
2 minute read
Rajasthan
39
40
Advertisement

Rajasthan has an age old tradition of terracotta art and the state is well known for its various distinctive terracotta articles. The arid state also has a special connection with clay and terracotta as people in villages carry water from distant sources to their homes in terracotta pots. Moreover, their daily worship is connected to terracotta idols of deities. Alwar in Rajasthan is famous for making paper-thin light-weight pottery, also known as Kagzi while Pokhran is known for red and white terracotta articles with incised geometrical patterns. Terracotta horse figures, Ganesha idols, as well as idols of local deities like Nag Dev or the serpent god, Bhairav, and other heroes made in Molela are popular in the state. Bikaner district is famous for colorful pottery items painted with lac colors. Terracotta toys and animal figurines are sold in village haats or markets as well as in fairs. The art of making these toys is a legacy from the ancient Kalibangan site of Indus Valley civilization in Rajasthan. The clay used by artists comes from local ponds. Coarse clay is used for plaques and mixed with donkey dung collected by women folk in the proportion of 1:3 making the clay suitable for molding.
41
42
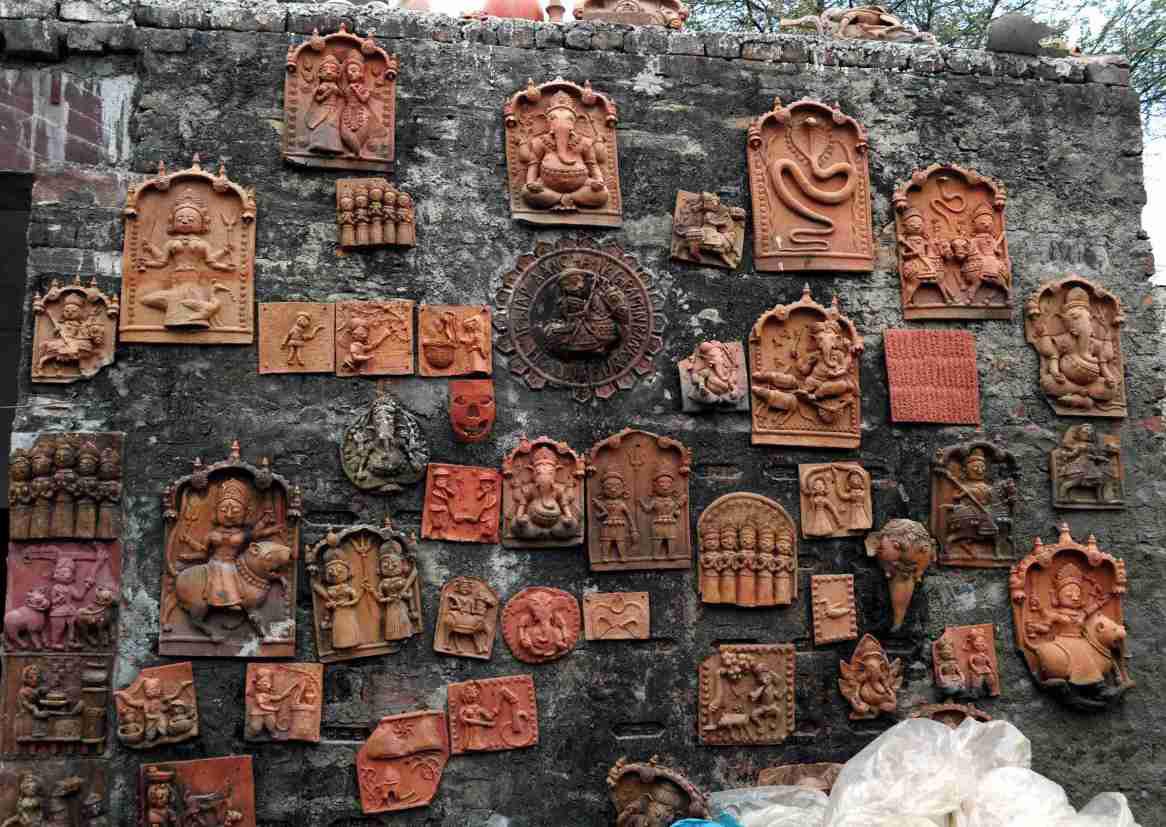
Terracotta of Molela
Molela is internationally known; mainly for its production of brightly painted terracotta plaques and figurines of the local deities and gods.
These clay gods are installed in the temples of towns and villages. Deities and gods are often depicted riding on a horse, a bull, a pig, a dog and even a crocodile. Molela ”peasant potters” descend from a tradition handed down, within families for over 5000 years and are today still satisfying a need for functional (water pots, cooking vessels etc.), decorative as well as religous ceramics.
A potter belongs to the many varieties of the Caste of Kumhar (potter) which in some cases have a close relationship with religous ceremonies.Two main types of earthenware clays are extracted from a local river bed; a pure clay and a sandy clay.
The dry clay is beaten and then sieved with a wire mesh to separate the stones and other impurities. The soft, purer clay is used mainly for throwing the functional wares. It dries to a grey colour which after firing turns terracotta red / brown or even a lustrous black finish (if smoke-fired in a closed kiln).
When the clay is mixed with 5 -10% donkey dung it is ideal for building the plaques and other sculptural pieces. The impure clay, contains plenty of sand, is ideal for throwing the ” supporting - pots”(called Gher) used in the construction of the kiln, and fires to a light pink colour.Nowadays, since the impure clay has far too much sand, 25% pure clay is added. Slips (clay colurs) are only used on the functional wares.White slip is made from a white mineral known as Khadi. White colour is powdered Mica (quartz rich rock), turning a greenish white afer firing. Black is achieved by the mixing of carbon and water. The carbon is scraped from bread pans and burnt coconut skins. Slips are mainly used on the functional wares while the icons are painted with watercolors after the firing.
43
44