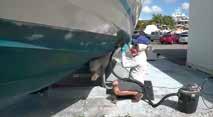
29 minute read
Largest yachts sold Jan.-Feb
NAME LOA BUILDER LAUNCHED CREW LISTING BROKER
Aquarium Zenji 203' 5" (62m) Benetti
2010 14 Michael Mahan & Shannon McCoy 183' 9" (56m) Perini Navi 2004 11 Alex Busher & Dirk Johnson
JANUARY 2022
Mirgab Vi Istros Renewal 2 Luna Rossa Relentless Virago 160' (48.77m) Hakvoort 2010 10 Antoine X. Larricq 138' 2" (42.1m) Feadship 1954 8 Henry Smith 113' 3" (34.5m) Sunseeker 2014 5 Jeremy Comport 111' (33.83m) Sunseeker 2012 5 David Johnson 110' (33.53m) Kingship Marine 2006 7 Nathan Farrelly 100' (30.48m) Nautor's Swan 2006 4 William Titus CPYB
Combined last asking price of all yachts over 79 feet (24m) sold: $153,017,842 USD
*NOTE THAT THIS IS A REFLECTION OF YATCO LISTINGS INTELLIGENCE AND ONLY REFLECT THE UPDATES ON YATCO AND NOT THE INDUSTRY AS A WHOLE.
FEBRUARY 2022
NAME LOA BUILDER LAUNCHED CREW LISTING BROKER
Amarula Sun Exuma Sea Kid Oryx Sensei 164' (49.99m) Trinity
2008 9 Albert Rodriguez & Carmine Galati 162' 5" (49.5m) Picchiotti 2010 7 David Legrand 144' 5" (44m) Baglietto 2007 7 Peter Thompson 131' 11" (40.2m) Benetti 2013 8 Hans Van Doornmalen & Simon Goldsworthy 128' 3" (39.09m) Mitsubishi 1991 8 Mario Liquori
Sea Star
109' (33.22m) Hargrave 2001 5 Yannis Zagorakis & Michael DiCondina Orso 3 108' 4" (33.02m) Benetti 2013 6 Arne Ploch & Fernando Nicholson Lady May Of Glandore 103' 3" (31.46m) Philip & Son Ltd 1929 6 Benjamin Bensahel Euphoria 100' 6" (30.63m) Horizon 2012 4 Sean Madgwick Combined last asking price of all yachts over 79 feet (24m) sold: $98,258,212 USD
One-Stop Services
ONE-STOP TENDER SERVICES
BOTTOM PAINT TENDER HAUL-OUT SERVICES
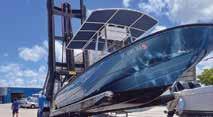
954-791-0550
2700 SW 25th Terrace Fort Lauderdale, FL 33312
www.umcmarina.com
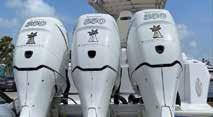
ENGINE SERVICE
BOTTOM PAINT | FIBERGLASS | ENGINE SERVICE | MECHANICS POLISHING | CERAMIC | ELECTRONICS | TOUCH-UP AND PAINT
READY, SET, GO!
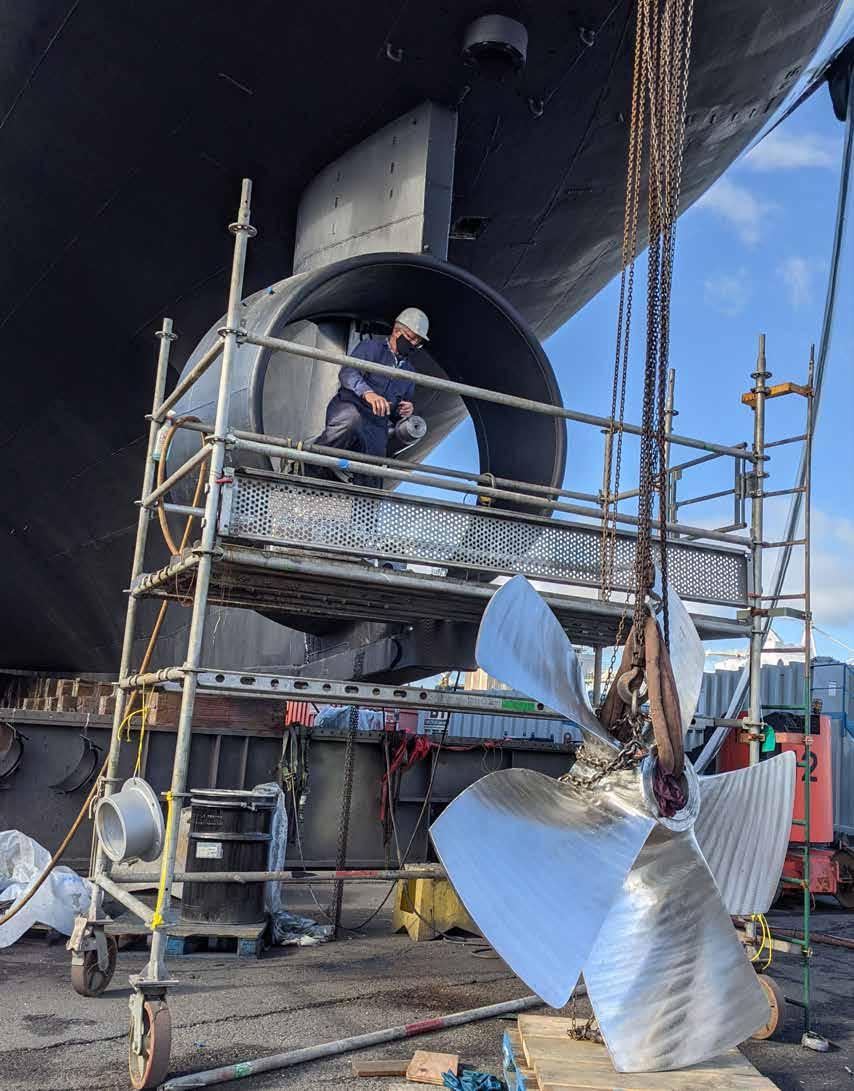
A successful refit means you must prepare to hit the ground running and maintain a steady pace.
By Dorie Cox
Think of a yacht refit like running a marathon: To ease the pain, start with a warmup, make a plan, and maintain flexibility along the way — it’s the same advice boatyard and project managers offer yacht captains before a yard period. Whether preparing for a race or a refit, there are supplies to buy, logistics to schedule, and sections to organize. “Pre-planning is the biggest part, especially with shipping delays in today’s world,” said Sean Hodgson, of DFD Drawings Fabrications and Details. “We've had vessels show up here with a spreadsheet of projects, but the parts are eight weeks out, no contractors have been booked, and the project gets a delayed start.”
