
11 minute read
Special Feature - ICTI Ethical Toy Program
Audit alone is not enough- how IETP provides the best solutions to support the toy industry
Experts in social compliance audits and remediation, The ICTI Ethical Toy Program (IETP) shares insights into its programmes and explains how it ensures transparency and maintains the best supplier assessment and engagement programmes available to the industry in order to achieve a credible ESG strategy. Aoife McCarthy, IETP executive, tells us more.
The ICTI Ethical Toy Program (IETP), formerly the ICTI Care Process, has operated since 2004. Initially created by the toy industry to oversee the implementation of the ICTI Code of Business Practices, the programme has since developed to reach far beyond audit, providing a number of programmes and assessments to meet the changing needs of workers, factories, and buyers.
We know that social audits are not, nor should they be, a complete labour standards oversight strategy for a company. They do, however, provide an important starting point for companies which are serious about respecting workers in their supply chain and meeting their legal obligations. To be effective, audits must be trusted. You must be able to rely on them and this is how the IETP programme differs from most other labour standards audit programmes.
Unlike other programmes, our work really begins once the audit report is delivered. At IETP, we remediate and close 100% of all non-compliances found in the audit report. Once all non-compliances are remedied the factory is certified. Certification is very different to audit-only programmes; it removes the risk for the buyer. Commonly used audit-only programmes record the issue, but fixing the issue is left to the buyer and the factory. Fixing compliance issues is not easy, especially when you cannot visit the factory. The buyer is therefore left exposed, aware of the issues, but they remain outstanding.
In 2022, we remedied more than 5,000 noncompliances. The three most common noncompliances found related to; Personal Protective Equipment (PPE); worker health checks and chemical storage. If not addressed, these and other non-compliances will lead to significant issues. Our remediation not only closes non-compliances but builds capacity in the factory to ensure they do not reoccur.
Certification from IETP saves money, time and resources for companies, providing peace of mind and enabling you to meet your due-diligence reporting requirements confidently. It provides evidence that your suppliers are operating to the standards required. IETP does not cost more for buyers, licensors and retailers than other programmes; quite the opposite, it saves companies many thousands of pounds. Reducing compliance costs is often a company objective, a review of the cost and value delivered by various programmes demonstrates the cost-effectiveness of the IETP programme. IETP also saves money for suppliers and factories; it removes duplication, provides consistency, helps build their capability and gives them access to programmes designed to meet their business needs. IETP is the best choice value programme for buyers and their suppliers.
Audits in all product categories can be subject to criticism, with allegations of corruption or other factors influencing the audit report findings. Central to how we operate are two factors: the quality of our programmes and their integrity. As a certification programme, the risk is on us - we are saying through the certification award that this factory meets the standards required. That is why we do things differently. Firstly, we only allow an approved group of auditors to conduct audits on our behalf. These auditors are from one of our approved audit partners and they must be an APSCA certified auditor (APSCA is the professional standards body for social auditors, and you can find out more about them at: www. theapsca.org).
The IETP team reviews every single audit report, and we decide the next steps; for example, to award Certification, agree the Corrective Action Plan and any Follow-Up actions. We have channels for reporting integrity issues and our operating methods mean you can rely on our audits; the retailers and licensors trust us. When they conduct quality control reviews of their approved social compliance programmes, we come out on top with zero gaps. This means less challenges for toy companies to manage. We work with major retailers and licensors to ensure the IETP program and their requirements are aligned. This collaboration results in lower costs and less audits. In 2022, we rejected 24.5% of audit reports submitted to us by our audit partners. This review process saves your internal teams time; they receive a high-quality, accurate report the first time. Just ask them how many times they must query a non-IETP audit report…
IETP wants to help increase the stability of your supply chain. We do this by supporting factories to maintain their compliance. IETP is the only programme to maintain engagement with the factory after the audit; we do this through our Progress Visits, which are conducted 4-6 months after a supplier has become certified. In 2022, we spent more than 1,000 days in factories conducting capability building training. The Progress Visit is an opportunity for the factory to share with us their challenges, and through training and expert advice we help them address those challenges, preventing a potential noncompliance from occurring. We work directly in the factory, we know the management, the workers and, importantly, the customers. We know the toy business better than anyone else, no other programme has the depth of industry knowledge as IETP.
With some regions still affected by Covid restrictions, there has been an increase in reports of audit delays, particularity with programmes that allow the factories to select the audit firm they would like to work with. IETP is proud that our members are not experiencing such delays. How are we able to avoid these delays? IETP chooses the audit firms for the factory, we also monitor the lead time of our audit firms to further reduce delays and audit disruption. By working closely with a small number of firms, we are kept notified if expected lead times change, allowing us to reassign audits to firms with shorter lead times and therefore avoid disruption.
