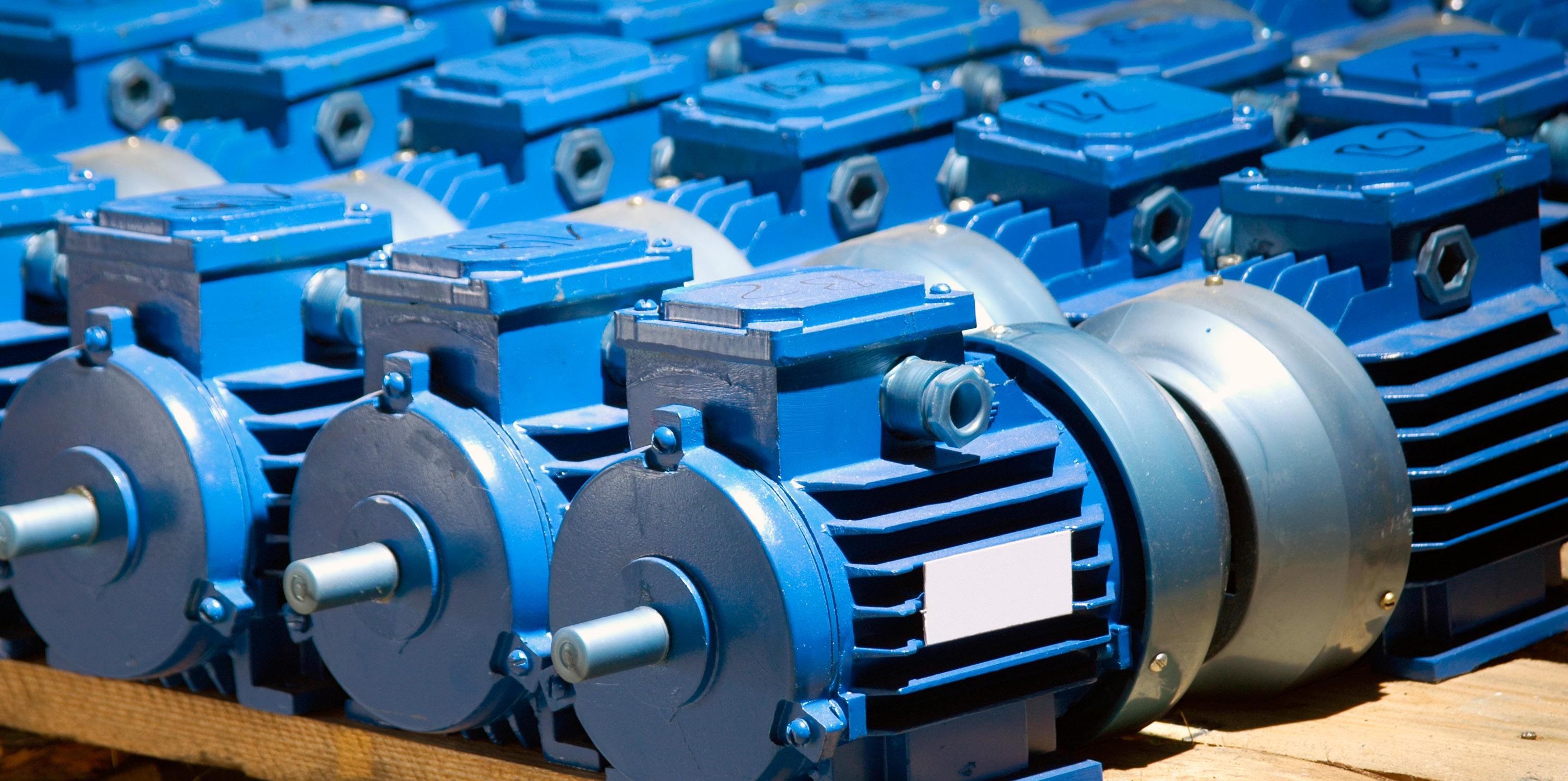
7 minute read
Is your stored motor ready for operation?
from Renew Magazine - Quarter 2, 2021. Condition monitoring and predictive maintenance focus
by touchwavegc
Is your stored electric motor really ready for operation?
Suzanne Gill gathers advice from AEMT members to help ensure that electric motors stored as spares are still up for the challenge when they are finally called into operational service.
Because electric motors are a crucial element of so many commercial and industrial operations, it is standard practice to store working spares on site to ensure fast response times in the event of a motor failure. For this reason, it pays to make sure that any stored motors remain operation-ready, and this requires correct management and regular servicing. Unfortunately, this is commonly overlooked, with many operations not putting enough emphasis on the correct management and servicing of stored motors.
Matt Fletcher, Managing Director at Fletcher Moorland, emphasises the importance of ensuring that the shafts of stored motors are rotated at regular intervals. If the shafts are not turned, the bearing balls will start to wear at the point they rest on the bearing raceway. When the motor is finally put into operation, the bearings will likely fail very quickly. “Turning the shaft regularly while it is out of operation helps to minimise wear on any one point of the bearings, prolonging their life,” said Matt.

"While most people acknowledge that this is necessary, we find that in practice, very few put it into action as no one person is tasked with the job." Matt's advice is that motor shafts get a dozen or so full turns every month, using the keyway as an indicator that this is being done. For example, in January, the keyway is left pointing upwards, in February, it is left pointing to the left, etc., giving a clear visual indication that the task has been undertaken. Matt also highlights the importance of making this task someone’s responsibility as part of a maintenance schedule.
