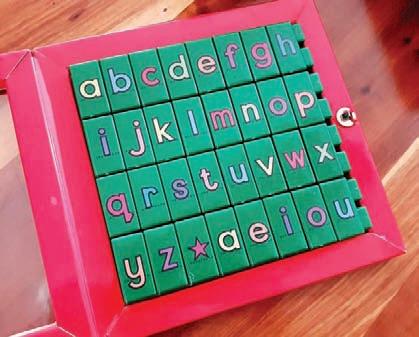
16 minute read
Educational blocks made by AfriEco from collected waste
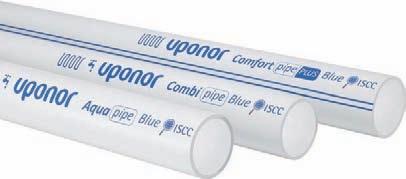
These eco-educational building block systems from AfriEco facilitate literacy and numeracy in our youth
Advertisement
AFRIECO of Durban, is busy turning clean-up work into marketable products. It is using items such as collected post-consumer bottle caps in the production of one of its latest products, eco-educational building blocks.
According to Jonathan Welch of AfriEco, much of its work is co-ordinated with Green Corridors, a Durban-based organisation involved in community activities, including tourism, eco activities and clean-ups, in which area it also cooperates in river and beach clean-ups organised by Plastics SA. AfriEco, in collaboration with Green Corridors (through its
KwaMashu Materials Benefi ciation Centre,) has set up a number of value chains for various waste materials.
“An example of such a value chain is one where Green Corridors buys in bottle caps, sorts them by colour, type and cleanliness and
World’s fi rst cross-linked polyethylene pipes based on renewable feedstock
Drop-in solution reduces carbon footprint by up to 90% vs comparable pipes made from fossil-based virgin PE-X
BOREALIS has been collaborating with pipe specialist Uponor to enhance the sustainability of crosslinked polyethylene (PE-X) pipes. The resulting PEX Pipe Blue is the world’s fi rst pipe portfolio made from PEX with accredited renewable feedstock.
Based on Borealis’ Bornewables™ polyethylene (PE) derived from second-generation natural resources, such as waste from pulp production or residues from food processing oils, the new PEX Pipe Blue products boast an unprecedented carbon footprint reduction of up to 90% when compared to conventional fossilbased PE-X pipes.
The signifi cantly lower carbon footprint of PEX Pipe Blue compared to traditional fossil-based PE-X pipes is based on Environmental Product Declaration (EPD) calculations according to EN15804+A1 and CML/ ISO21930 standards. EPD evaluates the environmental impact of products by means of life cycle assessment (LCA). All the data is verifi ed by an independent third party.
This means that for every ton of certifi ed Bornewables PE-X used in production, an equivalent amount of PEX Pipe Blue can be claimed as certifi ed renewable, without compromising on quality or effi ciency.
Uponor PEX Pipe Blue – the world’s fi rst pipe portfolio manufactured by Uponor from sustainable cross-linked polyethylene with ISCC PLUS certifi ed Bornewables PE polymer from Borealis
New recyclable bag for Woolies chicken
Makes good on 2018 ‘green’ promise
WOOLWORTHS has confi rmed that with the recent opening of a new PET wash plant in Cape Town an additional 1 000 of the retailer’s food packaging items can now be recycled in South Africa. Another packaging improvement is the current rollout of a recyclable polypropylene bag for its ever-popular rotisserie chicken, which means that on an annual basis over 11.5 million bags will not go to landfi ll and can be recycled.
The new rotisserie chicken bag is made from 60 micron cast polypropylene and will be rolled out to Woolworths stores across the country, as the old packaging supply is depleted.
“Zibo Container’s recent investments in PET wash and decontamination plants is a huge boost for recycling in South Africa. These new plants will reduce packaging waste to landfi ll, improve circularity of our resources which is critical for the planet’s survival as well as create much needed jobs,” says Latiefa Behardien, Woolworths Foods chief technology and sustainability offi cer.
