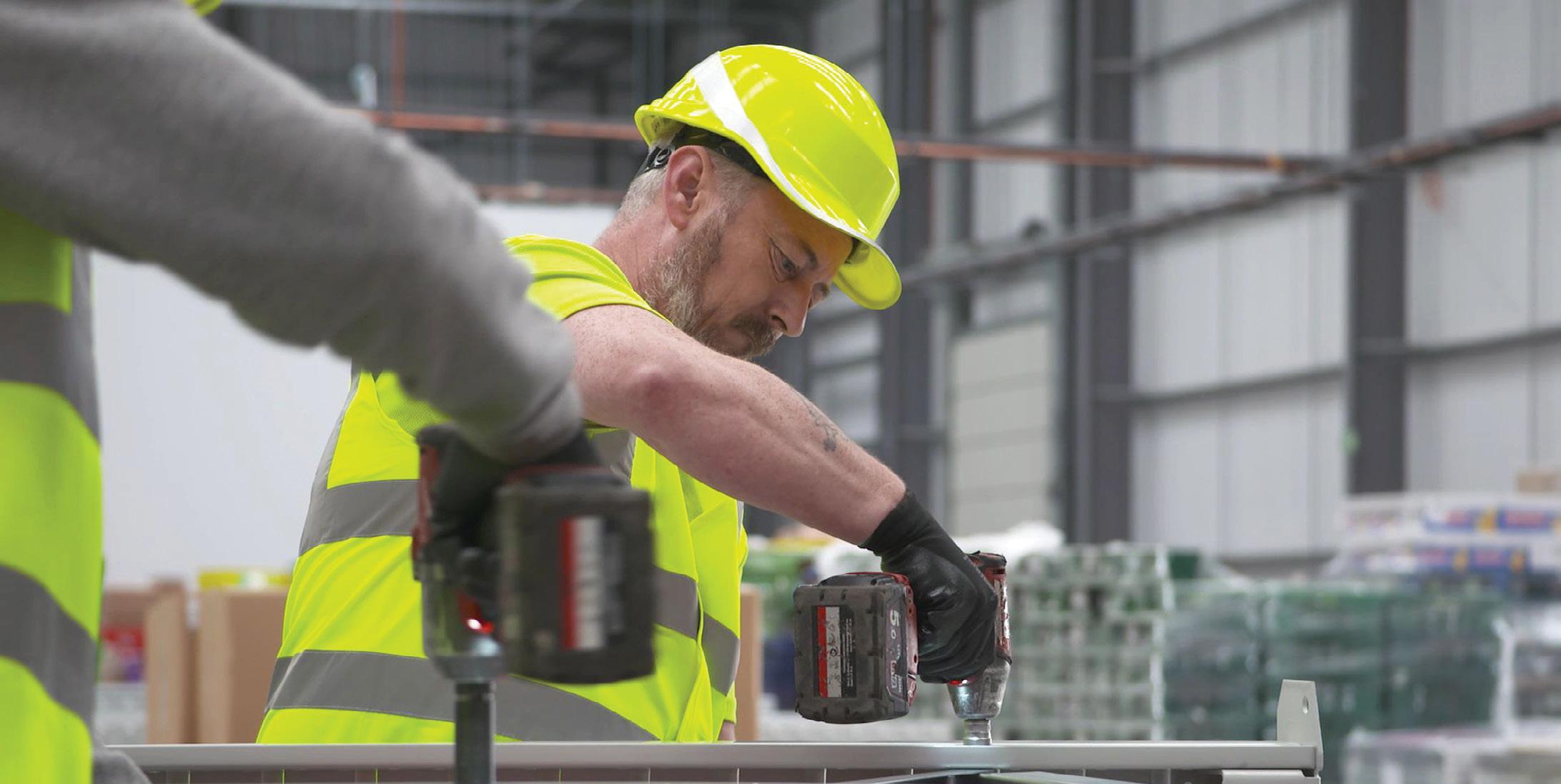
3 minute read
The Importance of Training
Have you considered the consequences if a bad accident happened at your workplace? The nightmare of sorting out the legalities, tidying up any mess and dealing with a visit from the HSE? The Storage Equipment Manufacturer’s Association (SEMA) can help stop a problem before it happens.
