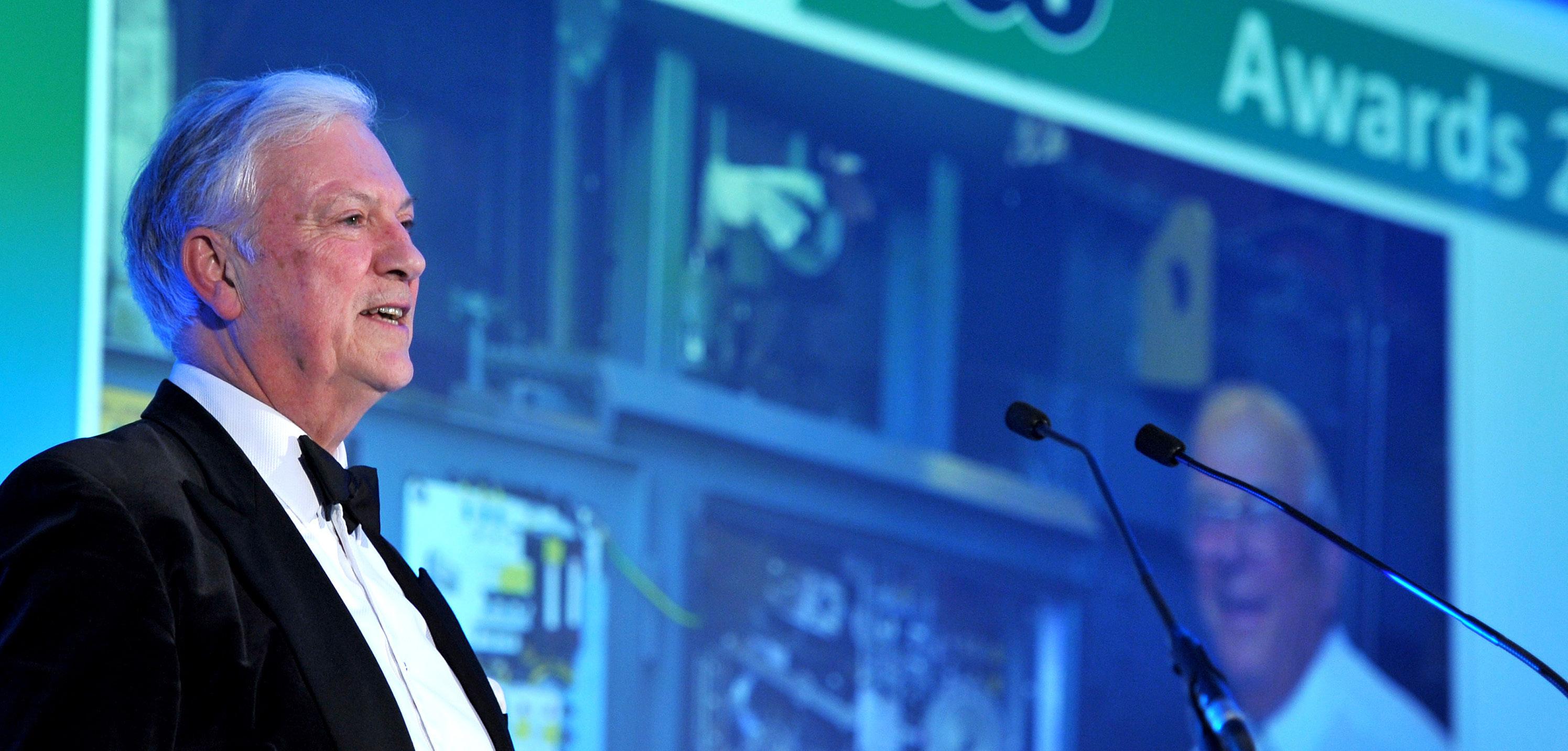
8 minute read
The times they are a changin'
from Renew Magazine - Quarter 2, 2021. Condition monitoring and predictive maintenance focus
by touchwavegc
The times they are a changin’
As he prepares to start his retirement and enjoy more time with his family, Tim Marks, who has spent 20 years as the Association for Electrical and Mechanical Trades’ Secretariat, reflects on how the repair sector has changed and looks at what the future holds.
