
9 minute read
High-Purity Vanadium Remains a Critical Material for Defense Applications, Economic Development
By Terry Perles, US Vanadium LLC
Titanium alloys are alloys that contain a mixture of titanium and other chemical elements, such as vanadium. These alloys have very high tensile strength and toughness (even at extreme temperatures). They are light in weight, have extraordinary corrosion resistance and the ability to withstand extreme temperatures. The high cost of both raw materials and processing limit their use to military applications, aircraft, spacecraft, industrial applications, bicycles, medical devices, jewelry, highly stressed components such as connecting rods on expensive sports cars and some premium sports equipment and consumer electronics.
The addition of vanadium to titanium alloys improves the strength of titanium alloys and promotes thermal stability. Several important commercial titanium alloys contain between 2.5 and 15 percent vanadium. Although “commercially pure” titanium has acceptable mechanical properties and has been used for orthopedic and dental implants, for most applications titanium is alloyed with small amounts of aluminum and vanadium, typically 6 percent and 4 percent respectively, by weight. (The most familiar example of this is the aerospace workhouse alloy Ti6Al4V.) This mixture has a solid solubility that varies dramatically with temperature, allowing it to undergo precipitation strengthening. This heat treatment process is carried out after the alloy has been worked into its final shape but before it is put to use, allowing much easier fabrication of a high-strength product.
The alloying of titanium alloys involves the melting of commercial pure titanium (typically referred to as titanium sponge) with master alloys containing the alloying elements. Typically vanadium bearing titanium alloys also contain aluminum. Vanadium/aluminum master alloys containing 50-80 percent vanadium are typically used to produce a variety of titanium alloys. The master alloy is typically crushed to ¼ inch by 65 mesh and blended with titanium sponge to form a consumable electrode which is melted in a variety of vacuum furnaces, depending upon the product and grade being produced. Vanadium aluminum master alloys have similar melting point and density as titanium sponge allowing for the production of homogenous titanium alloy ingots, plates and other physical forms.
Given the critical nature of the applications of titanium alloys, the quality of the vanadium used in this application is critical. The titanium alloys must contain very low residual impurities and must be free of any high or low density inclusions to avoid catastrophic failure. Strict quality controls including ISO-9001 and AS9100 certifications are required for producers of vanadium to supply the titanium alloy industry.

Vanadium
Roughly 90 percent of the vanadium produced globally is used in the production of high strength steels. In this application vanadium is a pure commodity—a typical addition rate is 0.05 percent vanadium in these steels. At this addition level any impurities present in the vanadium are not important to performance of the steel. As a result, 90 percent of the global vanadium supply base is set up to produce commodity grade vanadium at the lowest possible cost. This commodity grade vanadium is not suitable for titanium alloys and the titanium alloy industry relies on a relatively small number of producers of high purity vanadium to supply their needs.
The production of vanadium master alloys utilizes vanadium oxides V2O5 and V2O3 as well as pure aluminum in powder and or granular form. A blend of vanadium oxides and aluminum are melted in an aluminothermic reduction process to generate an ingot of vanadium aluminum master alloy. The ingot is shot blasted and crushed in a controlled environment to limit any possibility of contamination. The crushed alloys is 100-percent inspected by visual light for any foreign material, black light inspected to assure no contamination with slag, and X-ray inspected to ensure no contamination from high density refractory materials. The final product is packaged into drums with identifiable seals on each drum. The chain of custody of the final product is critical to ensure no contamination during storage or transport.
According to VANITEC (www.vanitec.org) global vanadium production and consumption have shown high rates of growth in recent years. From 2016 to 2021 consumption of vanadium globally grew from 71,700 metric tons pure vanadium (MTV) to 120,375 MTV for a compound annual growth rate (CAGR) of 10.2percent. Vanadium production over this period has grown from 76,530 MTV in 2016 to 115,667 MTV in 2021 for a CAGR of 8.6 percent.
Pre COVID-19 titanium alloy production consumed approximately 4 percent of the vanadium produced each year. During COVID-19 production of titanium alloys was drastically affected and in recent months production of titanium alloys as started to recover and we expect that by 2023 titanium alloy production will return to preCOVID-19 levels.
Today there are three major sources of vanadium production. Approximately 68 percent of the vanadium produced each year is recovered from vanadium slag generated at steel mills in the Ural regions of Russia and in Sichuan and Hebei provinces in China. These steel mills process local vanadium bearing magnetite in the production of steel and generate a vanadium slag coproduct.
