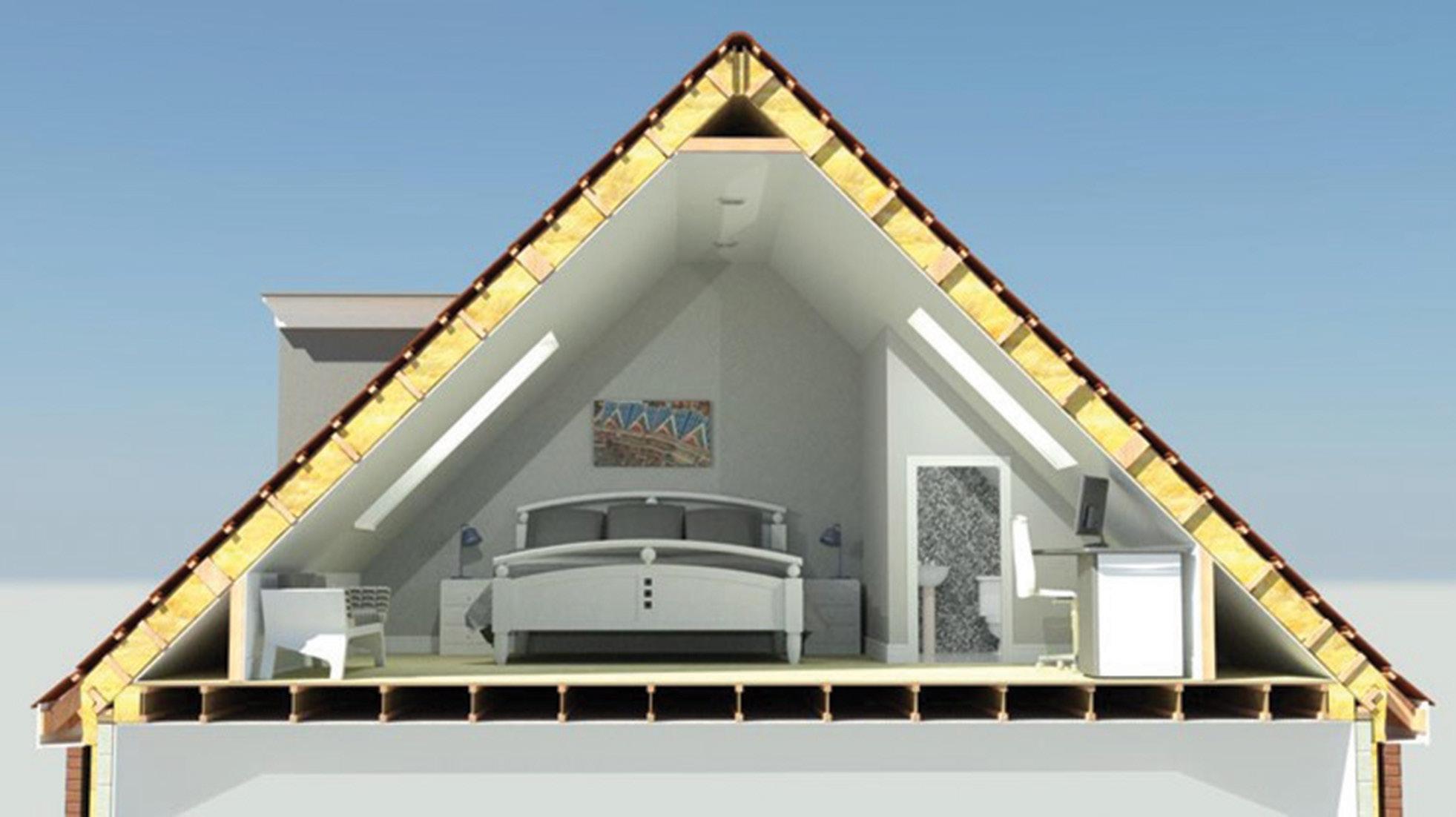
6 minute read
Part L and Going for Greener
Image © Smartroof
Getting to grips with the updated Part L of the Building Regulations should be at the forefront of anyone wishing to achieve a net zero target and improve their building’s thermal performance.
A
As the new Approved Document Part L of the Building Regulations is now in place, minds are focused on how the new guidance will modify energy efficiency standards and thermal efficiency of newbuild homes in England and Wales.
With the climate emergency declared, housebuilders are now expected to work harder to tackle carbon reduction. With energy bills likely to be unstable for some time, the recent changes are acting as a transitional step towards the Future Homes Standard, designed to reduce greenhouse gas emissions from the UK’s built environment.
