
5 minute read
Support Network
As head of one of the leading heavy duty racking manufacturers in the UK, we spoke to Steve Wickens, managing director at Wickens Engineering about being a market leader in a busy warehousing environment.
W
ickens Engineering was founded by Steve’s father, Bob Wickens in 1978 and now employs almost fifty loyal and highly skilled staff and have supplied around twenty thousand cantilever racking orders along with a similar number of bespoke storage solutions over the last 40 years.
“We pride ourselves on supplying high-quality products supported by first class customer service,” says Steve. “In turn, this means that we have frequent repeat orders from customers, many of whom have traded with us for a very long time. As a customer focused business, this company-wide culture ensures the very best experience for our customers from initial enquiry through to installation, thus removing the worry element from the important investment they are making.”
The most important aspect of any storage system is to make the best use of the space available and give the customer improved efficiencies through reduced handling of products – how is this achieved? “You must first understand what the customer needs – not what we are going to sell, says Steve. “Asking the right questions and developing a solution that works for the customer is our priority. Once we understand the requirements, we can then complete a structural design and propose a solution. Often the costing stage is at the tail end of the process, when we are sure that the customer is getting the racking design that works best for them.
“A reliable storage system’s design is based on structural calculations to ensure that the system is robust and suitable for the application. The quality then depends on the manufacturing processes and control systems, as well as the quality of steel and the finish employed. At Wickens, racking safety is paramount and with the product, quality is unquestionably a key to our business.”
“Key aspects to be considered when storing timber include ease of access to ensure good stock rotation; robust storage systems to prevent handling damage; packs of timber are well supported and at the correct centres to prevent warping; prevention of sun damage or discoloration; prevention of water damage.”
Cantilever racking and rack clad buildings are ideal for timber products – for the how do these different types of systems operate? “Cantilever racking is an open-fronted system, which is ideal for the storage of long and heavy timber packs. As there are no upright sections restricting access at the front, cantilever racks allow storage capacity to be maximised as packs of various lengths can be stored side by side. Adding a roof canopy offers some protection from both sun and rain, but this is limited unless full cover is given.
“A rack clad building is a fully-enclosed storage building where the racking uprights form the structural frame of the building. The uprights support the roof structure which can be fitted with rainwater goods. Purlins and conventional cladding are fitted on all sides, along with roller shutter doors and pedestrian access to form an enclosed structure.
“A rack clad building project can potentially require much more planning and consideration due to complexity of the project, but it can be erected in as little as 12 weeks from order. This solution is much quicker and cheaper than a conventional building that can typically take up to a year to complete. Such a building is fully modular and can be extended later or moved to a new location altogether.
Health and safety are of paramount importance in a warehousing environment, with many considerations to bear in mind when installing a system beyond the basics of ensuring that the racking can support the loads that are going to be stored upon it. To cater for a range of applications, Wickens design criteria are among the strictest in the industry.
“When comparing like for like designs, our systems would often use the heaviest sections,” says Steven. “Both our design and manufacture comply with the latest CE standards which are now a legal requirement and ensures that our welding is inspected and fit for purpose. Much of the welding is now carried out by robots, which ensures first class welds are consistently achieved.
“Installation is just as important. Ideally, it will be carried out by SEIRS qualified installers, and it is critical that method statements are followed closely. Failure to correctly install diagonal bracing, for example can have dangerous consequences. Load labels should always be fitted to clearly show the weight carrying capacities of each arm, but what is often omitted is the training of the forklift operators, so that they understand the loads that they are handling and how these apply to the racking system. As with any other product of a similar nature, racking requires some safety maintenance. Rack inspections should take place on a regular basis and any damaged components identified must be replaced.”
Warehousing and storage have become a hot topic lately and racking is seen as one of the ultimate solutions for increasing the stock volume without expanding the site or moving to new premises. The impact of Covid-19 and Brexit have brought unique pressures to all aspects of society and business and adding challenges with stock supplies for many industries.
