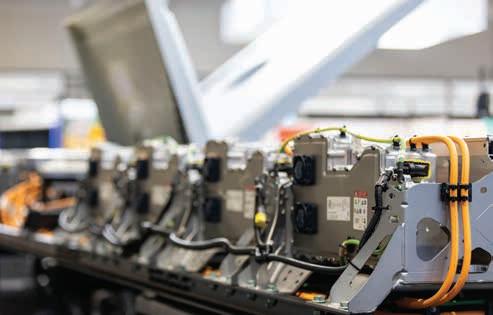
22 minute read
New Technology
MAN chose the Sydney Bus Expo at the start of October for the global premiere of its all new Lion Chassis E LF, a fully electric lowfloor chassis city bus, and along with local distributors, Penske Australia, were determined to make a splash at a show that was chock full of new tech. We spoke with some of the key MAN and Penske execs to find out all about the German brand’s strategy for zero emission buses in Australia.
The realisation that the world has to shift away from fossil fuel in an attempt to head off an existential crisis brought on by global climate change, is something that dawned in Europe well ahead of the more recent change in attitude here in Australia.
Advertisement
For European based bus and truck makers the need to develop zero emission battery electric buses has been afoot for some years, and for the VW Traton owned brand, MAN, it has been an imperative.
Locally MAN’s distributor in Australia and NZ, Penske, has also sharpened its focus to meet the expected rush in demand particularly, from state transit authorities, many of whom who have proclaimed some bold targets for de-carbonising their fleets.
Significantly, MAN made the massive decision to give its latest Lion Chassis E LF, fully electric low-floor bus its global premier at the Sydney Bus Show. It was a massive honour for this country and emphasizes the fact that Penske Australia and MAN are very serious about getting more of its electric buses on the streets of our major cities.
Penske Australia’s executive general manager for on-highway, Craig Lee said the move to a battery electric future for our city buses is the most obvious place to start the journey to zero emission transport.
“I mean in city bus, it’s a no brainer, along with the refuse and agitator market in trucks, but you go to mainstream zero emission, such as longer distance and heavy operations and it is just such a long stretch in this country,” said Craig Lee.
Craig Lee headed up an impressive team from Penske and from MAN in Europe at the Sydney Bus Expo, including Lutz Siebeling, product management and body builder development manager, for MAN Truck and Bus in Germany, Sylvain Messiant, MAN’s head of sales bus international, Christian Fischer, MAN’s vice president, head of sales management and international key accounts for bus, and of course Penske Australia’s newly appointed head of bus and coach, Crinel Geaboc, who comes to Penske from Voith and has a vast knowledge of bus and coach.
“We are very proud that we were able to be together, thanks to the Penske team, to present our MAN Lion Chassis E LF here for the first time,” said Christian Fischer.
“We had good discussions many months ago, and so Penske decided it was right to be here at the Sydney show and we pushed it a lot internally at MAN for sure,” Fischer added with a smile.
The Lion’s E Chassis is basically the bus chassis version of The Lion’s City Battery Electric complete buses we sell in Germany and across Europe, and we have been very successful in the last two years since launching the Lion City, which also won the coveted Best City Bus of the year award in Europe at IAA Transportation in Hannover in September, and may I say there was a great deal of competition with all the big OEMs,” said Christian Fischer.
Fischer is quick to point out that MAN won the same award at the last IAA in 2018 as well, so it was no fluke and points to the esteem the MAN bus range is held in Europe.
“This time I think it was awarded the prize because of its efficiency which is absolutely necessary for our customers,” he said.
“So what you see here in Sydney is the only battery electric chassis at this fair, that was able to drive in under its own power,” he added.
“I think it’s important to know that it took us a little bit longer to come to the market with this chassis, and based on our tradition, let me say German engineering tradition, there was strong competition internally, my thought was to come earlier with something because there was such a need in the market.”
“But I’m very happy that finally it is here now with a complex and efficient product, from battery packaging systems, to the accurate technology and the efficiency of the bus overall, and I think this is something which is really usable for customers in different markets, and especially for the markets here in Australia.”
Fischer admits that Australia is a very different market to Europe, not just in terms of awareness for electric and take up of it at the moment, but also climatically, which he says is a challenge for any electric bus make on a broader scale.
