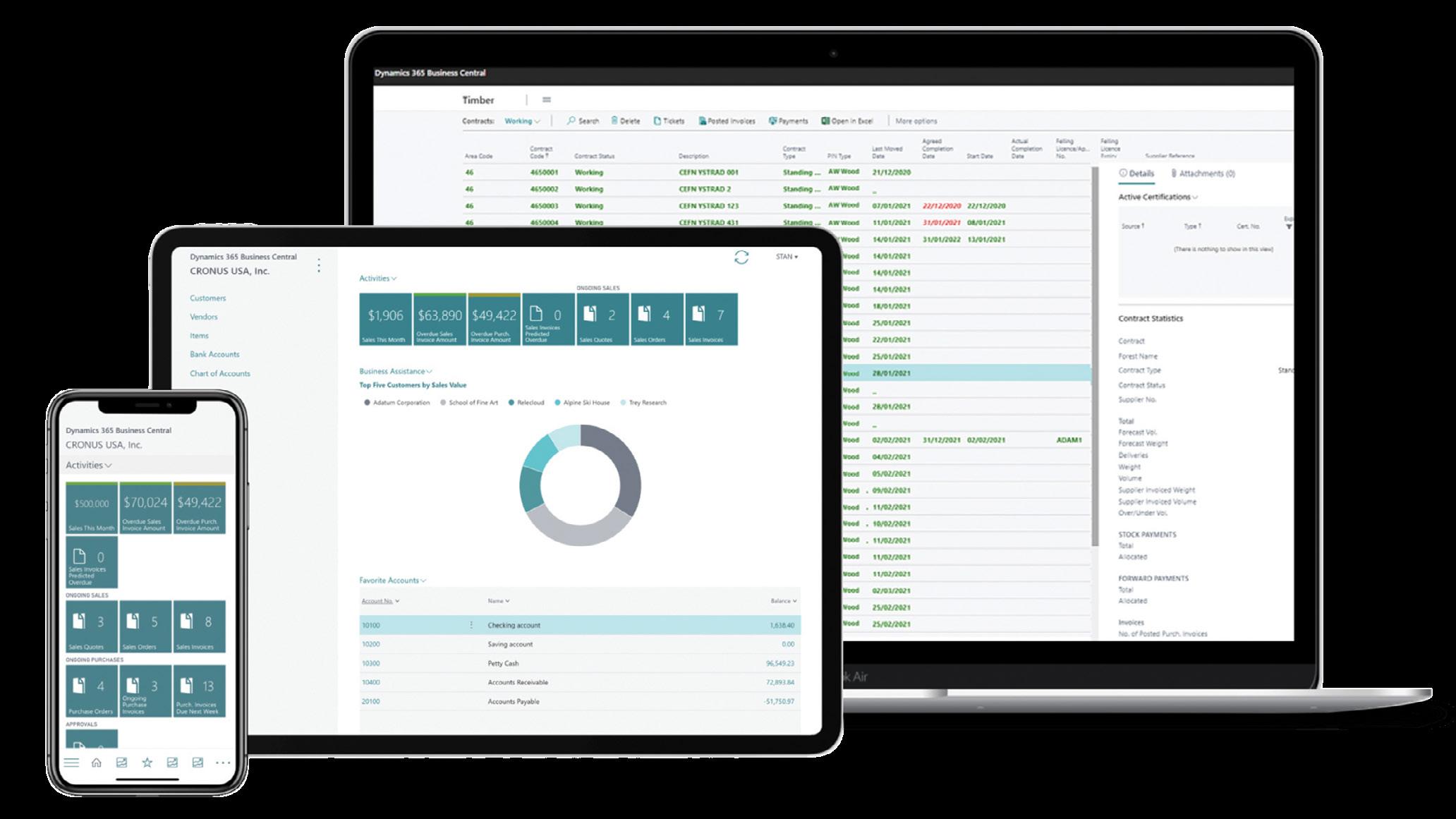
4 minute read
Transforming Information Management
Kenny Doole, commercial director, Turnkey Group, sees adopting smart manufacturing and automation as key elements of digital transformation and increasingly central to the way that timber merchants now work.
