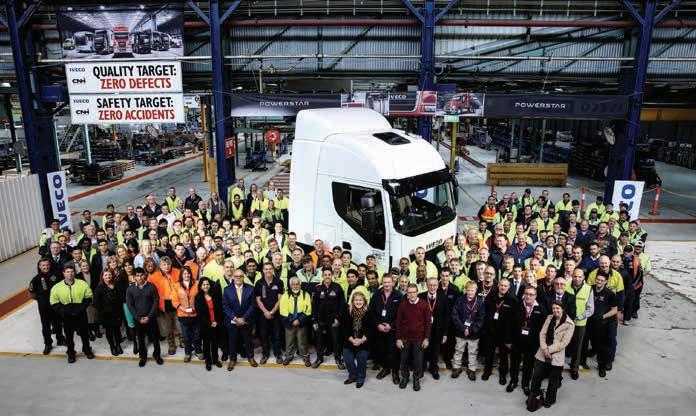
23 minute read
HIGHWAY 1
END OF THE LINE – IVECO TO SHUT HISTORIC LOCAL MANUFACTURING PLANT
AFTER 70 YEARS Iveco’s truck assembly plant at Dandenong will cease manufacturing trucks In June next year, as another Australian vehicle manufacturing operation is set to shut down. The shutdown of local Iveco truck production will leave only Volvo’s Brisbane operation and Paccar’s Bayswater factory in Melbourne’s East as the only remaining local vehicle assembly plants. The cessation of local Iveco manufacturing has long been rumoured with many industry pundits wondering how the Italian owned operation could be viable given the volume for its locally built product, particularly since the demise of the Australian developed and built versions of its ACCO model. However Iveco in its statement it said that as part of its ‘global transformation process’, it will develop what it is calling a Customisation and Innovation Centre (CIC) along with related changes that will ‘impact its Australian manufacturing arm’. Iveco currently employs approximately 120 workers in its manufacturing operation along with a team of around 25 engineers involved in local research and product development, the remainder of the 250-strong workforce are involved in sales, product support and marketing functions. It is understood that there will be job losses at the Dandenong facility, but Iveco is not saying how many will go, although it did say some staff will transfer into the new Customisation operation. The Dandenong manufacturing plant was opened in 1952 under the control of International Harvester manufacturing trucks and light utility vehicles for many years, when the IH brand was the market leader in trucks. Iveco purchased International’s Australian operation, including the Dandenong plant from the ailing American company in 1992. Many parts of the historic facility are now heritage listed and it is understood Iveco will continue
to operate from there with the CIC set to use part of the existing manufacturing plant. The factory originally covered around 34000 square metres and has produced more than 230,000 vehicles since 1952, and while it pumped out 2000 new trucks in its first year of operation in recent times the plant has built well less than half that volume each year. TTA sought comment from the remaining local truck makers. A Volvo Group spokesman told us that while it does not comment on opponents, the company has been actively expanding its local component supplier chain in recent times and has invested heavily in its Wacol plant to expand production with a focus on Queensland based suppliers. Iveco said it would move to fully import its heavy duty range from its Spanish advanced manufacturing facility in Madrid and it anticipates this will take place from the end of June 2022. Iveco already fully imports its light, medium and selected heavy duty trucks as well as its Daily based minibus and its off-road models to Australia. The company said the decision to fully import its heavy duty range will allow it ‘to more closely align model year introduction timings with that of its parent company in Europe’. It cited as an example, the fact that it will now be launching the new S-WAY model in Australia according to the global launch plan. Iveco said its new S-WAY model for Australian and New Zealand will have ‘undergone thousands of hours and kilometres of validation testing on local roads and highways and had input and development from Iveco’s local engineers and specifically selected customer partners, ensuring it is designed and then tested to meet the needs of the local ANZ market’. The company also said this will include a further iteration of its imported dual control ACCO model for the local waste market. In what is a huge announcement for the company Iveco Australia and New Zealand managing director, Michael May, said that by focusing on the Customisation and Innovation Centre, the company would ‘strengthen one of its key selling points in the Australian and NZ market’. “Historically, our most unique value proposition has been our ability to customise and specialise vehicles for our market, leveraging the expertise of our local engineering team and the local facility,” he said. “By further enhancing this service, we believe there is considerable potential to provide additional value to existing and prospective customers, while growing the CIC’s capacity and scope of work.” Michael May said the decision to move to local customisation of fully imported vehicles was a natural progression of Iveco’s ANZ transformation. “Given our brand’s long history of manufacturing in Australia, this next step towards customisation strengthens our ability to remain agile and responsive to demanding regional requirements,” he said. “This move will also ensure that we are in a position to offer the market the very