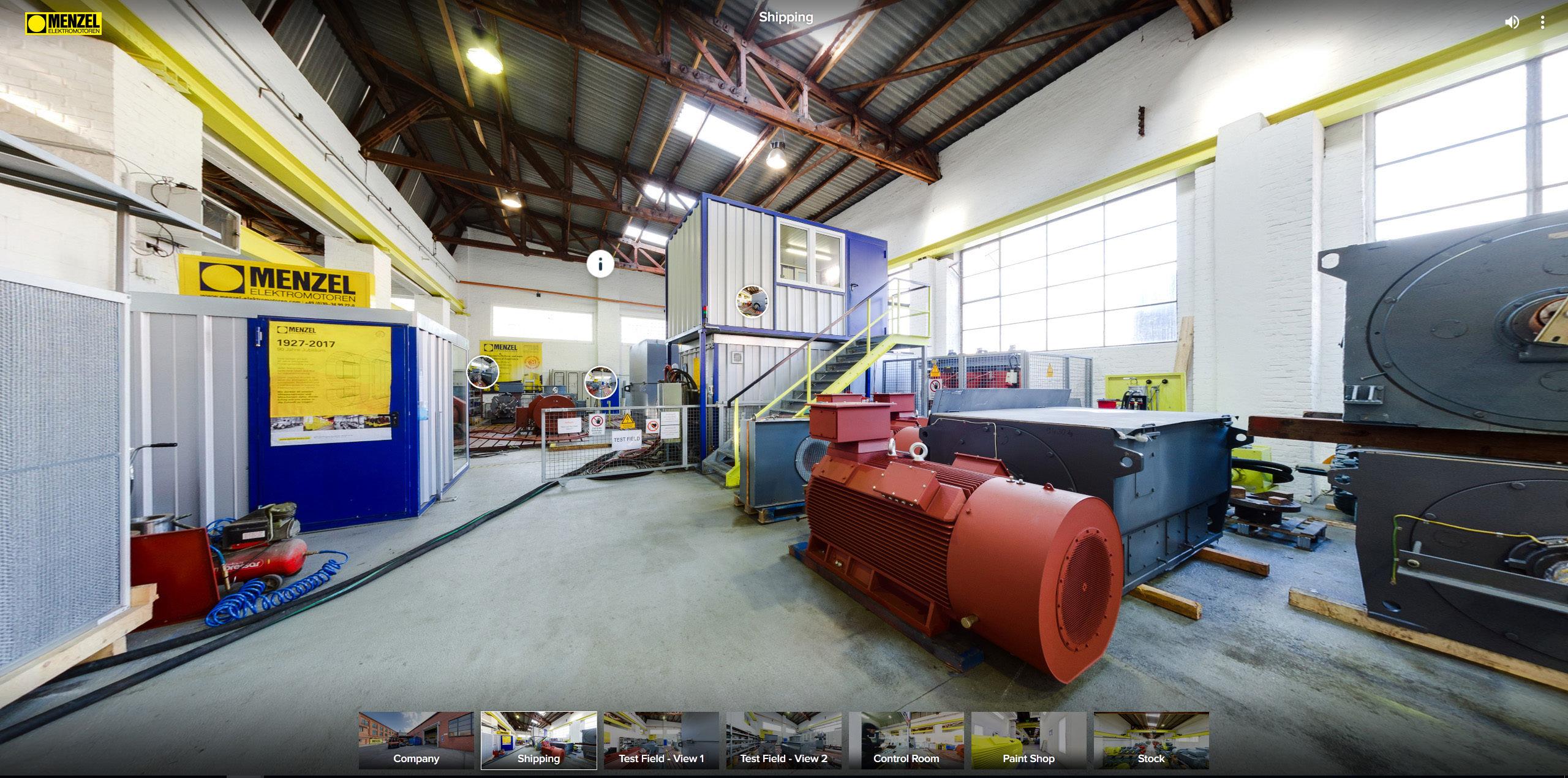
4 minute read
Putting motors through their paces
from Renew Magazine - Quarter 2, 2021. Condition monitoring and predictive maintenance focus
by touchwavegc
Putting motors through their paces
Mathis Menzel, CEO of Menzel Elektromotoren, discusses load testing and temperature rise testing of large electric motors and entire drive systems. He looks at the benefits of different test methods and how testing can contribute to efficient commissioning and operation.

