
20 minute read
Boost for recycling as bottle labelling trial signals success
JUNE / JULY 2021 6
section 18 ePR is here...
Advertisement
Existing producers to register no later than 5 November 2021
AS A pro-active response to the growing national concern around waste and its impact on society and the environment, South Africa recently published the Section 18 Regulations to the National Environmental Management: Waste Act on 5 November 2020, which refers to the Extended Producer Responsibility (EPR) aspect of the National Environmental Management Waste Act (NEMWA). The regulations came into effect on 5 May.
This new legislation makes EPR mandatory for all producers and importers of packaging. It changes how producers, brand owners, retailers and importers design, make, sell and keep their products in the recycling loop as far as is practicably possible.
It is now compulsory for producers to belong to a Producer Recovery Organisation or to form their own independent EPR scheme if they choose not to join a PRO to demonstrate your EPR.
Any company or brand that makes or imports any form of plastic packaging for distribution is required to pay an and the Southern African Vinyls EPR fee. Strict targets have been set Association for PVC. by Government for yearly collection and recycling that need to be met over The following are required for producers: the next five years. EPR will see • Existing producers to register an investment in collection with the Department of infrastructure. Not only will EPR will Environment, Forestry this provide consumers see an investment in and Fisheries from with more convenient collection infrastructure. 5 May and no later recycling facilities, but Not only will this provide than 5 November 2021 a concerted recovery consumers with more (as per the amended effort at the pre- convenient recycling EPR regulations consumer or post- facilities, but a concerted released on industrial phase. recovery effort at the 15 January 2021).
Luckily, South pre-consumer or post- • Join or form an EPR Africa’s plastics industry industrial phase. scheme that includes is well positioned for this the entire value chain. next stage of environmental • Be accountable for the legislation. We have four voluntary, operation and performance industry-led PRO’s that have been of an EPR scheme. running for many years now and have • Pay the appropriate fees to the EPR impressive track-records of collection and scheme. Fulfil monitoring and reporting recycling successes, namely PETCO for obligations – to begin Q1 2022. PET, Polyco for polyolefins (PP, HDPE, We urge you to start the process now LDPE/LLDPE and multi-layer), the by engaging with the relevant plastics Polystyrene Association for polystyrene, industry PRO’s as soon as possible, as
Boost for recycling as bottle labelling trial signals success
A GROUND-BREAKING trial that renders plastic bottles with self-adhesive labels fully recyclable promises positive spin-offs for the environment and plastic producers who have until November to comply with Section 18 of the National Environmental Management Waste Act.
Until now, PET plastic bottles with adhesive labels have hampered South African recycling processes, because the glue from the labelling has discoloured the recyclate. This has meant that discoloured recycled PET (rPET) from those bottles could not be repurposed into high-quality, clear plastic beverage bottles, but only be used to produce a limited range of products.
Extrupet, PETCO, UPM Raflatac & Java Print partner in trial
Post-consumer PET bottle recycler Extrupet trialled the new wash-off label adhesive in April in conjunction with PETCO – the national industry organisation supporting PET plastic bottle recycling and collections. Self-adhesive label manufacturer UPM Raflatac and label printers Java Print partook in the trial with bottler Oasis Water.
“Lab results following the trial have shown a more than satisfactory result,” said Extrupet joint managing director Chandru Wadhwani, adding that the new wash-off label adhesive used in the trial easily washed off the PET flakes created as the plastic bottles underwent recycling.
“The chemical composition of the new wash-off label adhesive makes it easier to remove during recycling, and the glue retention on the label has met our recycling standards requirements,” he said.
ECO-LABELLING: Yvonne Griesel and Gerrie Swanepoel of Oasis Water take a closer look at the new eco-friendly wash-off labelling trialled on 10 000 of their bottles recently
Section 18 EPR is here... are you ready?
