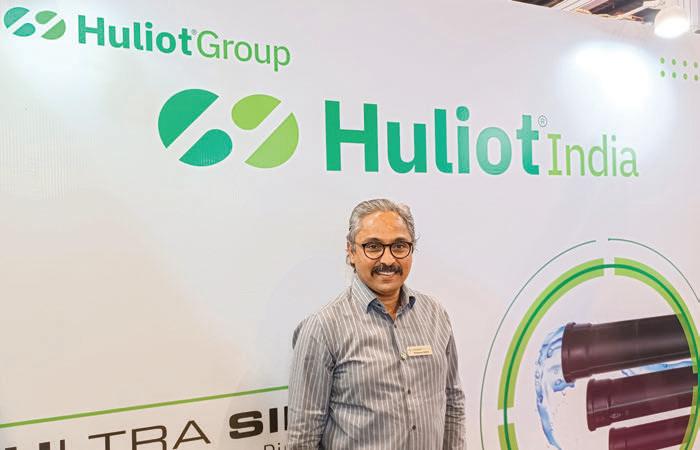
4 minute read
Huliot India: PP Plastic Pipes & Fittings to Overcome PVC and CPVC-Induced Hazards
The global population is aiming to become as plastic-independent as possible, however, we need to accept the fact that plastic cannot be eliminated from our lives. Plastic was a wonderful discovery and led to many revolutionary products and applications, such as plastic pipes and fittings for drainage systems. Yet again, the hazardous effects of PVC and CPVC material cannot be ignored. Huliot India, a unit of Huliot Group, is among the pioneers of supplying safer plastic-based alternatives in the Indian market, as it uses PP to manufacture its products. In a conversation with Tube & Pipe India, Mr. Prasanna Shetty, Deputy CEO of Huliot India, shares how PP drainage products can solve the collective market concern. He also sheds light on the company's journey, new developments, advanced products, and future plans.
Tube & Pipe India: Please share with us Huliot India's journey, overview, and crucial milestones.
Mr. Prasanna Shetty: Huliot Group was first established in Israel in 1947 and was the first company in the country to manufacture PP plastic products. The company expanded its operations to set up Huliot India - Huliot Pipes & Fittings Private Limited in 2014. The establishment was among the first companies to introduce polypropylene (PP) pipe manufacturing and its domestic applications in India, while also contributing to the Government of India's Make in India programme. Since 2014, Huliot India has worked to advocate the use of PP drainage systems in residential and commercial buildings, against PVC and CPVC applications. We have also developed advanced products like STP, HT Pro, and Ultra Silent (acoustic and non-acoustic) drainage system applications. Our company is wholly dedicated to developing reliable and safe domestic drainage systems, and all our products have applications in water supply, drainage, sewage, and gray water recycling systems.
TPI: Please tell us about your manufacturing set-up, capabilities, and capacities.
PS: Our manufacturing plant is in Vadodara, Gujarat, where we have 2
German-made extrusion lines. The lines have a production capacity of 400 kilograms per hour, which exceeds the average market capacity by a huge margin. As of 2023, our plant supplies 40-45 percent of domestic market demand, and we import at least 55 percent of our products from Israeli manufacturing units. We plan to expand our manufacturing capacity to fulfill 100 percent of domestic demand from our Vadodara facility by 2025.
Apart from manufacturing set-up, we have an in-house design and engineering support team. The team is responsible for designing and building entire drainage or supply systems for large-scale projects. They provide turnkey solutions for underdevelopment or planned infrastructure projects, including designing BOQs and checking installations.
TPI: Can you elaborate on your company's product portfolio for us? What is your USP?
PS: We make acoustic and nonacoustic PP pipes, which are triplelayered and 100 percent recyclable. These pipes have a temperature resistance range of -20 to 95 degrees, and chemical resistance of ph2 to ph12. Hence, our products can be used for both hot and cold flow discharges. We offer pipes with diameters ranging from 32 mm to 160 mm. We also manufacture accessories and fittings, and all our products are push-fit insertion enabled, providing a leakproof flow and discharge.

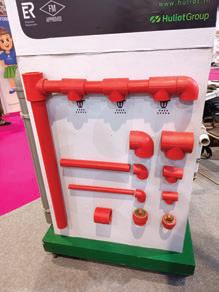
Our products are wholly recyclable and have a life cycle of 50 years, which is in alignment with the majority of buildings or structures' life cycles. All our products are cutto-length according to clients' requirements to avoid material wastage.
Our in-house engineering and technical support provide system design and engineering services. They design the whole drainage system and manufacture pipes and fittings accordingly, and we provide a 10-year guarantee to clients who use 100 percent of our solutions and products for their buildings or project.
Our products are ClearBlack STP, which is an IoT-enabled STP plant working on MBR technology to eliminate the need for 24x7 manual supervision. The operators can easily supervise and fix the product by identifying the problem area on the interface.
TPI: Please tell us about your market footprint and major clientele.
PS: Our product line wholly caters to water flow discharge, which along with our advanced technical and structural applications help us serve a vast range of clients. In India, we have been a supplier to big-time luxury and premium real-estate projects, hospitals, hotels, and newly emerging industries and sectors. Huliot India has also been part of various government-backed projects, like AIIMS Bhatinda, AIIMS Kanpur, IIT Hyderabad, car parks, disaster management buildings, etc. We have a wide network of distributors and sales channels, which helps us enhance our market presence in the domestic market and serve endusers.
TPI: Are there any recent developments that Huliot India has invested in?
PS: We have developed the Red Fire system. It is manufactured with state-of-the-art three-layer polypropylene (PP-R+FG) and is used for hoses and sprinklers in medium-risk areas. The welding is done by thermofusion method, where the pipe and fittings are molecularly fused forming a homogenous connection, thus producing a highly reliable single piece.
We use crimping joint technology for our water supply range of multicomposite and SS 316 L, making it 100 percent leakproof. Our IoTempowered manufacturing capabilities, which can use solar power to operate, help us serve bigscale industries where the drainage systems are widespread and require focused and expedited attention.
TPI: Please share your observations on the plastic tubes and pipes market.
PS: There was a lack of awareness in the pre Covid-19 years, as people were less inclined to learn about the possible hazards of using PVC and CPVC pipes. Post-pandemic, big industries to end users, all are more interested in knowing about the products that are being used, and it is easier for us to explain how PP pipes are better. It is now comparatively common knowledge that PP is a green product, as it does not exhume toxic fumes and gases while burning and it can be wholly recycled.
Furthermore, there used to be a pricing concern as well. It is true that our product will cost more on meters by meters scale, however, its overall cost for the whole project will be 5-7 percent lesser than PVC or CPVC systems.
TPI: What are Huliot India's plans for the future?
PS: The increase in general awareness has led to an increase in demand for our products. Hence, we are looking forward to expanding our current distribution and sales channels. Moreover, we also expect to add a third extrusion line in comping September to self-satisfy the demand in the Indian market.
Huliot India's future plans are in line with our parent group's core thinking, to manufacture sustainable products through sustainable processes. We plan to invest in R&D, development of innovative technology, and solutions with futuristic applications. As urban areas focus on transforming into Smart Cities, we intend to integrate practices and solutions which cater to both the transformation process and the post-transformation existence. Our vision is to develop clean, recyclable, zero-waste, and sustainable applications.