latest in Iveco performance, comfort and safety innovation, in the most timely fashion, and at the same time, capitalise on our design and validation engineering expertise and customisation capabilities.” Iveco said that over the coming months it will continue to engage with its employees who may be impacted by the announcement, and will provide appropriate support to the involved workforce. The company said that the CIC will be a business unit that will ‘further leverage Iveco’s local engineering and manufacturing expertise, transforming the company’s focus towards the customisation and innovation of its vehicles for local markets’. It said that promoting innovation will be a key aspect of the CIC, allowing it to work more closely with Europe and local partners to ‘explore areas such as alternative propulsion solutions, digitisation, connectivity and autonomous driving’. It added that the CIC is being developed to better assist its customers and body-builders – particularly those with complex body types – to achieve a more streamlined design and body fitment process for their vehicles. HYUNDAI’S INNOVATIVE hydrogen fuel cell electric XCIENT trucks will be on Kiwi roads as soon as next year, following a bold move by local NZ importer Hyundai NZ. The first of Hyundai New Zealand’s five new fuel cell electric XCIENT trucks arrived in Auckland in November ahead of a local hydrogen demonstration program in 2022. Hyundai NZ will convert the Swiss specification XCIENT 6x2 to righthand-drive and have a body locally fitted ahead of field demonstrations in the second quarter of 2022. New Zealand is just the third country to have access to these trucks, following Switzerland and South Korea. Hyundai NZ has initially taken the Swiss specification to get the programme underway early. “As a Kiwi owned company, we are big believers of implementing alternative fuel technology here in New Zealand,” says Andy Sinclair, Hyundai NZ general manager. “We have championed this through the introduction of NZ’s first hydrogen-powered SUV, NEXO, in 2019. Now with the XCIENT FCEV, we have an opportunity to help fast track the large-scale adoption of alternative green fuels in the New Zealand road freight sector.” The Hyundai XCIENT Fuel Cell is the world’s first mass-produced heavy-duty truck powered by hydrogen. Hyundai NZ will work with local partners in the freight sector to determine where the trucks will operate regionally. This demonstration will give insights into how the trucks fit into timetables, capacity, maintenance schedules, refuelling, drivability and user-training specific to New Zealand. The XCIENT FCEV has a Siemens supplied electric motor which receives power from two 90kw fuel cells and a 72kWh battery pack. (72kWh). The battery is continuously charged from the fuel cell. The XCIENT FCEV has a clean and quiet motor and the only emission from the process is water. Compared to an equivalent diesel truck, Hyundai estimates each XCIENT FCEV will save 50 tonnes (based on 80,000km per year) of CO2 emissions per year.
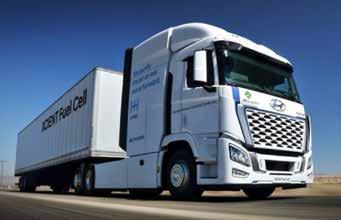
RETURN TO SENDERS -AUSSIE POST FIRST TO TAKE UP FUSO eCANTERS
IT’S OFFICIAL, Fuso’s recently launched eCanter electric truck has been embraced by arguably Australia’s largest truck fleet, Australia Post, with the giant operation placing an initial order for 20 of the battery electric light trucks. As we have predicted the eCanter will, in the initial stages be taken up in Australia, by the big image conscious fleets, desiring to be seen as taking a stance against emissions, and who have the resources to pay a premium and to install charging equipment. That being the case, it was no surprise when Daimler Trucks announced that Australia Post would be the first customer for its eCanter in Australia. The government owned postal service is the first local fleet to sign up for the eCanter, initially agreeing to take on 20 of the electric trucks, continuing the electrification of its fleet, with the first arrivals hitting Australian roads in October. Australia Post is the largest operator of electric vehicles in Australia, with a fleet of more than 3000 of them currently in use, most of which are the new electric trikes, being adopted for post delivery services, replacing the Honda Postie bikes it’s used for decades. “With the significant growth in parcel volumes, more vehicles are required in our network,” said James Dixon, general manager, networks for Australia Post. “It makes good sense to add electric vehicles as part of this requirement. Not only will these eCanters fit our needs in this delivery category, but they will also contribute to our science based target to reduce emissions by 15 per cent by 2025 from a FY19 baseline,” James Dixon added. According to the media release from Daimler, the eCanters will operate across the Australia Post and StarTrack businesses in major