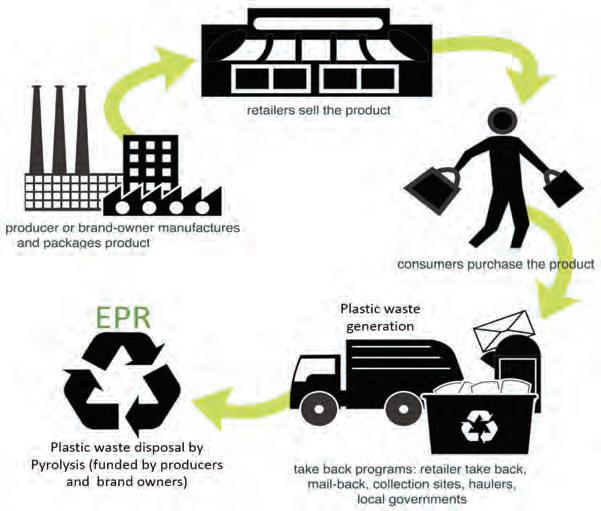
reporting against the gazetted targets starts in Jan 2022. For more information or guidance in this process, contact the relevant PROs directly via their websites: • PETCO: www.petco.co.za • Polyco: www.polyco.co.za • PVC: www.savinyls.co.za • Polystyrene: www.polystyrenesa.co.za
Wadhwani added that plastic producers would benefit from the new technology as it would help them comply with new government legislation on Extended Producer Responsibility (EPR).
“While self-adhesive labels are not the preferred choice for ideal design of a PET bottle pack – a polyolefin wrap-around label with minimal or no glue is preferred – the new wash-off adhesive label is a preferred option when a brand owner absolutely has to use a self-adhesive label,” he said. “We’re not promoting the use of selfadhesive labels, but if you have to use one, make sure it’s eco-friendly.”
Wadhwani said that as long as a label was made from polyolefin, it could be recycled.
“Once the label is separated from the bottle, it is melted together with the glue, and used to manufacture products such as outdoor furniture, pallets and school desks,” he explained.
Changed chemical composition of adhesive makes it better for recycling
UPM Raflatac packaging solutions manager, Trevor Isaacs, called the trial a milestone, saying: “We successfully changed the chemical composition of the adhesive, making it easier to wash off and remove the label during recycling, with no residual adhesive.”
“It’s been fantastic to be part of this trial. We’re really excited about taking the product to scale and hope that suppliers, manufacturers and producers get on board quickly so that sustainable labels are soon the norm,” Groves said.
10 000 bottles with new label tested
Extrupet extensively tested 10 000 Oasis Water bottles that featured the new labelling as part of the trial. “We welcome the new Section 18 requirements and happy to say we are compliant,” said Oasis Water director Naas du Preez.
Latest force majeure also beyond Safripol’s control
UNDER-PRESSURE convertors will not have been impressed by the latest force majeure declaration by Safripol which, as in the two disruptions over the recent summer, was again due to factors beyond its control. Wet ethylene received from its supplier, Sasol, resulted in the delay of the restart of its HDPE plant in Sasolburg. The line was stopped in May for routine maintenance.
Safripol advised customers around the country and region in a regular communique, and informed them it would only be able to recommission the line once in-spec ethylene was received. That was on 31 May and the expectation was that the delay would be a few days, but that was not certain.
Co-polymer and random co-polymer supply was most affected.
This comes on the back of massive interruptions in polymer supply internationally, which has seen the terms ‘allocation’ and ‘quotas’ used more than ever before. The sheer frequency of the interruptions appears to have been at least partly the result of plant problems encountered during restarts after the Covid induced slowdown.
The spotlight has been turned on the material suppliers and importers, who have regularly over the years been able to supply when the local manufacturers have not, but although the market has began to stabilize, the importers have in many cases not been able to fill the shortfalls.
Perhaps only the smartest convertors will be unaffected, but holding full material stores at plants is now more of a rarity, not least because it involves the tieing up of too much capital.