Employee and customer safety is hugely important and adopting correct Health & Safety processes in the workplace is critical, but this must extend through to your storage equipment – an area that can be easily forgotten.
Fortunately, fatal racking accidents are rare in this country but there is always the potential for them to happen. We certainly know our SEMA Approved Racking Inspectors have plenty of real-life stories to tell on the ‘what could have happened’ and ‘what might have been’ scenarios.
Get the basics right
The process of ensuring that your storage is safe starts at the point when you decide to buy the equipment. You need to select storage equipment that has been designed and independently assessed to ensure it will live up to its intended role. The design should address the space and width of your unit, maximise your storage capability, improve efficiencies and protect employees around the warehouse.
Once on site, the racking must be installed correctly to meet manufacturer and industry specifications using installers who have been correctly trained.

What happens when the equipment has been installed? You load the racking, and everyone starts using it. But this is when the problems can start. When in use your racking will be subject to knocks and bumps. These ‘little incidents’ can develop into serious problems with the risk level usually increases if the damage is left unchecked.
Meet Your Racking Responsibilities
You should be aware that your racking is classed as work equipment. Under PUWER (Provisions and Use of Work Equipment Regulations 1998) you have a responsibility to ensure it is suitable for the intended use, safe to use, maintained in a safe condition and inspected. You must ensure it is only used by people who have received adequate information, instruction and training.
When it comes to the ongoing maintenance of your racking the ideal solution is to equip your employees with the tools to become safety advocates. They will be using it daily, making them ideally situated to notice if anything goes wrong. This can only happen successfully if they have been trained on how to correctly load and work with the racking.
Training, training, training
At SEMA we believe that training plays an essential role in maximising safety levels, and it is something we instil throughout the lifetime of a racking structure. For example, we have a national registration programme for installers of racking equipment called SEIRS. An important element of the programme is to train under assessment conditions on the safe and correct installation methods to meet SEMA defined standards and also manufacturer’s specifications. This includes very important details that guarantee the integrity of your structure such as the number and type of floor fixings and how they should be positioned and tightened to meet manufacturers’ tolerances. We also advocate training for your employees, our Rack Safety Awareness course has been developed around the SEMA Users Code (and other guidance) and very specific to end users sites. This recommends that warehouse and management should nominate a Person Responsible for Racking Safety (PRRS). The PRRS is responsible for ensuring the racking is correctly used, inspected and maintained.
The course also provides guidance on the best inspection routine to implement. It will advise on how to conduct a risk assessment, record an inspection and report on damage levels and action points. Committing to a structured inspection should identify any problems early and can significantly reduce costly maintenance bills.
What if my racking needs repair work?