capitals in two body configurations and will be supported by the Daimler Trucks network. “Since working with Daimler Trucks on the pre-production eCanter, we have been keen to have the truck in our fleet. Daimler Trucks is a good choice for Australia Post in the fleet space with a large network and focus on safety,” concluded James Dixon. The eCanter is equipped with advanced pedestrian-sensing emergency braking technology, a collision mitigation system, lane departure warning and Electronic Stability Program for optimum safety. Daimler Truck and Bus president and CEO, Daniel Whitehead, said Australia Post is the perfect first Australian customer for the eCanter. “Daimler is thrilled to partner with such an iconic brand as Australia Post on a journey towards carbon neutral freight transportation in Australia,” Whitehead said. “The Fuso eCanter’s active safety features, zero local emissions and near-silent operation make it perfect for parcel and letter deliveries in the city and the suburbs,” he added. Fuso Truck and Bus Australia Director, Alex Müller, applauded Australia Post for its electric mobility leadership. “Australia Post is setting a great example with deployment of the eCanter, demonstrating that you can get the job done in a sustainable way,” Müller said. “The eCanter is a vital proposition for any company that is serious about reducing emissions,” Müller added. The eCanter uses six liquid-cooled lithium ion batteries mounted in its frame to store 82.8kW/h of electricity and feed a permanent magnet synchronous motor. Power output is rated at 135kW and 390Nm of torque can be delivered the moment the accelerator pedal is pressed. The eCanter, which has a Gross Vehicle Mass of 7.5 tonnes, became the world’s first small series electric production truck in 2017. It has been the subject of a rigorous testing regime around the world, including a six-month Australian test running with a maximum load, in addition to real world driving in overseas markets.
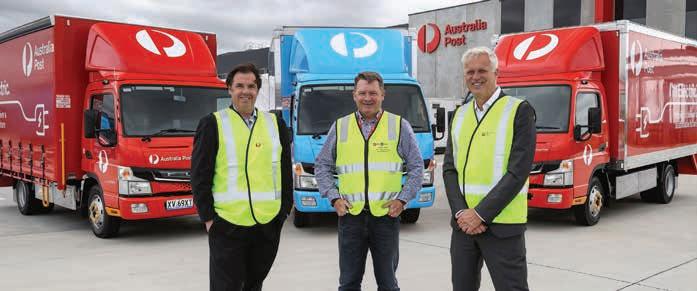
CHASING RUBBISH – NEW LOCAL BUILT FRONT LOADER CF TO TARGET WASTE MARKET
THE VOID that has been left in the waste collection market since Iveco scrapped its locally designed and developed Acco in favour of a heavier, adapted imported model, has seen a number of truck makers clamouring to grab a piece of the action. The latest is Paccar which says it has utilised its five decades of local engineering expertise with its Kenworth range and applied that resource to its DAF Euro 6 range, to produce an optimised variant, specifically for the waste industry. Paccar said that after almost two years of planning and design work by the local engineering team, the new lightweight DAF CF 340 FAD, is entering service to demonstrate its attributes with some of Australia’s prominent waste companies. “With a strong focus on producing a low tare-weight solution to optimise payloads, we’re confident we’ve got a fantastic transport solution for waste management,” said Felipe Rubio, DAF Trucks Australia general manager. The release of the DAF Euro 6 model range in 2020 provided significant improvements in the areas of performance, fuel efficiency and driver safety over the Euro 5 model range, which had successfully seen the DAF CF75 FAD establish a strong presence in front loader and hook lift applications in the waste industry. Building on these attributes, Paccar Australia’s engineering department worked with DAF’s engineers in the Netherlands to produce a local version of the DAF CF 8x4 cab chassis that was both lighter and more manoeuvrable specifically for the waste sector. The primary focus for Paccar Australia’s engineering department was the rear end. Kenworth Airglide suspension and locally sourced Meritor tandem axles with disc brakes were fitted to the body builder-friendly chassis and provided significant weight saving for this excellent new product,” said Rubio. Adaptation and validation of this hardware set, including software integration for DAF’s latest generation of safety systems, was completed with assistance from Paccar Australia’s local supply chain network. All parties involved focused on producing a product to achieve industry-leading tare weight to maximise operator payload, a huge consideration for the waste transport industry. “That’s what sets us apart, being able to use Paccar Australia’s unique engineering and manufacturing capability to produce quality products specifically designed for the Australian market,” Rubio said. “The result is exceptional, the team at Paccar Australia have delivered a Euro 6 emissions compliant product with all the latest safety technology; offering exceptional performance and fuel efficiency, manoeuvrability, driveability and driver comfort with exceptional payload capability for the waste industry. This is something we are extremely proud of,” he added. DAF’s modern and powerful