At the centre of Part L are the guidelines for constructing homes with low carbon heating technology and high energy efficiency, so the housebuilding industry and homeowners can reach the UK’s 2050 net zero targets. Under Part L, all new homes must now produce 31% less CO2 emissions in operation than what was acceptable under the previous Part L Building Regulations. To help, the new guidance outlines a raft of changes that new homebuilders must work towards to increase energy performance standards. The Future Homes Standard, which comes into effect in 2025 represents a further uplift in domestic energy usage. Homes built from that date will be expected to produce 75-80% fewer carbon emissions compared to current standards.
The 31% reduction of emissions can be achieved through a better ‘fabric first’ approach. A massive part of the change in improving thermal efficiency is also the correctly specified and installed insulation material – a vital building fabric component – and key to new homes achieving Approved Document O (Overheating) of the Building Regulations. Also introduced earlier this year, Part O accompanies the Part L regulations to improve ventilation and prevent properties overheating and suffering from high solar gain. Correctly installed in floors, walls and roofspace, the many types of insulation (including low carbon woodfibre) provide a barrier that prevents exterior temperatures outside from impacting interior air conditions and helping maintain a steady indoors climate – whatever the weather outside. Well-insulated building fabric helps save energy and reduces bills. A recent report by the Department for Business, Energy & Industrial Strategy, revealed that heating and power account for 40% cent of the UK’s total energy use, hence the need to address the thermal performance of the UK’s 28 million homes.
Offsite thermal options
Faced with these ambitious aims and the upcoming Future Homes Standard, Smartroof’s offsite modular roof system is an example of a system that meets these ambitious targets and can lower carbon emissions, address heat loss and is proving to be one of the most cost-effective and efficient ways for housebuilders to address thermal bridging at junction details within the roof build-up.
Tom Wright, Design and Technical Director at Smartroof, says: “The Smartroof solution offers a wide range of U-values. This offers significant increases in design flexibility as its insulation levels can be adjusted to suit the customer’s requirements. Not only does this allow the client to ‘futureproof’ their roof, but it also potentially offers significant cost savings as the SAP assessor can trade off gains from one
U-values
SAP 10, the latest update to the Standard Assessment Procedure (SAP) is incorporated within the revised Part L regulations and designed to ensure correct thermal modelling junctions are used.
When it comes to achieving U-values for domestic newbuild projects it is a requirement for an energy consultant to give SAP advice. SAP informs the thermal ratings of walls, floors, roofs, junction details and any bolt-on renewable technologies – the performance of which must correspond with or exceed the required regulations for the building. These elements can be changed if the property achieves the required dwelling performance. The alternative to a SAP assessment is to work on the notional dwelling specification, which must be followed as a minimum to achieve a pass. In addition, to add clarity on how to carry out U-value calculations, the updated Conventions for U-value calculations – aka BR443 – came into force in June in England and will be adopted later this year when respective Building Regulations are also changed in Scotland and Wales.
More at https://bregroup.com/sap
area to another. Achieving higher Fabric Energy Efficiency Standards (FEES) in house types specification’s will be crucial for housebuilders in order to pass SAP and comply with Part L.
“Smartroof recently carried out an independent assessment of its junction details to assess the psi value. All details have outperformed the psi values given as default in table K1 for 2020 regs. Smartroof will happily make these details available so that SAP assessors can take these into account. The ‘loft zone’ above the ceiling in a room-in-roof system will have a negative effect on SAP calculations and result in a higher U-value specification for roof components. The result will be more expensive materials and/or more follow-on trades. The majority of Smartroof systems have no structural beams, thus allowing the housebuilder flexibility to adjust their ceiling height. A system with structural beams is likely to be more restrictive when adjusting ceiling height and will result in costly compromises.
“We have always worked closely with leading SAP assessors and its ‘room in roof’ panel system is already meeting the standards required. Computer modelling enables the company to produce bespoke roofs that are tailored to a client’s needs. Production of the Smartroof system in a factory environment ensures no cold spots in the panels or spandrels that may arise from more traditional methods onsite. The system’s design makes it inherently airtight and an ideal roof solution for those developers adopting a fabric first approach. Smartroof’s in-house production facility enables it to stock a wide range of materials and insulations to ensure it meets every customer’s thermal requirement.
As the construction industry continues to attempt to secure net zero emissions across the built environment, the new Part L requirement will play a major role, alongside innovative products and systems that provide people with energy-efficient – and affordable – homes that will still be saving energy both now and for years to come.
To read more about the changes Conservation of fuel and power: Approved Document L go to www.gov.uk/government/ publications/conservation-of-fuel-and-power-approved-document-l
More about Smartroof at www.smartroof.co.uk
Insulation Boost
Earlier this year, Knauf Insulation invested over £45 million across its two UK Glass Mineral Wool plants to boost capacity as well as improve the range, availability and sustainability of its products for the benefit of its customers.
