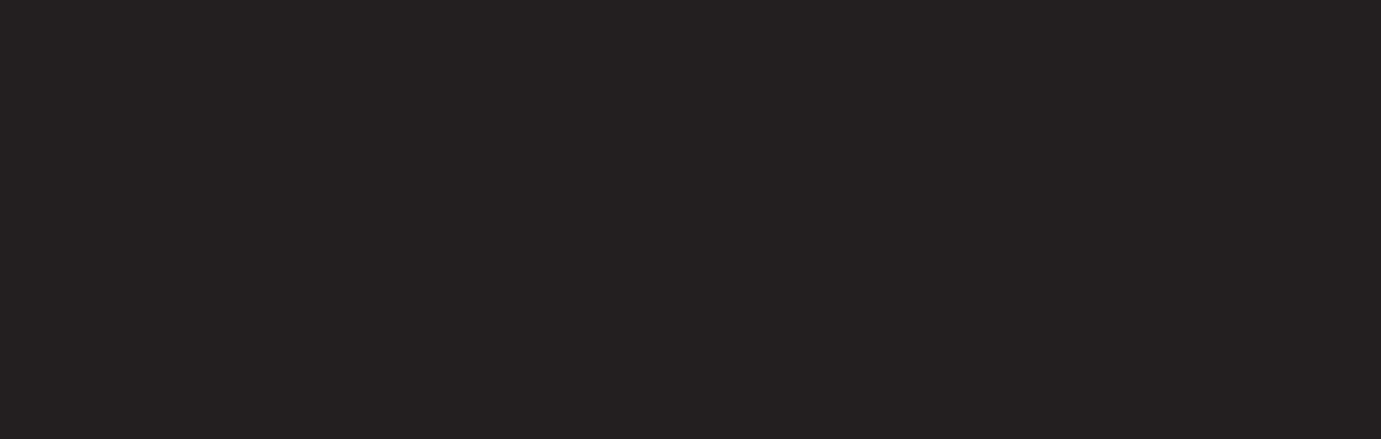
3 minute read
Safety Corner
Patrick W. SaltmarsTim Hunt, CHST h Corporate Safety Director Dir. of Envt’l, Health and Safety J. Derenzo Companies W. L. French Excavating Corp.
GHS: Secondary Containers
In 2012, OSHA revised the Hazard Communication standard. That revision included the addition of compliance with the Global Harmonized System (GHS). Material Safety Data Sheets (MSDSs) became Safety Data Sheets (SDSs), and the standardized form for SDSs was adopted. However, compliance with GHS is more than just Safety Data Sheets. We have all heard of the term “Right to Know,” which was created with the original standard, the revised version brought about the term “Right to Understand.”
Asecondary container is any container holding a product that is not the original container supplied by the manufacturer. Three common causes of incidents or health effects that can be traced back to secondary container labels include: 1. The material was not being used within the same work shift as the person who transferred from primary to a secondary container. 2. The person who oversaw the transfer left the work area. 3. The secondary container itself leaves the work area where it cannot be correctly identified.
At a minimum, a secondary container label must include the full name of the chemical and the hazard. Secondary containers are usually smaller, such as spray bottles, jugs, and jars. A driver of whether a secondary container needs to be labeled is based on the term immediate use. Immediate use means that the hazardous chemical will be controlled and used only by the person who transfers it from a labeled container and only within the work shift in which it is transferred.