“It is particularly exciting for us as it means that an additional 1 000
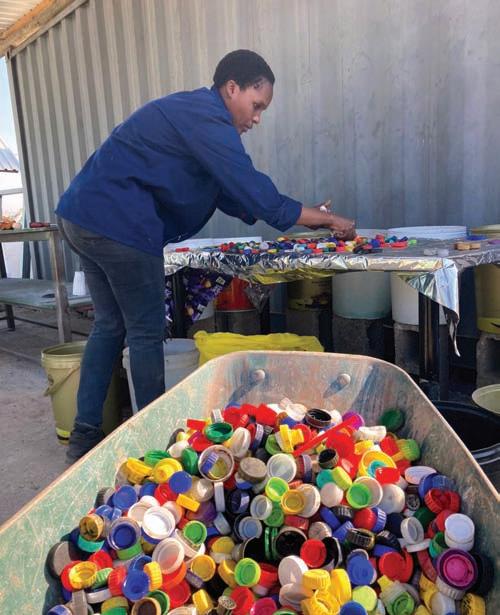
then washes and granulates them into different grades of recyclate material for the production of new products,” explains Welch. (AfriEco buys the highest grade of product for its ecoeducational building blocks whilst its lower grades are used to colour green concrete paving stones.)
Some teething problems were encountered with the fi rst version of the system, launched in 2020, but Welch and his team have honed the design, had moulds made by a Durban convertor and production for market testing is now underway.
“We see the sale of eco-educational building blocks to educational suppliers and toy stores as a vehicle to not only improve literacy and numeracy in South Africa, but also to drive up viability of the collection, sorting and processing of materials often discarded into the environment,” Welch adds.

Woolworths’ semi rigid PET thermoform foods packaging items can now be recycled. And this recycled material is then reused into the same semi rigid PET thermoform packaging, so it is circularity at its best,” she says.
“As part of our vision to have ZERO packaging waste to landfi ll, we are designing our packaging for circularity. This means that we are designing our packaging to keep it out of landfi ll and that it can rather be reused in a continuous process within the packaging supply chain.
“An example of which is our recent switch to an ‘easy wash off’ glue like Cleanfl ake which ensures that the glue from the packaging’s label washes off entirely in the recycling washing process leaving no leftover residue to compromise the recycled plastic. This results in the entire piece of packaging being recycled versus just the parts with no residual glue,” adds Behardien.
Avery Dennison’s CleanFlake™ adhesive technology is specially engineered to support the recycling of PET and HDPE packaging, making sustainability an easy choice. During PET recycling, the adhesive deactivates to allow both label and adhesive to separate cleanly, leaving the plastic free of contamination. During coloured HDPE recycling, the label stays attached, but does not compromise the resulting plastic pellets.
“In the fl exible packaging space our goal is to eliminate all multi-polymer structures, moving them from previous nonrecyclable laminates and co-extrusions to mono polymer laminates and co-extrusions. We’ve already shifted more than 300 tons of multi-layered multi-polymer structures to mono polymer materials which can be recycled primarily in the PE and PP streams One such success is our coffee bags which shifted from traditional coffee laminate of PET/ALU/PE to an all-PP structure,” comments Diane Peterson, Woolworths sustainability communications consultant.
In November 2010, Woolworths was the fi rst retailer to introduce recycled content into its packaging, and now the packaging of over 2 000 of its foods products have between 30-70% recycled content with some packaging like the WLab Breathease 2-in-1 laundry liquid made from 100% postconsumer recycled HDPE.
“While recycling alone cannot solve the world’s pollution problems, it has signifi cant potential to impact on cleaning up our waste systems, creating jobs and reducing the use of virgin plastics. Every step of the way helps to bring about a cleaner country for all,” concludes Behardien.

