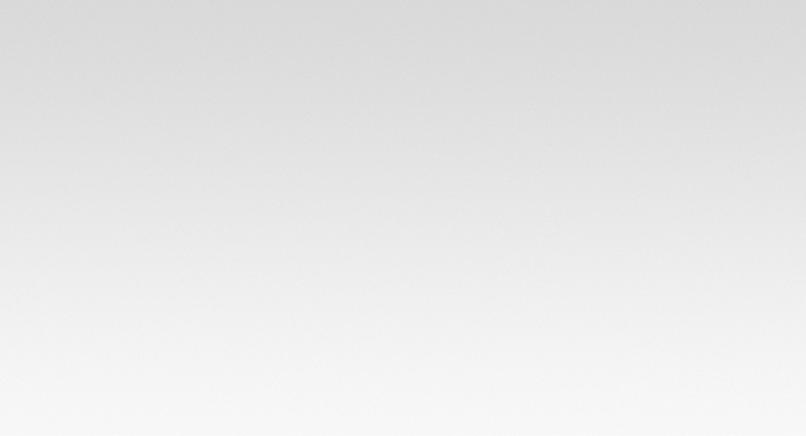
5 minute read
Anticipating Commercial Production, Coogee Reports MeltFree Titanium Powder Operations Proven at Scale
from Titanium Today: Promoting and supporting the use of titanium metal in new and existing applications.
By Michael C. Gabriele
Despite the global coronavirus pandemic throughout 2020, Coogee Titanium has continued with its substantial investment in the MeltFree titanium alloy powder production facility located outside Perth, Australia. “The pandemic slowed but did not stop Coogee Titanium’s progress,” Art Kracke, the president of AAK Consulting LLC, said, regarding Coogee’s strides towards commercial production. “Creative approaches and tenacity allowed work to proceed achieving significant progress toward full production of in-spec, high-quality, low-cost Ti 6-4 Grade 5 and 23 powders.”
Kracke, based in Charlotte, NC, has been an executive in the titanium industry for nearly four decades and serves as a consultant to Coogee. “Vision, commitment, and tenacity are required to stay the course while others are battening down the hatches to weather the pandemic storm. This is exactly what Coogee Chemicals, the parent company of Coogee Titanium, has in its dedication to bringing their patented game-changing technology into the production of commercially pure (CP) titanium as well as titanium alloy powder.”
As reported here last year, Coogee Titanium Pty Ltd. is completing construction of its integrated MeltFree continuous titanium powder production facility outside Perth, Australia. The 200-metric ton fluidized bed reactor was commissioned in 2019 and in recent months the Gen4 CVDU (Continuous Vacuum Distillation Unit) was brought online successfully. In addition, Coogee Titanium has built, commissioned and is producing ultra-low oxygen magnesium (Mg) powder at a UK facility. This plant has a capacity in excess of 400 metric-tons per annum.
Ultra-low oxygen Mg powder is a critical feedstock to the MeltFree process as it is used to reduce TiCl4, AlCl3, and VCl4 in a continuous Kroll-like reaction. Coogee’s Technology Director, Dr. Peter Duxson, believes that “all major unit operations for Coogee Titanium’s MeltFree process have now been proven at scale and routine powder production from the facility in the year ahead will demonstrate our ability to achieve consistent quality finished product, with an oxygen level <1000 ppm.” This is a genuinely transformative technology and the engagement with industry over the upcoming period will establish the credentials of the MeltFree powder process.
Commercial production at the Perth-based facility of Ti6Al-4V and 6Al-4V ELI (extra-low interstitials) powder will be geared for industrial applications include powder bed, DED (direct energy deposition), and cold spray additive manufacturing technologies, MIM (metal injection molding), HIP (hot isostatic pressing), and CIP (cold isostatic pressing). Duxson explained that “in addition to powder production for additive manufacturing, the MeltFree process offers the industry a new flowsheet enabling continuous production of titanium in a fullyenclosed controlled production environment—the operational and product quality benefits compared to the conventional Kroll sponge process are potentially significant.”
