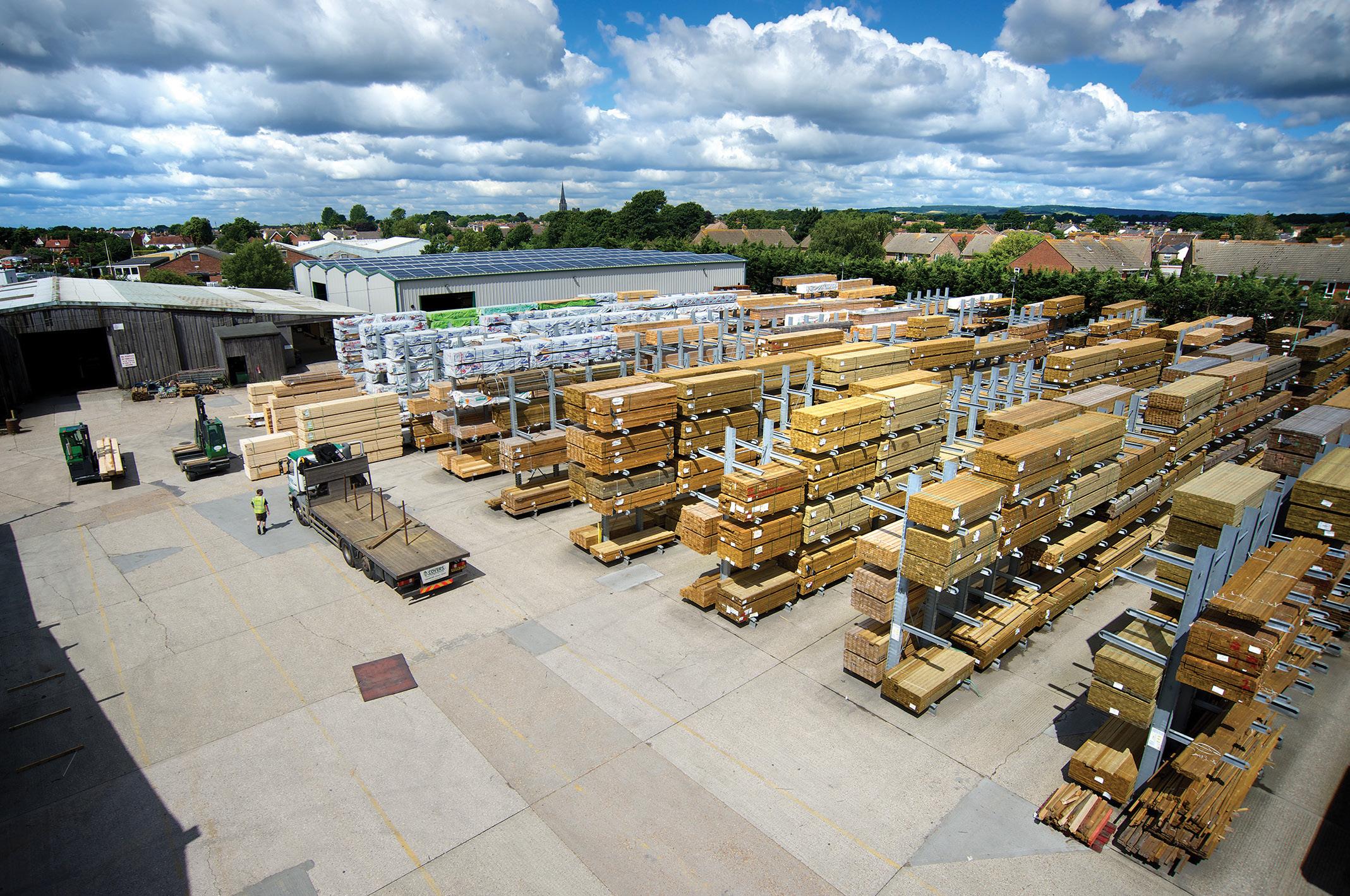
11 minute read
Keeping the Timber Market Covered
Covers has been providing a range of high-quality timber services to customers across the south of England since the early 1840s and recently celebrated 175 years of timber trading. From delivering local woods by horse and cart to its modern timber mill of today – complete with state-of-the-art equipment – this independent, family-run company has survived and thrived.