Silindokuhle Mhletywa, project manager; Ronelle BonnesseSwem, business development manager, and Nigel Bennett, operations director, at the new Ebor East London plant
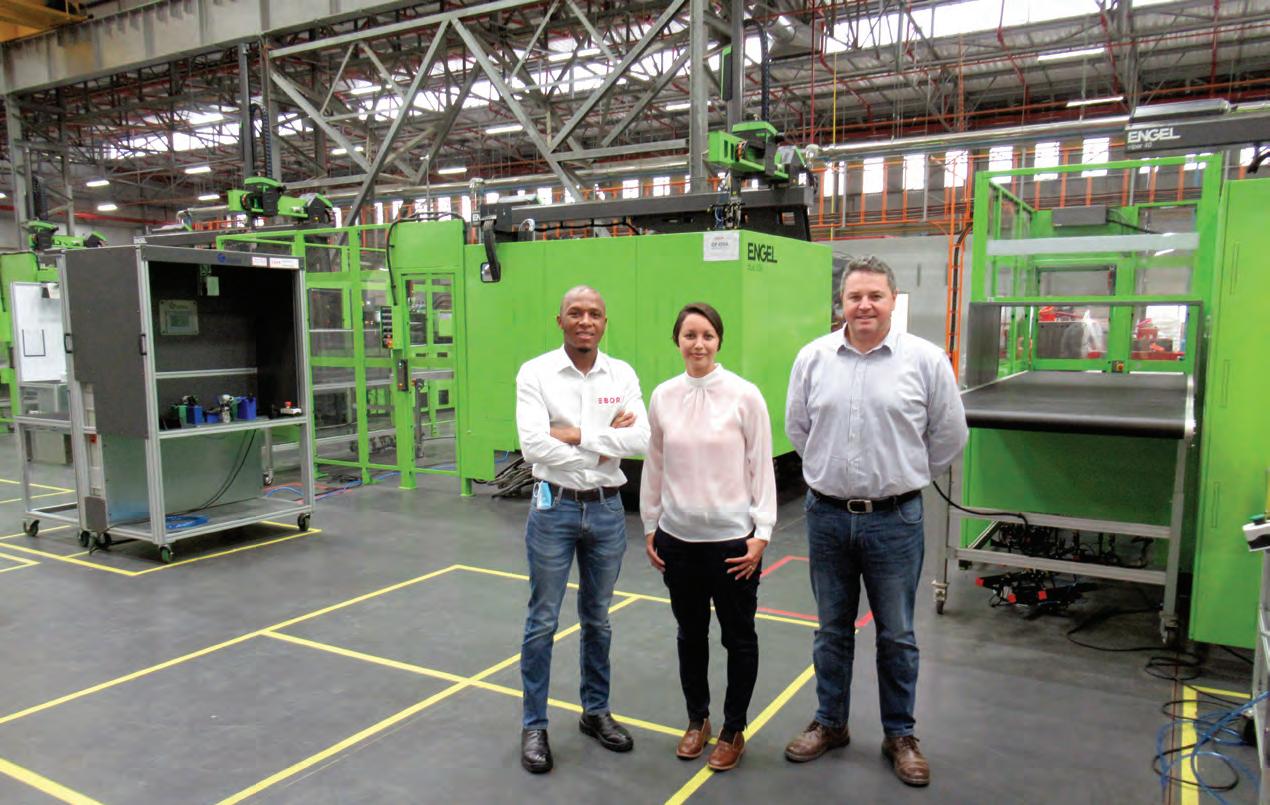
JUNE / JULY 2021 8
second venture by ebor group as Ebor East London starts
Major auto component plant starts up in IDZ
EBOR East London, the second manufacturing unit in the Ebor group following the establishment of Ebor Automotive Systems in Port Elizabeth in 2014, has gone into operation at the East London IDZ.
A major venture following the success of the group’s first venture in PE, Ebor EL has been set up specifically to supply first-tier automotive manufacturers, in this case to supply Mercedes in East London.
Following on the example of Ebor Automotive Systems, Ebor EL is using Engel injection machines, with all 10 of the machines installed so far being equipped with robots.