“However we are selling buses all around the world, and Australia is not that different in terms of climate to say Barcelona, or in Abu Dhabi,” said Fischer.
“I might say we have also sold diesel buses in those places as well and for sure they are built to work in high climate environments,” he added.
“Climate has an impact on the mileage of an electric bus for sure, but our test shows us that we can easily handle 200km, but certainly in most situations they can achieve 250 to 350 km but with 480 kilowatt hours of batteries on the roof you can have roughly 400 kilometres,” Fischer said.
“An average range is important because when you measure performance, because you need to understand the consumption, and the range is also dependent on the driving style, and with that in mind there is a lot to be gained from driver training that comes with the MAN product and which helps customers to achieve better range and more efficiency.”
Fischer says that in implementing new electric buses to fleets fleet there needs to be strong planning and analysis of the energy consumption for the routes, training of drivers, specifying the number of batteries and the range that operators want to achieve are all important in getting the best efficiency out of an electric bus.
“Extended range options can also be deployed using up to 80 per cent of the battery capacity, or you can have a reliable range using only 65 per cent of the capacity of the battery bank, which is guaranteed for the life of the battery, which is eight to ten years,” said Fischer.
“The scenario would be to have only one set of replacement batteries replacement in the 20 plus years life of the vehicle. The warranty of the batteries is currently eight years and that will eventually increase to 10 years which will reduce that total cost of ownership of the bus and that is really important,” he added.
MAN’s electric buses have managed to achieve way more than 350 kilometres, in fact one test result saw them exceed 550 kilometres, although Fischer says they won’t make such bold claims.
In the implementation of the new Lion Chassis E LF MAN is supplying mobility services to help customers to transit from the diesel conventionals to electric buses. Helping to achieve the ambitious goals announced by Australian state governments, particularly NSW, which wants to transition out of its diesel buses possibly by 2035, is the goal of achieving a 50 per cent reduction in carbon.
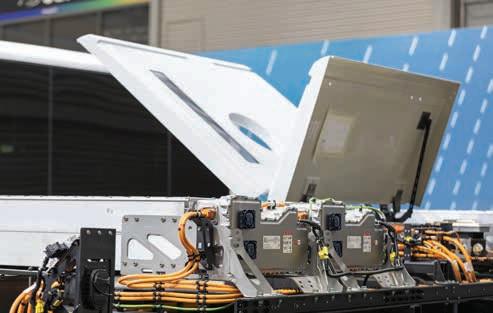
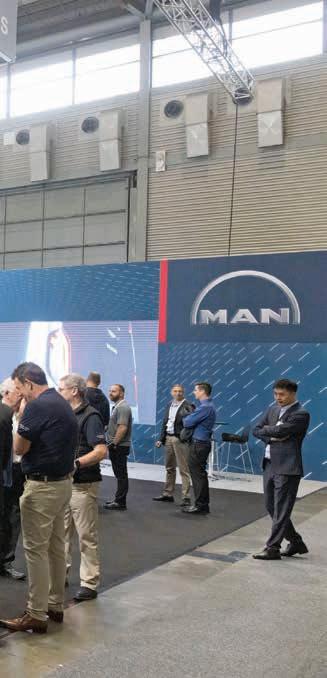
MAN says that now with its electric chassis it has 30 per cent local content, and it does that by counting such elements as after sales, training and shipping, which some may question, but clearly the company values all of those elements.
Local Penske boss of on highway operations, Craig Lee says the local operation completely supports government strategies to decarbonise our cities, and thinks it is an admirable aspiration.
“We are committed to that, we are committed to growing our MAN portfolio extensively in truck and bus and buses are strategic for us, Australia and New Zealand are very strategic to MAN and it has recognised them as important markets.
“That’s why this collaboration has come about with the global premier of this bus and the markets that we are continuing to grow,” said Lee.
“Those are not just words being said by MAN, we actually have a strategic vision at Penske Australia, that we’re working towards at the highest levels of MAN and Penske globally,” he said. “We’re very motivated by this and not just with electric, because we see that diesel is going to play a major role for some time to come,” Lee added.