A
dapting and evolving are crucial to maintaining market share and this is something that Covers has achieved since it was founded by William Cover in Chichester. When William Cover, who was later joined by his son, David Cover, in 1857, first started trading out of the Canal Basin in the West Sussex town, their mission was to provide a friendly service that promoted unity and had community at its heart.
Bought by the Green family in the 1940s it is headed up by its current chairman, Rupert Green, and managing director, Henry Green. Covers now employs more than 400 staff and has annual sales exceeding £90 million. It is the leading family-owned timber and builders’ merchant in the south of England.
Rupert Green, chairman of Covers Timber & Builders Merchants, attributes the company’s success to their ongoing investment in, not only the business, but its people and the communities that surround them: “We have come a long way since the early days, consistently investing in our depots, vehicles and state-of-the-art timber machinery so we can offer unrivalled products and service to our trade and DIY customers.
“Covers has grown due to a dedicated team of staff – many of whom have been with us for twenty to forty years or more. This is testament to our approach to making our staff feel part of the family – we listen to them and care about what they want to tell us. They are intrinsic to our values and ensuring our customers receive expert service every step of the way.”
Modern solutions that make a difference
Covers is a constant investor in its timber mill and a keen advocate of sustainability and eco-friendly alternatives. In the 1900s, it used mechanical sawing operations driven by steam. The boilers used to produce this steam were fired with timber offcuts.
In 2016, Covers relaunched its timber mill following a multi-millionpound investment, which included expanding the range of hardwood timber stocks in a new hardwood shed and extended timber treatment facilities, such as the Tanalith green and Protim clear treatment plants. Additionally, the company made a considerable investment in two Weinig planing and moulding machines, a new production line and an extension to its existing building.
As a result, the company’s timber mill is one of the best on-site timber facilities in the south of England and creates stock and bespoke timber products of the highest quality and specifications. These include on-site timber treatments, lacquering, priming, laminating and specialist machining.
“We are extremely proud of our on-site timber mill and are continuously seeking ways to improve and invest to make it even faster for our customers,” says Rupert Green. Covers regularly produces more

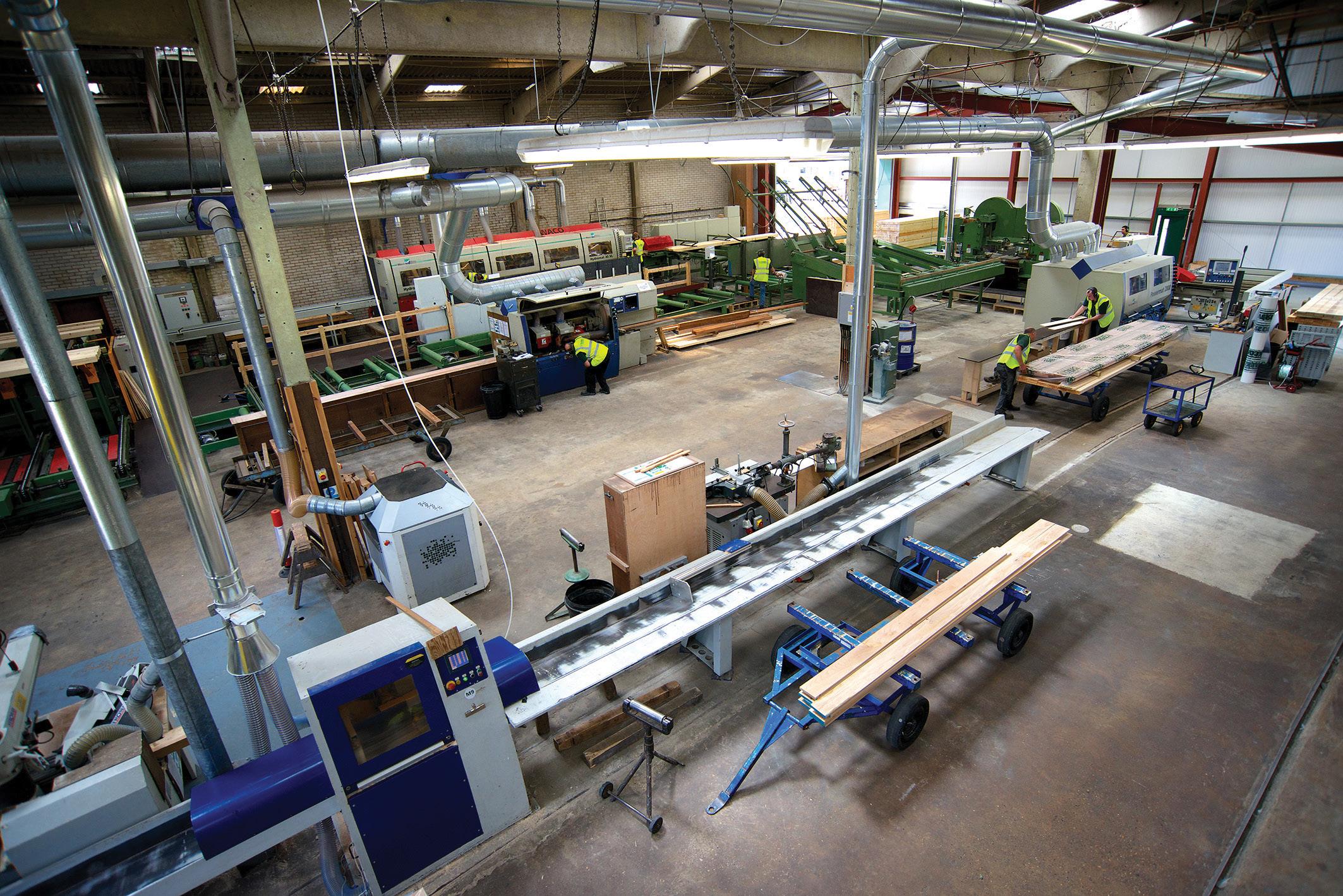
than 150km of timber per week – something that would have been impossible before the machinery was installed. The specialist machinery is also able to produce more than 200 types of mouldings, as well as bespoke creations tailored to a customer’s specific requirements.