C
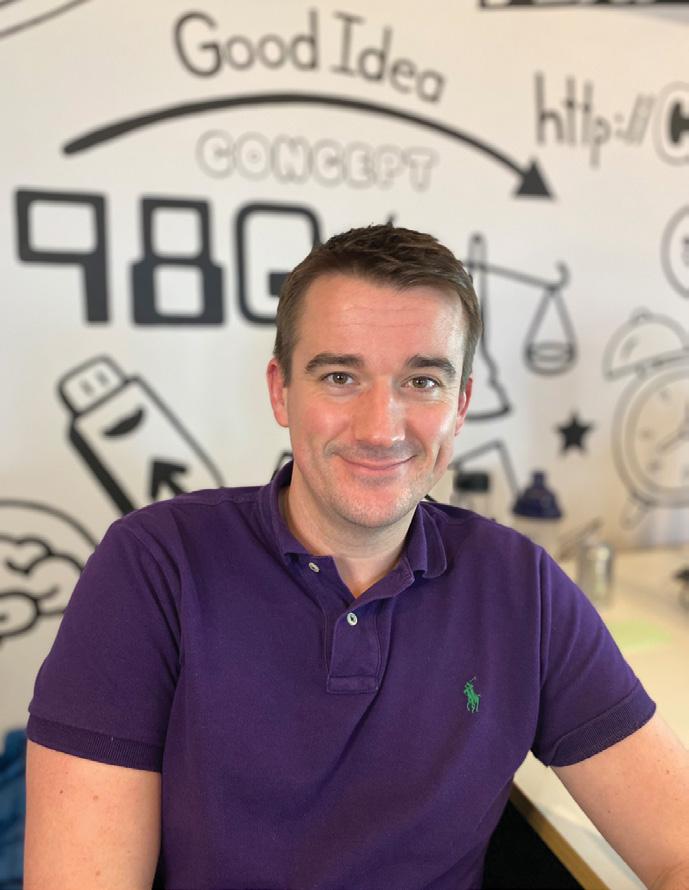
ustomers across the timber industry are making a significant shift in how they use technology to achieve and drive business efficiencies. Embracing paperless processes underpins this move, understanding how to utilise technology to directly interface with manufacturing equipment, and automating repetitive tasks where possible.
Despite the rapid evolution of technology, some businesses are still antiquated in the way they approach data and systems. In an ever-changing digital world, the need for wholly integrated software systems that bring together people, processes and technology has never been greater.
Why integration?
Together, the use of smart manufacturing and equipment integration can drive automation and data exchange. For example, having a direct interface to sawmilling equipment or weighbridges means teams’ productivity increases and errors are reduced by eliminating manual, often repetitive, data entries.
Historically, making investments in new equipment meant trawling through up to a years’ worth of physical data sheets and manually extracting relevant data. With modern systems operational teams can get instant access to data in a format to suit them. Furthermore, data analytics can be easily provided in the form of graphs and charts giving businesses a snapshot of performance and allowing them to make rapid, informed decisions.
With a product such as the Turnkey Timber software, integrating XML feeds directly from the Forestry Commission (UK) & Coillte (Ireland) systems can advise the user of incoming deliveries. Electronic Data Interchange (EDI) allows the system to then capture contract details, including map locations electronically from key partners.
Kenny Doole, commercial director of Turnkey Group
Embracing digital transformation
Digitisation can support all the areas of the timber industry from harvesting to sawmilling, timber sales, timber merchants to co-products including biomass.
Liam Kearns, ICT Manager, ECC Timber Products
Digitising processes provides a complete transparent document trail for a logs journey. Managers can see at any time where a log is and what processes it has been through from treatment to cutting to delivery. Previously handwritten labels would have been extremely time consuming and labour intensive to review – using unique bar coding and pack IDs gives instant traceability and batch information when needed.
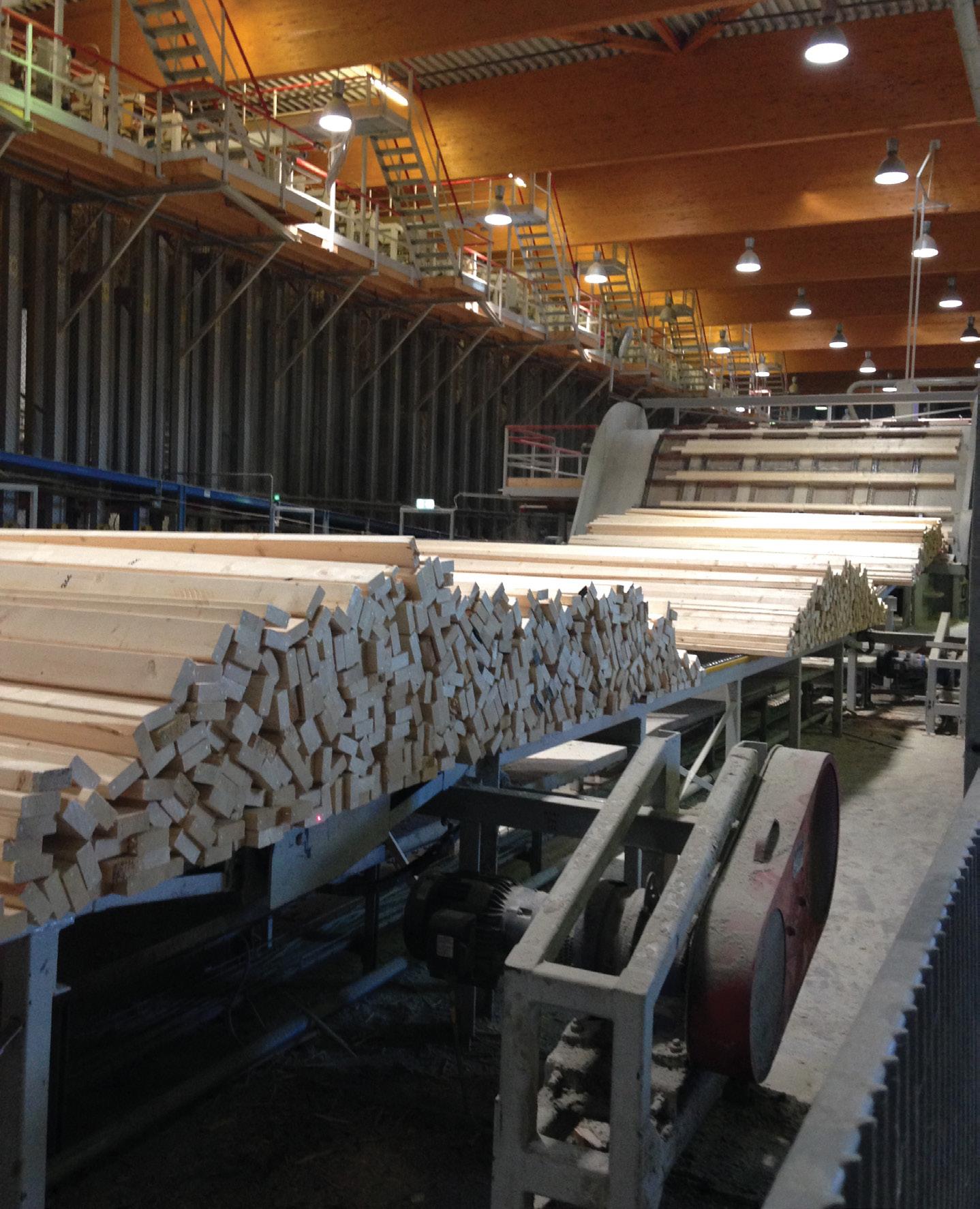
Designed for growth