Paccar MX-11 Euro 6 engine has been mated to an Allison 3200 Series 6-Speed automatic transmission to provide the best balance between performance, efficiency and durability. Rated at 340 horsepower (251 kW) and providing a maximum torque of 1500 Nm, the engine and transmission combination provides maximum torque and driveability at low engine speeds with higher loads. To help drivers and fleets maximise the fuel efficiency of this new engine, a driver rating system is another key feature. The truck evaluates the driver behaviours and provides live driver performance feedback, which can be used to significantly improve fuel efficiency and reduce vehicle maintenance costs. Fleets can further reduce fuel and maintenance costs, as well as track vehicles and vehicle performance, with Paccar Connect. Driver and fleet information is made available via live tracking on desktop computer or mobile devices through easy-to-read and fully customisable dashboards and detailed reports that provide convenient and timely insights. Paccar Connect can also share vehicle data with third-party fleet management systems, seamlessly integrating Paccar vehicles into businesses. This truck will be the latest DAF product to be built at Paccar’s Bayswater production plan, alongside existing CF MX-11 and MX-13 powered prime mover models, and Kenworth’s entire Australian model range. In 2021 Paccar celebrated 50 years of manufacturing Kenworth trucks in Australia, at the same time producing the 70,000th truck at the Bayswater facility. “It is both exciting and important that the new light tare-weight model be built in Australia, because if nothing else, the past 18 months of an economy dealing with COVID-19 has shown that Australian manufacturing is not only vibrant, but essential in creating jobs for Australian families,” Fellipe said. “We hope that Australian operators continue to buy local products and support local suppliers and workers.” Like all DAF trucks, buyers of this new light tare-weight model can take confidence that it is fully supported by Paccar Australia’s extensive sales, parts and service dealer network located throughout Australia. The DAF CF 340 FAD is positioned to be well received by the waste transport industry, either in front loader, rear loader or hook lift applications, and is now on sale at DAF dealers.
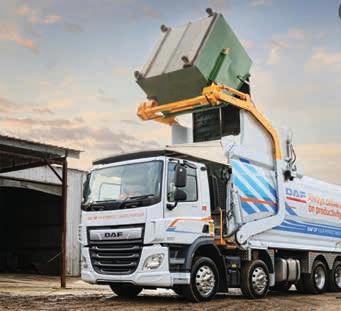
New Dainler Truck Financial Services CEO Greg Cubitt, with Daimler Trucks Australia boss Daniel Whitehead

INDEPENDENCE DAY – DAIMLER TRUCK NOW A SEPARATE CORPORATION
DAIMLER TRUCK officially became an independent company on 1st December, forming a separate operation from its former parent company Mercedes-Benz passenger car division. The truck operation is now an independent global commercial vehicle manufacturer which it says will allow for a sharper focus on commercial vehicle customers. Daimler Truck says that the global changes will enable its business to continue delivering class-leading Mercedes-Benz, Freightliner and Fuso trucks and buses into the future as it moves towards zero emissions. The move has also seen Daimler Truck and Bus Australia Pacific grow its workforce as it takes on previously shared internal services, but says that the big news for customers is the creation of a new dedicated truck and bus finance company; Daimler Truck Financial Services. Previously, Daimler’s commercial vehicle finance offerings were provided by Mercedes-Benz Financial Services, the same finance company that delivers finance for MercedesBenz passenger vehicle customers. From now on, Daimler Truck Financial Services will be wholly dedicated to truck and bus customers, through the established Daimler Truck and Bus dealer network. Experienced commercial vehicle finance executive, Craig Cubitt, has been appointed chief executive officer of the new organisation that will be based at Daimler Truck and Bus headquarters in Mulgrave, Victoria. Daimler Truck and Bus Australia Pacific president and CEO, Daniel Whitehead, said the independence of Daimler Truck is a big plus. “We are excited that Daimler Truck is now a standalone global entity because we know that independence will make us more nimble and enable us to continue making the investments needed to develop the best trucks, buses and associated services of the future,” he said. The creation of a dedicated financial services company for Daimler Truck and Bus customers is also a welcome development, says Whitehead. “Running a fleet of trucks or buses is very different to operating a passenger vehicle and the finance requirements they need for their business are also unique. We are excited that Craig and his entire team will now be able to focus solely on our truck and bus customers and provide them with the best and most innovative commercial vehicle financial products and services,” he said. Craig Cubitt said the Daimler Truck Financial