Neil Woods joined Covers as timber director in 2017: “Our team of skilled technicians uses state-of-the-art machinery to produce timber profiles that will perfectly match or replace sections of timber grown from most wood species. Customer designs can be processed quickly and easily. Drawings are stored electronically so they can be retrieved swiftly for future orders.
“Our machinists can produce a wide range of products, including skirtings, architraves, flooring, panelling, handrails, window sections, dado and picture rails, and window and door frame sections from softwoods and hardwoods. Customers can either provide architect drawings or their own illustrations to meet specific requirements.”
Customers are everything
Timber treatments along with different cycles of treatments to cater for a variety of risk factors that might affect wood are also available. The company ensures all its Tanalised treated timbers are “Our team of skilled technicians use state-of-the-art machinery to produce timber profiles that will perfectly match or replace sections of timber grown from most wood species.”
given the correct treatment type based on the end use specification so customers can be assured they will receive timber products of the highest quality that are fit for purpose. Covers can also produce laminated sections of timber up to 3.0m long with longer lengths available to order via its specialist team.
“Materials are taken from our extensive inventory of hardwood and softwood species,” adds Neil. “Using the most appropriate glues, they are accurately bonded together under extremely high pressure and can be used for a variety of purposes, including laminated Iroko posts for heavy gates and solid oak work surfaces for desks and kitchens.”
Priming timber can be a laborious on-site job but Covers offers a quick, consistent and efficient priming service. “Our vacuum coater evenly applies paint to all four sides of a moulding in one pass and removes excess paint by using an advanced vacuum coating process resulting in a high-quality painted finish,” says Neil. The machine also supplies a vacuum-applied lacquering service to create factory-finish results and protection.
For now, the company is relishing its 175 years in business and celebrations are well underway. These include hosting a range of special events, competitions and discounts, such as supplier demo days, exclusive offers and the chance to win some top prizes like televisions, iPads and gift cards worth £175. In keeping with the spirit of its mission to serve and support communities, Covers will also be making a variety of donations throughout the year to local charities and community projects in honour of its anniversary.
“We are excited for our forthcoming programme of celebrations,” says Rupert Green. “We hope that our customers and suppliers will join us in a very happy anniversary. Here’s to another 175 years in business.”
