
4 minute read
Abel Libisch
When Is It Time to Replace Your Guardrails? Technology has improved railings, but they can still fail
ABEL LIBISCH
Advertisement
Guardrails play a critical role in a building’s life safety. They can be seen all over town on walkways and lanais of multi-story buildings, in place to prevent accidental falls, where there is a fall hazard greater than 30 feet. It is typically building management and AOAO responsibility to perform regular inspections of the railing.
What to look for
Most hotels and condominiums in Hawaii were built in the 1960s, ’70s and ’80s. Many of their railing systems are now coming due for replacement. Structural and code compliance issues are the key to determining whether or not railings can be considered safe when inspecting
Certified: SERVPRO Cleaned is a defensive cleaning program that goes way beyond janitorial or carpet cleaning. This is proactive viral pathogen cleaning. As the #1 choice in cleanup and restoration, we stand on over 50 years of experience and expertise so you can rest assured that you’ve selected a higher standard of clean for all Americans – you are Certified: SERVPRO Cleaned.
SERVPRO ® of Kailua 808-235-5015
SERVPRO ® of Central Honolulu 808-744-2730
Independently Owned and Operated railings. For building managers and AOAOs to determine if their railings are due for replacement, it is helpful to understand the materials that the railings are made of and what elements to look for in regards to code compliance.
Steel railings
Structural issues are quite common with old railings after spending decades exposed to the Hawaiian climate. With steel railings, the most common issues seen are corrosion of the metal itself. Steel railings from the ’60s and ’70s were factory welded, painted and embedded into concrete walkways and decks. The applied paint helps to isolate the steel from the salty rainwater, but once the paint gets damaged or water penetrates through the coating, corrosion of the steel begins immediately. As the corroding steel expands, cracks form on the paint and in the concrete where the railing posts are embedded, eventually making the posts loose and unsafe. Railing corrosion also causes serious issues in the concrete walkways and decks, as water sneaks into the cracks caused by the expanding steel, causing corrosion of the rebar in the concrete (spalling).
Aluminum railings
The majority of railings installed in the 1970s and ’80s were anodized aluminum. Anodizing is an electrochemical process that converts the metal surface into a durable, corrosion-resistant anodic oxide finish. Anodized aluminum has excellent corrosion resistance—it can be exposed to rain for decades with almost no effect on the integrity of the material. However, anodized aluminum railings from ’70s and ’80s are also showing signs of corrosion, despite the premium metal. The reason for this is anodized aluminum railings have mechanical connections—instead of being welded, they are assembled with fasteners. The fasteners used in the past were typically made of poor-quality steel, which can corrode, especially in the Hawaiian climate. Corroded steel fasteners can break without warning, making the whole railing system unsafe. Nowadays, aluminum railing systems are fastened with stainless steel screws. The fasteners are coated with torque-resistive nickel primer and zinc-rich aluminum topcoat at the factory. The combination of high-quality steel and additional coating provides excellent corrosion resistance.
Aluminum also reacts with the alkalis found in Portland cement concrete. Old aluminum railings commonly show significant corrosion at their post base, resulting in the expansion of the metal, causing cracks and spalling in the concrete just like with steel railings. With new aluminum
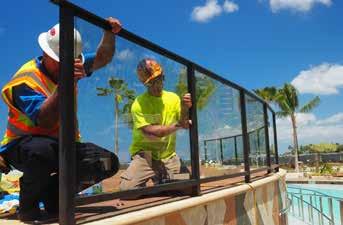
railings, direct contact is avoided with the use of alkali-free materials, such as epoxy, to isolate the aluminum from the concrete.
Code compliance
Old railings in town were commonly built to be 36 inches tall, which has since proven to be insufficient. Current building codes mandate all guardrails to be at least 42 inches tall, in some cases up to 48 inches. Furthermore, the openings in the railing system in the past were allowed to be as large as five to six inches between railing components. In the current building code, the four-inch rule applies: No opening on a guardrail system should be large enough for a four-inch sphere to pass through. This rule was created to prevent small children and objects from falling through the railings.
A couple things to keep in mind:
Newly installed railings must meet current building code requirements and new railing systems may not match the existing railing system.
And all new railing installations require site-specific engineering and a building permit.
It is important to pay close attention to these details and act quickly if the guardrails show signs of failure. When in doubt, make sure to consult with a professional to assess the existing
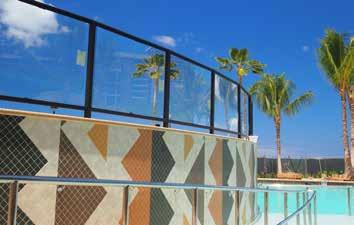
railings to verify if the railings are due for replacement. ❖
Abel Libisch, an architect, is project engineer at Elite Railings & Windows, a respected supplier and installer of aluminum railings and windows for condominium and commercial installations. Working alongside architects, engineers and consultants helps the company remain at the forefront of technology by utilizing state-of-the-art products, material and techniques available for all types of railing and window installations. Reach Elite Railings & Windows at 842-7245 or erw@erwhawaii.com.
HAWAII’S LEADING - RAILING & WINDOW - REPLACEMENT COMPANY
THE ELITE MASTER PLAN:

COMPREHENSIVE ASSESMENT Contact us today to receive a complimentary, comprehensive assessment for your building.
TO EXPERIENCE THE ELITE MASTER PLAN Your personalized, strategic game plan executed to care for every need, concern and detail.
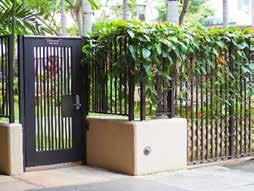
RECEIVE PEACE OF MIND Enjoy increased property value, no liability headaches, and happy occupants.