Partners in the venture include Don Searle and Possey Mina of Aeteus (a venture capital business) and High Street Capital of Johannesburg. The introduction of the new business is testament to the foresight of both the latter partners as well as the Ebor management team, specifically Wesley Strydom (former production manager who is now group MD) and Andy Dealtry.
Strydom and Dealtry had been running Visteon in PE, a venture by Ford group but which had elected to exit the sector and shut the Port Elizabeth plant in 2014. They along with Aeteus and High Street later that year put together a ‘rescue’ plan which purchased the production equipment of Visteon SA and restarted the plant, in the process saving most of the jobs that would otherwise have been lost. Ebor Automotive has since expanded and now employs about 140 people in PE.
Successful operation of the first plant – and specifically on-time delivery to the very exacting specs required – saw Ebor’s relationship with the automotive OEMs grow.
“That at least got us in the queue to supply the automotive groups,” said Searle, who even though in his 70s now continues to invest in plastic converting businesses, an example of commitment that appears to be at the core of the Ebor philosophy.
The same partners mentioned above are now involved with Ebor East London. The plant’s layout is designed to optimize production, which is one of the advantages of starting from scratch. The experience of the managing partners, built on years in the manufacturing sector, has been put to very effective use in this respect. The 4000m² property in the Industrial Development Zone is leased from the IDZ authority.
The group operates a staff trust through which all employees are shareholders in the company.
JUNE / JULY 2021 10
PMM install largest
injection moulding machine yet
CABLETECH Marketing recently commissioned a 530-ton Haitian injection moulding machine at Precision Moulding and Moulds (Pty) Ltd – the largest of three that have been installed at the company over the past two years.
Precision Moulding and Moulds (PMM), established in 2015, started off in a 450m2 building and grew into a 3 200m2 building that they now call home. Owners, Pieter Kleinhans and Morne Steenekamp, boast with over 50 years’ experience between them in the fields off injection moulding, blow moulding, extrusion, roto moulding and toolmaking.
The company’s injection moulding machines range from a 60-ton up to the new 530-ton. Precision Moulding and Moulds specialises in difficult and complicated work; their success to date has been their focus on good customer service and high quality products which is non-negotiable and at an affordable price.