The manufacturer’s digital offer includes live streaming of motor tests to customers and a virtual tour of the test field on the website.
Motor testing might be required for a variety of reasons. In the first instance, it offers a way to verify data.
Motor manufacturers can identify limitations, weaknesses, and performance reserves of products. Notified Bodies use test services because they need to verify data independently, while motor users can check whether their motor or drive system meets their specifications. In addition, testing can also be used for troubleshooting and for parameterisation.
For motor manufacturers, testing is generally the most appropriate way to see ‘how far can we go’ and which solutions are possible. For example, during type testing, it might be questioned whether a motor designed for continuous operation at a certain rated output can also drive another application with a slightly smaller load, with intermittent operation, and if so, what cooling periods are required? Or, might different or more powerful cooling solve a performance issue? Testbed operation offers a safe setting for load and no-load runs. Drive systems can be tested even with extreme parameters, such as severe short-term overloads, voltage drops, or various duty cycles or other non-standard situations during operation.
Load testing creates a very broad database about the tested equipment, and this can be very useful to answer questions at any later stage when the equipment is in the field. For example, the mechanical output is ensured with tested efficiency points, and so the mechanical input for the driven machine is also ensured.
DATA QUALITY
onventional tests with a direct coupled load usually just show that the motor works properly on load. The efficiency values from such a setup will be guesswork. Menzel uses a slightly more sophisticated setup that allows calibrated measurements and produces high-quality information on the actual efficiency ratios. The exact input current is measured with current and voltage transformers. A torque measurement shaft installed between the motor and load measures the generated torque. Losses and efficiencies are calculated from the difference between the (electrical) input power and the (mechanical) output power. With the tested motor and the load generator operated in a closed loop, this setup only consumes power for startup and any energy loss. Therefore, supply lines do not have to be over-dimensioned, and energy-saving tests can be performed over hours and hours. This setup also allows for precise simulation of the application load profile to determine the motor’s performance at individual load points.
COUPLED OR UNCOUPLED
During normal operation, the motor’s thermal behaviour is continuously monitored via temperature probes in the motor windings and on the bearings. These also provide some orientation during temperature rise testing. However, the only relevant reading is the winding resistance, which is measured in a de-energised state after the heat run to determine the final temperature. In addition to direct coupled heat runs, dual frequency testing according to IEEE / IEC 60034-29 is another way to determine a motor’s thermal capacity. This is a viable alternative if direct coupled testing is impossible or not economical. This once common procedure is still being used in the US and Asia but is little known in Europe today. The test specimen is operated at no load; two supply voltages with different frequencies are induced. These different frequencies are adjusted so that the motor’s rotational speed oscillates. The current input can be varied, allowing for a heat run at rated voltage, rated current, and rated speed. The motor’s temperature rise is within safe margins – at a maximum 6% higher than at regular load.

Berlin-based Menzel Elektromotoren operates two in-house load test fields for large industrial motors.
Since dual frequency testing requires no coupling to a load machine, vertical machines and machines with special shaft ends can be tested without modifications. This test method offers energy saving benefits because only the energy losses must be covered as active power. However, it is used exclusively for determining thermal characteristics and does not provide information on efficiency. As an added advantage, test fields that do not have the facilities to test high-output machines at load can instead perform dual frequency testing if they have the necessary know-how.
SYSTEM TESTS WITH ADDED VALUE
If components that have been tested and provenindividually are combined into a drive system, whole new problems can arise. Comprehensive system tests are used to detect and resolve potential interface problems between individual components ahead of commissioning. This simplifies planning and reduces waiting times for end-users.
Over the years, Menzel has noted that the demand for entire drive systems tests has dramatically increased. For example, there is a high demand for testing configurations with a transformer, variable frequency drive (VFD) and motor. Load testing is a means to verify system efficiency at different load points, but it can also be used to set the VFD parameters so that all settings and startup are completed before shipping. This enables true plug-and-play solutions, which helps keep downtimes to a minimum.
To be able to perform a system check, it takes more than just having standard test facilities: there must also be sufficient space to securely place and operate all components, flexible measuring equipment – to measure efficiency on any component of the system – and, most importantly, personnel with the necessary experience to ensure a safe setup that will provide accurate data.