jonathan@afrieco.co.za
www.durbangreencorridor.co.za
AfriEco set up a materials benefi ciation centre in KwaMashu in Durban to process non-recyclable and organic waste streams… as well as to recover items which can be reused, such as the post-consumer bottle caps being sorted here by Nokuthula (who also operates the hammermill)
New recyclable bag for Woolies chicken
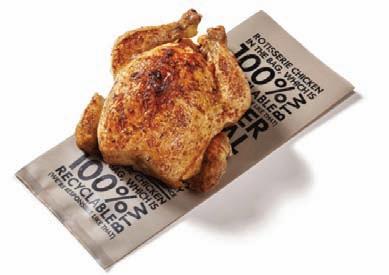
‘ Ocean Action’ from UPM Raflatac uses SABIC’s certified circular polyolefins
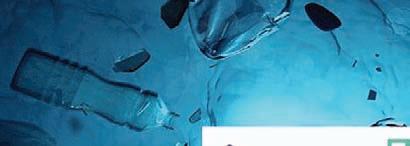
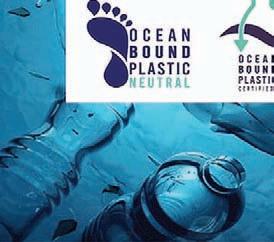
Reprocesses recovered ocean-bound plastic that could end up in rivers and oceans
SABIC, a global leader in the chemical industry, has joined an innovative project with value chain partners to help UPM Raflatac launch the world’s first packaging label materials made from SABIC certified circular polypropylene based on advanced recycled oceanbound plastic (OBP). The label materials are marketed under the UPM Raflatac Ocean Action™ brand of labels.
“We are proud to offer our customers another more sustainable choice through the advanced recycling of used plastic that could otherwise end up in our rivers and oceans,” adds Lada Kurelec, GM for the polyolefins and elastomers businesses for petrochemicals at SABIC.
Ocean-bound plastic is abandoned plastic waste found in areas up to 50kms inland from waterways that may eventually be washed into the ocean by rainfall, rivers or tides, according to the groups’ protocols. Zero Plastic Oceans, a non-governmental organisation dedicated to addressing plastic pollution issues, has estimated that OBP from uncontrolled waste disposal accounts for 80% of marine plastic litter. ”The new innovative Ocean Action label material is the latest step in our beyond fossils journey. It does not only help prevent the plastic waste from ending up in the oceans but also offers brand owners the possibility to meet their recycled content targets for packaging. The Ocean Action label material is an easy-to-use drop-in solution created especially for food and cosmetics end-uses as it has exactly the same performance as the current fossilbased labels,” says Eliisa Laurikainen, business development manager from UPM Raflatac.
AMERICAN company, Avient Corporation has introduced its breakthrough PCR Colour Prediction Service for polyolefins and polyethylene terephthalate (PET) resins, and the company’s new polyolefin antioxidants, Cesa™ Nox A4R additives for recycling. These sustainability solutions are specifically designed to improve the customer experience of working with post-consumer recycled (PCR) content for materials used in packaging.
The PCR Colour Prediction Service, helps brand owners understand what colours are achievable based on the amount of PCR used. It uses sophisticated technology to determine – through prior colour matching – if colours are feasible in a new application that incorporates PCR content. A first of its kind for the plastics industry, this internally developed solution also calculates how much PCR content can be added to an existing application without affecting its signature colour.
Using proprietary software, Avient experts measure resin characteristics to identify the gamut of colours that can be successfully reproduced in a specific PCR-based material. By speeding up the evaluation process, the service also gives greater flexibility to customers that may need to switch from one PCR content source to another.
Avient’s new Cesa Nox A4R Additives for Recycling are based on a special
The new labels – marketed under the UPM Raflatac Ocean Action™ brand – are believed to be the world’s first packaging label materials made from certified circular PP produced from recycled ocean-bound plastic from SABIC
The OBP used in the project is recovered by local partners of HHI, a Malaysia-based recycling company. The sustainable sourcing, proper collection and management of the OBP is certified by Zero Plastic Oceans and Control Union. HHI converts OBP into a pyrolysis oil by using advanced recycling, and SABIC uses this oil as an alternative feedstock to produce certified circular SABIC PP polymer for further processing to film by Taghleef, a manufacturer of BOPP films for labelling and packaging. Then, UPM Raflatac produces the label material.