They also have a fully equipped CNC toolroom with in-house CAD/CAM product and mould design.
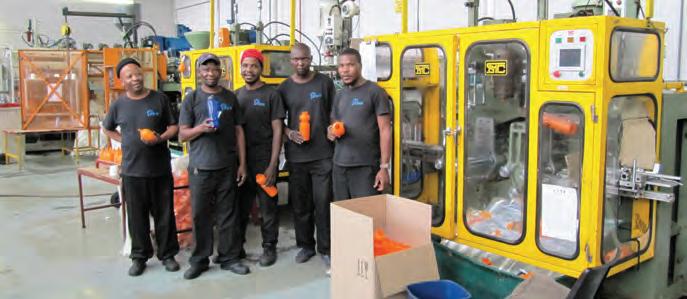
Timothy Khanya, Alpheus Raphaladi, Blessing Josephy, Phanuel Nkuna and Stanley Maluleke with some of the blow moulded products manufactured at PMM
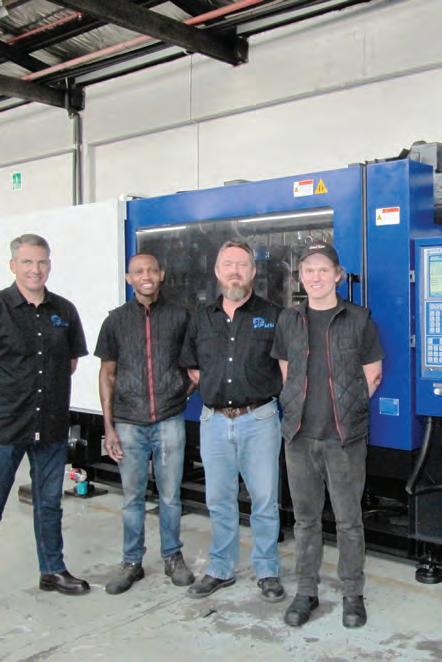
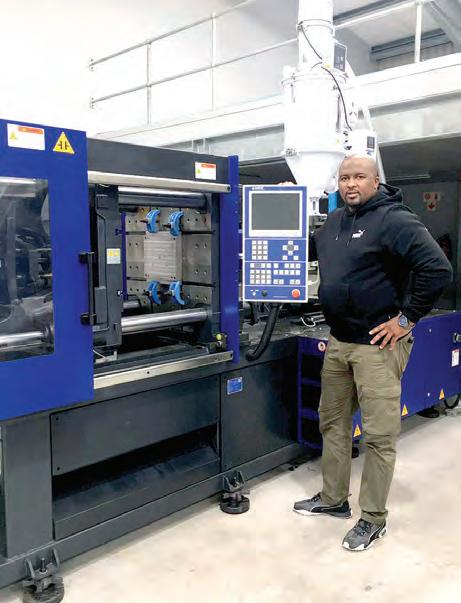
new Breed Holdings starts up
NEW Breed Holdings, an injection moulding business, has recently opened for business in Port Elizabeth.
New Breed is a venture by Luvuyo Sineke, who started out at Transnet, then spent 15 years at Venture SA in Uitenhage (where he learned first about injection moulding), was at Continental Tyres in PE and finally at ISG in East London before taking the decision to go on his own.
According to Luvuyo, who has a National Diploma in Cost & Management Accounting, New Breed “aims to be at the forefront of localization and transformation in South Africa in the automotive and nonautomotive sectors.”
He has been involved in injection moulding since 2018.
Luvuyo Sineke has recently started moulding at New Breed Holdings in Port Elizabeth using two Haitian machines
luvuyo@newbreedholdings.co.za 082 782 9253
The recently commissioned Haitian injection moulding machine at PMM, with Morne Steenekamp (owner), Banele Masimanga, Pieter Kleinhans (owner), Louie-Pieter Kleinhans, Judas Mabasa and Tiaan Visser, Cabletech Marketing sales manager
“We have high speed spindles that allow us to run very small diameter cutters and up to 50 000rpm, resulting in better finishes and faster turnaround times, We are capable of machining moulds with plate sizes of 1 000mm x 500mm. In conjunction with our mould design department, PMM find ways to machine the majority of its moulds without sparking. This relates to quick turnaround time in mould manufacturing,” exsplain Steenekamp.
PMM also offer a turnkey solution in terms of blow moulding for HDPE, LDPE and PVC and all the moulds can be designed and manufactured in-house. PMM can blow mould up to a 2.5-litre sized product and have three double station with single head machines, one double station with double head machine and one single station with single head machine. The company also has visi strip capability.
The company services the mining, electrical, building, stationary and medical industry, to name a few.
“Cabletech Marketing strives to provide service on demand as well as exceptional products for our customers,” says Tiaan Visser, Cabletech Marketing sales manager.