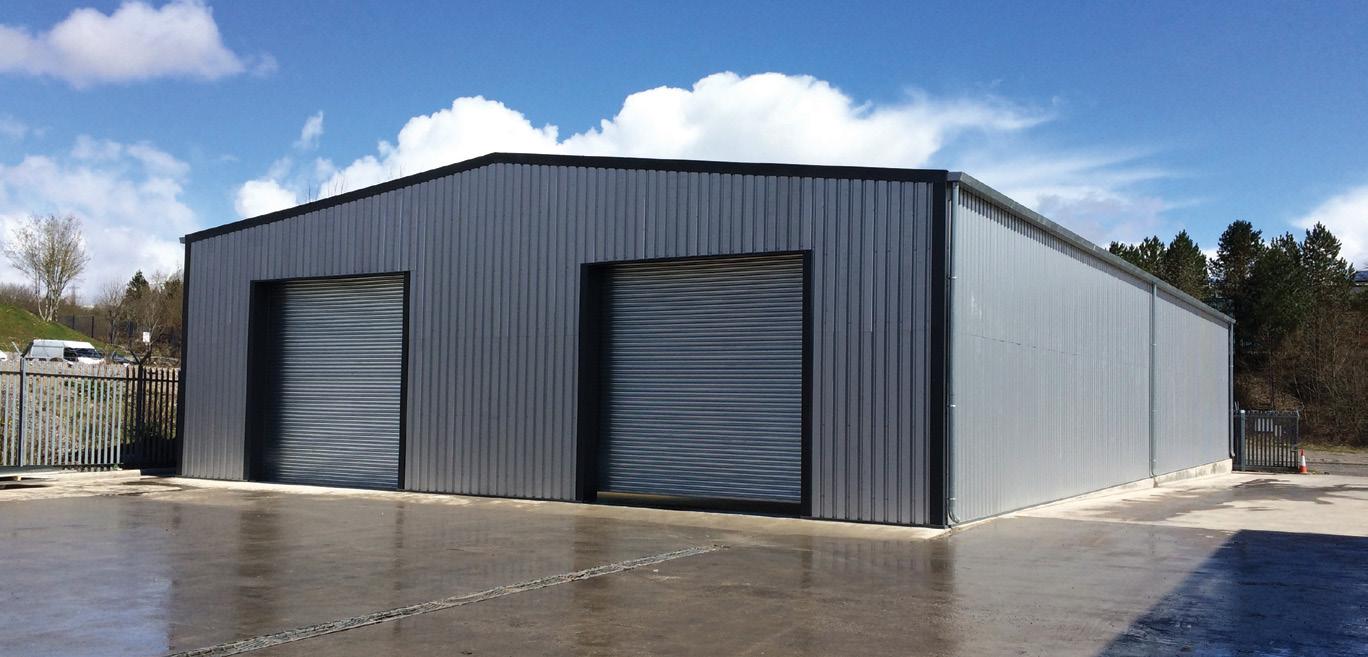
A complete rack clad building
“We saw the storage market slowing down briefly due to uncertainty, which was then followed by a strong recovery,” continues Steven. “The timber sector has been particularly strong due to the high domestic demand during lockdown and the need for timber companies to increase their organisation and efficiency. They no longer have the time to move materials to access a different item, as time costs money, so there is much more appreciation of the longer-term benefit of cantilever racking.”