The goal is to begin work when the yacht hits the dock, like with his company’s current refit on M/Y Amaral, a 190-foot (58m) Abeking & Rasmussen formerly known as Lady Sheridan.
“Say they only have eight weeks to do the job, and now they have spent two weeks calling for parts and contractor appointments and waiting for shipments. Now they have burned through half their refit schedule,” he said.
George Whitehouse, of Savannah Yacht Center in Savannah, Georgia, sees the same situation.
“You have bigger and better planning, then you have a bigger and better job,” Whitehouse said. “Going into the shipyard is not something everyone enjoys. Owners get into yachting to use the yacht, to travel. But yard periods are necessary — outrageously important.”
Flexibility comes into play with unforeseen situations along the course. “If you hit something or hit bottom and bend the shaft, a new shaft might take seven months to get,” Whitehouse said. He has seen new valves have a six- or sevenmonth lead time. Most yacht captains understand because they have similar challenges procuring regular operational supplies on board. The supply chain is bad and getting worse, but it’s a worldwide situation — everyone is running into it, Whitehouse said.
Although a marathon is often a personal challenge, there are many others in the race, too. In the refit marathon there are loads of yachts undergoing work and shipyards are busy, said Dan Bornarth, assistant vice president of operations at Bradford Marine in Fort Lauderdale..
Calendars are booked and if a yacht is scheduled for refit or basic services, like a bottom job, but other necessary repairs are found, then the project scope changes, he said.
“This could turn into an issue because yard space is at a premium and the yard may have difficulty accommodating the expanded time or work, as there are times of the year when yards are overbooked,” Bornarth said.
“We have more work than we can
even handle,” said David Hole, general manager of Marina Mile Yachting Center in Fort Lauderdale. “We have a guy returning calls for about 30 to 50 boat inquiries a week. It's more than a month out to get a boat hauled.”
To keep things on schedule, captains can be more realistic on work service quotes for systems like heads, airconditioning, hydraulics, electrical, and electronics, Hole said. Although many yacht owners request three quotes, most systems require technical troubleshooting to identify what the fundamental scope of work is.
“Owners, captains would be better served scheduling a limited-service call rather than asking for an estimate to do troubleshooting on the head,” he said, although for bigger jobs like a teak deck or a paint job, it may be worth getting quotes.