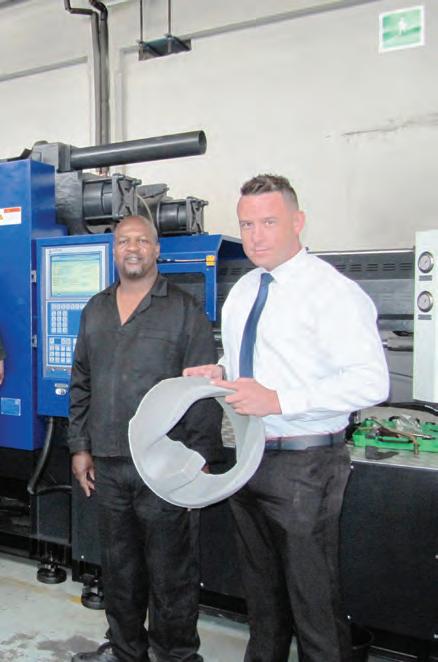
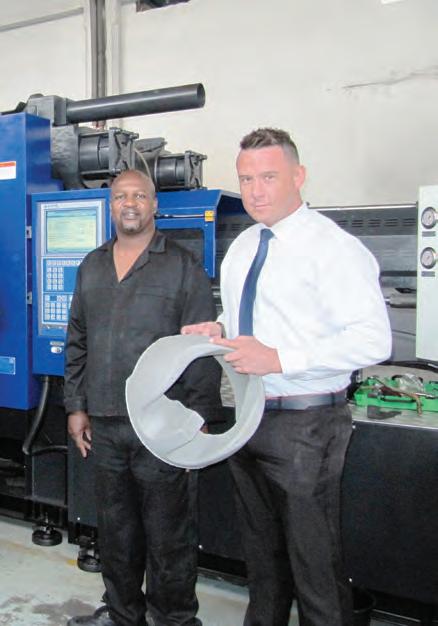
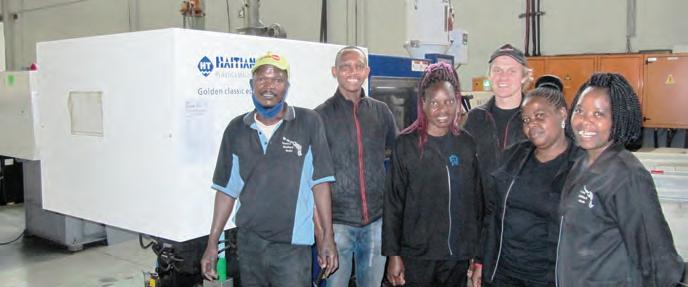
PMM’s injection moulding division with Japhta Makofane, Banele Masimanga, Fidelity Ngwenya, Louie-Pieter Kleinhans, Letta Mavessi and Sandra Mphumela
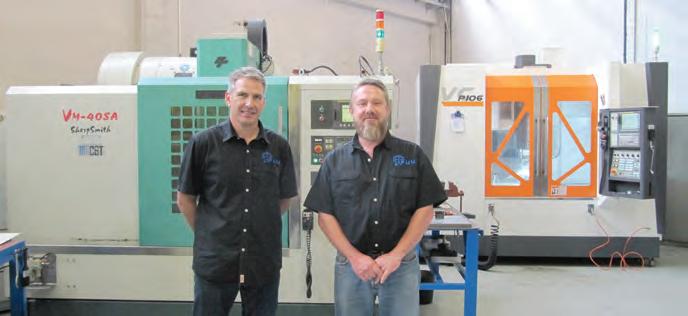
Owners Morne Steenekamp and Pieter Kleinhans, boast over 50 years’ experience between them in the fields off injection moulding, blow moulding, extrusion, roto moulding and toolmaking
Recycler Afri Waste closes doors
AFRI Waste Group, which set up for recycling at Fort Jackson in 2016 and had considerable potential to both reenergise the plastic recycling sector in the Eastern Cape region, has closed. With what appeared to be a solid business plan, Ikusasa inspired hope and there was potential for job creation too. Some customers felt Afri Waste wanted to sell its materials at higher rates than has been standard in the recycled market in SA. Most of the equipment, which included a heavy-duty Enma recycling extruder ex-China, has been auctioned off. The wash plant (the only one in the region up till now) has yet to find a buyer, however.
Kibo, IGES to develop portfolio of waste-toenergy projects in SA
THE share price of JSE- and Aimlisted Kibo Energy rose by more than 7% and 3% on the JSE and LSE, respectively, on 18 May, after the company announced that it had entered into an agreement with South Africa-based Industrial Green Solutions (IGES) to jointly develop a series of waste-to-energy projects in South Africa.
The companies have established Newco, in which Kibo will hold a 65% interest and IGES the balance, to deliver the projects. The parties have set an initial target of generating more than 50MW of electricity for sale to industrial users.