New Directions for 2022
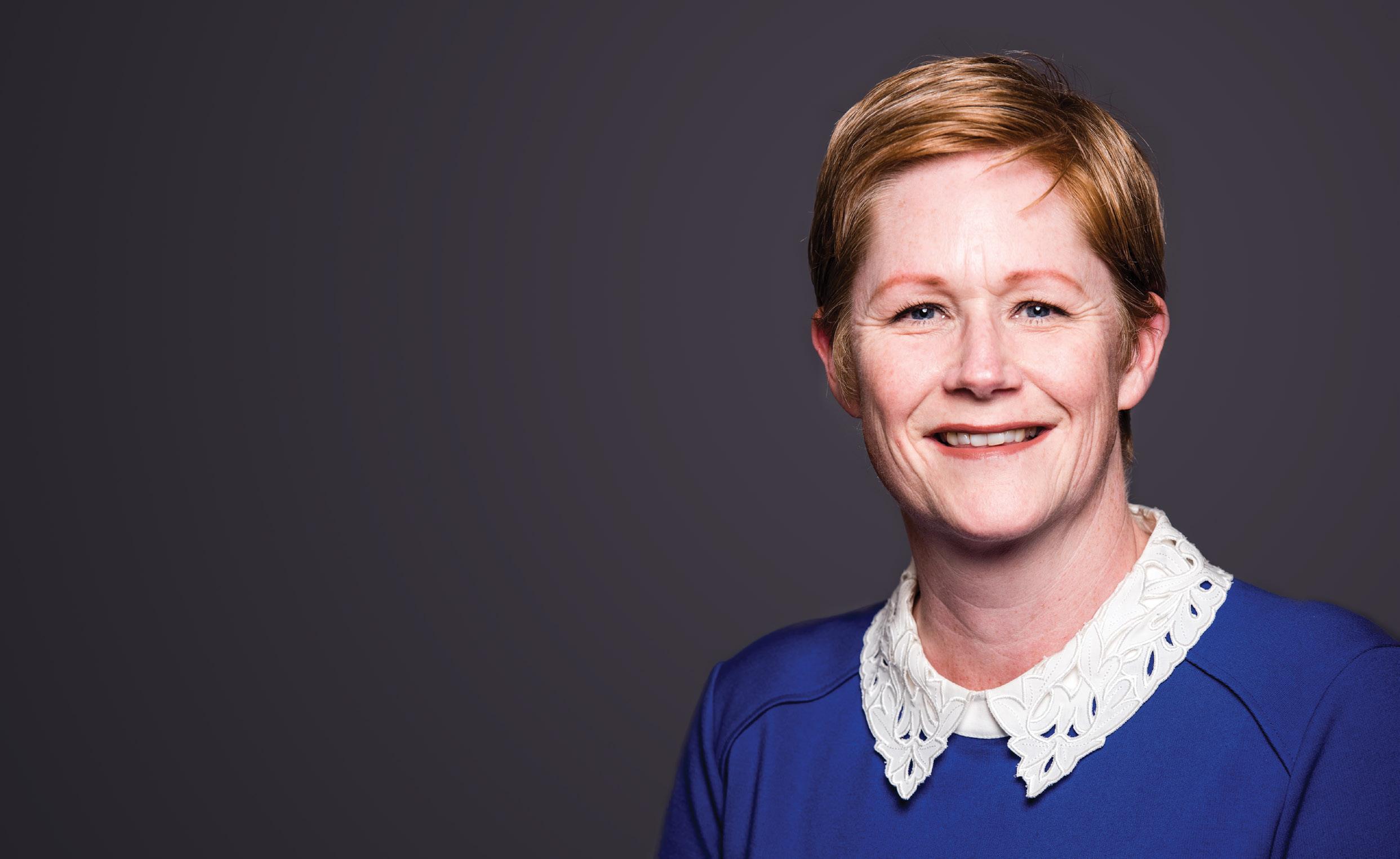
Helen Hewitt, CEO of the British Woodworking Federation (BWF) sees many challenges and opportunities ahead in 2022 for the woodworking and joinery sector.
O
ur sector has had to overcome major hurdles in the past 12 months, including supply chain interruption, the increase in the cost of materials and rising labour shortages. Although data from the Timber Trade Federation (TTF) highlights that the supply chain challenges are stabilising, we know from our recent BWF membership survey that these issues remain front of mind for our members’ as we enter 2022. The BWF will continue to respond to the challenges facing our members and the wider sector, as well as ensure we take advantage of the many opportunities that lie ahead.
Ensuring the voice of our sector is heard
Throughout 2022, we will be working closely with our members and industry partners to find new and innovative ways of raising the profile of the sector with government and other stakeholders.
