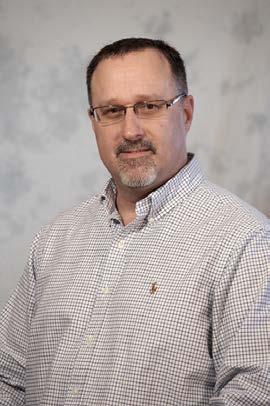
6 minute read
Technology in Construction
John Kane, B2W Software, Inc.
Why You Should be Automating the Preventive Maintenance Process
Software helps contractors cut costs, reduce breakdowns, and downtime by sticking to PM schedules.
The approach at a mid-size excavation and site work contractor that recently adopted specialized software to manage equipment maintenance was very typical.
The owner has a mechanical background, knows every piece of equipment inside and out and takes pride in keeping his fleet in top notch condition. He was managing a relatively effective maintenance program based primarily on his individual knowledge and supported by some basic spreadsheets and paper-based process.
So, why make the move to fleet maintenance software, or a CMMS (computerized maintenance management system), as it is sometimes referred to? This owner is approaching retirement and the company is growing. The next generation of family ownership saw maintenance software as an opportunity to make a smooth transition to a more automated, systematic approach to keep uptime high and costs low. Automating how preventive work is managed was one of their top priorities with the software.
What is Automated Preventive Maintenance
When I get the oil changed in my car, the mechanic puts a small sticker on the windshield indicating the mileage and date for the next oil change. That works well for maintaining one or two family cars. A construction company, however, might have 50, 100 or several hundred expensive, sophisticated pieces of equipment, each with dozens of critical preventive
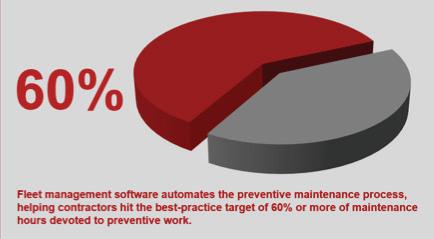
maintenance requirements that should be completed at various intervals.
Unfortunately, many rely on systems not much more advanced than the sticker on the windshield. They track maintenance intervals on spreadsheets or on pieces of paper in files in the shop or on the equipment. I’ve even seen masking tape on filters and hoses with the date they were changed written with a Sharpie marker.
Offline, analog systems make it too easy to miss or delay preventive maintenance. Maintenance management software, in contrast, brings automation to the process.
Contractors populate the software with the timing and scope of preventive maintenance work for each asset. This is based on recommendations of the manufacturer, as well as the company’s own requirements and preferences. The system then alerts them automatically when the work is due, what should be continued on page 39
New England’s Premier Precaster!





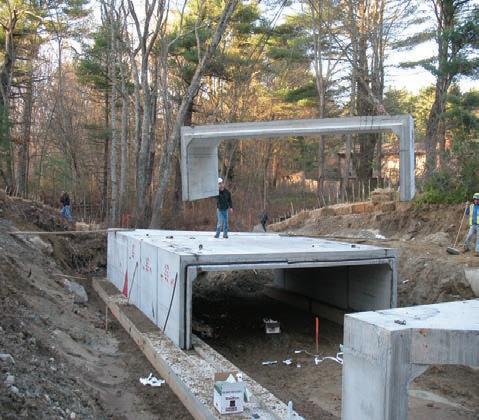
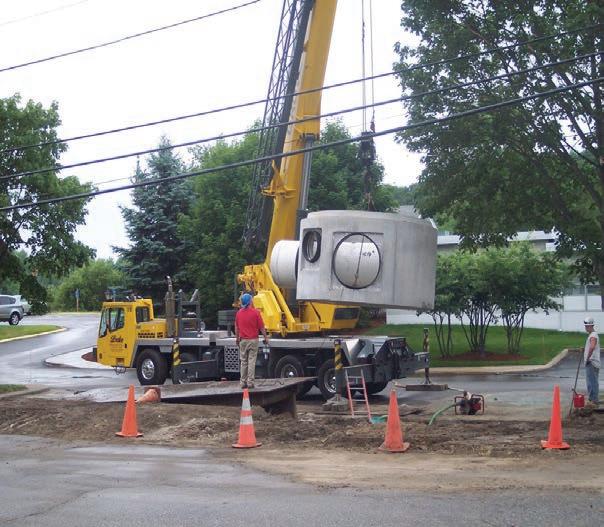
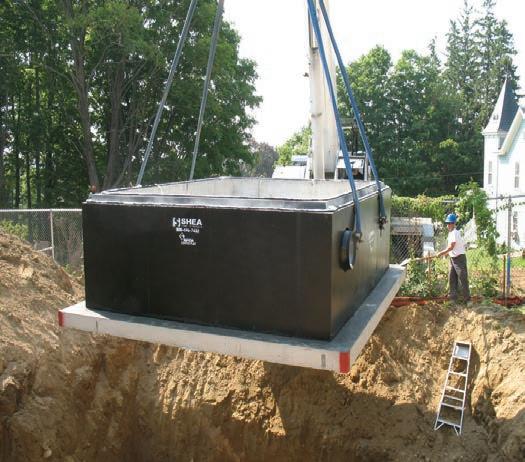
