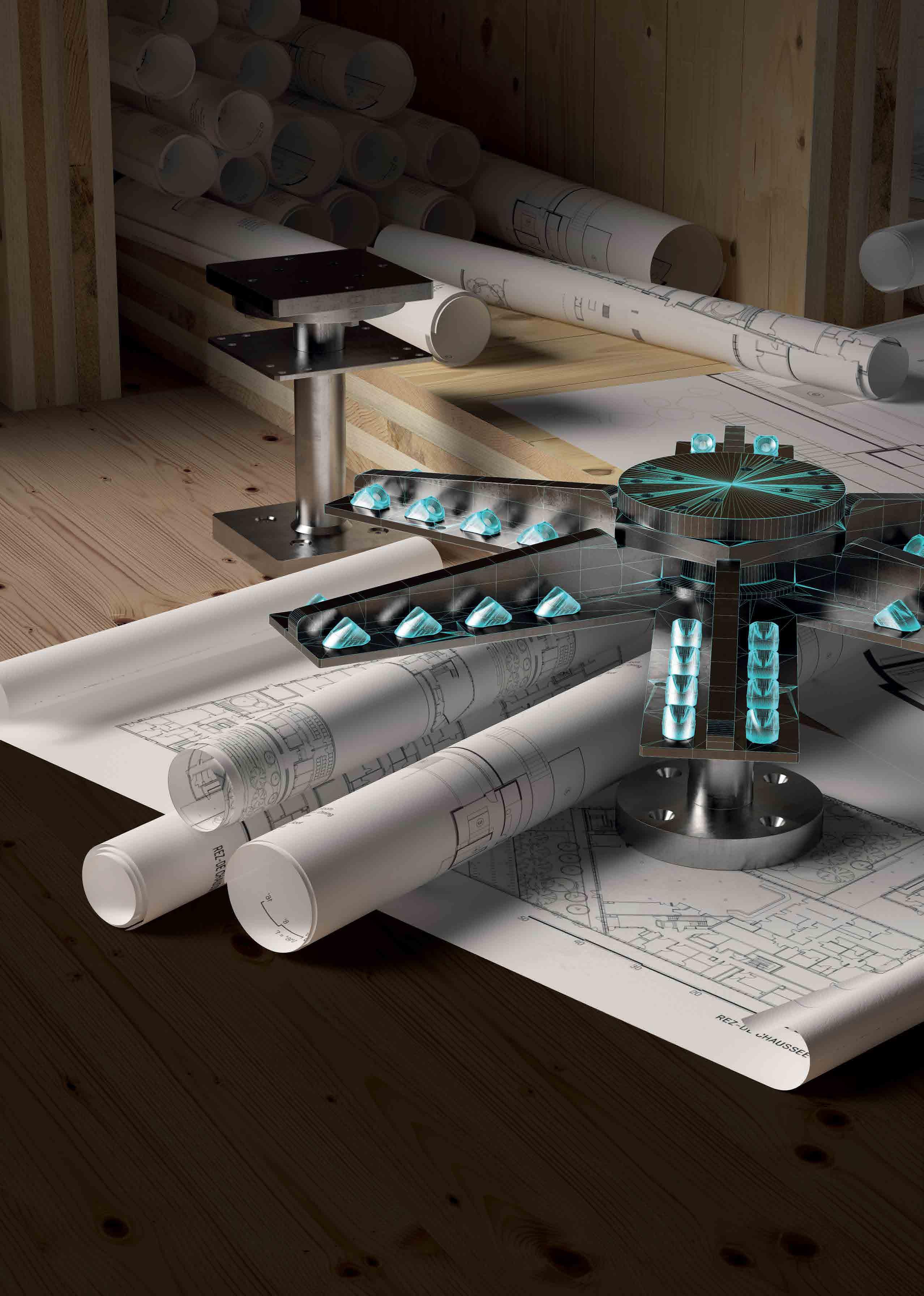
ARE YOU READY FOR THE CHALLENGE?
