Unlocking the potential of modern construction
Matt Holman considers how to help unlock the potential of modern methods of construction with inputs from a series of panel discussions, held over the past six months by Gardiner & Theobald, with experts from across the supply chain.
The term ‘modern methods of construction (MMC)’ has become synonymous with innovative ways of building – utilising a variety of processes and systems, often involving digital technology to maximise productivity and efficiency. Although popularity is growing, there is uncertainty from some stakeholders about the future of these innovations and whether or not the current supply chain challenges can be overcome
Over the last six months, Gardiner & Theobald (G&T) convened a series of panel discussions with experts from across the supply chain to help unlock the potential of MMC. Oliver Booth and I hosted these discussions which focused on key considerations for off-site manufacture, the impact using MMC can have on procurement and the challenges that can be faced on-site. Each stage of the project life cycle was examined by an expert panel, breaking down the myths and dispelling many preconceptions.
Insights drawn from these conversations included the need for greater engagement with the supply chain to ensure design and delivery partners are aligned from the outset. We discovered the importance of understanding the manufacturing process of any chosen MMC solution when embarking on a new development, to help the project team respond to questions from independent consultants such as a building control officer, and the insurance industry. We also highlighted key considerations for mitigating against on-site challenges and how to ensure maximum value when Designing for Manufacture and Assembly (DfMA), accounting for the impact that taking an alternative procurement route can have on the programme of a development.
In the following discussion, I outline the takeaways from these sessions.
Designing for off-site manufacture
In the first discussion of the series, the live audience voted on what they perceived to be the biggest challenges that might be faced when implementing MMC within construction projects (Figure 1)
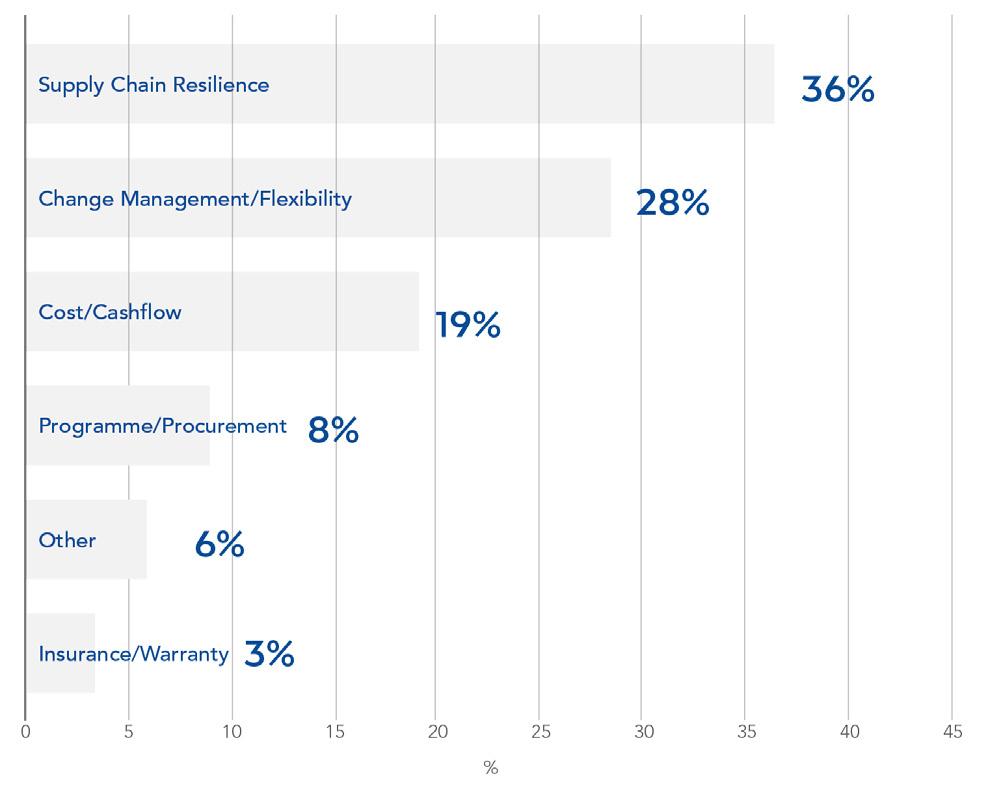
Supply chain resilience was thought to be the biggest challenge, closely followed by change management and the perceived lack of flexibility when implementing the solutions on-site. In the discussion that followed, the panel advised that designing for off-site manufacture at the outset of your project and engaging with your chosen manufacturer early will help to mitigate against risks that may be faced later down the line in the project life cycle.