There will always be delays, but every aspect that helps keep the yacht on schedule works for the budget, the owner, the captain and crew, as well as the entire yard, Hole said. “If you're late, there is a domino effect that affects the whole yard.”
To better assess the yacht’s status and uncover issues, Hodgson’s team mandates a sea trial before the boat is hauled. Also, the yacht undergoes a vibration study, a shaft and propeller check, and a back pressure reading on engines and generators. Deck target measurements are taken to ensure the boat sits on the keel blocks the same as in the water.
Most yards won't let yachts transfer liquids when it's on blocks, so captains need to do that ahead of time, Hodgson said. “We drop the anchor and chains to get the weight off, and usually it's a time to take the life raft and tender to have serviced.”
George Whitehouse, Savannah Yacht Center

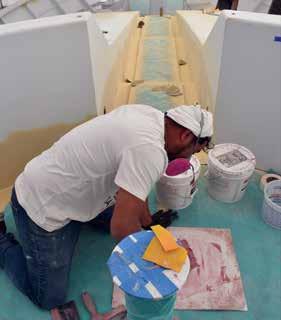
Perishable, valuable or delicate items are removed, then flooring, walls and equipment are covered for protection. Hodgson’s team replaces engine room floor plates with plywood floors. And this is a time to schedule yacht class or flag inspections, check fire systems, replace running and steering gear, etc., he said. It is important to work closely with the crew to see what storage they need, what engineering might be necessary — all the details. And to give the yacht owners a reality check on the amount of work involved.
“This is the part the owners don't see and is where all of the money goes,” Hodgson said. “The weekly report goes to the owner with updates, and unless it's a big, flat-screen TV, they typically have no idea what's going on. I remind them the yacht is a self-contained city, making its own electric, water, and processing sewage.”
The bottom line is that a good refit strategy follows the playbook of long-haul runners at the start line: Break the work into manageable segments, enlist the best support group available, stay on course, and reassess often. ‹ It doesn’t take long for yacht refit costs to climb. But for large jobs, there is a way to save.
Since 2015, yacht owners in Florida have taken advantage of the sales and use tax cap on repairs of boats. “When a yacht gets to $1 million in qualified refit or repairs, then they no longer are responsible for additional sales tax,” said Patience Cohn, industry liaison with Marine Industries Association of South Florida (MIASF).
The nonprofit trade group initiated legislation to provide a competitive edge to local marine businesses that led to the tax incentive for yachts getting repair work done in Florida. Yacht projects must meet certain requirements, Cohn said. For example, they must use single-source billing, through a company like a shipyard or management company, so that there is a single audit source.
Several yards in Fort Lauderdale have worked with their clients to help them take advantage of the savings. The general manager of Marina Mile Yachting Center, David Hole, said he recently was able to extend
OTHER REFIT STORIES
☛
TAX SAVINGS FOR YACHT REFITS
By Dorie Cox
the tax credit to an owner when the yacht’s refit job expanded in scope and the tax cap threshold was met. “I informed the captain that their tax had been capped and they would get no more tax,” Hole said. Georgia has had a similar cap since 2017, but the cap is on $500,000 of work for repair and refit. “The Georgia state refit tax caps still run under the same rules: $35,000 cap on materials, regardless of what you spend,” said George Whitehouse, business development director of Savannah Yacht Center in Savannah, Georgia, where the total tax rate is 7%. “It can be hefty “When a yacht gets to $1 million savings if you’re going through a large refit or in qualified refit or repairs, then large paint job, they no longer are responsible for or whatever.” additional sales tax.” Several states also have exemptions, discounts, Patience Cohn, MIASF or caps on vessel taxes. Tax laws continue to change, but currently, these states include Alabama, Connecticut, Maryland, Massachusetts, Maine, New Hampshire, New Jersey, New York, North Carolina, Pennsylvania, South Carolina, and Virginia. ‹
SIGN HERE — BUT FIRST, READ IT!
A refit means oceans of paperwork, but the critical need to decipher yard contracts and insurance policies cannot be overstated.
By Dorie Cox
Often, captains focus on refit costs and overlook aspects of the shipyard agreement, said attorney Andrew High, manager at High Law, of Florida and Washington, D.C. “They just agree on a number and don’t think to call their insurance company or us. From the legal side, we want to make sure they don’t waive their rights.”
An insurance company or attorney can try to negotiate amendments later, “but there is no guarantee that we can make this happen once they have a signed agreement, especially if work has already begun,” said Rob Carron, senior associate with WTW Marine Superyachts.