buildtheimpossible.rothoblaas.com
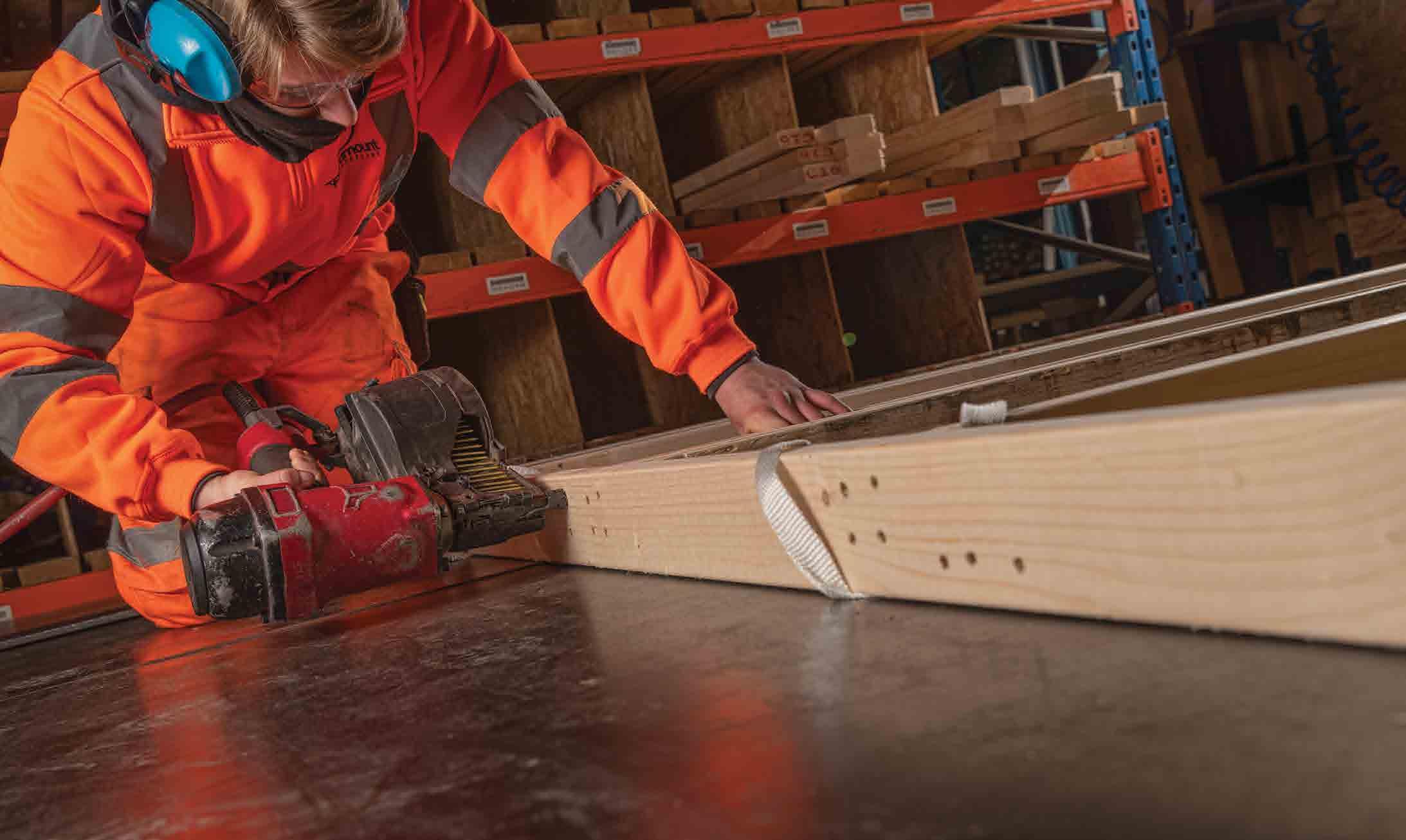
A new in-depth NHBC Foundation report has looked at how lessons learned from the past century can help increase the use of timber frame and other offsite construction methods. The 48-page document, Modern Methods of Construction: Building on Experience, looks at steel and concrete as well as timber construction. It examines the drivers which sparked their use in the past and how problems encountered can be used as learning tools to ensure the industry can provide enough high-quality homes over the coming decades.
Although volume housebuilder such as Barratt Developments (with its acquisition of Oregon Timber Frame, one of the UK’s largest timber frame manufacturers) have adopted timber frame more with targets of building at least 20% of its homes using an element of offsite construction including timber frame, it is still not fully understood from a volume housebuilder perspective. Actis specification manager Dan Anson-Hart, who works with many in the UK timber frame industry says the report should now give volume
Timber vs Masonry Savings
Average house size: Cost per sqm for timber: 91 sqm* 1,148.38**
Cost per average house size for timber: 104,502.58
Cost per sqm for masonry: 1,180.34** Cost per average house size for masonry: 107,410.94 Cost for 90,000 average homes a year in timber: 9,405,232,200 Cost for 90,000 average homes a year masonry: 9,666,984,600
Cost Saving of £261,752,400
*According to RIBA Homewise report 2015 **According to study by Rider Levett Bucknall housebuilders more confidence. “Offsite production is much quicker than brick and block, making it an ideal way to build the homes we so desperately need here,” explains Dan. “But speed is just one of its merits. It is not speed at the cost of quality. Far from it. Construction within a factory environment means each stage of the process is carefully measured, with construction details clearly laid down, to ensure the performance of the final building is as predicted. From a thermal point of view a timber frame building can be much more efficient than its traditional equivalent.
“Elements such as wiring, plumbing and insulation take place in the factory. Our insulation systems, which can eliminate thermal bridging and in real life deliver or improve on the U-values predicted under lab conditions, take between 25 and 50% less time to install than traditional alternatives, which all helps to speed up the process.” In his foreword to the NHBC report, Government MMC champion Mark Farmer said: “Calls for a system of prefabrication, which would enable us to build houses in the same way as cars and aeroplanes, have been made for nearly a century - often as a response to the extreme need that followed times of social and economic upheaval. As we navigate the Covid-19 crisis and come out of the EU, there is, again, an opportunity to innovate, to build better with homes that use new technology and delivery mechanisms, meet net zero carbon targets, and provide jobs of the future.”
The report concludes: “We must harness technological advances and digitally enabled design and deliver economical and numerous factorymade homes to respond to pressing housing need and the climate crisis. Homes should be better performing, good-looking and long-lasting, be spacious and comfortable and enhance neighbourhoods. Design should be based on established good practice principles such as construction detailing and building physics like heat loss and ventilation.”
More at www.paramounttimberframe.com www.insulation-actis.com
FOR TIMBER THAT KEEPS OUR FORESTS STRONG, CHOOSE FSC®
Our forests give us many things, including a huge variety of timber and timber products. FSC helps look after forests and the people and wildlife who call them home. So you can use timber, panels and other forest products while keeping our forests full of life.
www.fsc-uk.org