During this session education and upskilling the current workforce were noted as key challenges we would need to overcome to encourage greater uptake of MMC solutions. However, the panel suggested that these challenges also >>
“We discovered the importance of understanding the manufacturing process of any chosen MMC solution when embarking on a new development.”
present a great opportunity for future growth within the sector – changing the focus from the need for a skilled on-site workforce to a need for the education of those engineering the products in the factory.
Planning, procurement and the role of government
The central part of the series looked at planning, procurement and the opportunities for considering alternative approaches, as well as the role the UK Government has to play in driving the uptake of MMC.
Key considerations included early supply chain engagement as a top priority for ensuring that developments benefit from the programme opportunities and efficiencies available when using MMC. Securing a manufacturing partner early was once again mentioned, and that early engagement with a building control body can also benefit the overall project programme and help ensure successful delivery.
This was a continuous theme throughout all three sessions – so much so that by halfway through the series, 83% of the webinar audience agreed that they would be open to considering alternative procurement routes for future projects to ensure maximum value and support earlier engagement of the supply chain (Figure 2)
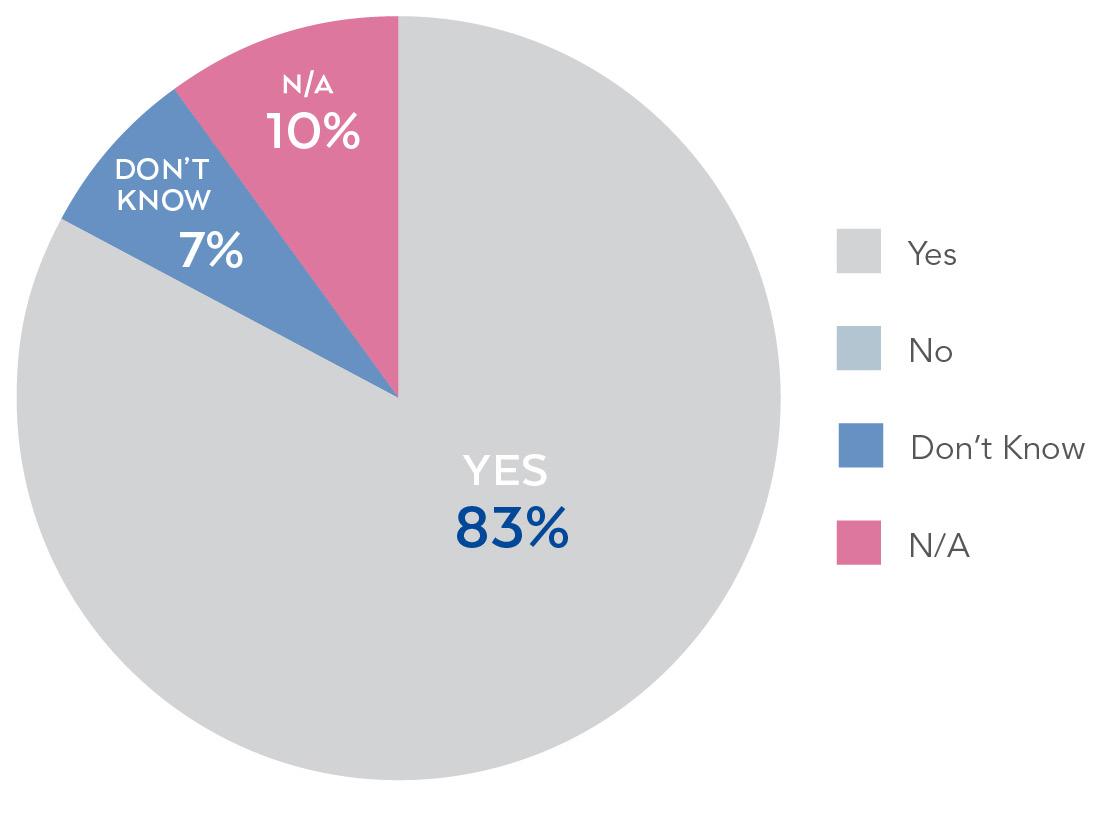
Insurance, onsite challenges and buildability
In the concluding part of our series, we turned our thoughts to the insurance industry, key on-site challenges and what can be done to mitigate against these challenges. We also asked experts from the supply chain, and developers who have implemented MMC solutions successfully, for their advice.
Insurance is often a difficult part of any project that uses new or innovative approaches and, as such, was highlighted as a key topic from the outset. Experts from the supply chain and insurance sector shared experiences of obtaining insurance on recent MMC projects and concluded overall that challenges were often the result of a gap in education. A key lesson from the process was to ensure early engagement with insurance providers, bringing the consultants along on the journey from the factory to the construction site.
