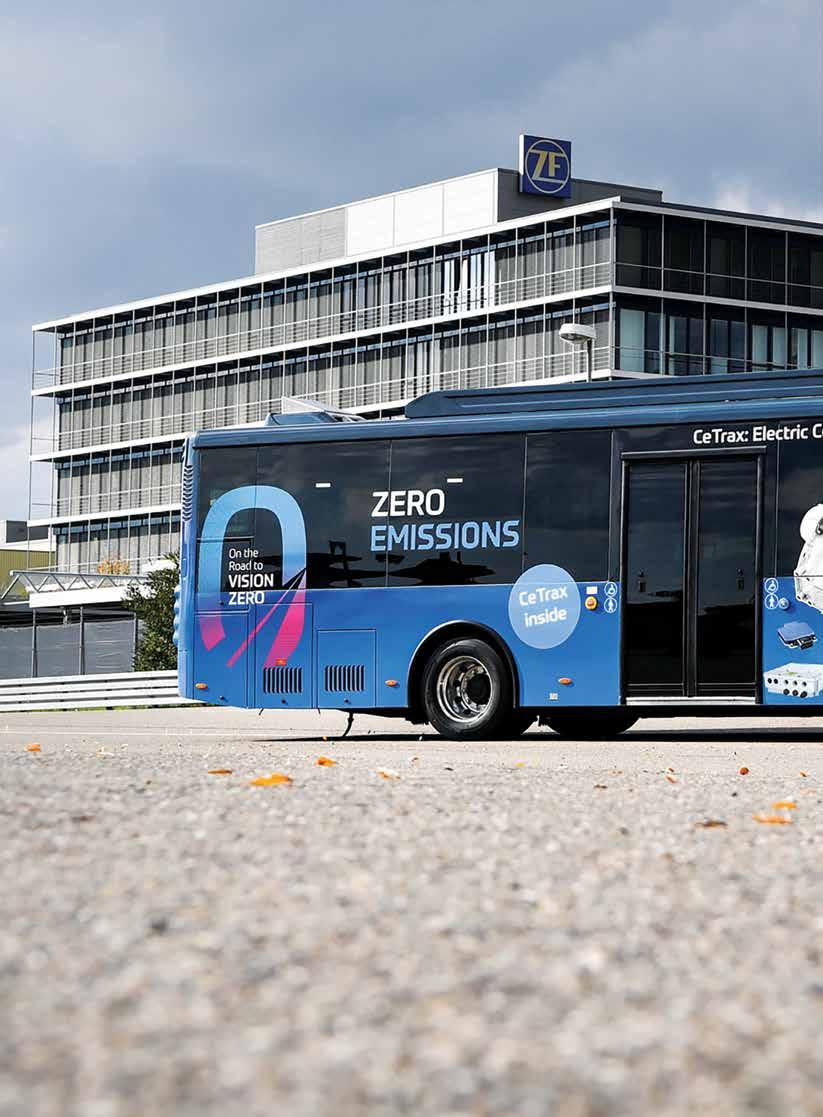
6 minute read
GEARING UP FOR AN ELECTRIC FUTURE
German based global automotive component maker, ZF is best known for its transmissions, using the expertise and engineering capabilities that were first established to create drive systems for Germany’s Zeppelin airships. With the writing on the wall for internal combustion engines, ZF is well advanced in a pivot to electric drive trains for commercial vehicles. We take a look at some interesting electric vehicle innovations from the German drive meister.