The plastic waste used in the process value chain of making Ocean Action label material is certified under the Zero Plastics Oceans programme, and the final label material under ISCC Plus. This means that the material flow is controlled and tracked from the oceanbound plastic to the final packaging following a set of predefined and transparent rules. The Ocean Action label material is available as white and clear top coated PP films with RP37,
The Ocean RF37, and RP74 adhesives Action label material has exactly the same and PET 23 PCR and glassine liners. These label materials are a perfect fit for fastperformance as the moving consumer current fossil- goods (FMCG), such based labels as household goods, personal care, packaged foods, and beverages. Since the certified circular PP from SABIC performs the same way as comparable fossil-based virgin PP, the switch to the OBP material solution required no changes to the film and label material manufacturing processes.
www.sabic.com
Vision for the future: Trucircle™ from SABIC
OUTLINING its initiative aimed at developing a circular economy solution for plastics, material manufacturer SABIC summarised its Trucircle™ programme as follows:
“Society is currently facing some of the biggest challenges and we must work together to solve them. SABIC’s vision for the future is that plastic should never end up in the environment, landfill or in our oceans and instead is reused and remade into new products.
“This vision requires a total transformation of the value chain. We have been working with our downstream and upstream partners to reinvent and pioneer our way towards a circular economy for the good of people and the planet. Our Trucircle portfolio and services play a significant part in achieving our vision and closing the loop on used plastic.
“The Trucircle portfolio and services showcase our circular innovations. We want to give manufacturers access to more sustainable materials. That way, they can give the endconsumer more confidence about buying products with the knowledge that the material can be recycled and repurposed, or that it has been produced in a way that can help protect our planet’s natural resources,” its statement added.
The Trucircle portfolio and services currently include: • Design for recyclability • Mechanically recycled products • Certified circular products • Certified renewable products • Closed-loop initiatives
formulation that protects post-consumer polyolefins against oxidation, which can lead to defects like black spots, gels and discolouration. The antioxidant can be added to PCR content early in the recycling process or incorporated in virgin resin to prepare it for future recycling.
www.avient.com
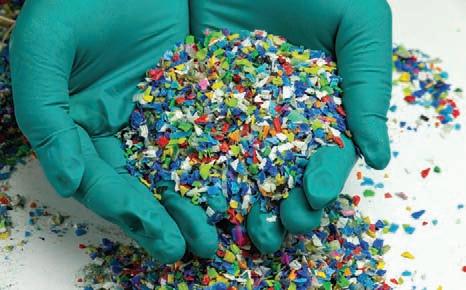
RWC Sevens building sustainability
Global rugby family contributing to a healthier planet,more sustainable society
PLASTIC waste from Rugby World Cup Sevens 2022 – which kicked off in Cape Town on 9 September – will be turned into affordable housing as one part of the tournament’s drive to deliver South Africa’s most environmentally responsible rugby event ever.
World Rugby’s Environmental Sustainability Plan 2030 – launched earlier this year – maps out what the global rugby family should do to contribute to a healthier planet and a more sustainable society.
SA Rugby ran a pilot project during a Test match earlier this year where all the plastic waste – including what was once regarded as non-recyclable material such as chip packets and polystyrene boxes – was collected and converted into pellets to go into the manufacture of bricks.
Springbok Sevens men’s and women’s players teamed to go on-site and build houses at a development outside Cape Town called Garden Cities, part of the Breaking New Ground Homes housing development plan for sustainable human settlements.
World Rugby chief executive Alan Gilpin said: “It is fantastic to see recommendations from World Rugby’s Environmental Sustainability Plan 2030 being put in to practice by South Africa’s men’s and women’s sevens players in this innovative project to help build affordable homes using plastic.
“The players actions will no doubt inspire many others to take notice and be a force for good, helping to protect the planet for future generations to continue to enjoy playing rugby in a healthy environment.”
Fulfi ls a very tangible need
THE British Plastics Federation (BPF) has published a book called Sustainability Management in Plastics Processing: Strategies, Targets, Techniques and Tools. Written by the plastic manufacturing expert Dr Robin Kent of Tangram Technology and supported by BPF Energy, the book covers all the main areas of a product’s lifecycle.
The book was written to fulfi l a very tangible need, said Dr Kent. “Despite all that is written about sustainability and plastics, there is still a lack of practical information for the plastics processor who wants to improve the sustainability of their business. This book aims to provide plastics processors with the knowledge and tools needed to improve their sustainability and to demonstrate this to the outside world. It shows that sustainability management is not ‘rocket science’, simply good management and engineering with an eye to the long-term effects of our actions,” he explained.