Bringing low-cost MeltFree titanium powder to production requires multiple innovations, Kracke explained. The first was scaling up, controlling the reaction, and commissioning a 200T fluidized bed reactor (FBR). “The FBR transforms liquid metal chlorides into an intermediate stage solid alloy particle. The second innovation was the design and construction of a 50ton continuous vacuum distillation unit (CVDU), which has been commissioned.”
Continuous processing has eluded titanium sponge production for decades. Coogee Titanium’s process, from a high level, is similar to the Kroll sponge making process, but produces individual powder particles instead of multi-ton unalloyed sponge cakes. “Titanium alloy powder’s time has come,” Kracke said.
Kracke acknowledged that metal producers know that what can be done in the lab or pilot facilities may not be achievable on a production scale. However, Coogee has confronted these challenges,
according to Kracke. “Coogee’s core chemical engineering skills and scale-up discipline became the discerning factors which overcame the challenges.”
He offered an example: “Titanium easily and rapidly absorbs oxygen on its surface. The greater the surface area the more oxygen is absorbed. Powder particles have an extremely high surface area to volume ratio. For passivated powder to meet or exceed customer oxygen requirements requires making unpassivated powder with exceptionally low oxygen content. To achieve low oxygen unpassivated powder, ultra-low oxygen magnesium is required. Low oxygen magnesium powder could be purchased for smaller quantity runs but could not be bought in the large quantities needed for producing tons of titanium powder on a monthly basis.”
“What did Coogee do? They contracted to build a magnesium atomizer and worked collaboratively to design an atomizer to make ultra-low oxygen magnesium powder,” he continued. “The benefits of this investment include ownership of a critical part of the process, supply chain security, and control of quality and cost of their magnesium powder. High quality and low cost are essential to accomplishing production goals.”
Kracke outlined the next steps in Coogee’s MeltFree titanium operations. “The focus is on quality and cost reduction at every stage of the process,” noting one example of the recent addition of Argon recycling at the facility. Duxson believes “work completed to achieve tight control of high-yielding particle size coupled with unique process design can transform the cost from powder to additive manufacturing.” The facility in Perth is now well down the path of being fully integrated from starting chemicals to finished and packed titanium alloy powder. In the year ahead, a particle spheroidizer will be installed at the facility. This follows a substantial work program to identify and validate the best technology to transform irregularshaped powder to a spherical form suited to additive manufacturing machines.
Commercial development has also progressed, he pointed out. Of particular note are customer engagement programs to initiate applications for non-spherical powder. “The specifics are covered by non-disclosure agreements, but what can be said is the potential volumes are significant and will consume major chunks of Kwinana’s capacity.”
Kracke said the cumulative impact of these achievements is expected to deliver cost-effective, highquality, production-scale titanium powder with less than 1000 ppm of oxygen. “This will provide powder consumers in the aerospace, biomedical, motorsport, and recreation industries justification for growth. Developers of new high-volume, highly efficient advanced manufacturing applications, such as in the automotive industry, will have dramatically improved business cases which promise to break down barriers to entry and help drive growth of titanium powders.”
Coogee Chemicals Pty Ltd (headquartered in Perth) is the majority shareholder of Coogee Titanium Pty Ltd. CSIRO, the Commonwealth Scientific and Industrial Research Organization, an Australian government agency is a minority shareholder. All MeltFree technology patents are owned by Coogee Titanium.
According to a forecast published in the 2019 Wohlers Report, additive manufacturing is projected to be a $35-billion global industry by 2024. (That estimate may need to be revised due to the disruptions cause by Covid-19.) Wohlers Associates Inc. (https:// wohlersassociates.com) an independent consulting firm based Fort Collins, CO, publishes Wohlers Report, which provides a worldwide review and analysis of additive manufacturing and 3D printing business sectors. n
(Editor’s note: Art Kracke, the president of AAK Consulting LLC, provided a substantial amount of information for this article.)