(800) 696-SHEA (7432) Fax: (978) 388-6959 www.sheaconcrete.com info@sheaconcrete.com
Other Products Include:
Median Barriers, Tanks, Pump Stations, Leach Chambers, Fire Cisterns, Utility Structures, Curbing, Precast Footings, Bollards, Stairs, etc…
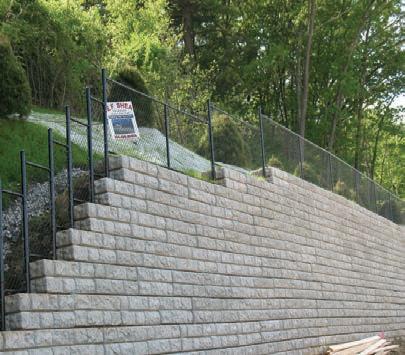
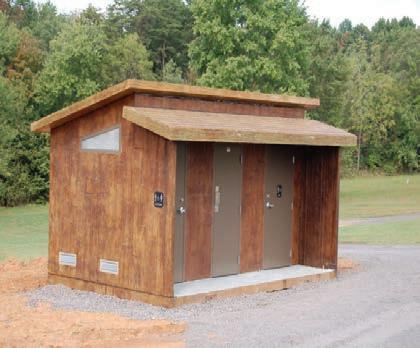

773 Salem Street773 Salem Street 87 Haverhill Road153 Cranberry Hwy 153 Cranberry Hwy160 Old Turnpike Road Wilmington, MA Wilmington, MA Amesbury, MA Rochester, MA Rochester, MA Nottingham, NH Mail: PO Box 520 ● Wilmington, MA 01887 Mail: 87 Haverhill Road • Amesbury, MA 01913
Technology in Const. continued from page 37 Finally, with a more automated and prevendone, what parts are required and if there is any rel- tive approach to maintenance, contractors exevant warranty information. tend the lifetime of their equipment and make it
Maintenance managers specify how far in ad- safer to operate. vance they want to see preventive maintenance Personal knowledge and experience of menotifications, which are triggered by dates, meter chanics, managers, and executives are vital to efreadings from equipment, or both. The readings can be transferred from field logs, inspections or other sources. Ideally, they come into the system directly fective construction equipment maintenance. As companies and fleets grow, and assets get more via telematics or GPS technology. advanced, however, that may not be enough.
What are the Benefits? Supplementing expertise with a software system that makes preventive maintenance systematic Automating preventive maintenance makes it far more likely that contractors will complete preventive work on time. When they do, the results are universal. Breakdowns, downtime, and maintenance costs Boston Area Locations and automatic is a proven way to increase equipment uptime and hold maintenance costs to a minimum. n all decline. 2 Dexter Street When they don’t, these three metrics create a downward spiral. Skipping preventive mainteBoston Area Locations Everett, MA 0 431 Second S 2149 treet Bos Lo ton cat Ar ion e s a nance increases the rate of unex- 2 Dexte Everett r , Street MA 021 2 49 Dexter Street pected breakdowns. That drives Everett, MA 021 Eve49 rett, MA 02149 unplanned downtime, which disrupts productivity in the field and 431 Second Stre 43et 1 Second Street adds cost for rental or replace- Everett, MA 021 Eve49 rett, MA 02149 ment equipment. Finally, as a BOSTON AREA LOCATIONS maintenance strategy, waiting for 2 Dexter Street 100 Fremont Street 431 Second Street something to fail and then fixing it Everett, MA 02149 Worcester, MA 01603 Everett, MA 02149 is always far more expensive than preventing it from failing in the first place.
