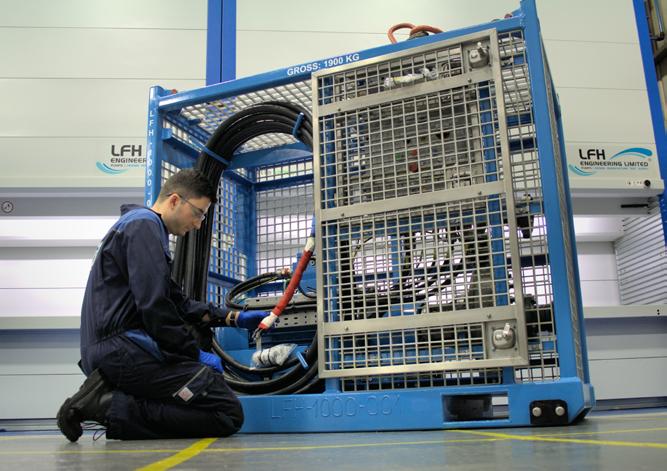
2 minute read
Oil & GAs sector updates
Wellbore pump for light and heavy duty
LFH ENGINEERING HAS INVESTED £250,000 to develop a specialist pump for the oil and gas industry. Having successfully met the demands of the world’s leading diesel engine manufacturers for the past ten years, LFH Engineering has now launched a wellbore testing transfer pump system for the oil and gas industry.
The LFH-1000 electric driven centrifugal pump improves flow performance and solids management processes, overcoming many operational difficulties associated with traditional pump systems.

The compact design can be mobilised quickly and takes up less space than olderstyle pumps. Furthermore, the centrifugal design maximises fluid recovery and maintains a constant flow rate. The pumps are designed to cope with a wide range of fluid transfer applications.
Commenting on the new system, Les Hill, CEO of LFH Engineering, said: “Pumps are what we do – and in particular pumps which are designed to safely withstand extreme pressure, temperature and vibration, all of which are seen in the oil and gas environment.
“Our design calculations determine the pumps capability to withstand a 10g shock load which is necessary for the nuclear industry, so we can ensure the performance we offer is fit for the most demanding working conditions.”
Neil Williamson, Business Development Manager, added: “The LFH-1000 has been under development for several years with input from major well service companies, and we are now in discussion with oil and gas operators and contractors to utilise our pump unit either on or offshore.
“By working closely with a customer, LFH can make minor adjustments to ensure optimum performance. LFH applies detailed finite element analysis to ensure pumps are capable of performing at peak productivity.
“This is a very exciting time for LFH as we are confident that we have designed and built a pump system which is truly unique and meets the needs of a wide variety of offshore and onshore situations.” The Zone 1 electric driven centrifugal pump unit is ATEX and DNV 2.7-1 certified and can handle 11,500 barrels per day (21.2 litres per second) at 33.7 bar.
www.lfhengineering.com
EXPLOSION-PROOF AND SMART
KSB IS OFFERING ITS CUSTOMERS MONITORING solutions for pumps and other rotating equipment used in potentially explosive atmospheres.

The KSB Guard smart monitoring solution is designed for monitoring already installed pumps and is ideal for retrofitting – regardless of pump make. A sensor unit – comprising a vibration sensor and a temperature sensor – attaches to the pump’s bearing bracket and/or drive lantern or to other rotating equipment to record the relevant data. The transmission and battery unit wirelessly transmits the measurement data to a gateway which, in turn, transfers the data via encrypted mobile communication to the KSB Cloud. This is where the data is evaluated and processed. The user can then view the information in the KSB Guard app and on the KSB Guard web portal.
A new feature of the KSB Guard solution is the use of ATEX-certified hardware. The recently launched KSB Guard ATEX gateway is supplied in a flameproof enclosure. The external antennas can be screwed on directly or positioned elsewhere via an extension cable if necessary. The KSB Guard ATEX sensor unit and KSB Guard ATEX transmission and battery unit are intrinsically safe (Ex-i). Both solutions are also suitable for outdoor installation thanks to robust lithium thionyl chloride batteries with a service life of five to eight years in conjunction with 60-minute measurement intervals.