Approximately 19 percent of global vanadium production is from primary vanadium mines. There are three primary vanadium mines in operation today: the Largo Maracas mine in Brazil; the Glencore Rhovan mine in South Africa; and the Bushveld Vametco mine in South Africa. These producers mine a vanadium bearing magnetite similar to the ore used in the steel mills that generate a vanadium slag, but in these cases, they do not monetize the iron in these ores.
The final 13 percent of global vanadium production is based on recovery of vanadium from residues, ashes, spent catalysts and other waste materials that are a result of burning or refining vanadium bearing oil. Companies including US Vanadium take these industrial wastes and extract valuable vanadium from the materials and repurpose the residual solid materials into concrete and asphalt.
The production process for vanadium is to bring the vanadium into an aqueous solution either via a caustic or acid based leaching circuit. The typical vanadium plant
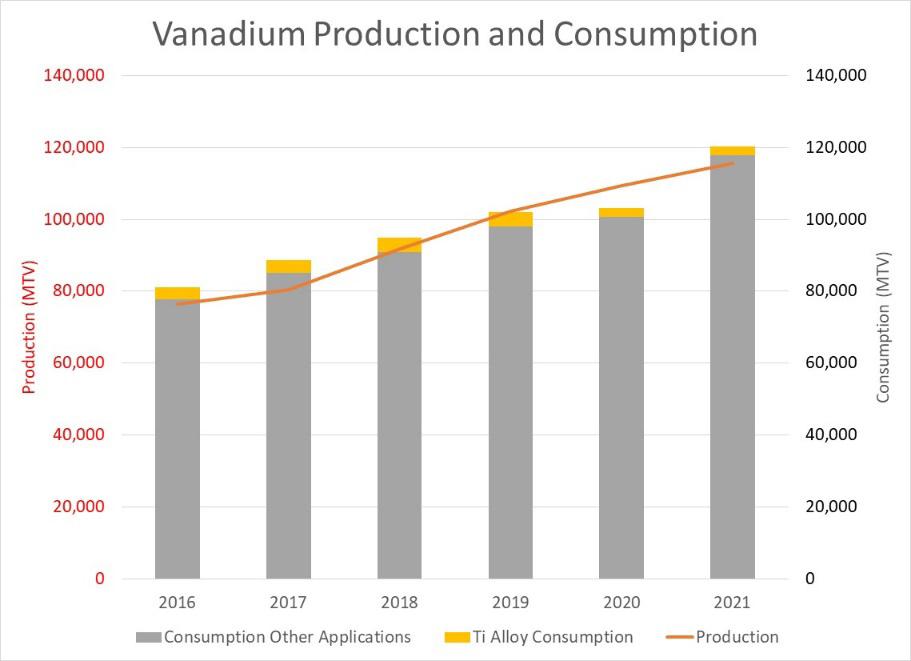
Figure 1: Global Vanadium Production and Consumption
producing commodity grade vanadium will precipitate the vanadium from the pregnant solution as a salt and then typically calcine the salt to an oxide (V2O5 or V2O3). Producers of high purity vanadium like US Vanadium LLC utilize additional technology including ion exchange/solvent extraction and multi-stage growth type crystallization circuits to eliminate any impurities from precipitating in the vanadium oxides.
Today vanadium is being utilized in vanadium redox flow battery (VRFB) systems used for grid level stationary storage applications. Massive growth in the demand for grid level energy storage is being seen around the world today and the VRFB is one of the technologies uniquely suited for this application. VRFB systems offer essentially unlimited life with no degradation of capacity over time, and no danger from fires. Demand for vanadium from these sources is expected to grow significantly in the coming years.
Growth in vanadium supply over the past five years has been relatively high and this trend will have to continue in order for the new demand envisioned from energy storage systems to occur. Our projection shows growth in supply that will come from a combination of existing and new production facilities.
Industry expectations anticipate a fairly balanced but quickly growing vanadium market in the next several years. Global Vanadium identified reserves are sufficient to supply current global vanadium demand for the next 125 years. Vanadium is more abundant in the earth crust than many other critical elements including lithium, cobalt, copper, and nickel. The future availability and price of vanadium will be dependent upon how fast the supply base can expand in the face of surging demand.