When asked what role government could play in supporting the uptake of MMC (Figure 3), 41% of the audience voted for changes to regulation and legislation, followed by the application of planning conditions (19%) and increased subsidies alongside tax reliefs (14%). This shows the desire for greater engagement from government with these new building approaches and that new legislation and guidance would be welcomed by the built environment.
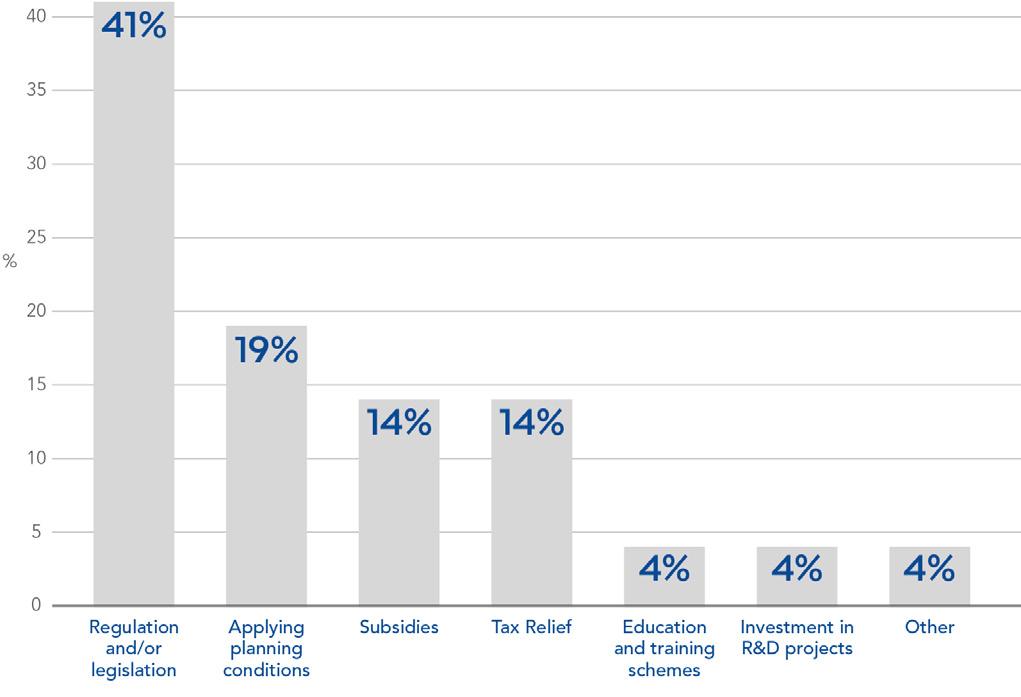
80% of the audience thought MMC solutions would be easier to use on-site than traditional construction methods.
Although our discussions suggest that the biggest challenge faced on-site is perceived as the interface between traditional elements of a development and MMC solutions, we discussed with the experts how best to mitigate against this. >>
“Key considerations included early supply chain engagement as a top priority for ensuring that developments benefit from the programme opportunities and efficiencies available.”
Involving the supply chain throughout the project life cycle will help to ensure all stakeholders are aligned on the plan for delivery and assembly from the outset, avoiding potential problems later downstream. This was noted as being especially important when using MMC, as there is a smaller margin for error on-site, when components are being manufactured off-site.
In summary
The conclusion at the end of our three-part series was that early engagement with the supply chain and wider project team was vital for success when using MMC solutions. Early engagement helps align both the design and delivery as well as maximising efficiencies within the programme and this approach can be felt at every stage throughout the project life cycle.
Education, to ensure consultants and stakeholders are taken on the journey from the outset of the development, can also help mitigate against the key challenges in the factory and on-site. It can also help to avoid downstream manufacturing issues, such as the identification of interface discrepancies or assembly challenges before they have left the factory floor. If choosing an MMC solution, considering an alternative procurement approach to help support early engagement could help mitigate the risk of later-stage programme challenges.