“Ideally, captains would call when they have a quote for services, with as much lead time as is feasible,” he said. “And they should call before they sign anything.”
It’s important to review the shipyard’s contracts for adverse language that transfers a third party’s liability back on the yacht owner, Carron said. “Most yacht hull insurance contracts contain an exclusion stating that they will not cover physical damage claims when the shipyard contract states the yard is not responsible for damages caused to the yacht, even if the damage is the fault of the shipyard.”
The wording typically goes on to not allow the owner or owner’s insurance to ‘subrogate’ or recoup their losses from a responsible party. “This is commonly referred to as a ‘waiver of subrogation’ and is unacceptable to yacht insurers,” Carron said, adding that yacht insurance underwriters are not in the business of insuring shipyards.
YOU’RE DOING WHAT?: PROPER COVERAGE
The terms “maintenance,” “repair,” and “refit” seem to be used interchangeably, so what is considered a yard period may vary in time and scope. Because the definition is unclear, owners should consult their insurance company about specific needs, including whether they should add “builder’s risk” insurance to property and material coverage, Carron said.
Even installing a handrail can require insurance changes. Hot work does not have to be a major cut in a steel hull — but welding, soldering, grinding, or work that produces heat or a spark. This increases insurers’ loss exposure, Carron said. To be sure you are protected, request each contractor’s insurance information, procedures, and work description, he added.
The yacht insurance company also may request to see the yard’s insurance policy to ensure that the work being done is covered, said Dan Bornarth, assistant vice president of operations at Bradford Marine.
After hurricanes Harvey, Irma and Maria, insurance coverage changed, according to Carron. Many yachts had refits in the U.S. when they stayed for the summer during the Covid-19 pandemic instead of crossing to Europe — and summer hurricane season is an increased insurance risk. “In particular,” he said, “if you're not going to be able to move the yacht to sea in the event of an oncoming storm, there is a strong possibility the yacht will be faced with a complete windstorm exclusion or a very high named-windstorm deductible.”

NOT MY FAULT: CAPTAIN, OWNER, SHIPYARD LIABILITY
In the case of an incident, liability can be complicated for the yard, yacht owner, contractor, or even the yacht captain.
Attorney High said he reviews coverage protections for the yacht owner. But sometimes the owner tries to blame the captain. “The owner says, ‘My captain signed this and he shouldn’t have,’” High said. “But the law of agency applies. The captain is your representative and if he has acted on your behalf, then he is able to sign.”
Still, yacht captains may be liable for more than they expect. Marina Mile Yachting Center in Fort Lauderdale requires service technicians and contractors to have a certificate of insurance (COI), but captains may try to work around the rule, said David Hole, general manager. They say, "I’m just looking," or “I’ve been doing this for 30 years” — or the captain will put the contractor on the daywork list. But if the captain hired a contractor that was not covered on the insurance, the captain himself could be held liable.
“As captain, you have the responsibility to assess the risks and to protect the yacht owner. Anyone who is on the boat is a potential liability,” Hole said. “How many captains read their insurance binder? Some don't even have a copy of their insurance policy.”
“It’s not a scary process, just don’t be nonchalant,” High said. “This could be a good feather in the captain’s cap, when the captain says to the owner, ‘Hey, heads up, let's get on the phone together, so you don’t have increased risk.’” ‹
Check the rules before the refit
Modifications that don’t account for regulations can be disastrous on budget, time, future use and resale value.
By Capt. Jake DesVergers
Planning for that long-awaited and much-needed refit? Perhaps it was an unplanned trip to the drydock due to an emergency? Regardless of the reason, when dealing with a yard period, it is important to remember that changes to the yacht can affect the current or future status. It is the responsibility of the owner, through his captain and crew, to comply with all applicable rules, while ensuring a safe work environment.
FLAG STATES
The first reference to be made by the yacht is any flag state regulations. Depending upon the yacht’s registration, the flag state may have rules that affect the refit plans. These rules can range from radio equipment modifications to removing a door, or even some new carpet. It is important that the flag state’s rules are referenced to ensure continued compliance.
For yachts flying the U.S. flag, the best source of information is the Code of Federal Regulations (CFRs). For other flag states, such as the Cayman Islands, British Virgin Islands, or Jamaica, the REG Yacht Code (formerly Large Yacht Code) may be applicable.
It is especially important to not only consider the current use of the yacht, but also its future. On many yachts that are “private,” it is assumed that most regulations are not applicable and anything goes. This is not usually the case.