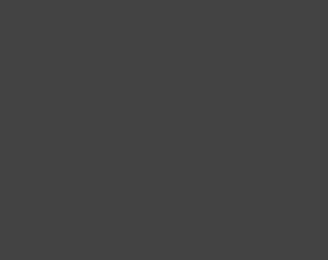
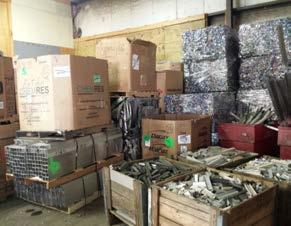
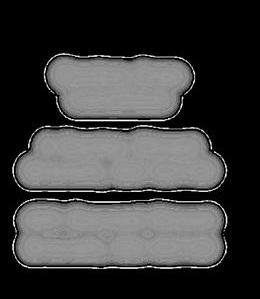
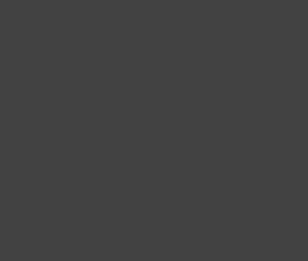
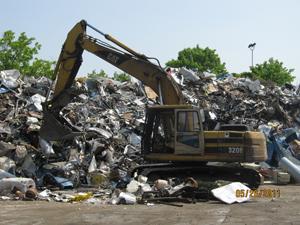
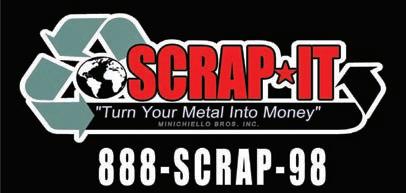
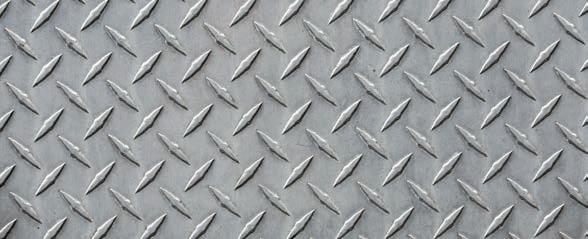
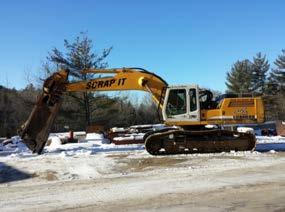
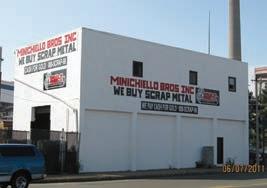
There are other benefits too. Maintenance managers and mechanics are in high demand, and their time is valuable. Automation optimizes that time by eliminating administrative work, improving scheduling and increasing “wrench time.” Minichiello Bros./Scrap-It, Inc., Minichiello Bros./Scrap-It, Inc. With software providing visibility into the upcoming prevenServes over 2500 customers a week and is one New England's largest buyers, sellers and processors of scrap metal. For over 60 years our goal has remained the same - to provide the best prices in the industry along with top notch Serves over 2500 customers a week and is one of New England’s largest buyers, sellers, and processors of scrap metal. For over 60 years our goal has remained the same - to provide the best prices in the industry along with tive maintenance requirements of customer service! Call Fred Rogers at 617-595-5505 top notch customer service! Call Fred Rogers at 617-595-5505 the entire fleet, managers can plan Minichiello Bros./Scrap-It, Inc., work more efficiently. When an as- Minichiello Bros./Scrap-It, Inc., set is in the shop for a repair, they Serves over 2500 customers a week and is one New England's largest buyers, are prompted to do upcoming preventive work in advance. Likewise, when they assign a mechanic to go to a jobsite to work on one Serves over 2500 customers a week and is one New England's largest buyers, sellers and processors of scrap metal. For over 60 years our goal has remained the same - to provide the best prices in the industry along with top notch customer service! Call Fred Rogers at 617-595-5505 sellers and processors of scrap metal. For over 60 years our goal has remained the same - to provide the best prices in the industry along with top notch customer service! Call Fred Rogers at 617-595-5505 piece of equipment, they can look into other equipment at that site and assign preventive work in advance, potentially saving trips back and forth to the site. Turn your metal into money today! Minichiello Bros. Inc.,/Scrap-It Inc. Turn your metal into money today! Minichiello Bros. Inc./Scrap-It Inc.
