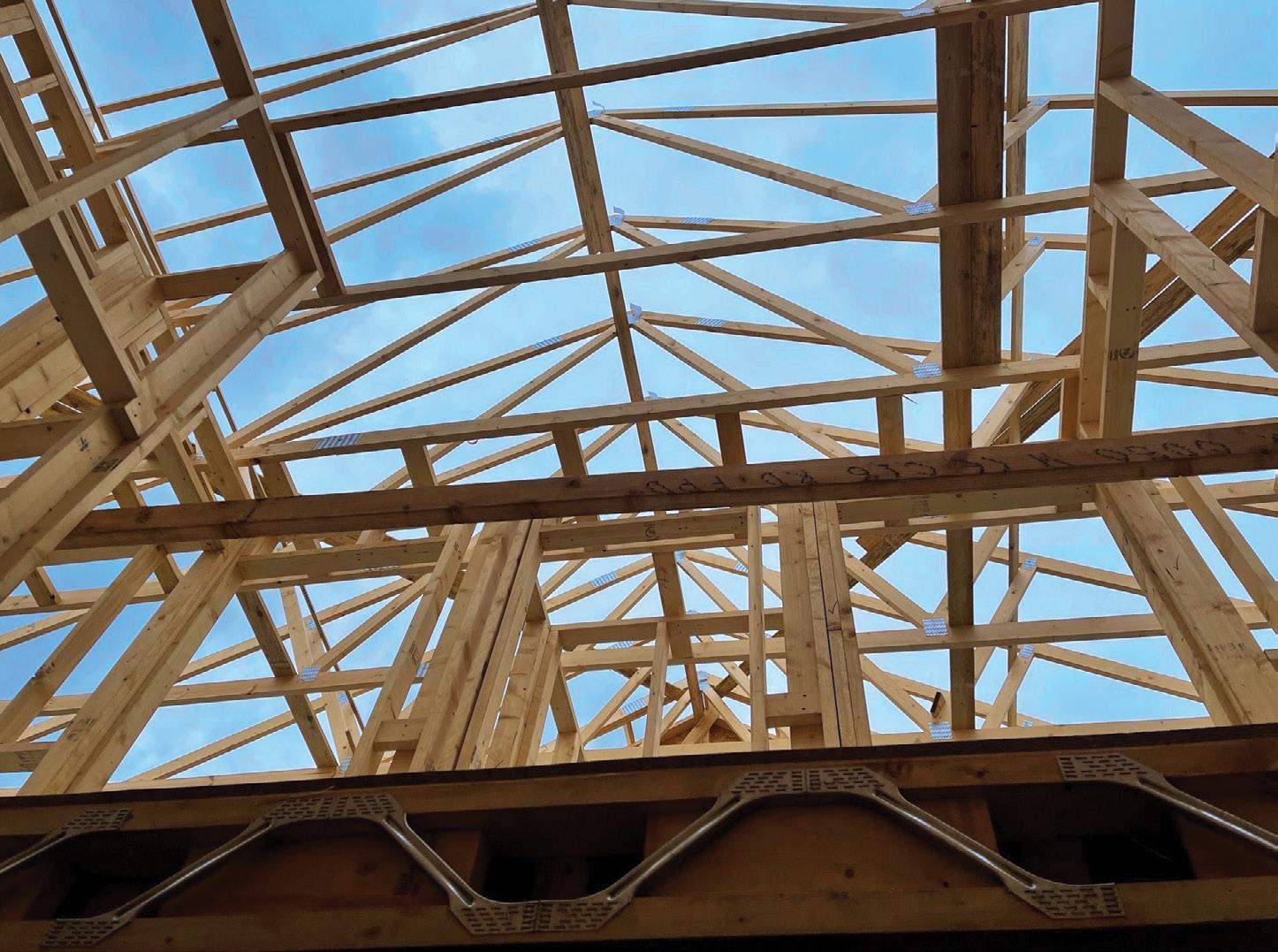
2 minute read
Optimum Energy Performance
In order to meet spiralling energy costs and our climate change targets, new technologies and modern offsite construction methods can maximise energy savings through their structural components, whilst meeting the latest building standards.
Energy efficiency and the increase in fabric standards are at heart of the Future Homes Standard (FHS) which will ensure that all new homes built from 2025 will produce 75-80% less carbon emissions than homes delivered under current regulations. This will be achieved by having high levels of energy efficiency through a fabric first approach and low carbon heating systems.
A fabric first approach to design encourages the performance optimisation of the walls, roofs, windows, doors and floors. This approach allows the building to effectively retain heat and can greatly reduce the energy requirements necessary to maintain a comfortable indoor environment.
First pioneered by the Passive House Institute, this focus on the building fabric prioritises low U-values and minimal air leakage. The U-values of the notional building have been reduced in the recent regulation change (0.18 W/m2K for exterior walls for example) which highlights the move towards improved fabric performance. When the building fabric is well designed and insulated this will reduce the demands on renewable heating systems such as air source heat pumps which will only work effectively when the fabric is of a good standard.
Timber frame design
Offsite timber frame construction can provide the ideal fabric for buildings to achieve low energy demands and the new U-value requirements set out in Approved Document
L. Offsite manufacturers have had to respond to the reduction in U-value targets to ensure their system is compliant with new regulations, and end user demands for more energy efficient homes. In doing so, many timber frame manufacturers have reviewed their wall build ups in pursuit of an optimised solution.
While increasing insulation thickness is the obvious solution to lowering U-values, this is not always cost effective. In addition, it increases the wall thickness which can impact footings, internal floor area and the erection processes. As an alternative, many manufacturers are exploring the use of reflective foil breather membranes and vapour control layers (VCL).
Reflective foil membranes are designed to perform their primary function (protect against wind and rain, or control water vapour) as well as improve the heat retention of a building element. When these membranes are installed adjacent to a cavity, they enhance the reflective value (R value) of that cavity – remember, the higher the R value, the better.
Open and closed panel timber fraes
The UK timber frame industry is made up of a mix of open panel systems and closed panel systems. Put simply, open panel systems typically install a breather membrane in the factory, but leave the internal side of the panel open, while closed panel systems apply internal sheathing to the panel, and in many cases, also install the VCL in the factory.
Both open and closed panel systems can benefit from switching standard membranes to reflective foil membranes. For example, one of our existing customers had been building an open panel until recently. They were achieving a U-value of 0.21 W/m2K when using a standard breather membrane externally and no VCL. By swapping from a standard breather membrane to Partel ECHOFOIL EXO, they can reduce their U-value to 0.18 W/m2K. If they were to close the panel in the factory, and install Partel ECHOFOIL IZO as well, they would achieve a U-value of 0.16 W/m2K. Remember, this U-value improvement can be achieved without increasing the wall thickness. While this example is specific to this customer’s wall build up, it can give an indication of the benefit of using the Partel ECHOFOIL range in timber frame construction.
At a time when energy efficiency and net zero carbon is high on the agenda, offsite timber construction is being seen as one of the most attractive ways of delivering buildings that are high quality, sustainable and cost effective. The development of reflective foil membranes which offer high performance and can meet new the thermal and air permeability targets is set to revolutionise the way timber frame structures are designed and built.
More at www.partel.co.uk