Penske also had MAN Euro six buses on display at the Sydney show, and says they will be an important ongoing part of the market in Australia for years to come, particularly with coaches.
“People forget that Euro six is very clean, in fact it’s incredibly clean, and we recognise domestically that we need clean internal combustion engines to eliminate all of the challenges that Australia is going to be faced around range, operating conditions, availability of charging, infrastructure and capacity,” said Craig Lee.
“We recognise all of those challenges, which is why we will continue to run our regional and our metro fleets and regional non metro fleets, with a strong focus on diesel and Penske absolutely wants to get more than our fair share in our market,” he said.
Lee said governments have to continue investing in zero emission and thinks it doesn’t just need investment, saying that it needs government policies to help meet the infrastructure needs and to ensure bodybuilders have the capacity to meet those targets.
“So our strategy for the nest two years is that 2023 is very much about getting the product well and truly tested and developed for Australia from a dimensional and an application specific perspective. Then in
2024 we plan to be in supply of our 2.5 metre wide bus in Australia,” said Craig Lee.
The Penske executives believe that a move to a 2.55 vehicle width is still being closely guarded by local content and bus builders, which is why we are still the last country with 2.5 vehicle width in the southern hemisphere.
“I think that we will have both products available in the medium term, so we will have 2.5 metre electric buses here from the first of January 2023, but 2023 is very much a year of development, testing and verification, we won’t have any 2.5 metre electric buses selling in 2023,” Lee said.
“So alongside our product roadmap, we are not standing still, EV technology is moving very fast, so our plans on product procurement also involves the high floor or intercity version with updated battery technology, so that means we are talking about different packaging, and different levels of kilowatt hours available in the buses,” he added.
Lee said that in terms of volumes, the industry has to also be mindful about integration of the electric buses into the electrical infrastructure of depots and the lead times that are involved in getting a bus depot converted from a diesel operation to a base for electric buses.
So it’s really 24 months from the moment a bus operator decides to place the order to when you can actually put your buses on the road, including getting the approvals and putting in a bigger energy supply, to the various development approvals and to actually put the infrastructure into the depot. That includes cabling, upgrading substations, installing chargers, it is all going to be a massive challenge,” Lee emphasised.
“So transition from diesel to electric won’t take just five minutes, and it’ll be a lengthy transition.”
MAN like the other Traton subsidiary, Scania appears to be lukewarm about the prospects of Hydrogen fuel cell as a zero emission technology, and Craig Lee said he doesn’t believe Hydrogen is something that they may end up focusing on at this point.
“MAN recognises it as a potential solution at this point and they certainly have one eye on it, but from a bus perspective, at this point, the focus is very much on battery electric,” said Craig Lee.
Christian Fischer took up the line from a MAN factory perspective saying that hydrogen is a challenge for the European market in getting sufficient supplies of green hydrogen and for it to be cost relevant on the same level as BEV, and he doesn’t believe this will happen any time soon.
“Hydrogen is available, but it’s much, much more costly, so it doesn’t fit the cost expectation of the customers and to get it green, is also a challenge,” said Fischer.
“Today, it’s not realistic but let’s say it’s something that is not feasible today, but let’s see what the future brings,” he added.
From January 2024 MAN says it will have an intercity electric bus available, although it will be 2.55metres wide with exactly the same driveline and with its batteries located in the luggage bins rather than on the roof as in the city buses.
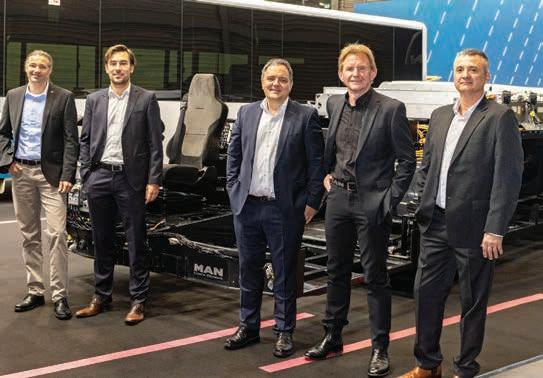
MAN’s battery technology benefits from its family ties to Volkswagen, as part of the German auto giant’s Traton commercial vehicle arm, using VW’s new Battery Development Centre in Nuremberg, so the battery technology is designed and approved by VW when it is used in Traton vehicles according to Fischer
“So what that means in terms of safety, performance and efficiency is that it’s well proven under the highest specification,” he said.