As a result of the investment, Knauf Insulation expects to see a circa 20% improvement in the embodied carbon of products supplied from its St Helens plant, building further on its industry-leading position in terms of sustainability.
Neil Hargreaves, managing director of Knauf Insulation Northern Europe said: “These investments support the anticipated growth in demand driven by the Future Homes Standard and improved energy efficiency in new buildings as well as from more renovation of existing buildings. These developments are critical as we step up our efforts to tackle the cost-of-living crisis, climate change and energy security.”
More at www.knaufinsulation.co.uk
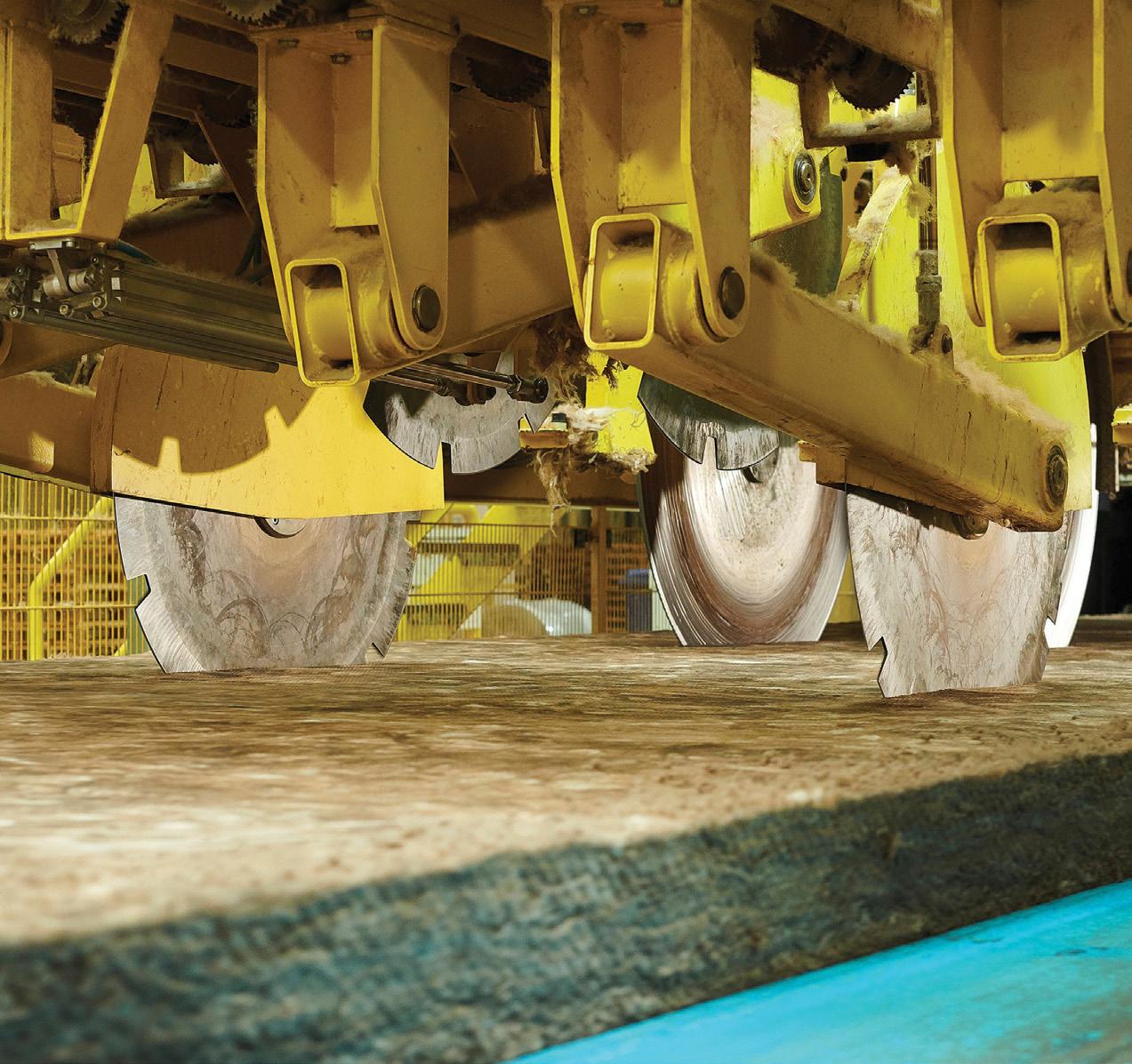