Furthermore, a modification completed now, if not done in accordance with the rules, may affect future use of the yacht. Especially important to older yachts, certain changes can eliminate a previously “grandfathered” allowance. It may also have a negative effect on the resale value. In a recent example, a 164-foot (50m) motor yacht was undergoing a quick refit following a change of owner. With requested. the addition of a towed tender and significant water toys, the captain hired an additional crew member. However, the existing berthing arrangements were not sufficient. It was decided that a new cabin would be created in a section of the lazarette. Unfortunately, the cabin designers and builders did not incorporate
E ___
Ad
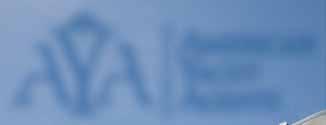
Providing support to yachts throughout South Florida and the Great Lakes. Announcing our new office located at the Port of Palm Beach. Berth One suite ���.
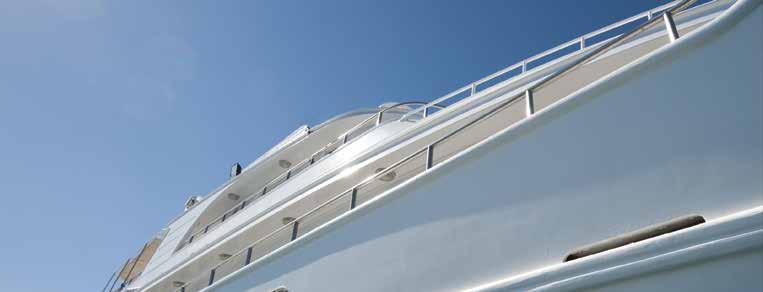
CUSTOMS AND IMMIGRATION
DOCK RESERVATIONS GUEST TRANSPORTATION
AIR CHARTER + OFFICE ASSISTANT + FUEL & WASTE MANAGEMENT +BANKING + FREIGHT FORWARDING + AND MUCH MORE
o: 954.908.7559 | c: 954.684.9456 | captdeb@americanyachtagents.com
the minimum size specifications outlined in the Maritime Labour Code (MLC). In addition, the space was not certified for crew berthing, as there were numerous dangers, including machinery, electrical panels, and a fixed CO2 firefighting system. By installing this cabin without prior flag state approval, the cabin was declared as condemned. The captain was instructed by the flag state to remove the cabin and return the space to its original condition, which meant a lot of time and money lost.
CLASSIFICATION
For those yachts that are classed by a particular society, it is important to ensure that the refit plans are within their rules. Each society can have stipulations for items that range from hull penetrations like underwater lights to satellite domes that may affect stability.
It is especially important to remember that regardless of the classification society, each of them has wording in their terms and conditions referencing unapproved modifications. With rare reversal, class societies can automatically suspend a yacht’s classification, even retroactively. The old approach of “do it and ask for permission later” will not work. And my personal favorite, “that’s how it has always been,” is not going to remedy the situation either.
In another recent example, a 130-foot (40m) yacht was replacing its generators. The engineer was told by the vendor that because the new generators were basically the same and below 130 kW in power, it was not necessary to obtain class approval. The engineer did not verify these statements and the yacht was suspended from class once the unapproved modification was discovered.
OCCUPATIONAL SAFETY
Depending upon where the refit is located, that country will have its own regulations for the protection of shipyard workers. In the U.S., that agency is the Occupational Safety and Health Administration (OSHA). As all readers can attest, the work environment during a refit is far from comfortable. It is the responsibility of the shipyard, subcontractor, and yacht to provide a safe and healthful work environment. This may require limited access controls, personal protective equipment, use of a marine chemist, or specific hazardous training.
Monetary fines from OSHA can be hefty. However, when one reviews the history of those fines, it is almost always after a serious injury or fatality. In over 90% of those situations, the root cause was determined to be preventable. While a refit project is most often focused on returning the yacht to a pristine cosmetic condition, it cannot be forgotten that there are many steps to get to that point. As the old “5-P” adage goes, proper planning prevents poor performance. ‹
CAPT. JAKE DESVERGERS IS CHIEF SURVEYOR FOR INTERNATIONAL YACHT BUREAU (IYB), WHICH PROVIDES FLAG STATE INSPECTION SERVICES TO PRIVATE AND COMMERCIAL YACHTS ON BEHALF OF SEVERAL FLAG STATE ADMINISTRATIONS.
