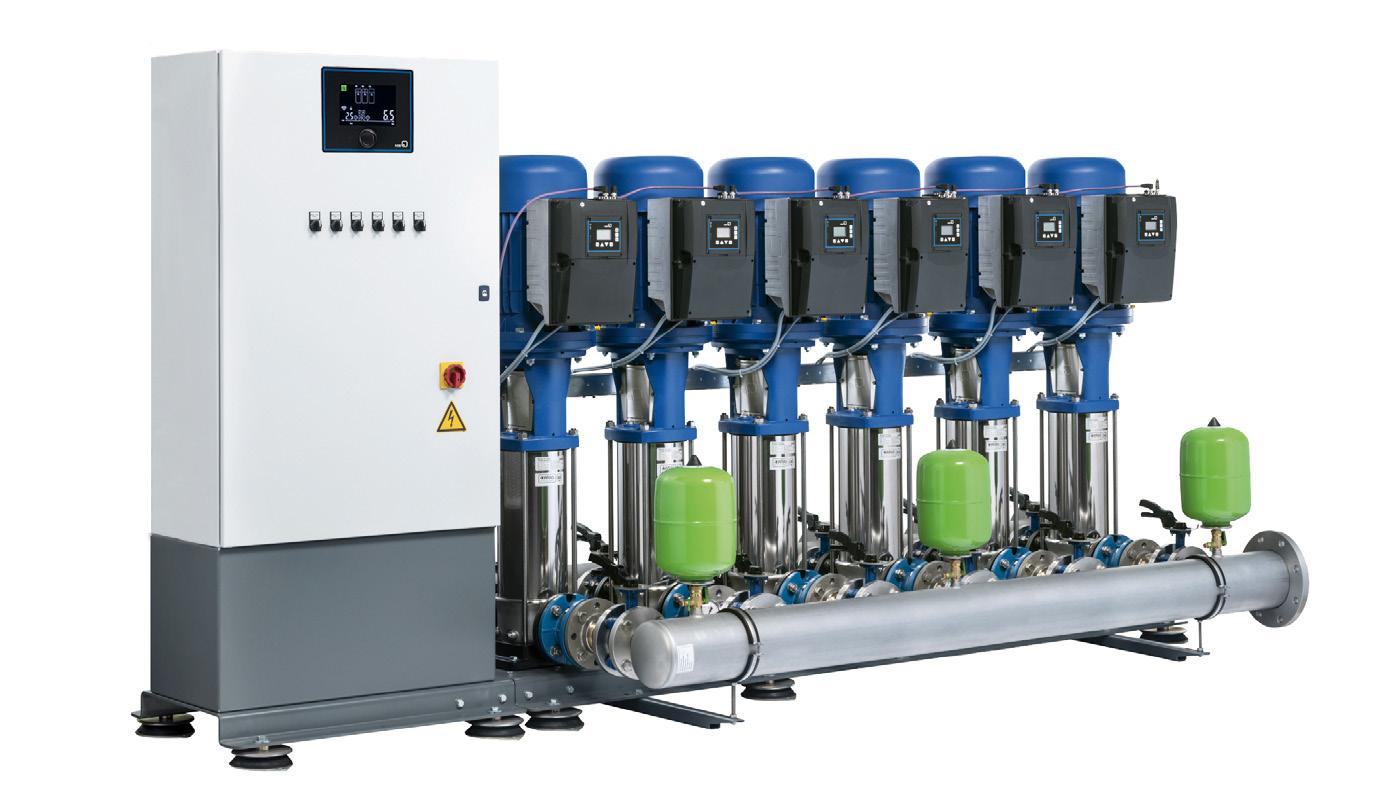
5 minute read
New pressure booster systems for water supply applications
KSB HAS INTRODUCED NEW ready-to-connect pressure booster systems, the Delta Macro type series, designed for large flow rates. The maximum flow rate per system is 960m3/ hr, and the maximum pump head is 160m as standard. The ready-to-connect units operate fully automatically and are equipped with between two and six Movitec high-efficiency centrifugal pumps.
The system’s microprocessor control unit (Booster Command Pro+) starts and stops the pumps in line with demand using either cascade control (F variant) or a frequency inverter for speed control (VC and SVP). LEDs on the control panel indicate the system’s current operating status. A Modbus RTU interface, provided as standard, facilitates connection to external communication devices. For transmitting warnings or alerts to a higher-level control station, the standard configuration has two volt-free contacts on terminals in addition to other optional signal terminals.
The pressure booster systems can be connected to the KSB Delta FlowManager app using a Bluetooth LE interface. The app shows the current status of the pumps, the pressures on the suction and discharge side, and the programmed parameters. It also allows users to control and operate the system directly and change the settings.
The SVP version is fitted with highefficiency IE5 synchronous reluctance motors from the Supreme type series and the PumpDrive variable speed system. The F and VC variants are equipped with IE3 motors. The first pump is started by a pressure drop in the piping on the opening of a consumer installation. While the pressure booster system is in operation, the microprocessor control unit starts and stops the pumps in line with demand.