The maximum capacity of the roof top battery used in the e Lion is currently 480 kilowatts from a bank of six batteries, however it’s a modular system which allows for batteries to be removed to increase payload with the trade off being less range. This allows flexibility across various bus lengths with a shorter bus being able to run perhaps four batteries, a longer one potentially five and a long bus up to six batteries in the modular system. The batteries used are the latest water cooled NMC technology.
Its clear that MAN is serious about being a part of the battery electric bus revolution in Australia and the fact that it gave this new electric bus its world debut in Sydney is a pretty good measure of that seriousness.
As we race toward a zero emission future some are questioning how we can achieve this with our massive vehicle fleet when many of the materials needed to create the electric motors and batteries are both hard to extract from the earth and not particularly plentiful. One British start up reckons it is addressing this with a very different type of electric motor that might save the planet on two fronts. We sat down with one of its founders to find out all about Advanced Electric Machines.
British based specialist electric motor technology company, AEM, was spun off from Newcastle University and is on a mission to change. the global automotive and aviation industries away from using rare earth magnets in high tech zero emission power trains. It wants to switch to electric motors using the two most abundant metals on earth, aluminium and steel.
Instead of demolishing a mountain to source a meagre amount of rare earths for a growing demand in electric motors, the company, Advanced Electric Machines, believes economically, environmentally and on an efficiency basis its solution will be better on every level.
Coach & Bus met with Advanced Electric Machines’ (AEM) co founder Dr James Widmer for a briefing on the company when he was in Australia recently, where it came from where it is going and its ideas and philosophy on the electrification of the World’s transport operations.
Widmer pointed out that last year around 450,000 electric and hybrid vehicles were registered in the UK– and that represents a one in four ratio for all new cars and vans. While three new cars in every four rely totally on internal combustion engines, the numbers are swinging toward electric with a rapid year on shift.Meanwhile some experts predict there will be 20 million electrified vehicles on global roads by 2025.
AEM was a spin off from one of the epicentres of advanced electric vehicle development globally, Newcastle University. Newcastle found itself at the centre of electric vehicle power thanks to a century old legacy as a leader in the field of electric motor development. Of all areas of the UK, the North East of England is already benefitting the most from this global move towards electrification, thanks in part to the work at Newcastle Uni.
Aided by the introduction of the Nissan Leaf–arguably the world’s first massmarket EV–which entered production at the company’s Sunderland facility near Newcastle in 2010, the region now boasts burgeoning electric vehicle expertise.
At the same time that Nissan began production of the Leaf more than a decade ago, it also opened a local facility to produce the vehicle’s battery cells. This spawned smaller companies that both supplied and fed off Nissan’s plant–such as Sunderland-based Hyperdrive, which repackaged the plant’s battery cells into bespoke applications.
Newcastle University boasts the UK’s largest academic research group in electrical power, and so it was within this group, and as faculty at the university, that
Dr James Widmer and Dr Andy Stevens first pioneered the technology that underpins Advanced Electric Machines’ proposition. Drs Stevens and Widmer were a part of the electric motor research and development centre within the university when it was decided to spin it off in 2017 as a commercial entity.
“Back in 2010 it was hard to imagine that the electric vehicle industry would grow up in the way that it has, and that the North East would become such a relevant part of its future,” Dr Widmer said.
“As well as the gravitational pull of Nissan’s electrification program, this was also thanks to several academic and industry initiatives,” he added.
However while Widmer and AEM maybe based in England, the company is aggressively pursuing opportunities around the world and of course here in Australia with a variety of enterprises, including potentially local bus makers and commercial vehicle makers.
AEM is now recognised across the globe for its rare-earth free, high performance electric motors and powertrain systems. The journey to get to this point has not been simple, and we’re still only at the start of our overall mission to make the world’s EVs sustainable, but to get a picture of how everything began for us, let’s rewind to 2009.