Services team, which has extensive industry experience in Australia, is perfectly positioned to deliver the best products and services to Daimler Truck and Bus customers. “We aim to be a truly customerfocused organisation that puts our truck and bus customers at the centre of everything we do,” Cubitt said. “Our new structure as a stand-alone finance company means we can serve our truck customers and dealers better than ever before.” Daimler Truck Financial Services says that it offers a wide range of financial solutions, including business asset loans, hire-purchase, and lease products, as well as some unique innovative solutions that are not available anywhere else in the industry. The company also says it will offer two unique and exclusive products including something it calls, Fast Track Finance, which offers a fast streamlined approval process, as well as the popular Daimler Guaranteed Buy Back program, which provides customers a guaranteed future value on their Daimler truck right from the beginning of their contract. The company says that the Daimler Guaranteed Buy back is unlike traditional loans, as it also offers several options at the end of contract including the option to hand back the truck or alternatively, the customer can choose to retain the truck or trade it in for a new one.
ISUZU TECHS SELECTED TO REPRESENT AUSTRALIA IN VIRTUAL WORLD TECH COMP
Isuzu has wrapped up its annual National Technical Skills Competition with 47 of its best automotive technicians battling it out for the chance to represent their Isuzu dealership and Australia at Isuzu Motor’s I-1 Grand Prix. Isuzu says the top two technicians from the NTSC will form Australia’s I-1 GP team, and they are now looking ahead to the challenge of an international I-1 Grand Prix e-Competition—which has been refreshed in a new virtual format due to COVID-19. The I-1 GP finals have traditionally been held at Isuzu Motors head office in Japan, with each country’s qualifying team flying in with a coach to compete in both ‘individual’ and ‘team’ finals. The company says that in essence, the competition remains the same, with individual and team events taking place. However, this year each technician will be competing virtually on home soil, with Australia’s team set to undertake the tough e-Competition in Brisbane. The company said that the NTSC this year challenged technicians with a series of Interactive Virtual Online Diagnostic tests with results tallied up against a 60-minute written exam and each tech’s personal scores from their Isuzu Technicians Guild Questionnaires held earlier in 2021. In Australia, the top two technicians were picked from a competitive field, with only a seven per cent difference in combined scores separating first and tenth place. Harry Minnis, who only started his apprenticeship with Brisbane Isuzu Eagle Farm in 2016, fresh from high school, was this year’s Australian NTSC winner, scoring 100 per cent during the second virtual failure diagnosis test. The other member of the top two Jason Peterkin, began his apprenticeship in 1995, working for his father in Darwin, before going on to complete a dual trade qualification specialising in diagnostics for both electrical and mechanical faults. He joined Tony Ireland Isuzu in 2012 as the leading hand at its Townsville workshop. Isuzu says that with a combination of smarts and on-the-job experience, Jason is recognised as one of Australia’s best technicians when it comes to Isuzu’s 4JJ1 engine series. This isn’t his first time for Peterkin in the I-1 GP circuit—he’s competed several times in the NTSC and took home an honourable team fourth place in the 2018 I-1 GP in Japan. Jason scored the highest mark in this year’s NTSC Technical Knowledge exam, earning him his spot on the 2021 Australian team. “The NTSC tests are definitely getting harder each year, and this year’s was daunting at first being fully virtual, but it’s come out to be a well-polished competition. “The level of experience and competition is always very, very high… but I’m quietly confident of our chances this year,” Jason said. “Going over to Japan in 2018 was an experience of a lifetime, being in the testing centre there and having all of Isuzu Motors watching you compete… I’m looking forward to getting out there again sometime in the future.” Isuzu Australia Limited national service technical manager, Brenton Cook, congratulated all entrants and the type two technicians for their achievements so far. “As always, it’s fantastic to see the level of talent that comes out of events like this and the broader I-1 GP event program. We couldn’t be prouder of the results achieved this year and the technician’s commitment to being the best they can be. “A hearty congratulations to all participating technicians, but to our Top two technicians Harry and Jason, well done and good luck in the final round,” said Cook.