As standard, IETP operates an unannounced audit policy, audits can occur anytime within a two-month period. Based on input from our Technical Advisory Council, which is made up of global factory, brand and retailer representatives, we recently introduced the option for announced audits. Factories can request announced audits; however, Buyer Members are not obligated to accept them, and we maintain the right to refuse announced audit requests based on a factory’s past audit performance and transparency.
We understand the real and pervasive issue of “audit coaching”- that’s why our auditors are highly trained. In a Human Rights Watch report published earlier this year (titled Obsessed with Audit Tools, Missing the Goal), Kashyap recently cited: “[t]here’s an entire consulting industry that helps game the system…consultancies to avoid audit scrutiny were particularly pervasive in China and now common in other countries, including Bangladesh, India and Malaysia”. Our auditors are specially trained to identify when a factory is not being transparent, when they are not showing the real information. When we speak with workers, for example, we ask different questions on the same topic to verify and gain a true understanding of the standards in place. We triangulate data to confirm we are viewing accurate records: for example, — does payroll match reported working hours? Do workers report the same hours as the payroll? Is the factory able to produce the volume of goods ordered or are they using unauthorised sub-contractors? Does shipping information support production data? This robust approach and our expertise mean our audits are relied upon.
Without confidence that you are seeing the real situation in the factory, you cannot have confidence in your audits. Only once the real picture is understood can support be given to improve standards. IETP never terminates a factory from the programme if they commit to fixing the issues found on audit; In 2022, we remedied 4,626 noncompliances and 90% of factories renewed their certification. This renewal rate demonstrates the value IETP delivers to directly for factories. It is a case of understanding the real cost of effective remediation and long-term sustainable improvements, cost versus value.
In addition to our robust auditing methods, our online Connect platform increases transparency. Kashyap stated that: “a lack of transparency allows poor-quality audits to thrive unchecked, under the radar” - none of our audits go unchecked, ever, and our Connect platform mitigates the transparency risk. Connect stores the full audit history and compliance data of all the factories in our programme. Once a buyer connects with a factory in the system they can: view their full compliance history, access corrective action plans, download audit reports, receive alerts if zero tolerances occur and even access real-time grievance mechanism information. These features give buyers a clear understanding of the real-time situation in their factories and the confidence that issues which occur will be addressed.
Our Connect platform also houses the Environmental Assessment data of our factories, allowing connected members to gain an understanding of the environmental performance of their entire value chain. The data is digitised and stored allowing for progress to be measured over time. The IETP Environmental Assessment, helps factories share their impacts and is an efficient enabler of scope 3 GHG Emissions reporting. IETP also offers the Social Impact Assessment which provides a verified assessment of the effectiveness of management systems in place to safeguard labour standards at any supplier, agent or vendor within your value chain. This low-cost, efficient assessment is conducted remotely and can be deployed globally, wherever your supply chain extends to.
All IETP programmes can be deployed individually, this means IETP has a programme to support all elements of your ESG strategy and your supply chain oversight objectives. We will work with you to identify who should undergo a full on-site audit and who is appropriate for a remote assessment. Remember, as the only specialist toy industry programme, your supplier may already be working with us, so the data is already available to you. We can also help you find new suppliers.
In addition to robust auditing methods and technology platforms helping factories and buyers, we have our Worker Helpline. This is a free-to-access grievance mechanism, a compulsory element of our programme. We ensure all workers have access to this anonymous grievance channel and have operated this Helpline with great success for more than 12 years. The Helpline is a confidential service, and we ensure that 100% of cases are closed. We welcome the due diligence requirements being introduced by governments all over the world, agreeing that such requirements are essential to improve transparency and encourage remediation. No other programme offers this benefit to its users. Implementing effective grievance mechanisms is an increasing regulatory demand; by working with IETP you meet this requirement with ease. IETP Buyer Members are provided with real-time Helpline analytics including data such as the number of calls received from their factories, the reasons for calls and benchmarking against the IETP factory universe. There is no additional charge for Helpline use for IETP members.
Another reason why IETP delivers much more for companies than audit-only programmes is our Worker Well-Being programmes. These include our commitment to benefit 30,000 children through the provision of quality childcare by the end of 2025, our Family-Friendly Factory Program, and our recently launched Gender Equality Program.
Why is IETP your best choice:
• We are more cost-effective than audit-only programmes. We are the only specialist programme for the toy industry
• We reduce your risks
• We simplify your reporting
• We are your one-stop ESG partner
As we start 2023, we are aware of the challenges ahead for the toy industry. Record inflation in key consumer markets and high inventories in Q4 2022 have resulted in uncertainties for all parts of the value chain. IETP reaffirms its commitment to the industry, we will help our members navigate the challenges ahead and fully leverage the opportunities.
For more information on how we can support you, please contact Todd Merton, Head of Business Development at: todd.merton@ethicaltoyprogram. org or visit us at www.ethical.toys.
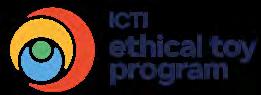