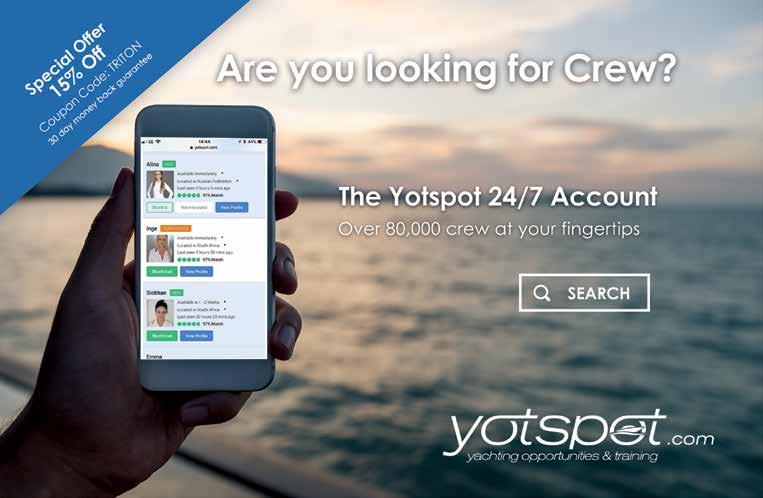
When chaos reigns
We were replacing two engines. They had to cut two holes in the bottom of the boat, disassemble the engines and pass them out through the openings in the bottom. It was scheduled to take two months. The owners decided to redo the cabins too, so all new carpet, wall coverings and linens were ordered.
At first, work was on schedule, but some parts were late arriving. That meant workers did not have anything to do — some were temporarily laid off, so they quit and went elsewhere. Everyone was falling behind. Tension between the contractors and the captain and engineers was heating up. The owner, who was prone to yelling, was impatient to get the boat in time for the Caribbean season. The engineers were under a ton of pressure to get the work done and start rewiring the boat. And of course, once the engines were installed, the bottom would have to be welded, then painted.
All the contractors for the different projects were falling behind. This was costing them overtime charges trying to get caught up, which was added on to the existing budget for the captain to approve.
The interior was scheduled to be installed that last week of the yard period. With everyone else running late, the interior outfitter also was behind schedule and had to cancel or reschedule other projects to complete this one.
Finally, the owner gave an ultimatum to leave by a certain date. The captain and engineers nearly came to blows arguing over whose fault it was that the job was poorly scheduled and the bid was too low to cover the extra fees.
When we got underway, we had electricians on board trying to complete the wiring, and one of the interior outfitters came with us to finish the installation. So we had five extra workers sleeping in the guest cabins, which would have to be detailed and set up after we arrived at our destination. We only had two days to completely clean and set up the entire boat, launder and iron all the new linens, provision, and complete pre-arrival duties before the owners came aboard. The crew was exhausted before the trip even started.

— STEW
Wait — why me?!!
Picture this. The owner has fired the captain and for some reason has put you in charge of an entire refit. Interior, deck, engine room — the works. The contractors are confused: Where is the captain and who the heck is this person? The owner is angry that jobs are not getting done as quickly as anticipated. People are getting fired. This is your first refit. You cry a lot in secret. Who are you? You’re the chief stewardess, and you’re living your worst nightmare.”
— STEW
boatyard nightmares
It's OK, take your time
I’ve found dealing with a union yard the most difficult. The manning requirements to do even the smallest of tasks can be exasperating. One of my favorites from a big Florida shipyard was during the fitting of a new outdoor cabinet. There was a fire hydrant standpipe that came up from the deck. On top was a 90-degree pipe bend that was fitted to the standpipe with a four-hole bolted flange. To fit the new cabinet, it was necessary to unbolt the flange, turn it 90 degrees in a different direction, then replace the four bolts, spring washers and nuts. Apparently, this task would require a minimum of two men and cost $850. A deckhand managed to do the job in about 15 minutes.
At another yard it was promised that the treads of an access staircase from the dock would be covered with corflute sheets so that all the dirt, mud and grit didn’t get tracked up onto the boat. Two workers were sent out to tackle this highly technical task. We watched with utter frustration as it took them three hours to cut corflute rectangles and tape half of the 12 steps before knocking off for a long lunch break. The afternoon session to finish the work dragged on until the finish whistle sounded, and they packed up the tape and scissors and headed home. It made us wonder how the other work would get done when it had taken two guys a full day to cover 12 treads.
Papier-mâché
I heard a story from a boat I used to work on that was recently sold. The new owner is now replacing all the teak. One of the contractors was walking on the deck and his foot went right through the deck. We had previously had a lot of work done to the boat — basically a whole interior refit, took the hot tub off, etc. Turns out, when the contractors had taken the hot tub off, all they did was put cardboard down. They just literally took cardboard, cut a round circle, put it in and put a little resin on top, then chucked the teak on. It was ridiculous. We had a leak in the salon for years that we could not find. Now I know why.