When water consumption stops, all pumps are ramped down sequentially once the stop pressure has been reached. This ensures that the individual pumps operate only in line with actual demand. If a pump has not been operated for over 24 hours, the microprocessor control unit initiates a test run for the pump. Should a lack of water occur in the inlet, the system stops automatically to prevent damage caused by dry running.
www.ksb.com
NEW TECHNOLOGY FOR HOMOGENISERS CAN REDUCE WATER CONSUMPTION BY UP TO 97%
THE HOMOGENIZER WATER RECYCLING SYSTEM (HWRS) from SPX FLOW is designed to recycle up to 97% of the water used by homogenisers. Traditionally, a continual flow of water gets supplied to homogenisers to cool the transmission oil and lubricate the plungers. The HWRS technology recaptures that water, sanitises and chills it, then returns it to the homogeniser.
The amount of water saved depends on the homogeniser, but the HWRS can save up to 2 million gallons each year (7,500m3). For context, it takes almost three seconds for that much water to flow over Niagara Falls.
“Water recycling has become increasingly urgent as the cost of water and sewer bills rise and the availability of water shrinks,” said Con O’Driscoll, SPX FLOW’s Global Product Manager of Dispersion Products. “We believe sustainability is paramount, and we are continually developing innovative processes and solutions to help our customers reach their goals. The HWRS is a great example.”
The HWRS can be used with both new and existing homogenisers made by any manufacturer. It’s compact – only 533.4 x 812.8mm – and if any problems emerge, the HWRS has its own control system, including fail-safe features that would default to fresh water without causing downtime.
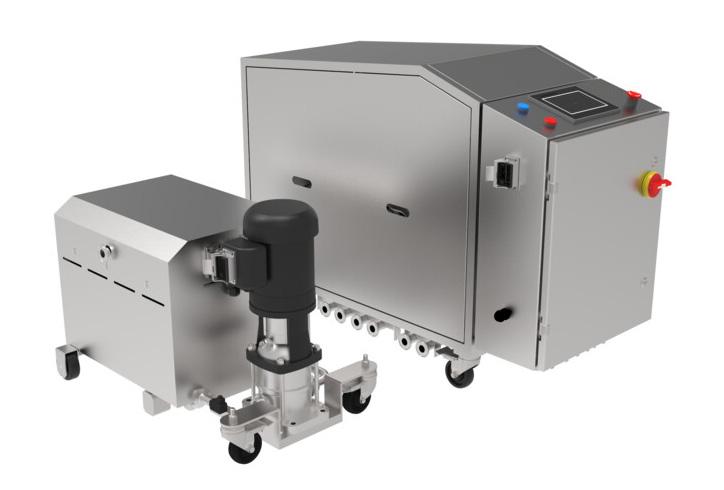
BOREHOLE PUMP RANGE EXPANDED WITH TWO NEW SERIES
CAPRARI HAS EXPANDED ITS product range with two new launches.
The new E6KX series offers the first 6in stainless steel borehole pumps in the EASYWELL family, said to be ideal for professional agriculture, the water sector, and domestic and industrial applications alike.
The E6KX borehole pumps offer a compact design, long-term fuel-efficient performance, high levels of reliability and a low environmental impact thanks to a careful and efficient manufacturing process.
Among other defining characteristics, the attachment between the hydraulic element and the motor can be NEMA 4 or 6, making the pumps compatible with all readily available standard motors. Moreover, the impellers and diffusers are made from stainless steel, and the suction support is in precision-cast stainless steel to offer durability and a long lifespan overall.
The valve body is also made from precision cast stainless steel with an integrated clapet, eliminating the need to install an additional valve, allowing customers to save money while ensuring maximum protection against water hammer.
The E6KX pumps perform even in the presence of sand, thanks to their waterlubricated radial bearings. A booster can also be installed, with a cooling mantle (for the motor) in either a horizontal or vertical position, allowing flexibility of use.
Also joining the EASYWELL family of pumps is the new compact E5MX monobloc series available in ten models and two sizes.
The E5MX series is ideal for domestic, civil and industrial applications, the supply and transport of water from wells and tanks, and irrigation systems.
The EASYWELL E5MX series features a stainless steel compact structure for corrosion resistance, technopolymer impellers and diffusers to ensure reliability even in the presence of sand and an electric motor protected by a double mechanical seal for durability.

www.caprari.com
App calculates drive efficiency
AUTOMATION SOLUTIONS MANUFACTURER, WEG, has developed a new app called EcoDrive which allows engineers to calculate the efficiency of their system — be it a variable speed drive (VSD), motor or a combination. WEG EcoDrive is free to download from the Apple App Store or Google Play.
Last year the European Union changed its ecodesign legislation for electric motors. From July 1, 2021, it became mandatory to meet the minimum IE3 energy efficiency levels for three-phase electric motors (from 0.75kW to 1000 kW), and VSDs having their own efficiency levels of IE2.
In light of this, WEG has developed the app to ensure engineers are in line with the new legislation. It automatically calculates the eight operating points of the VSD and of the system and provides the ability to check the efficiency class of the motor.
“Our app helps to demonstrate the efficiency and losses of WEG inverters and motors in accordance with IEC618009-1 and IEC 61800-9-2,” said Marek Lukaszczyk, Marketing Manager for Europe and the Middle East at WEG. “Avoiding energy waste is crucial for sustainable consumption.
“The regulations regulate the efficiency of VSDs by subjecting them to information requirements such as energy efficiency at different load points in terms of speed and torque. WEG has a complete line of VSDs that exceed the requirements established by the new directive.”