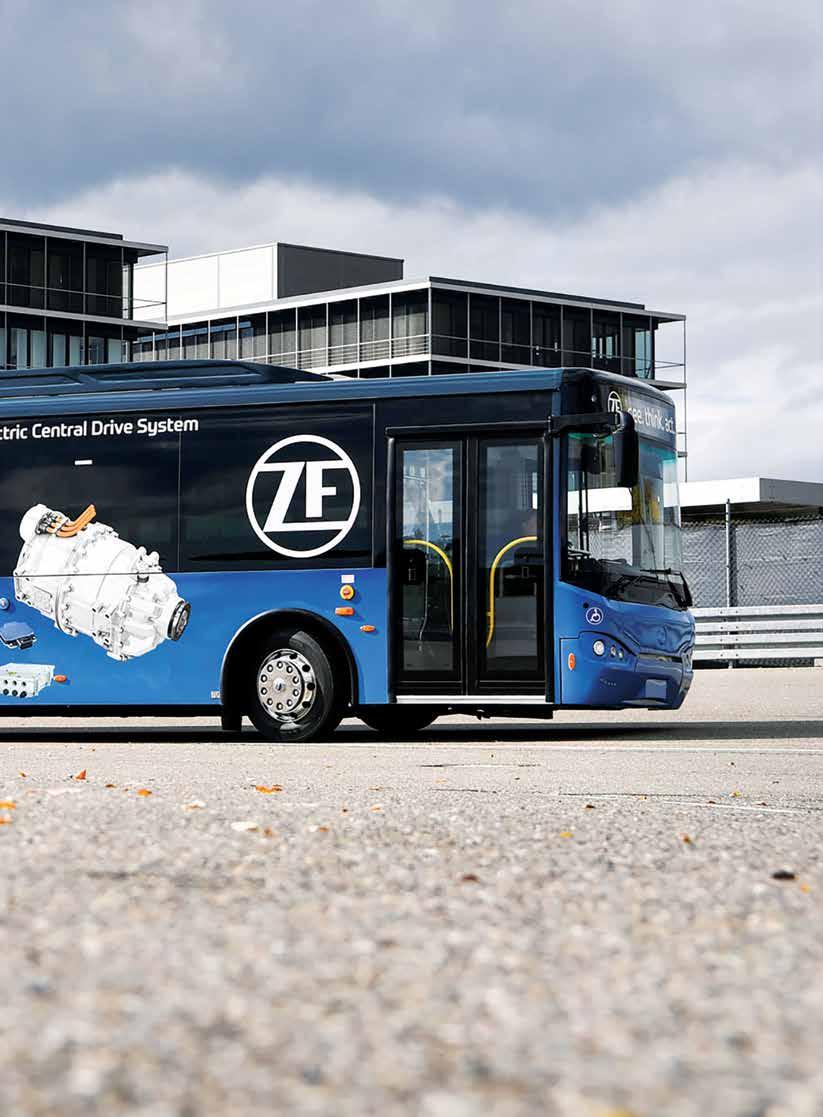
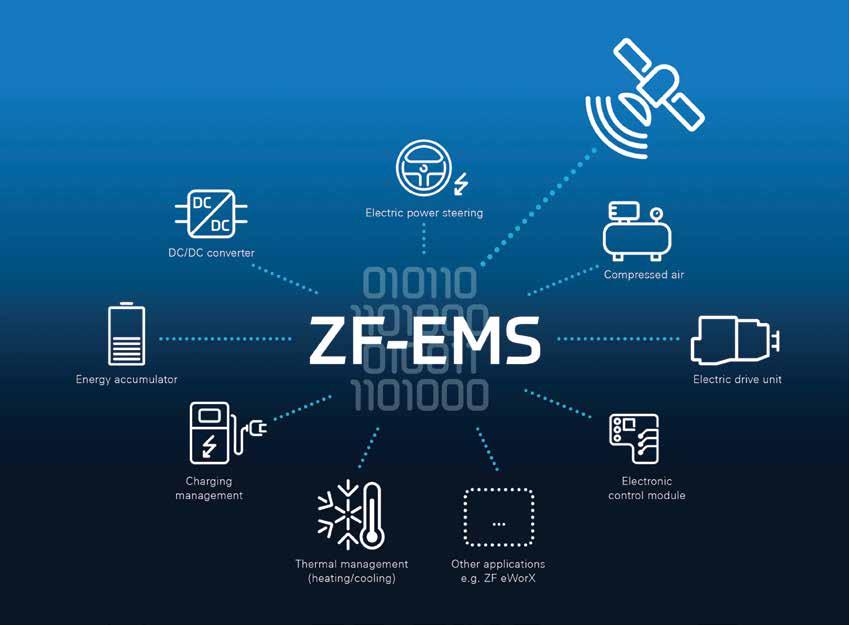
While many have the belief that the move to electric power trains in our buses and other vehicles is almost as simple as swapping out the internal combustion engine for a bank of batteries, some regulators and an electric motor, there is in fact a lot more involved. Clearly it is far more complex than that and requires a lot of computer control and management of the electric systems that enable a smooth and efficient operation of an electric vehicle.
Energy management systems or EMS are essential in electric vehicles and control the entire flow of energy in an electrified commercial vehicle.
Global automotive drive and component giant, ZF has developed a new EMS software solution to handle exactly what we have just described.
ZF’s new EMS software solution is designed to regulate the energy allocation for driveline and auxiliary systems in electric buses and trucks, delivering higher energy efficiency, longer battery life and easier system integration.
The ZF EMS is available as either an add on system or as an integrated part of volume production electric vehicle drivelines. With the new EMS software, ZF is providing another attractive proposal for the commercial vehicle market.