Be aware that any work on your storage equipment could affect your manufacturer’s warranty. For example, when you buy a structure manufactured by a SEMA Full Member it provides reassurance that a
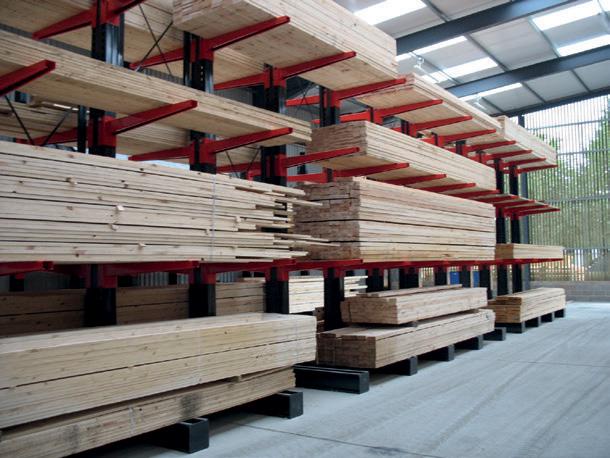
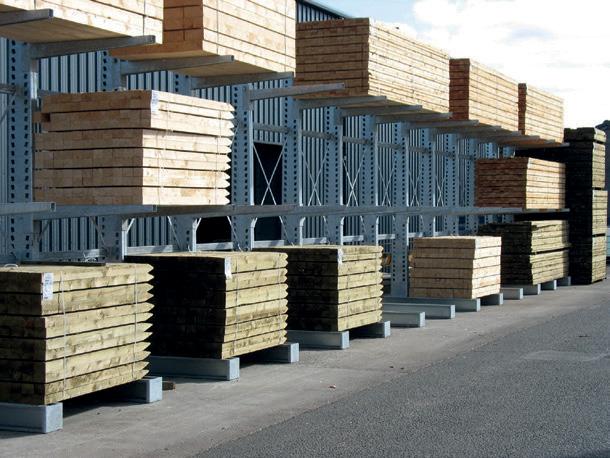
For over 50 years, SEMA has been working hard to provide technical standards and guidance to the storage industry with aim of enhancing safety over the lifetime of your racking. As a leading voice within the industry, our work is upheld by member companies who are united in raising standards and helping warehouse owners meet their legal obligations. SEMA manufacturing members’ products are independently tested to guarantee they have been designed, manufactured