Dr. Widmer, was an aerospace expert with BAE Systems, when he decide to go back to university to do a PhD and to aim to work in more sustainable technologies. It wasn’t an easy venture, given at that time electric vehicles were only just beginning to look like a feasible possibility. Andy Stevens was also working at the uni at the time and was an expert in rotating machinery and transmission technologies, with a long and successful stint in industry. Both Andy and James, were seeking to pursue their passion for developing sustainable technologies in an increasingly unsustainable world.
Back then James noticed that vehicle manufacturers were looking to employ permanent magnet motors as part of their electric vehicle solutions, and he realised that if these vehicles were to become the norm, the quantity of rare earth metals needed could become catastrophic for the environment.
James began to research and develop rare earth-free electric motors, supporting the first-generation development of OEM vehicles with JLR, Airbus and Cummins in the process. He became the director of the Advanced Propulsion Centre’s Electric Machines Spoke, a role in which he would meet , Mike Woodcock, who acknowledged another limitation of the use of permanent magnet electric motors – the lack of a route to recycling due to the copper and magnets they contain, meaning many would end up in landfill. This led the pair to question the possibility of removing the rare earths and the copper from the motor, and creating a fully recyclable solution. This would become the eventual mission statement of Advanced Electric Machines.
James and Andy’s work eventually led the pair to a realisation that they had developed a commercially viable product that had the chance to change the world.
So in March 2017 Advanced Electric Machines. was spun out of Newcastle University and into the commercial world.
“The problem with rare earths is that it’s an easy way to achieve a goal, but it’s very flawed in lots of ways. For a start when you put these magnets on the spinning part of the motor. it’s where it’s the most difficult to get heat out of, they’re great when they’re cold, but as they get hot performance drops off,” said James.
“So AEM’s motors do not use magnets at all instead using the combination of steel and aluminium because we can get really good performance out of it, we have a patented way of making coils that go around the motor, it makes it lighter, more efficient and gives the motor a longer life,” he said.
It’s some of those qualities that make Dr Widmer and AEM want to look to potential uses for its electric motors in heavy commercial operations including trucks and buses, particularly given the often high ambient temperature and demanding conditions that face operators here, with buses and coaches as well as heavy trucks up to and including road trains in outback areas.
“We see a lot of potential in Australia and we have a focus on this part of the world,” he said.
The company currently has a sales office in Bangkok, where is senior business development manager for the region, David Hunter is based.
”We’re in discussion with a lot of OEMs looking to buy this latest generation of electric motor technology, we’ve got another generation we’re looking at for quite a lot of the big global companies to see if they can use the technology and there doesn’t seem to be anybody else out there doing anything similar at the moment.”
AEM currently employs about 60 people. and currently has a production line which by the end of this year will be able to do 12,000 advanced electric motors a year. and is looking to move to a bigger facility of around 12,000 square metres at the back end of this year which will allow it to do much larger volumes and they’re also looking at plants in the US and potentially in Thailand.
Transport operators around Australia are focussing on reducing emissions from their bus and coach fleets, and while electric drivelines seem to be the topic de jour across the industry, Scania has some alternatives that may be the bridge to a low carbon emission future. We take a look at one major coach fleet which is resetting the emissions agenda with some innovative thinking.
Ask anyone in the transport industry about the challenge of coming up with a clean power solution for buses and coaches and the various hurdles are quickly rolled out.
There’s the cost, the availability of electric buses, the charging hardware, the availability of enough electricity and the list goes on.
There seems little doubt given the massive investments that the big bus makers are making in electric technology, that electricity is the future and at some point in the future it will dominate the market. However that may be some way off given the challenges we’ve already mentioned.
So in the meantime we still need to make efforts to be cleaner and more efficient potentially with internal combustion engines, to help bridge the gap between current diesel power and future electric drivelines. Scania reckons its biofuel-ready engines are the ideal solution to help get us through the transition.
Bio diesel has been reasonably big in Europe in recent times, but has not had a massive take up here in Australia, although Scania would like us to consider biodiesel as a cleaner, friendlier fuel source for diesel engines, allowing the technology to buy operators some breathing space ahead of a switch to electric power.