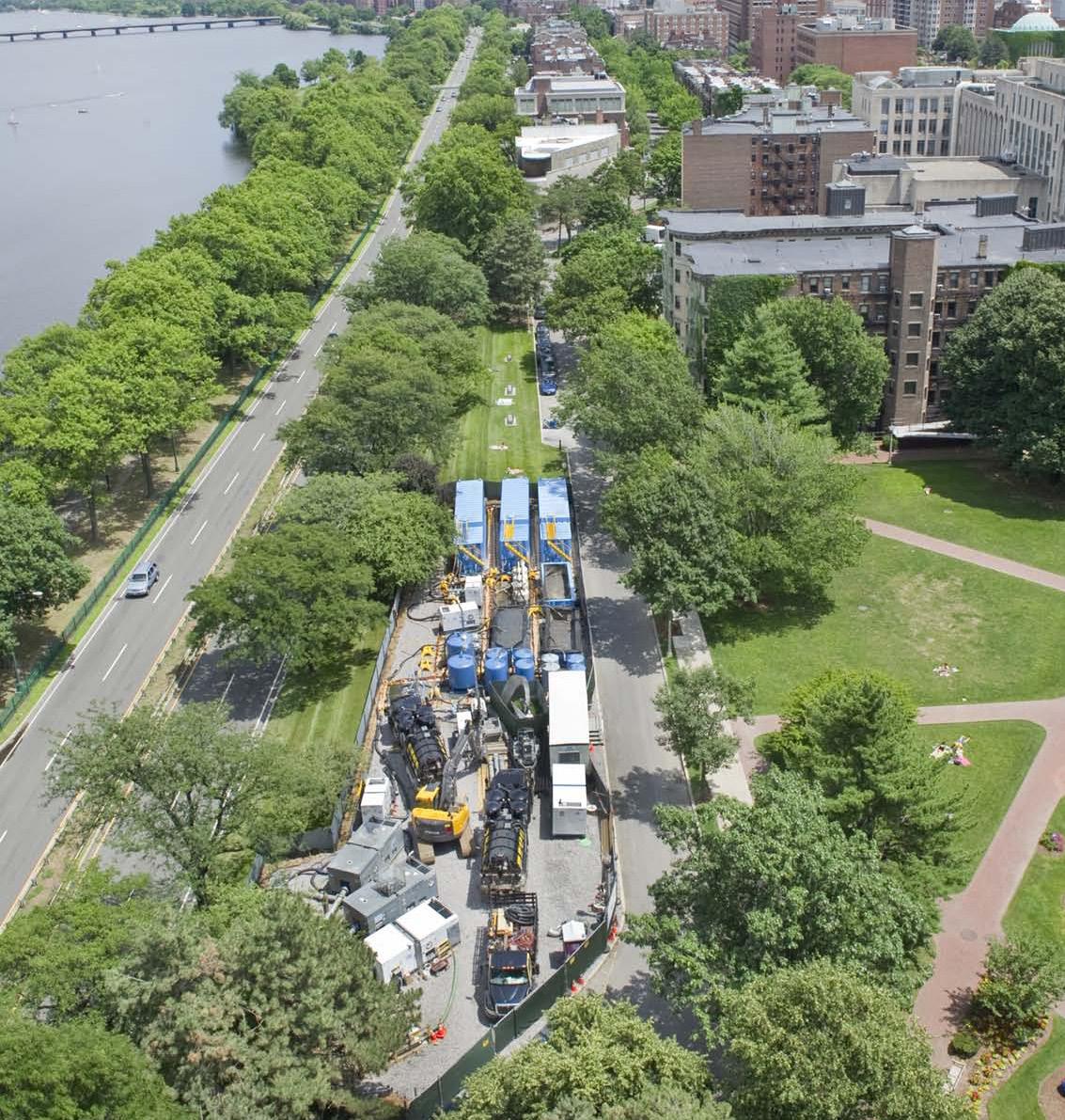
rainforrent.com