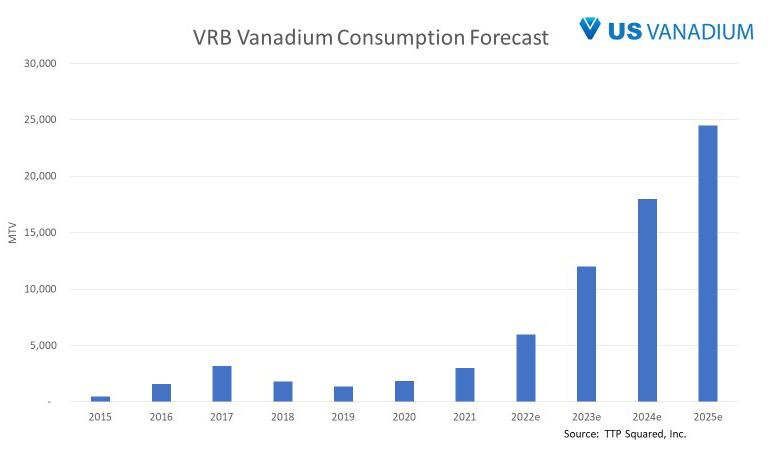
Figure 2: Vanadium demand in VRFB Applications

Figure 3: Sources of Increased Vanadium Supply 2020-2025

Figure 4: Global Vanadium Production and Consumption Projection
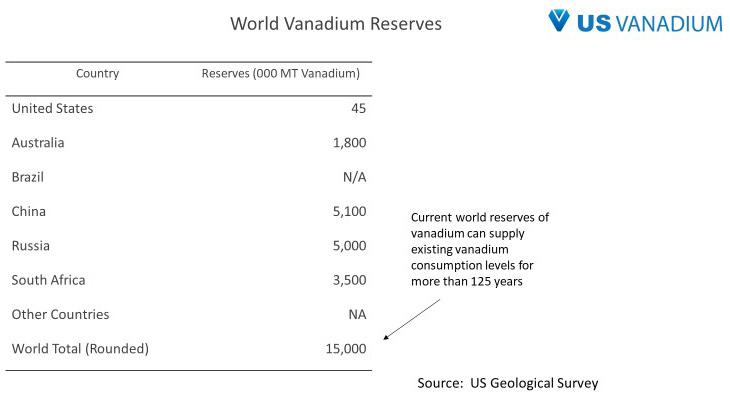
Figure 5: Availability of Vanadium
Vanadium has been classified as a critical mineral by the European Union, the United States and other jurisdictions. High-purity vanadium is critical for various national defense applications including jet engines, airframes, ballistic missiles, and as a coating for night vision goggles. Vanadium is critical in the production of many basic chemicals and petrochemicals and as a pollution control catalyst. Vanadium consumption in these critical applications will continue to grow in the coming years and the supply of high-purity vanadium for these applications will continue to be important from a defense and economic development standpoint.
(Editor’s note: Terry Perles has 33 years of experience in the vanadium industry in roles including sales, marketing, strategic planning and senior management. Perles joined US Steel Corporation in 1980 as a Construction Management Engineer and held assignments at the company’s steel mills in Homestead and Clairton, PA. In 1988, Perles joined vanadium producer Stratcor and during his 20-year tenure held positions in sales, marketing and senior management. In 1998, he was appointed vice president of sales and marketing and charged with the responsibility to manage global vanadium sales to the steel, titanium and chemical industries.)
In March 2010, Perles established TTP Squared Inc., a metals industry consulting firm serving both producers and consumers of vanadium chemicals and alloys. In December 2010, Perles established MoTiV Metals, LLC, a Pennsylvania corporation acting as a North America sales agent for metal producers supplying vanadium, molybdenum and titanium alloys and chemicals to steel, titanium alloy and chemical industries. In May 2012 Perles joined the senior management team of Atlantic Ltd., owners and operators of the Windimurra vanadium project in Western Australia. In 2019 Perles and a group of investors formed US Vanadium LLC for the purpose of acquiring Evraz Stratcor Inc. and the vanadium production facility in Hot Springs Arkansas. US Vanadium now operates the facility in Hot Springs producing high-purity vanadium oxides and downstream chemicals. Perles is a non-executive board member at US Vanadium. He has been an active member of the Vanadium International Technical Committee (VANITEC) from since 2004 and served as chairman of the VANITEC Market Development Committee from 2012-2014.)