The projects will convert plastic waste, to be provided by waste disposal operators, into syngas using a pyrolysis plant. The syngas will be stored on site and fed into gas engines to generate electrical power. Kibo said that the first project would be developed in four phases of 2MW each, with the first 2MW phase to be completed within 16 months.
JUNE / JULY 2021 12
Cabletech Marketing expands range with Haitian Precision’s new Hision
VMC II CNC machine tools
Growing in-house mould manufacturing demand
CABLETECH Marketing, suppliers of solutions to the South African plastic’s industry since 1976, and proudly associated with Haitian International, has added Haitian’s Hision CNC range to the already successful Haitian injection moulding machine range.
The VMC series machines was specifically built for the mould making industry and features Hision’s own 12 000rpm BT40 spindle, Fanuc IO MF Plus control with 200 block look-ahead, and multiple augers to clear excess metal chips faster. The wide base construction of the machine allows for better rigidity and smoother finishes.
The Vertical Machining Centres with table sizes of 650 x 400mm up to 8 500 x 3 700mm on double column machining centres are complemented by a large range of CNC Lathes from 5-inch to 18-inch chucks and up to 2 750mm between centres.
New Hision CNC vertical machining centres meet growing in-house mould manufacturing demand
Cabletech recently installed two new Hision CNC vertical machining centres at customers to assist with the growing in-house mould manufacturing demand.
Moret Mining was established in 1990 by Roelf and Jodi van Blerk and has since grown exponentially as one of South Africa’s leading manufacturers of conveyors for bulk handling products, as well as for the overseas market. Every product is designed in-house and is manufactured in their Johannesburg factory. Moret passionately believes that with dedicated excellence and commitment to value-added service, great success can be achieved and that is why they use Cabletech Marketing as a machine tool supplier.
As no stranger to the Haitian injection moulding machinery quality and repeatability, the Hision VMC 1000II Vertical Machining Centre became the obvious choice. The machine features large travel sizes for such a compact machine – 1 000mm on X-axis, 600mm on Y, and 600mm on Z-axis – and has 750mm daylight between spindle and table.
Böck industries, however, opted for the smaller VMC 850II version in the VMC II range. Like the bigger brother, the machine also features the same standards but with a slightly smaller machine bed and travel.
Dieter Böck, owner of Böck industries and avid aircraft builder and pilot, felt the need to upgrade his toolroom and after months of deliberation decided that the Hision VMC 850II would be an excellent addition. Accuracy and detail were key and the Hision is able to deliver those requirements
Dieter started Böck industries with his father Ludwig in 1975 when they started manufacturing small household items like key rings and bird feeders. He now works with his son Karl in this multi-generation business. They manufacture household items in the pet, automotive, aviation and floral industries. Their large variety of machines allows them to produce many different products – from number plate holders to electric fence bobbins and much more.
www.cabletech.co.za

Proud of their new Hision VMC850ii are Dieter Böck, Sheree Bershart, Karl Böck and Grant Dennis from Böck Industries and Francois van Wyk from Cabletech Marketing

VinylLoop gets the go-ahead as new vinyls packaging PRO
l p
Driving a circular economy for the vinyls packaging industry
MEMBERS of the Southern African Vinyls Association (SAVA) voted unanimously in favour of forming a separate Producer Recovery Organisation (PRO) within the association, whose specific focus will be to manage the collection and recycling of post-consumer and post-industrial vinyl packaging waste.
JUNE / JULY 2021
14 Why a separate PRO for vinyl packaging?
Explaining the rationale for forming a new PRO for the vinyls packaging industry, Monique Holtzhausen, CEO of SAVA, explains that 70% of the local PVC market goes into non-packaging products that are used in longterm applications such as pipes, window frames and doors, flooring, cables, ceilings or in the healthcare industry. “Some of these products last in excess of 150 years. It is therefore not the responsibility of these SAVA members to fund the collection and recycling activities for vinyl packaging that occupies less than 2% of the overall market. The decision was therefore taken to form VinylLoop for packaging members, Monique funded by packaging Holtzhausen, CEO of SAVA, members and headed up and Adri by Adri Spangenberg.”