The ZF EMS takes a central role in the electric or electrified driveline, controlling all auxiliary units such as air compressors, steering pumps and thermal management as well as coordinating the energy requirements of the driveline.
This integrated approach can help make electrically driven commercial vehicles more efficient: Energy consumption per kilometre can be reduced, resulting in a corresponding increase in range as well as a potentially positive influence on the battery’s service life. In addition, there are further advantages for maintenance, diagnosis and reduced battery costs.
The modus operandi of the ZF EMS is that it coordinates the correct startup, availability and interaction of all components in the vehicle relevant for the flow of energy. This ranges from the battery’s state of charge to the electric drive and all auxiliary units such as the compressor, DC/DC converter and heating.
“Only such an integrative approach makes it possible to further increase the efficiency of electric vehicles,” explains Winfried Gründler, who is responsible for
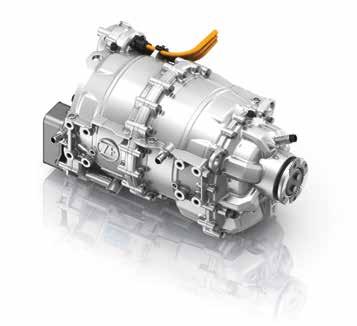
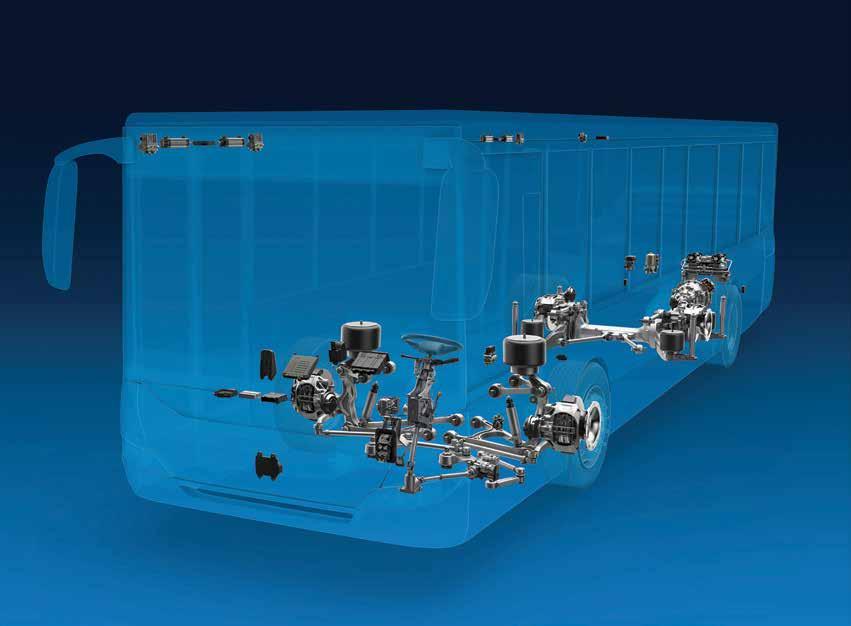
E-Mobility in ZF‘s Commercial Vehicle Technology Division.
“This illustrates the strategic importance that software expertise has for our Group strategy: Next Generation Mobility.” In this context, by utilising other recognised ZF functions such as ePreVision, we can make the system even more powerful.
Thanks to the predictive ePreVision function, the software takes the topographical profile of the route into account to coordinate the energy requirements of the consumables. For example, during predictable, long downhill runs, the compressor can operate on recuperated electrical energy. The EMS can also take over charging management at the depot where there are also advantages to predictive functions: If a vehicle is routed via a long downhill run in the first trip after leaving the depot, the batteries are not fully charged - as this recuperation phase has been predicted and taken into consideration.
Should the charging state of the battery decrease during a long journey, the EMS can lower the energy requirement priority of the auxiliary units to extend the range. Since the EMS continuously checks the functional status of all consumables, it also simplifies diagnostics.
“With our system, we are targeting bus and truck manufacturers unable to develop their own EMS or want to use them differently,” says Gründler. “Fleet owners such as transport authorities also benefit when only one partner assumes overall responsibility for the energy management of a vehicle.” Overall, ZF’s EMS supports a faster launch to market of highly efficient all-electric commercial vehicles.
Manufacturers also benefit from reduced functional integration efforts. ZF’s EMS uses the electric drive control unit - no additional control units are required - and ZF software controls the units via CAN bus interfaces. The interaction of the drive and energy management software is perfectly aligned.