Like many people, Tim Marks came into the industrial equipment repair industry by chance, as he explained: “Back in 1945, my father started a Lucas agency in York and North Yorkshire. There were few foreign cars or tractors at that time, and Lucas had a virtual monopoly on vehicle electrics.
“We also had a small rewind company. It was a Brook Crompton authorised repairer and sold its motors if a repair could not be done in time. And so, I quickly learnt to love the smell of a burnt-out motor.
“Then, when my father passed away while I was in my late 20s, I took over the running of these companies.”
In around 1975, the rewind company in York joined the Association for Electrical and Mechanical Trades (AEMT), and Tim was encouraged to attend the organisation’s Associates Display and AGM. Suddenly, he realised there was much more to the industry than he had suspected. “In what seemed like no time at all, I found myself on the Association’s council in 1982,” Tim continued. “Then, by 1989, I became President, a position I held for two years, and then again for a year in 1996.” For many years the Association had been fortunate to have a very professional Secretary in Tony Harman, until his retirement in 1991. Then three other secretaries held the role over the following years, all for relatively short terms.
“When in 2001 the AEMT was once again looking for another Secretary, and having been on the council almost continuously since 1982, I suggested that I may be able to carry out the role if it only took up two days per week,” added Tim.
Tim’s offer was accepted, but the AEMT seemed to become more and more of a full-time job. So he stepped back from his other interests to give the Association his full attention.
AN EVER-CHANGING INDUSTRY
When Tim first got involved with the industry, there were many small motor repair shops with very elementary repair equipment: pegboard for formers, a few selfmade ovens, large cans of not very clean grease, no bearing heaters, hammers and chisels to get the windings out, and even the occasional bonfire to loosen difficult windings. And in those businesses, there was often a large queue of motors on the floor waiting to be wound.
But it became clear, through ‘state of the industry’ surveys the Association carried out in the 80s, that the sector was changing, and there were too many rewind companies fishing a smaller and smaller pond. Heavy industry was being affected by political and economic influences, meaning the overall number of industrial motors was reducing. Plus, where in previous years cheaper labour and the relatively high cost of motors had seen most companies want to repair their machines, an influx of low-price motors from countries such as China reduced prices and what could be rewound economically.

Tim Marks speaking at the inaugural AEMT Awards
As a result, over the following years, the number of workshop staff in many rewind and repair companies shrank, and sales of energy-efficient motors and drives increased, needing more people in sales roles.
The electric motor became a commodity identified by a part number, and bearing companies began selling motors with very little knowledge about them or why the previous machine had failed.
Today far greater attention is being paid to ensuring motors do not break down, employing condition monitoring, predictive and preventative maintenance techniques. The Association’s members began supporting their customers by ensuring that unplanned failures were minimised.
As a result, the workforce has evolved once again and now needs to be of a higher quality than ever. Many businesses have an electronics department repairing and fitting drives. A growing number also have teams that carry out maintenance and condition monitoring and the removal and refitting of machines. As motors were increasingly sent for repair with a pump, the industry began to repair pumps and gearboxes as well as the motors. While, of course, the sector also began to carry out inspections and repairs of hazardous area machines.
When North Sea oil was discovered, there was a significant problem that the oil companies were experiencing with the repair of hazardous area machines. The manufacturers were insisting that these machines could only be maintained and serviced by the manufacturer. So the oil companies asked the AEMT and BEAMA, the UK trade association for manufacturers and providers of energy infrastructure technologies and systems, to find a solution so that the repair industry could repair Ex rated equipment without compromising safety and conforming to the original certification. To meet this request, in 1984, the original AEMT BEAMA Code of Practice was published. Then in 1993, this was adopted word-for-word as the International Standard IEC 60079 19 – which covered the repair, overhaul and reclamation of electrical machinery for use in explosive atmospheres – positioning the AEMT as a global authority for this standard.