The book opens with a detailed introduction to sustainability management, and then goes on to explore how gains can be made by examining management systems, design, raw materials, manufacturing practices, energy use and water use. It also covers establishing a carbon footprint for both sites and products, minimising waste, the use and endof-life phases for products, social responsibility, and reporting principles and standards.
As the author explains in his preface, ‘each topic is dealt with in a single 2-page spread…and most can be read independently of each other – this is not a cover-to-cover book’.
It is intended to provide practical guidance to plastics processors, providing them with the knowledge and tools to improve their overall sustainability by showing how improvements can be made in key areas. Spanning some 434 pages, written in clear and concise language, it is an accessible and practical reference book, a ‘fundamental manual’ as BPF Director General Philip Law, described it: ‘so comprehensive in its sweep that its practical guidance will be referred to time and time again by companies in the plastics industry.’
Sustainability Management in Plastics Processing is available to buy now at Amazon.co.uk.
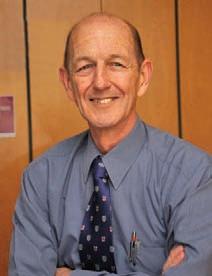
_ literally
RESIN8 incorporated into mix for concrete blocks
A special plant converts the waste into an “eco-aggregate”, called RESIN8. The manufactured RESIN8 is then incorporated into the mix design for the casting of conventional concrete blocks – disposing of 100% of the plastic waste and reducing the need for conventional quarried materials by up to 20 percent.
Each house requires 1 200 bricks per unit; the Springbok test match produced 398 bags which resulted in 875kg of plastic waste, producing 3 500 bricks (or almost three houses).
Springbok Sevens men’s and women’s players teamed to go on-site and build houses at a development outside Cape Town called Garden Cities, part of the Breaking New Ground Homes housing development plan for sustainable human settlements
The “bag that builds” initiative is just one part of the event’s sustainability drive to contribute to World Rugby’s climate action focus areas of the carbon footprint of the sport; introducing climate adaptation measures across events and using the sport’s global platform to spread awareness.
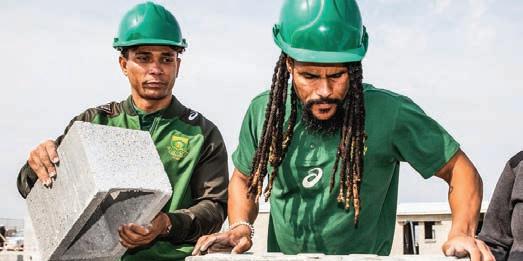
TPV with 25% recycled content
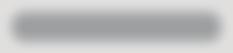
SARLINK thermoplastic vulcanizates (TPVs) are a great choice for critical applications that require superior elasticity and long-term performance, like extruded seals and hoses or moulded gaskets. Sarlink TPVs have steadily been replacing thermoset rubber, like EPDM, in sealing applications due to improvements in processing, design, and weight reduction. In addition, unlike EPDM rubber, Sarlink TPVs are recyclable, both in-process or at the end of the product’s life cycle. Teknor Apex has now introduced the latest innovation in the Sarlink portfolio, which can further help brands achieve their sustainability goals, by incorporating recycled content into TPVs.
The new grade, Sarlink R2 3180B incorporates 25% post-industrial recycled (PIR) content. This is a pre-coloured black, high-durometer multi-purpose TPV that is essentially the functional equivalent of its virgin counterpart in terms of processing and performance. Sarlink TPVs in general have faster cycle times or throughput rates versus competitive TPV products on the market, and the addition of recycled content has proven to maintain this advantage during processing trials.
Automotive, industrial and building & construction industries are ideal markets for this new Sarlink TPV, which can be overmoulded or co-extruded with PP or other thermoplastic elastomers. Not only does Sarlink R2 3180B reduce plastic waste by incorporating it into the compound, but products made from this grade are still fully recyclable at the end of the product’s life. • Teknor is represented in South Africa by Advanced Polymers (Pty) Ltd
The NEW Sarlink® R2 3180B TPV with 25% recycled content is a multi-purpose TPV containing highquality post-industrial recycled (PIR) content and processes and performs like its virgin counterpart
www.teknorapex.com