and installed structural engineer has designed it to meet SEMA codes and independent tests have been conducted on the equipment to ensure it meets its intended role. Any unauthorised work or repairs could dramatically impact the integrity of the structure. to rigorously defined standards. SEMA Distributor Companies and SEMA Approved Installation Companies are routinely audited to ensure they consistently meet industry standards, Codes of Practice and legislative requirements. The circle is completed by our SEMA Approved Rack Inspector and SEIRS training initiative for installers.
At SEMA we have a supportive structure of distributor and installation companies who are qualified to conduct work on the manufacturer’s behalf. For peace of mind always check that the installers erecting your equipment are correctly trained and qualified to do the job. Ask to see their SEIRS card before any work starts – it’s the best way to maximise safety.
You can find out more about SEMA training courses by emailing: enquiry@sema.org.uk or visiting www.sema.org.uk
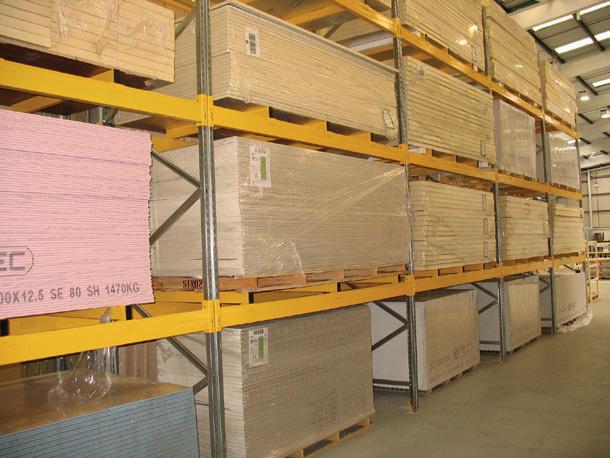
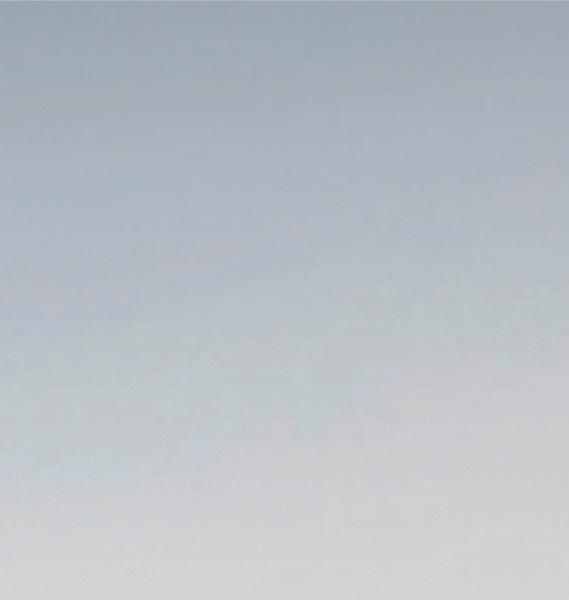
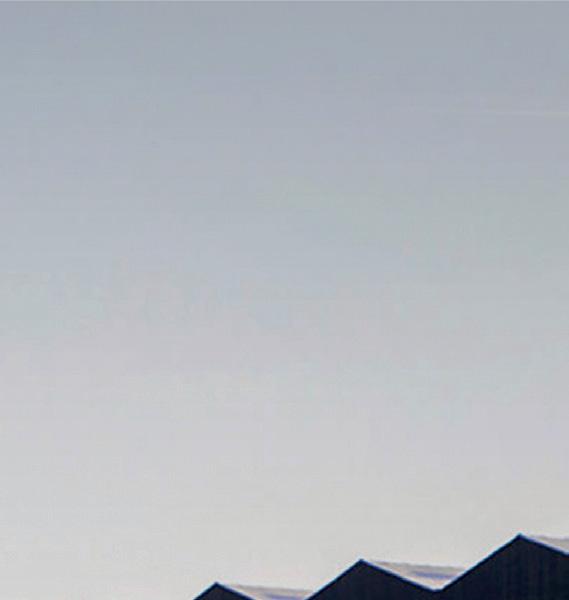



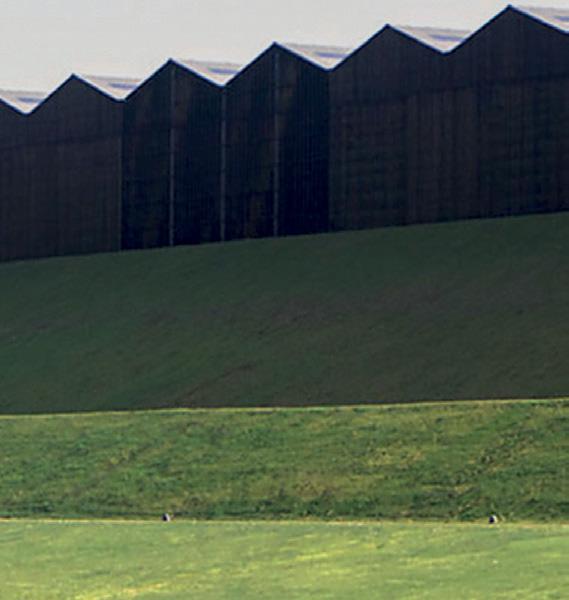



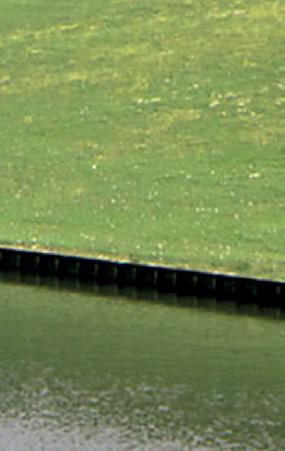

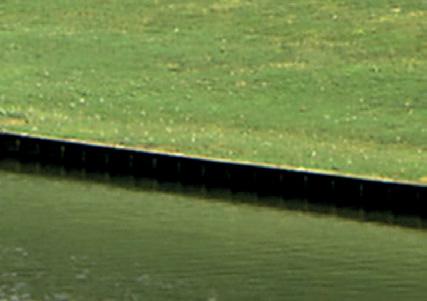
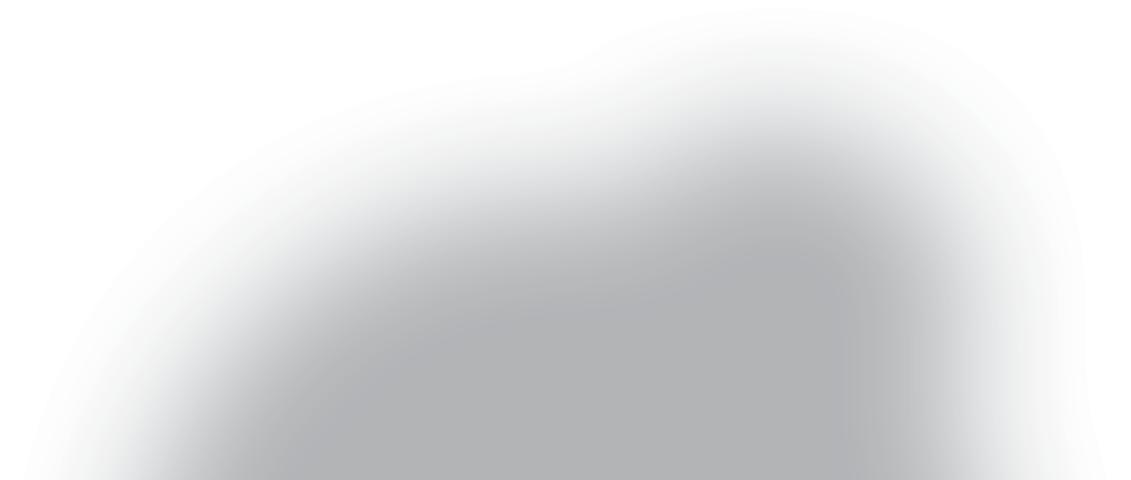
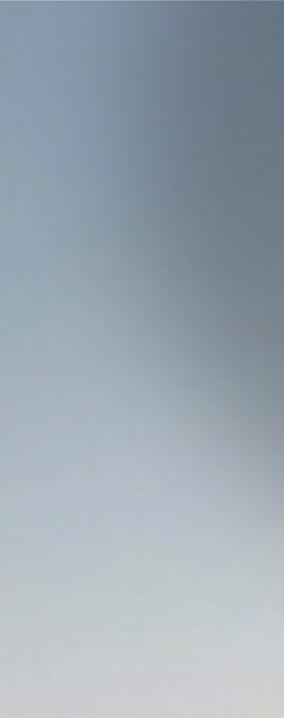

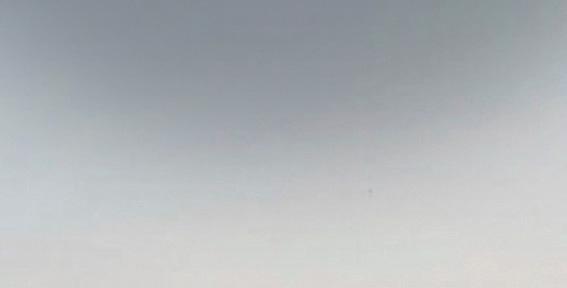
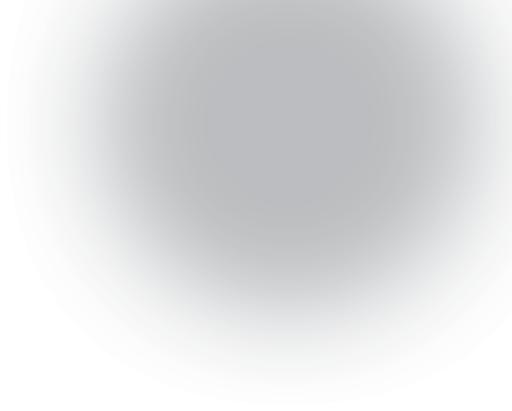