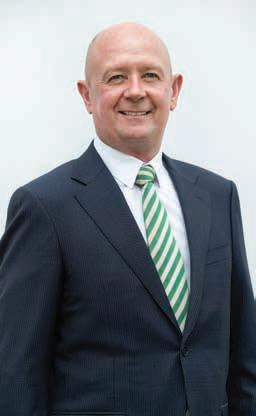
One major operator coach operator which is giving biodiesel a try, is Murrays Coaches.
Murrays, one of Australia’s longest established and best known coach operators, currently has six Scania buses in operation in Queensland with another five new Scanias on order. However importantly two of those original six are running on biodiesel.
The two bio diesel Scanias on the Murrays fleet have been switched over to run on B100 biodiesel provided by Ecotech Biodiesel based in Queensland with fuel transported by Refuelling Solutions. The two biodiesel Scanias are fitted with IRIZAR i6 bodies.
Ecotech Biodiesel, Just Biodiesel and Refuelling Solutions have partnered with Scania to provide a turn-key solution for bus and coach operators around Australia looking to vastly lower their emissions. That the fuel is produced in Australia from local sources, reduces our exposure to imported fuels and importantly, keeps investment local, is a further advantage.
Before you start wondering about where the biodiesel is sourced and produced, it comes from a combination of things including reclaimed cooking oils, yellow grease, plant based oil production and animal fats and other waste products.
The fuel is produced by transesterification, a process that converts fats and oils into biodiesel and glycerin, which is a by-product. Approximately 50 kilos of oil or fat are reacted with five kilos of a short-chain alcohol usually methanol in the presence of a catalyst, usually sodium hydroxide [NaOH] or potassium hydroxide [KOH]) to form 50 kilos of biodiesel and five kilos of glycerin or glycerol. Glycerin, which is a sugar, is commonly used in the manufacture of pharmaceuticals and cosmetics.
Justin Cannon, Murrays Coaches’ national fleet manager said the decision to switch to biofuels and to order five new
Scania-powered vehicles run on B100 was taking the fast route to cleaner emissions driven by the company’s desire to cut tailpipe emissions now.
“Our customers are asking us how to reduce their carbon footprint, and we have answers,” said Anthony King, Scania Australia’s sustainability solutions manager.
“Today there is additional impetus from our customers and their customers’ asking the same questions. Fortunately, we have been prepared for this and have established partnerships with relevant stakeholders so that we can deliver a readymade, here-and-now solution.
“All Scania bus engines that we have sold in recent times can run on B100 biodiesel. It just needs to be pumped into the vehicle’s tanks. The fuel must comply with the EN 14214 standard, of course. And if they need to refuel away from the depot, regular diesel can be used,” Anthony said.
“Murrays’ two IRIZAR i6 bodies on Scania 360 hp powertrains will be the first to use biofuel as part of our carbon emissions reduction program for customers in Australia, and we are delighted that they will take delivery of a further five new vehicles that will also run on this fuel,” Anthony said.
“Murrays has several customers who are multinationals and who are tasked with reducing carbon emissions” Justin said.
“We had already been studying options and the Scania biofuel solution made the most sense because the buses need no adaptation to run on B100, as they are adapted at the factory.
“For our operating environment, biofuels make the most sense today,” Justin said.
“Our trials showed that the Irizar i6s running on B100 delivered no noticeable difference in power or fuel efficiency, but we have the benefit of the significant emissions reduction.”
Murrays has ordered five new Scania powered buses with bodies assembled by BCI, all of which will run on B100 and will be working on a contract to transport workers to and from the Surat Basin.
“We have had the flexibility with Scania and BCI to select the components we know work well in our operating environment to build buses that we are confident will stand up to Australia’s harsh operating conditions,” Justin said.
“Corporately we are keen to reduce our CO2 emissions, so the success of this B100 program could have implications for future fleet purchases,” Justin said.
“We currently operate six Scaniapowered vehicles in our fleet in Queensland and will add the new five BCI bodied vehicles. They’ll be running from Brisbane to Toowoomba as well as on to Chinchilla, and also out to St George and Cunnamulla.
“We expect that they will cover about 20,000 km per month running out there, so they will be racking up km quickly for buses,” Justin said.
“We’re delighted that Murrays has partnered with Refuelling Solutions” said Simon Roycroft, future fuels manager at Refuelling Solutions.