Matt also advises that motors be kept clean while in storage. Often when the motor is not being powered, dust can enter via the cable glands. “I have also seen motors, after long periods of storage, blowing alarming amounts of dust and grime out of their channels when powered up.”
Another area to consider is the shelf life of the grease in the bearings. “I wouldn’t advise leaving a motor with sealed bearings on the shelf for more than two years, as the grease inside the bearing will separate and so will not do a great job when it starts turning again,” said Matt. “If you are storing a motor with regreasable bearings, it is advisable to regrease them once every year or two. This can help prolong bearing life and will ensure that the motor is fit for service when needed.”with the job.” Matt’s advice is that motor shafts
WHAT’S INSIDE MATTERS
While a motor coming out of storage may look in good condition on the outside, it is important that while it is being stored, the inside of the motor is also kept in good condition.
Peter Hardy, Business Manager – lubricant and fluid control condition monitoring, at Socotec, offers some advice. “It is important to store motors in a dry environment because moisture, dampness or being open to the elements will result in moisture getting into the motor and speeding up the oil oxidation process.”
Peter advises that before putting the motor into storage, it is good to first drain the oil, flush it through, and replace it with fresh oil. Oil in operational motors helps ensure that any debris or particles are held in suspension while the motor is running. But, once stationery, any debris held by the oil will sink to the bottom of the motor sump. Then, when the motor is finally started up again, all the debris will be quickly pulled through the motor.
“Filling the motor with the right quantity of clean oil, and ensuring that it is sealed correctly, will slow down the oil oxidisation process,” said Peter. “But, over time, all oil will oxidise as it will react with any moisture and air inside the motor. Unless you are storing the motor in a temperature and humidity controlled environment, the motor will be subject to temperature fluctuations which causes the seals to expand and contract, allowing moisture into the motor, forming condensation – which degrades the oil.” Peter advises periodically checking the oil – once or twice a year – to make sure it remains fit for purpose. “Because all oil will degrade over time, it is also advisable to check the oil before starting the motor after a long period of inactivity,” he said.
Matt makes one last but very important point – don’t let anyone steal parts from stored motors! “I have seen this happen too many times,” he said. “In my experience, the parts most often missing from stored motors are terminal box lids and fan cowls. While it is often only the intention to ‘borrow’ the parts, to replace a broken part on an operational motor, more often than not, the part never does get replaced, which means that the spare motor will no longer be operation-ready.”
In conclusion, if kept in the right environment and properly maintained, motors with regreasable bearings can be safely stored for many years without encountering any problem when they are finally put into operation.
TOP TIPS FOR PROTECTING MOTORS IN STORAGE
GES Group has put together some useful information to help ensure electric motors stay in good condition.
Short-term storage:
Protect the motor from the elements, vibration, and extreme heat. Indoor storage is preferred. If storing outdoors, wrap the motor loosely with a rain-proof tarp but leave a space around the bottom for airflow. If wrapped tightly, condensation will build up inside the motor from the heat of the sun and lack of ventilation.
Long-term storage:
Store indoors in a clean and dry environment, with minimal to no vibration. Consider ‘floating’ the motor on a vibration-absorbing material. Store the motor vertically if it is to be used vertically; store it horizontally if it is to be used horizontally.
Prevent infestation of small animals such as mice or birds, which can damage the winding insulation. Prevent insect infestation by wrapping the motor loosely and covering all openings.
Coat the exposed surface areas to prevent rust and corrosion. Apply a rust inhibitor throughout the storage life of the motor. This will need to be cleaned and removed prior to placing the motor in service.
Frequent shaft rotation is necessary to prevent false brinelling (damage to bearings caused by fretting) and to redistribute lubricant. Rotate shafts on smaller motors a minimum of once per month. Rotate shafts on larger motors a minimum of once per week.
On grease-lubed motors:
Fill the bearing cavities completely for long-term storage. If moisture collects in the grease, drain and replace it. If the grease hardens, dismantle the motor, remove the grease, and repack the bearing cavities with new grease.
On oil-lubed motors:
Add just enough oil that contains rust and corrosion inhibitors to cover the bearings but not so full that it overflows the stand tube or the labyrinth seal.
Windings must maintain a temperature of 10°C to 20°C above ambient temperatures to prevent degradation of the winding insulation.
Take a baseline insulation resistance (IR) measurement before storing the motor, then a second measurement before installing the motor. Any decrease in the measurement can be addressed prior to installation, saving time and costs.
Take a baseline polarization index (PI) of form coil windings prior to storage then again before installation. The PI should be taken once each year the motor is in storage.
To prevent a chemical reaction in DC machines, some synchronous machines, and wound rotor machines, lift the brushes away from the commutator and/or slip rings. To prevent weakening the springs, place them in a relaxed position, if possible.
Out of storage and into service:
Before moving the motor, measure the insulation resistance (IR) with a megohmmeter. Remove dust, dirt, and old grease, and drain if it is an oil-lubed motor.
After installation, record vibration levels, and evaluate the spectra on motors with rolling element bearings for any signs of bearing fault frequencies. Perform a vibration analysis during start-up. Document uncoupled baseline vibration levels.