— CAPTAIN
Last in line
Find out when in the yard period the galley part will happen, because the galley will be shut down. I had a galley that was refit at the end, and that was horrible. The subcontractor finished off the project at 11 p.m. on the day before the owner arrived. It was a nightmare. There were still metal fragments lying around, and things that needed to be cleaned and sanitized.
— CHEF
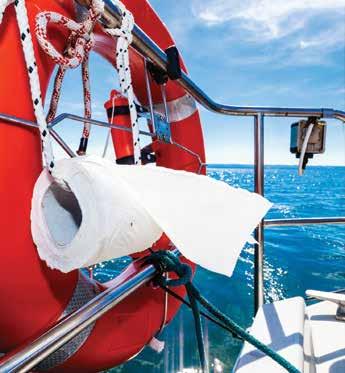
Poop deck
We were having all three decks sanded and we did not want the dirt brought inside the boat, so workers had been told to use the public restroom in the yard, which was very close by. One day, doing their usual round of end-of-day checks, the deckhands found that someone had used the top-deck day head, which had all gold fixtures.
Even though it had been taped off, with a
“Do Not Use” sign on the door ... they had defecated in the sink!
— STEW
Fisticuffs and cops
We had our usual trip to the Bahamas coming up, but the guys were running way behind on getting the teak work and swim platform done. The boss was arriving about 5 p.m., so they were really under the gun. About 3:30, they started getting heated on the platform. One of the guys got up and punched another — hit him right off the swim platform, straight into the water. He had to swim to the catamaran behind us to get out. Then someone grabbed a screwdriver and was going to stab the guy. By the time the boss got there, there were cops in the parking lot. He’s saying, “Oh, I wonder what’s going on here,” and I had to make up some story that there was some crazy person around. Poor planning, high pressure — it was classic.
He said, she said
The owner and his girlfriend would visit the boat occasionally to check on progress. Afterwards, the girlfriend would call me up to say she wanted a wall removed, or a door relocated, and a host of other changes that I hadn’t heard about and were not on the spec. I would call the owner to explain what the new changes were and the cost. Most times he would go ballistic and yell that he didn’t want those changes and not to listen to his girlfriend. Later, she would call me back and ask how the changes were going. I had to explain that the owner didn’t want those changes and they weren’t getting done, which then led to another dressing down as to why I wasn’t following her instructions. If you don’t have clear specification beforehand and know who’s paying the bills, you might just find yourself the meat in the sandwich.
YACHT PAINTING 101
Advice from the pros for getting the best job done on your boat.
By Scott Luxor
Painting your yacht seems like it should be a pretty easy event. But the paint itself is not the problem — it’s everything surrounding it that makes the process either bumpy or seamless.
Triton asked two experts for tips on how to approach your next appointment with a painter. James Brewer, managing director at Roscioli Yachting Center in Fort Lauderdale, has been running boatyards for more than 40 years in South Florida. His team does general maintenance on yachts, including a lot of paint work. Phil Burgess is a general manager with Pinmar USA, which paints about 50-60 percent of the new yacht builds coming out of Northern Europe. Their advice was much the same.
WAYS OF GETTING PAINT WORK DONE
Paint work can be done one of three ways, according to Brewer: • Full service shipyards that perform paint work. • Shipyards that simply provide space for subcontractors who work with yacht owners. • Shipyards that paint a boat for a client using subcontractors.
CREATING A CONTRACT
Both Brewer and Burgess agree that the original contract between yacht owner and painting contractor is the foundation for a good result.
“A successful paint job starts with a contract, which defines what the customer’s expectations are so that there is no misunderstanding between the customer and the contractor,” Brewer said. “The contract should be clear and unambiguous, and include a schedule, warranty considerations and typical protocols for dispute resolution.”
Burgess said that an agreement at the
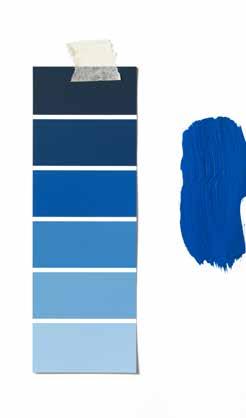
PHOTO CAPT. GRANT MAUGHAN outset makes a huge difference. “Without managing expectations at the outset, you’re going to find a lot of major issues at the end of a paint job, where the client obviously is the person that needs to be satisfied and happy.”