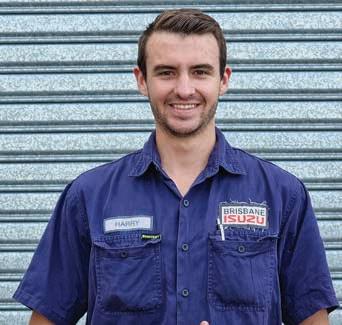


ALLISON has announced a groundbreaking deal with one of the leading truck competitors in the grueling Dakar Rally, to help develop electrically-powered trucks for the Dakar rally and other rally events. Allison announced the three-year partnership agreement with Team de Rooy, a multiple-winner of the truck division of the world-famous Dakar Rally. Testing is scheduled to start on an electrified truck with a conventional Allison transmission in early 2022, ahead of the vehicle’s competition debut at the Dakar Rally in January 2023. This ambitious project was affirmed at Team de Rooy’s premises near Eindhoven, in the Netherlands. Gerard de Rooy, the managing director of De Rooy Transport and owner of the truck rally team, has won Dakar, as both team owner and driver, in 2012 and 2016. “Dakar and other rally raids are really tough on mechanical components, especially the suspension, axles and gearbox. On hard surfaces, severe vibrations go through the whole driveline and consequently through the entire rally truck, hour after hour, causing damage. On loose sand traditional clutch-operated transmissions limit traction at low speeds. That’s why our team switched in 2018 to an Allison fully automatic transmission. Knowing how effective and robust Allison’s transmissions are, it is great to have the company’s support with our plans to go electric,” said de Rooy. In the most recent running of the Dakar Rally vehicles equipped with Allison transmissions dominated the top ten in the truck division. Team de Rooy’s new Iveco electrified truck will use Allison’s 4000 Series fully automatic transmission with retarder. This is suitable, like all Allison Automatics, for all medium- and heavy-duty commercial engines and all fuel types and electric motors. Allison’s 4000 Series is also being integrated with an electric motor in Hyundai’s XCIENT hydrogen-electric heavy-duty truck, which went into production in 2020. De Rooy believes, the Allison torque converter, which multiplies torque at launch, will enable its electric rally raid truck to utilise a smaller and less powerful drive motor to optimize range and efficiency, and to perform well when powering up sand dunes. It says that another advantage is the dampening effect of the fluid coupling in the converter, which helps protect the truck’s drive motor from shock loading associated with torsional forces in the driveline. A further benefit is made possible by self-learning algorithms in Allison Automatics, which continually optimise engine speed and torque level. This helps maximize efficiency and minimize energy use in electric motors. While the new electric truck is under development, Team de Rooy will enter the 2022 Dakar Rally with dieselpowered Iveco trucks equipped with Allison fully automatic transmissions, supplied and supported by Drive Line Systems (DLS), the official Allison Authorized distributor for the Netherlands, Belgium, Luxemburg, Iceland and Turkey. Team De Rooy will also drive the Classic DAF trucks “dubbelkop” (translated: Twin Head), driven by Jan De Rooy, Gerard’s father. This Classic truck is also equipped with Allison fully automatic transmissions. The “dubbelkop” has two complete power packs equipped with two Allison transmissions on board. As well as being the largest global manufacturer of medium- and heavyduty fully automatic transmissions for commercial and defense vehicles, Allison is a leading designer and manufacturer of conventional, electric hybrid and fully electric vehicle propulsion solutions. Allison recently expanded its presence in the EV sector by bringing the eGen PowerTM series of electric axles to the truck and bus market. These e-Axles are fully integrated electric powertrains that replace conventional driveline components including axles, engine, transmission and propshaft in medium- and heavy-duty trucks. The e-Axles can fit into existing chassis configurations with minimal modifications and this compact confguration will allow for extra space for battery packs in the truck. “Pioneering and innovation have been in Allison’s DNA since its foundation in 1915 and the electrification era is no different. On and off-road, and even in the sand dunes, we are helping our customers transition from solutions which are available now – combining our conventional transmissions with an electric motor, for example – to designing fully integrated electric axles, providing the same maximum levels of reliability, performance and driveability,” said Edgar Lips, Senior OEM Account Manager, Allison Transmission.