An essential part of this will be our rigorous programme of meetings with MPs, which will help ensure that the voices and views of the woodworking and joinery sector continue to be heard and that the sector is correctly positioned to advise government.
Our 6-Point Blueprint for Wood will play a crucial role in conversations with stakeholders over the coming 12 months and allow us to champion timber as the sustainable product of choice in the construction industry, demonstrating how it can help the UK become a built environment global leader.
Not only will this enable the UK to take positive steps towards more sustainable construction, but it will help maximise opportunities for our members. As part of this, the BWF’s Build it Better with Wood campaign will promote why wood should be considered by homeowners and developers for windows and doors, staircases, home furnishings and, where possible, as a construction material.
Guidance on regulatory changes
A key component of the Building Safety Bill, announced last year in the House of Commons, is a requirement for the accountable person to retain fire and structural safety information, often known as the ‘golden thread’. The golden thread will mean that important information regarding building materials will need to be passed between stakeholders throughout the building’s lifecycle. This is a significant step forward for maintaining fire safety products that are installed within a building, particularly fire doors.
Throughout 2022, the BWF will also be continuing our Be Certain Be Certified awareness campaign to promote the importance of third-party certification and what key audiences should be looking for when procuring lifesaving products such as fire doors.
There are other long-awaited changes coming into effect that will impact manufacturers in the timber sector, such as the new Code for Construction Products Information (CCPI) launched by the Construction Products Association in response to Dame Judith Hackitt’s ‘Building A Safer Future’ report. The Code will set the benchmark for how product information is presented and marketed by manufacturers. The BWF will be sproviding updates, support and guidance as the code is implemented.
The BWF will respond and comment on consultations and amendments to regulations that will impact on our sector, as well as representing the industry on technical committees. We will be continuing to provide our members with detailed insight, and we’re delighted that, as part of this, BWF Technical Director Kevin Underwood has been appointed as Vice Chair of the Construction Products Technical Committee, and Chair of BSI Technical Committee for Stairs (B/208).
Attracting and developing talent
The COVID-19 pandemic has undoubtedly had a significant impact on our sector’s skills and training efforts, reducing the opportunity for employers to provide much needed apprenticeships and continued professional development for employees. Developing the skills of our current and future workforce is one of our biggest priorities as an industry and remains one of my personal goals as CEO of the BWF.
The BWF is constantly reviewing its skills and training offering to ensure it meets the needs of our members and the sector, resulting in the development of e-learning and face-to-face training courses which are available to members and non-members in the sector. We’ve also had fantastic success and uptake of the first quality assured training course, which we launched with the National College Open Network (NOCN). To date, more than 600 individuals have gained knowledge in the principles of Fire Door Installation and a further 195 have taken our new e-learning course in Fire Door Awareness.
In 2022 the BWF will be launching more online training courses across areas including windows, doors and stairs, to educate and inform those who are new to the industry and upskill those already working in the sector. We will also be launching a campaign to highlight the opportunities, diverse roles, and career paths that exist within the woodworking and joinery sector. The campaign will encourage the next generation to consider a career in the woodworking and joinery sector through an apprenticeship route.
It’s important to look back at all the challenges we’re overcome to remind us of the resilience our sector has demonstrated. There are considerable opportunities available for the woodworking and joinery manufacture sector as we look to the year ahead, and the BWF looks forward to supporting members and the wider sector to maximise these opportunities.
More at www.bwf.org.uk

New trainees join Glasgow construction company’s ‘offsite manufacturing’ division
CCG (OSM) Ltd has commenced its recruitment drive for 2022 with the appointment of two new trainees. Based in Glasgow, OSM is a division of the CCG (Scotland) Group, one of the country’s largest privately-owned construction and manufacturing companies and a key contributor to skills development and replenishment in the Scottish construction industry.
The firm employs over 120 direct employees with their new recruits, Stuart Hunter (29) and Greig Barnstaple (19), set to undertake training programmes in timber frame design and quantity surveying respectively in ‘offsite manufacturing’; a process that refers to the ‘design, manufacture and assembly of building elements at a location other than their final place of installation to support rapid and efficient construction’. In the case of CCG OSM, entire walls (integrated with windows, doors, insulation, and linings) are completed in their bespoke factory setting before being transported to a construction site, principally supporting CCG (Scotland)’s delivery of over 1500 homes every year as well as care accommodation for the elderly, nurseries and schools.