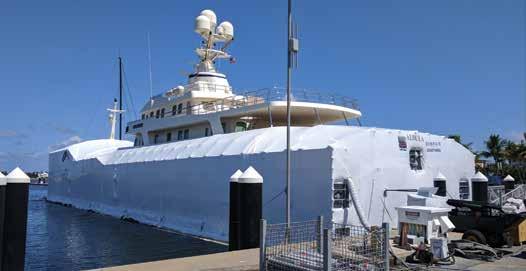
FINDING A CONTRACTOR
Locating a reliable contractor who can take on a project as important as a full boat paint job is critical.
“Some contractors are good, some are really good, and some are not as good,” Brewer said. “The boat owner should check that the painter has a good track record, that he’s performed what he said he would do.”
Brewer cautioned that it’s important to find a contractor that has some depth, since any given “shoot,” or painted section of the ship, may have to be redone if it is bad for any reason. Paintwork is split up into smaller shoots, because any job is too big to do in one fell swoop.
QUALITY OF THE PAINT JOB
The issue of a quality paint job is not just about the color choice, or the even application of the paint. The critical part is the base that the paint is being applied to, since the end result will only be as good as what has been done before.
“We try to minimize a thing called ‘orange peel,’ which occurs when the surface is not completely smooth,” Brewer said. “We also focus on trying to minimize inclusions, which are dust particles and contaminants that can fall into wet paint.”
Brewer said that sometimes contamination can be eliminated by buffing and polishing. However, buffing does degrade the surface, so it’s best not to do business with the paint contractor who relies on it.
Burgess agrees that the quality of the job can all depend on the surface of the boat. “Things behind the surface are called substrates. Whatever you put on the surface is going to accentuate what’s beneath it. A good gloss coat on top will only magnify what’s beneath.”
Burgess warns against impromptu cleaning methods on the painted surface. “You can ruin the paintwork by using the wrong cleaning products or the wrong methods. I’ve seen people use a ‘magic eraser’ to clean the paint finish, and that’s a mistake.” ‹
CREW & CONTRACTORS
KEEPING IT REAL

Whether contractors get the next job may depend on how their workers conduct themselves on board.
By Alene Keenan
Most yacht crew will visit a shipyard for a refit or repair project at some point in their career. Whether they work alongside contractors or simply perform daily cleanup, communication and damage awareness is crucial. The contractor and all employees must abide by any agreement to work in certain areas only and ensure all contents are moved or properly protected as agreed, and crew are obliged to know parameters.
From contractor entry, security checks and work requirements to final installations and cleanup, expensive furniture and fixtures are at risk. Covering decks and interior areas for protection is the first step. Drop cloths, fitted canvas covers, and runners go over furniture, carpets, and cabinetry to protect from dust. Artwork and sculptures must be removed or protected from accidental breakage.
Any work outside of the agreements should be brought to the attention of the captain and crew so that appropriate protection can be applied. If beds must be taken apart to access tanks or wiring, let the department head know. If the air conditioning will be off for any length of time, crew need to know. For example, any wine on board must stay within a certain temperature range, and leather goods can start to grow mold — good-bye, Jimmy Choo shoes and Hermes bags! If workers need to access panels inside cabinets or closets, expensive dishes, glassware, linens, clothing, shoes and accessories need to be protected and valuables placed in a safe place. Contractors should be aware that the cost of replacement for anything damaged will be expensive.
Due diligence is vital. Crew should know what is going on, understand their responsibility, and work with project managers on the punch list for items requiring immediate attention, or any work that does not conform to contract specifications.
CONTRACTOR ETIQUETTE
› Always provide adequate protection before entering work areas throughout the vessel. › Remove shoes or wear booties. › Avoid touching any surface and leaving fingerprints. › No food or uncovered drinks in work areas. › Ask permission and use only bathrooms designated for workers. › Maintain cleanliness of the work area. › Avoid carelessly placing tools and equipment down to prevent scratches and dents, even on covered areas. › Don’t pull anything apart without notifying the project manager or crew members. › No chemicals or solvents without approval. › Address any visible damage immediately. › Know who oversees each project and who to communicate with.
Crew must know the scope of each project and be aware of daily progress to properly protect the vessel. They should inspect and vacuum as needed throughout and at the end of each day. Even with everything covered, accidents happen, and something could be scratched, dented, or spilled that isn’t visible underneath coverings.
Shipyard periods can be tense. Scheduling can be complicated. Communication between crew and project managers is necessary, especially when using different contractors and navigating multiple contracts. It can be a great learning experience for everyone involved, and of course, nothing succeeds without mutual respect. ‹