Spangenberg, who will head Size of the PVC up VinylLoop packaging market in South Africa
South Africa manufactures roughly about 12 000 tons of vinyl packaging per month that goes into bottles, thermoformed punnets, pharmaceutical blister packs, cling film etc. This represents less than 2% of the total PVC market in the country.
“Although vinyl products are readily recycled in South Africa, there has never been a formal collection and recycling programme for post-consumer and postindustrial vinyl packaging waste due to the fact that the volumes in this market were considered to be too small to justify the costs of collection and transport,” Monique explains.
“As part of our strategy for dealing with packaging waste submitted to Government’s Section 18 Industry Waste Management Plan, SAVA is currently developing a unique collection model for household packaging waste that bears the Number 3 polymer identification code. This plan includes working closely with municipalities and the entire value chain.”
VinylLoop operations and responsibilities explained
VinylLoop operates under the SAVA banner, but will be registered as a separate Non-Profit Company (NPC), with its own board, bank account, membership forms and invoicing system in order to facilitate the bi-annual audits by Government and avoid administrative confusion.
“Companies who sign up to become members of VinylLoop will automatically also become members of SAVA and will therefore reap the benefits of belonging to both associations,” Adri explains.
However, where normal SAVA members pay an annual membership fee, VinylLoop members will be required to pay a monthly levy based on the declared amount of vinyl packaging (in tonnages) they produce over the next six months. Initially this amount will be R100 per ton until 5 November 2021, after which members will be informed of an adjusted membership levy. These funds will be used to set up the necessary infrastructure to ensure VinylLoop members reach the targets that have been set by Government for the collection and recycling of all PVC (vinyl) packaging that is used in the market over the next five years.
As the PRO representing the vinyl packaging industry, it will be VinylLoop’s duty to: • ensure the EPR scheme is audited by
Government; • collect and submit data to the SA
Waste Information system (including how much PVC vinyl packaging is collected and how much is successfully recycled); • put buyers and sellers of vinyl packaging waste in touch with each other; • keep records of identified products; • work with municipalities to develop the necessary collection and recycling infrastructure; • integrate informal waste collection; and • establish secondary markets for recycled vinyl packaging waste.
The new EPR regulations came into effect on 5 May 2021 and all the packaging streams in South Africa now have six months to comply. By 5 November 2021 it will be compulsory for all converters, manufacturers, importers, brand owners and retailers to either belong to a PRO or to have formed their own independent EPR scheme.
For more information about SAVA’s VinylLoop or to sign up, please email Adri@Vinylloop.co.za
www.savinyls.co.za/vinylloop
ASSOCIATED ADDITIVES
Associated Additives is a leading manufacturer and supplier of Lead and non-lead based products into a wide range of markets which include the PVC, mining, battery and chemical industries world-wide.

Our mission is to build on our history of product excellence and technology innovation to provide the highest-quality and most reliable products and services.
Organic Based Lead, Calcium/Zinc, Barium/ Zinc and Tin Stabilisers Titanium Dioxide
OUR PRODUCT RANGE INCLUDE
Processing aids, Impact Modifiers and CPE Calcium and Zinc stearates Internal and External lubricants Metallic Stearates (both Lead and Non-Lead) Flame Retardants Calcine, Assay and Gold-free Litharge Red Lead
Contact us on: Head Office: Tel +27 31 461 9700 | www.almstab.co.za
Physical Address: 245 Lansdowne Road, Jacobs, Durban, South Africa
Siyabonga Ngcobo – Managing Director
siyabonga.ngcobo@ecobat.com
Leanette Moodley – Sales & Marketing Director
leanette.moodley@ecobat.com
Sanele Ngcobo – Warehouse & Logistics Manager
sanele.ngcobo@ecobat.com
Thando Madlala – Market Development Manager
thando.madlala@ecobat.com