CCG OSM Director, David Crawford, said: “The Scottish construction industry has evolved greatly over the last 20 years and the CCG Group has been at its forefront. With impending changes to building standards and our move to become a ‘net zero’ economy by 2045, further evolution is ahead of us, and ‘offsite’ construction methods will be vital in reaching the necessary, enhanced levels of performance and quality for new build construction.
“The modernisation of construction practices also goes in hand with our industry’s approach to skills replenishment and development. ‘Offsite’ is a scientific, technological process so there is a great opportunity to attract new talent to the industry as the market for this form of construction continues to grow. Skills replenishment and training is a key element of the CCG Group’s ethos, and the appointments of both Greig and Stuart are examples of how we are continuing to pioneer offsite in Scotland. I’m delighted to welcome them both to our business and look forward to seeing how they progress over the coming years.”
More at www.c-c-g.co.uk
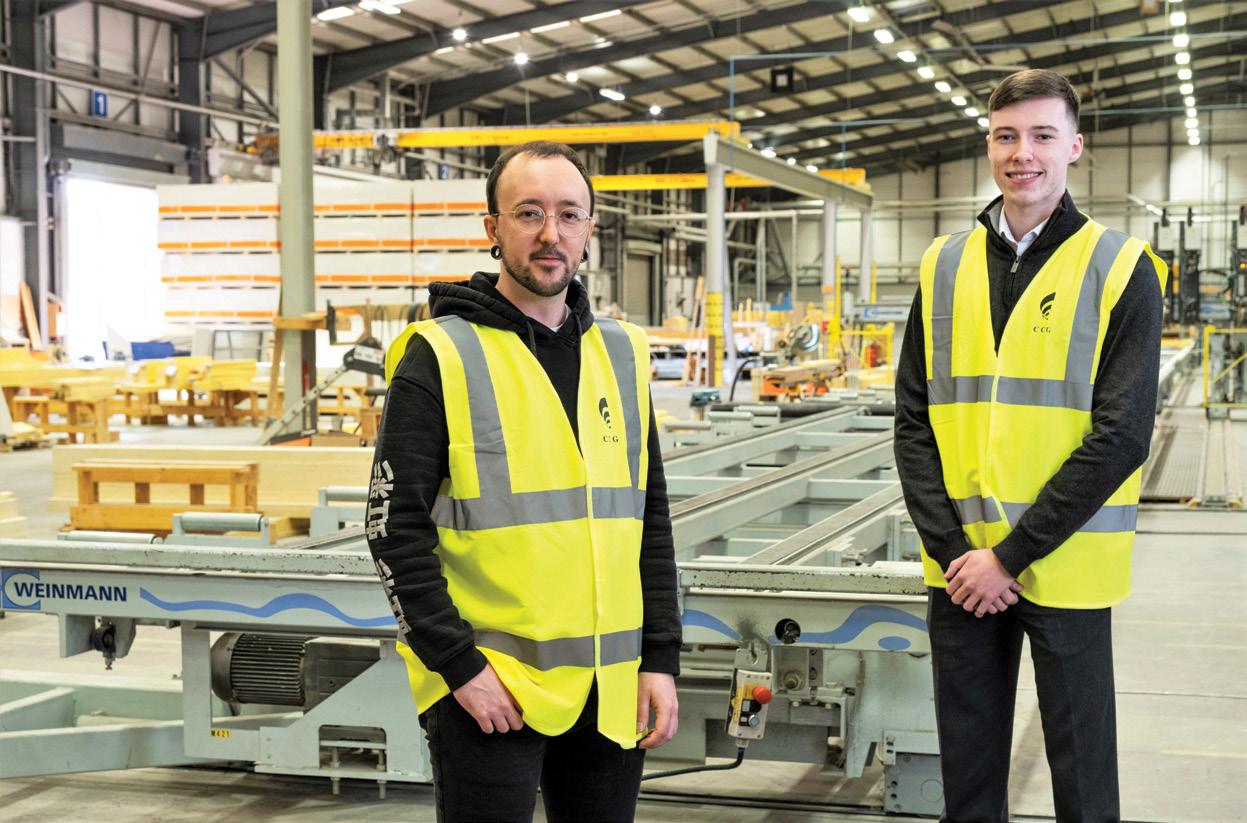
Creativity isn’t just in the mind. It’s in the connections.