Not all ERP systems are equal. For example, Turnkey Timber has been designed specifically for sawmills, harvesting and timber sales. It encompasses all the financial and administrative functionality a business needs as well as specific operational and timber functionality. No one size fits all. Often companies compromise on software functionality and still need to use multiple solutions to fit their processes. Turnkey offers a suite of extensions that can be built onto a base system and they can build tailored Apps to ensure users get the complete system needed to run a business effectively.
The underlying platform for Turnkey Timber is built on Microsoft Dynamics 365 Business Central – efficiency is built in as standard. The base configuration includes a chart of accounts and standard posting groups that make the process of assigning default general ledger posting accounts to customers, vendors, and items more efficient. The key benefits 365 Business Central offers include:
• Cloud Access – retrieve your data from any device, securely in the cloud • Speed – from clever shortcuts to responsive pages, 365BC is lightning fast • Microsoft 365 – seamless integration with other 365 products like Outlook and Excel • Scalable – 365BC is fully customisable and can grow with your business at any time
Efficient Processes
“We went live with Turnkey’s operations module in May of this year,” says Pat Twomey, chief financial officer, GP Wood.
“Due to COVID restrictions Turnkey had to manage this process remotely. All of the Turnkey team pulled out all the stops to get the ‘go live’ over the line. Users are very pleased with the system as it is user friendly, errors are significantly reduced, and the time involved in dispatching trucks has been reduced by half due to the introduction of handheld scanners. We are live for three months across two sites and the system uptime is 99%, which is well above our expectations.” • All-in-one software – view all your financials and operational data in one solution • On-premises or Cloud installation • Encrypted data back-up via Microsoft Azure • Integrates with Windows, Office 365,
Power BI, and PowerApps.
Ultimately finance teams get complete financial management including general ledger, workflows and audit trails, bank management, budgets, deferrals, bank reconciliation, dimensions, fixed assets, and currencies. Operations teams can achieve operational efficiencies through the use of automation to streamline business processes. Inventory or logistics managers, get information on inventory turnover, analysis of inventory movement, and much more. Turnkey Timber can help you with digital transformation and make your timber business more efficient across your processes, streamline your financial workflows, and remove siloed systems.