
5 minute read
ASTM Program, National Center at Auburn University Mark Milestones in Additive Manufacturing Technology
(Editor’s note: TITANIUM TODAY has dedicated significant editorial coverage on the topic of additive manufacturing (AM) technology for the titanium industry. As a complement to the feature article by Bill Bihlman, the following story provides excerpts of two articles that ran in 2021.)
The ASTM Global Additive Manufacturing (AM) Program has emerged as a well connected “Center of Excellence” to accelerate standardization and therefore industrialization of the AM technologies, a strategic field of interest for the titanium industry. Established in 2018 as a partnership between ASTM and founding partners (NASA, Auburn University, the Manufacturing Technology Center of England, and Edison Welding Institute [EWI]), the mission for this effort is to accelerate standardization of AM and provide critical education and workforce development offerings to support the adoption of the technology.
The partnership roster has grown to include the National Institute for Aviation Research at Wichita State University, Kansas, and the National Additive Manufacturing Innovation Cluster in Singapore. In addition, the AM Center of Excellence (AM CoE: www.amcoe.org) supports the ASTM F42 Additive Manufacturing Committee, which has over 1,000 members, in addition to other Standards Committees interested in AM. ASTM technical committees can utilize the AM CoE tools and resources to expedite their standard development.
Dr. Martin White, head of AM CoE Programs for Europe, said ASTM and its partners launched the AM CoE “to accelerate the closing of gaps in standards for additive manufacturing, and to provide critical training and workforce development offerings to facilitate the broad adoption of this technology in multiple industries. The ‘normal’ pace of development of standards does not keep up with the rapidly progressing world of AM, and we cannot wait for standards to be ‘reactive’ to information and data from industry.”
One of the key missions of the AM CoE is to identify gaps in AM standards, and then to fund targeted research and development projects “to close the gaps and accelerate standards,” Martin said. “The Center of Excellence ensures involvement of all 30,000-plus ASTM members as well as AM related technical committees in this process, by engaging them in the idea solicitation process for research and development projects. The same applies to already existing AM standards, as they must be regularly reviewed to ensure they are relevant and suitable for new technologies. Collaboration and shared funding have been utilized from other government agencies such NASA and America Makes.”
While its mission spans a variety of industrial materials systems (metals, polymers, ceramics), the AM CoE covers metallic systems such as titanium alloys and Inconel (a family of nickel/chrome superalloys) in its development projects. The center pursues “collaboration and coordination between government, academia, and industry to advance AM standardization and expand ASTM and our stakeholders’ capabilities,” according to Martin. “We bridge standards development with research and development.”
The trek towards the goal of arriving at a much-anticipated “inflection point” for AM technology has reached a major milestone, given the research, training and partnerships coalescing at the National Center for Additive Manufacturing Excellence (NCAME) at Auburn University, Auburn, AL.

Shamsaei Nima with lab technicians at NCAME
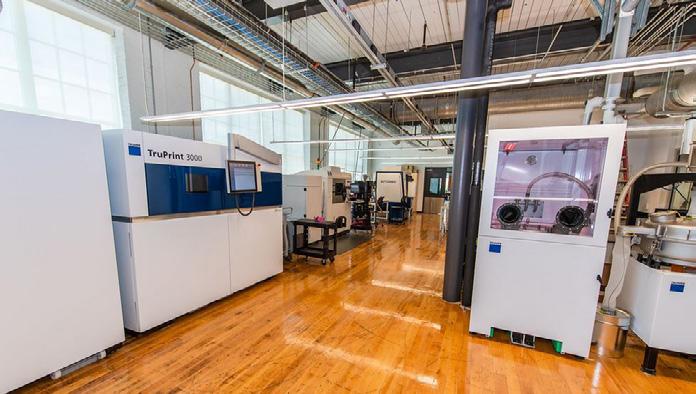
Auburn’s Gavin Engineering Research Laboratory
The center operates as additive manufacturing center of excellence, a collaborative effort among Auburn University, NASA, National Institute of Standards and Technology (NIST), and ASTM International, according to information posted on the group’s website (https://eng.auburn.edu/ncame). In addition to conducting research to advance the technology, NCAME’s mission is to facilitate effective collaborations among industry, government, academia, non-profit organizations, and ASTM committees, ensuring a coordinated, global effort toward rapidly closing standards and workforce development gaps in additive manufacturing. Nima Shamsaei, the founding director of NCAME and professor of mechanical engineering in the Samuel Ginn College of Engineering, said the program initially began to take shape in 2015 when Auburn established a partnership with the NIST, which is part of the U.S. Department of Commerce. In the fall of 2017, NCAME became NASA’s strategic academic partner and together they became the founding partners of the ASTM Additive Manufacturing Center of Excellence (see above). NCAME has benefited from strategic capital investments in recent years, which, collectively, have helped to transform the group into a hub for leading-edge technology. The list of investments and grants include a $18-million renovation of Auburn’s Gavin Engineering Research Laboratory; support from Auburn’s Presidential Awards for Interdisciplinary Research grant to explore additive manufacturing for medical implants; $7-million in grants from the NIST; a $4.5-million grant for the FAA; a $10-million award from NASA; and a $250,000 Concept Laser MLAB 100R metal printer from GE Aviation. Developing AM systems to produce parts for biomedical and aerospace industries are high on the list of priorities for NCAME. Shamsaei said the group focuses on powder metal and laser systems. Commercially pure titanium (for medical implants), along with Ti-6Al-4V, nickel-based superalloys, and aluminum alloys (for aerospace) are the materials being explored. “I envision the NCAME as a center to serve as a platform for transferring fundamental research to the applied knowledge allied with the needs of industry,” Shamsaei said. “We are working with our partners to develop commercial applications.” He stated that NCAME is working to meet the commercial production inflection point to establish three areas of additive manufacturing: design, processing, and material behavior. “Additive manufacturing is a challenging field. It’s unlike conventional production methods. You can’t separate those three areas. If you change the part geometry, it affects the microstructure and mechanical properties.”