A Brook Motors advertisement from 1946, shortly after Tim’s father had opened the rewind business Tim would later go on to run. (Image courtesy of Grace’s Guide - www.gracesguide.co.uk)
SHAPING THE INDUSTRY
In the 1990’s the AEMT carried out another series of projects. The first was to prove that burn out ovens could help strip motors without any adverse effects on the machine’s rated efficiency. Having confirmed this assumption, the Association produced the first research-backed good practice guide for repair companies to follow. “This first project looked at smaller machines,” explained Tim. “As more repairs were being carried out on larger machines, the AEMT invited EASA (the American Electrical Apparatus Service Association) to join us on a similar project with larger machines. This proved that motors repaired using the resulting AEMT/ EASA Code of Practice maintained their original rated performance and energy efficiency.”
Several years later, the AEMT also chaired and organised the total rewrite of the IEC Technical Specification for repairing rotating machines. This major rewrite of BS EN IEC 60034 23 was upgraded to an International and European standard when it was published in 2019 and incorporated all the lessons learnt from the above projects.
Thanks, in part, to the reputation the Association was gaining internationally, it has grown quite considerably. Up until 2004, the Association had just a handful of international members. However, with the growing use of the internet and emails, it became far easier for the Association to help international companies, as well as those based in the UK. This led to a rapid growth of AEMT members, particularly in the Gulf and South-East Asia regions.
The AEMT also began offering courses in these locations. This development meant that the major companies in the oil and chemical sectors knew that the service companies they were using had staff trained to the required international standards.
“I am pleased to say that, with its involvement in shaping the standards used globally by the motor repair industry, and through the training it was able to give those undertaking the work, the AEMT has grown to become recognised worldwide,” continued Tim.
THE ROLE OF THE INDUSTRY TODAY
When Tim became involved with the AEMT, electric motors were often left to run in hot, damp, dusty and dirty environments. But much has changed today. Yes, some of the older heavy industries could still be improved, however, the modern factory can now be clean enough to eat off the floor; just look at Maclaren’s facility.
Typically, the only wearing parts of a motor are the bearings. In a modern, clean, air conditioned factory and with modern switchgear, there is no reason why bearings in an energy-efficient motor shouldn’t last 20,000 hours if they are properly maintained and changed before they fail. If the rest of the device is also properly maintained, the machine’s potential life can readily be made to exceed 100,000 hours.
This evolution of the technology has seen the repair industry turn full circle since the early years of Tim’s involvement.
Today, the world uses an ever-larger number of electric machines – motors, generators, alternators, transformers, chargers, and batteries. Because of this, the demand for copper and aluminium is going to be immense.
The repair industry supports the aspirations of a circular economy and is ideally positioned to make the best use of the world’s limited resources. Rewind companies recycle the copper and aluminium they remove as part of a repair or replacement as the highest quality scrap.

Tim Marks with representatives from AEMT member, Asia Motor Service Center Co. during a visit to Thailand
As materials become scarcer, as the demand for more and more green energy grows, and industry and transport are electrified, the demand for companies to carry out remanufacturing of energy-efficient electric motors, pumps, fans and generators is going to grow.
“This is an amazing environmental advantage that the repair industry has to offer,” added Tim. “It ensures the best use of limited resources at a time when awareness of how a circular economy can preserve the world’s copper and aluminium for future generations isgrowing. Currently, these elements could run out within a lifetime. Thankfully, the repair industry is at the forefront of delivering that circular economy.”
Perhaps a lot of the machines will be exchanged and repaired by manufacturers, but many will decide that repair and maintenance is not their core business, creating an opportunity for repair businesses with the right expertise.
In what looks set to be yet another major evolution for the repair sector, the significance of the AEMT and its members looks to be as high as it has ever been. But Tim offered a cautionary observation: “Making the most of these opportunities requires major investment – in both facilities and skills. It will also require a determination to find ways of repairing the machines of the future. I truly hope that many of the AEMT’s members grasp some of the huge market potential and demand for remanufactured and repaired drive motors, wind turbines and other emerging technologies.”
So much has changed in the repair industry in the 20 years since Tim became Secretary. It is clear that his work has had a significant impact on the Association, the members it serves and the industry they all support. With so much opportunity facing the sector in the coming years, he leaves it on an extremely sound footing, ready to reap the rewards of the future. T