The launch of its EMS software comes as ZF has also launched a new all-electric central drive system for conventional bus designs, which it calls CeTrax.
ZF says that CeTrax is paving the way for zero local emission driving, offering bus manufacturers high peak and continuous driving power, ideal for demanding innercity applications.
ZF claims the intelligent design of the system allows for installation in traditional high or low floor bus configurations with a centrally mounted motor, meaning the CeTrax can be seamlessly integrated into existing bus layouts without the requirement for extensive re-designs to the chassis, axles, differential and body.
Notably, it can be also be retrofitted into existing internal combustion enginepowered buses.
The high-speed electric motor is integrated with a planetary reduction gear stage as found on the ZF EcoLife transmission, with the design featuring integrated water and oil cooling systems.
Offering a maximum power output of 300kW and maximum torque of 4,500Nm,
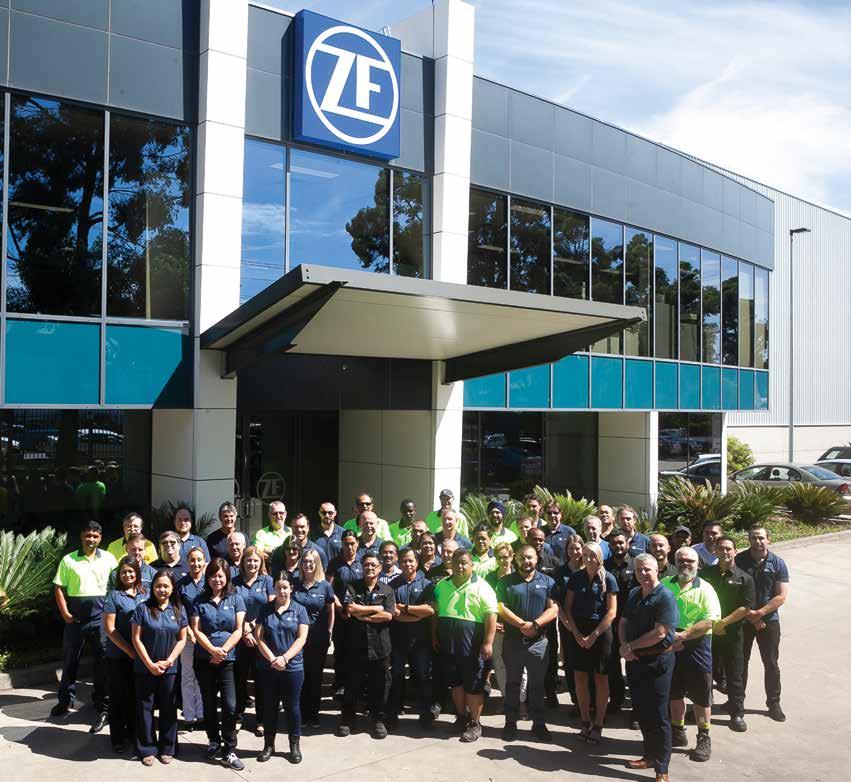
the credentials of CeTrax compare strongly with the competition, and it is capable of climbing 25 per cent gradients.
CeTrax offers multiple advantages to passengers, pedestrians, operators and communities adjoining bus routes, with pollutants such as CO2 and nitrogen oxide eliminated, while the motor is practically silent when in use.
Like other ZF electric drive systems, the CeTrax can be powered by battery, hydrogen fuel cell, supercapacitor, or mains power via pantograph for trolleybuses.
The system also offers impressive extended intervals between servicing.
The CeTrax system is supplied complete from ZF with an inverter and an electronic control unit.
Outside the CeTrax, ZF has also developed a comprehensive range of E-mobility options for the bus and coach market, including driveline, chassis, active safety and control electronics, as evidenced by the EMS software earlier in this story.
For instance, ZF’s AxTrax AVE Electric Portal Axle has found favour globally, thanks to its integrated wheel hub drive system perfect for low-floor installations. Adaptable for various configurations, including hybrid or fully electric drive, the AxTrax AVE can be installed in solo, articulated or double deck buses.
Also capable of being configured in 4WD, the AxTrax AVE allows for innovative passenger compartment layouts, with low floors able to feature from the front to the rear of the cabin.
ZF offers a full suite of electronic control units, ZF telematics and diagnostics, electric steering systems, and the CDC Continuous Damping Control system.
WABCO, a recent addition to the ZF family, also brings to the market its suite of advanced systems, assisting in the safety and efficiency of buses and coaches.
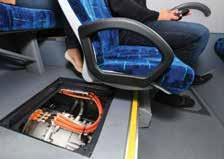