“We’re already working on future investment plans to extend emission reductions” he said.
“It is very exciting to be working with leading organisations that are at the forefront of this once in a lifetime energy transition, delivering customer focused renewable low carbon liquid fuel solutions.” Murrays philosophy is that its company logo isn’t the only thing that’s green! The company claims to operate Australia’s largest modern fleet, using new coaches that it says have been created with sustainability in mind, using the latest emissions-reducing components. It says that even its older coaches have been upgraded to increase engine efficiency and fuel economy.
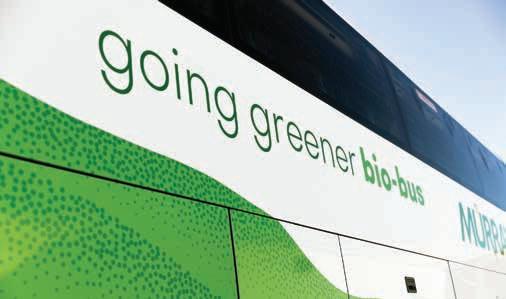
In recent times Murrays has purchased 70 new coaches, which is a significant investment in new technology and incorporating lower emission engines and sustainable engineering is a priority.
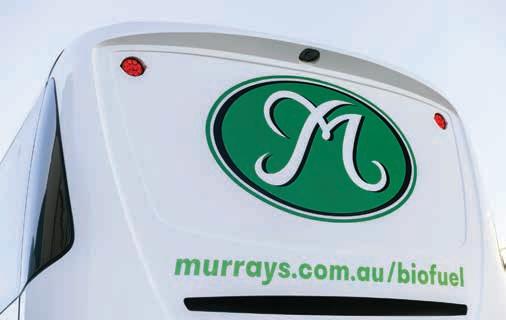
As well its depots have undergone significant improvement, including a reduction of risk in fuel storage with the safe removal of old fuel tanks, conservation or energy and reduction of waste outputs from the workshop area. The company has also done this through recycling waste oil, batteries, tyres, airconditioning and other vehicle parts.
Murrays has also looked at water conservation by installing large rainwater tanks in all its depot locations, together with recycling systems. It has also invested in both an automatic wash bay unit at its busiest depot in Sydney, along with portable bus washing systems at its other locations to further increase efficiencies. This effort has. It says has reduced water usage to almost nil.
Along with those environmental moves it has reviewed its use of fluid usage with coach wash, toilet chemicals and numerous other chemicals used in the cleaning and maintenance of coaches. The company says it now uses environmentally friendly products that are all compliant with local, sewer and stormwater regulations. In addition to this, it says the washing of vehicles takes places in bunded areas with all discharge regularly tested.
To further underline its environmental concerns Murrays has made adjustments over the years to its office environments and equipment. It says it has upgraded all equipment to modern, energy saving models, using up to 90 per cent less energy. In addition it reminds all staff to turn off electronics at the end of the day. Doing this saves energy in the office, and it says it is a small way to reduce its contribution to greenhouse gas emissions. Murrays says that whenever electronic equipment is updated, it is delivered to an electronics recycling company or distributed to our employees, reducing waste and harmful electronics in landfill. Its office policy is also to monitor areas where excessive lighting is used and many of the offices are now fitted with section light systems, ensuring overuse does not occur.
Meanwhile back with the switch to biodiesel, Anthony King says it is a major step toward creating a greener fleet now rather than waiting for full zero emission drivelines.
“We have very high confidence in the B100 biofuel,” Anthony King said.
“European operators have been running their Scania buses and coaches on biofuels for many years with excellent results and with up to 80 per cent CO2 emissions reduction well-to-wheel.
“Using B100 biodiesel gives you the unmatched Scania reliability you need today, with significantly lowered climate impact” he said.
It’s clear that while zero emission buses and coaches will be a part of our future, there are other ways to reduce the pressure on the environment now to build that bridge to a cleaner tomorrow.
Everywhere you look, there are more and more zero emission options emerging in the bus market and while there are a lot of battery electric buses arriving on the market, there have so far not been many hydrogen fuel cell buses available here, that was until now. We take a look at HDrive’s ambitious plans to bring a Hydrogen bus down under.