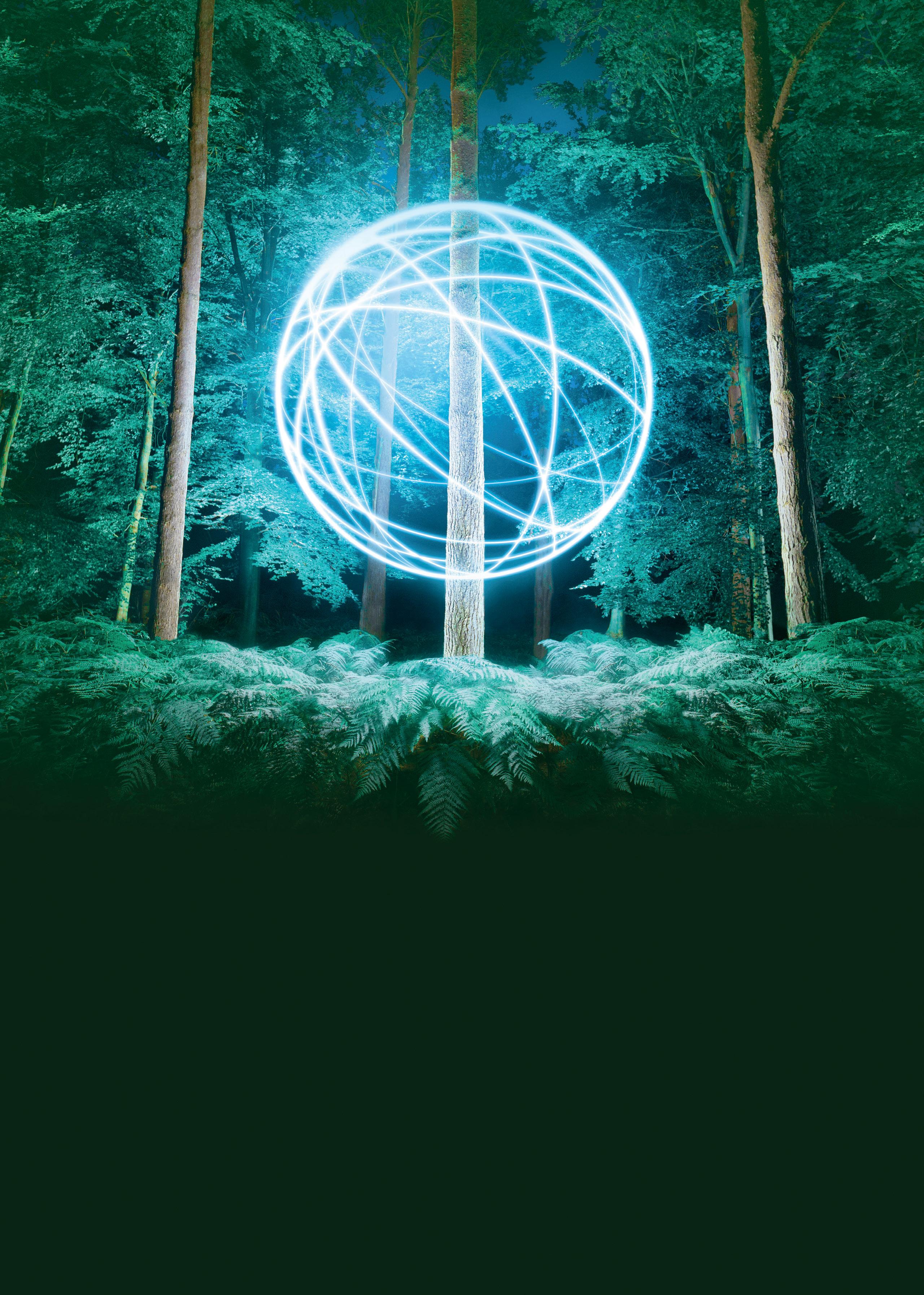
Innovation is about forming new connections to inspire fresh thinking. So we’re uniting our industry, bringing together experts to share ideas and accelerate change. It’s how we develop cutting-edge products and services, like IRO Timber and CarbonStore. And it’s how we can create future growth that’s both profitable and sustainable.