The full details and key findings from these discussions, including any outcomes, will be summarised in a white paper due for release later this year. If you want to find out more about our modern methods of construction series and access a full list of everyone who took part, visit our Market Intelligence website https://marketintel.gardiner.com
We would like to thank everyone who has supported this series, including all of our panellists and contributors throughout the sessions who have helped to make it so successful. n
Futher reading
• https://marketintel.gardiner.com/g-t-launches-modernmethods-of-construction-webinar-series
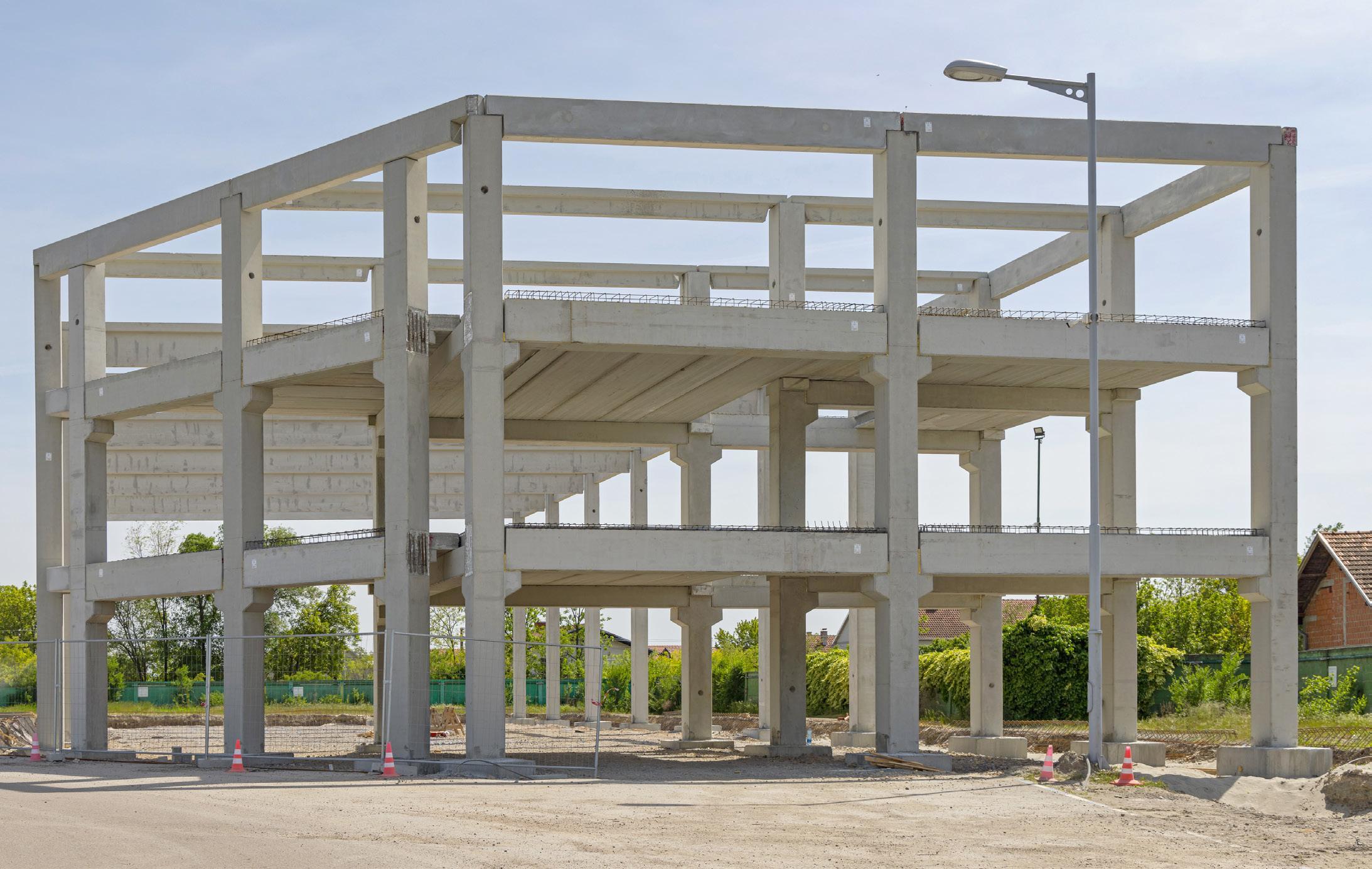
• https://marketintel.gardiner.com/modern-methods-of-construction
About the author
Matt Holman G&T Board Partner MMC Series Host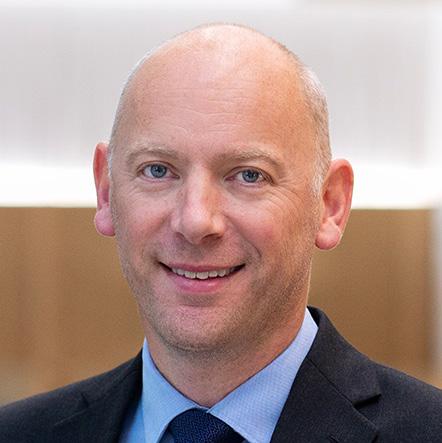