As we start a new year, what market/business developments and changes does Wickens have in the pipeline for the coming year? “We are looking forward to 2022 with a great deal of optimism,” says Steven. “There are a lot of improvement projects planned for the coming year and we are continuing to invest in our product development, machinery, facilities and, of course, our staff. All these improvements will help us to manufacture our products more efficiently and refine our processes to offer improved customer service at all stages of a project. Our focus is always on ensuring our customers find us easy and enjoyable to deal with. We do believe that the future is bright, and we would like to positively contribute to the success of other UK businesses, so we are all focused on working hard to make it happen.” More at www.wickens.co.uk
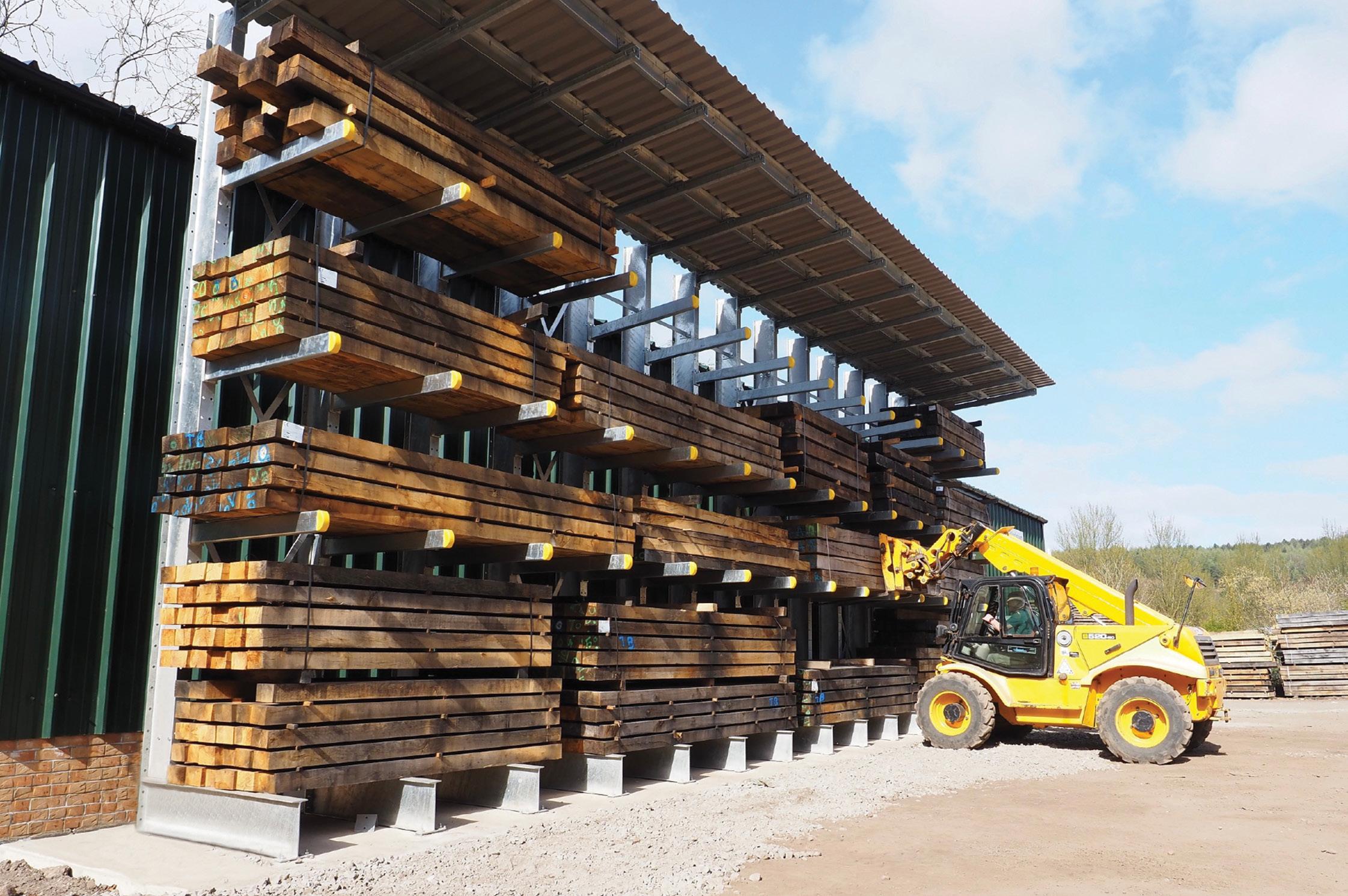