To create a secondary container label, you need to start with the Safety Data Sheet. Every primary container containing hazardous chemicals should arrive from the supplier with an OSHA-compliant Safety Data Sheet (SDS). The SDS will provide the information needed to create the secondary container label. You can find the product name in Section 1 of the SDS. Section 2 provides the pictograms, signal words, and any special hazard statements relevant to the secondary container label. Finally, the National Fire Protection Association (NFPA) and Hazardous Material Information System (HMIS) ratings can be found in Section 16. continued on page 58
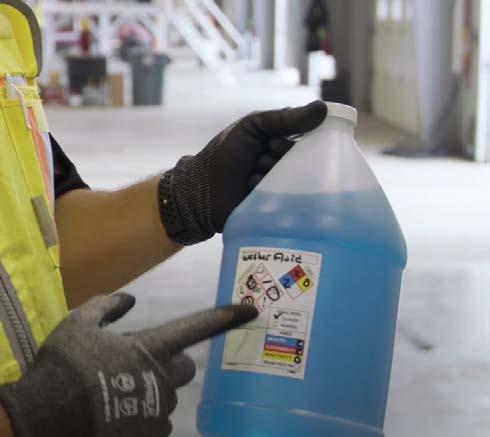
As a best practice, every secondary container should be labeled. The OSHA Hazard Communication standard allows some limited flexibility when labeling secondary containers. When it comes to primary containers, six clearly defined elements are required, but with secondary containers, the standard is less strict. All secondary container labels must provide the product name and a general hazard statement. To use the bare minimum elements for secondary container labeling, each container must be accompanied by auxiliary information such as the safety data sheet. Secondary containers are often the containers used most frequently, so it’s important to choose labels that are durable, waterproof, and specifically designed to resist damage from chemicals, abrasions, and extreme temperatures. Review which chemicals are frequently transferred to smaller containers and have a stack of those secondary container labels on hand. Ideally, that stack should be located with the primary container. If a particular container gets used repeatedly, you can label that container and leave it ready for the next transfer. Lastly, to ensure everyone understands and complies with the secondary container labeling requirement, you must train them on that. n

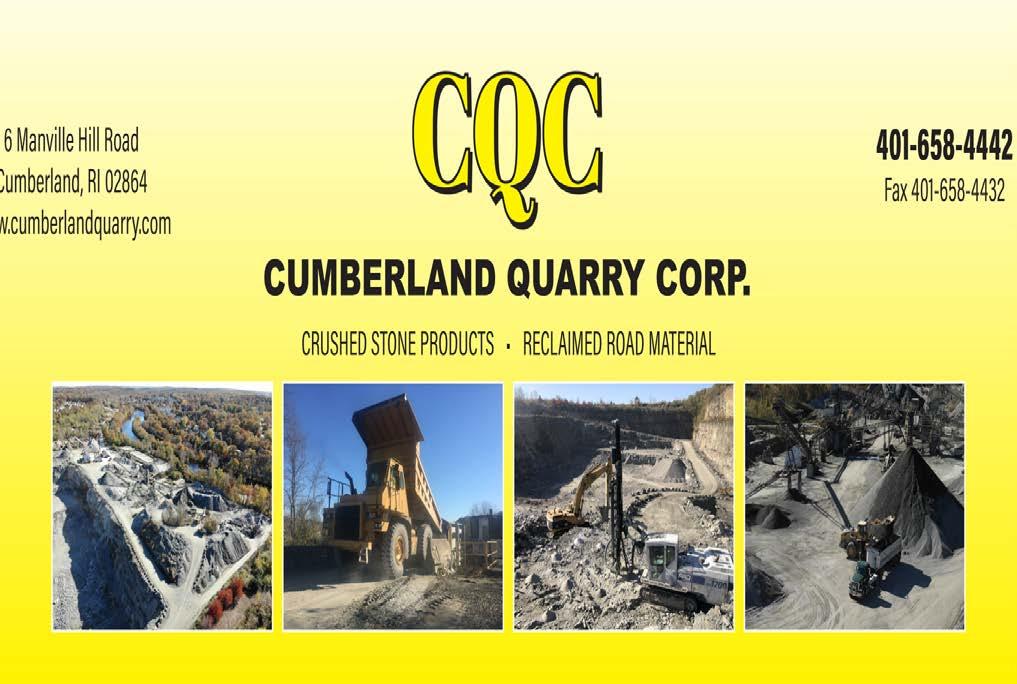
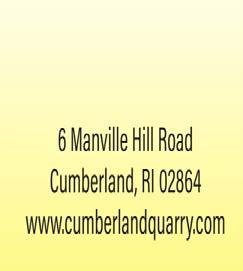