
8 minute read
READ THE BRITISH STANDARDS
READ THEM AND UNDERSTAND THEM
Earlier this year we were asked to “read the standing orders, read them and understand them” all be it by an apoplectic parish councillor. When it comes to separators however, it is important that as an industry we read the British Standards, read them and understand them.
British Standard BS EN 858-2:2003 covers, as well as other areas, the guidance on how to maintain separators (interceptors). With PPG 3 having been withdrawn and, as of yet, not re-released as a GPP the British Standard guidance is the authority for compliant separator maintenance across the UK.
The industry standard (for companies who actually have their separators maintained) is to have them emptied every 6 months.
Unsurprisingly companies who operate tankers have perpetuated the myth that emptying is required every 6 months with the below phrases all taken from tanker companies websites in June 2021:
“Interceptors must be maintained regularly (emptied and cleaned)” “Regular interceptor emptying and cleaning is an important part of keeping your site running efficiently” “It is recommended that interceptors are regularly maintained and cleaned ……. every three to six months.” “It’s vitally important to carry out regular interceptor emptying, cleaning and maintenance”
Whilst the above quotes are all accurate in the fact that regular maintenance is important, they all share the common misconception that emptying and cleaning are essential components of regular maintenance.
This practice is not what is required under the British Standard and does not meet the requirements to prove that adequate maintenance checks have been undertaken, in addition it generates unnecessary hazardous waste, water usage and carbon creation. One of our clients who switched from emptying their separators on a 6 monthly basis to having maintenance inspections conducted made annual reductions of over 1,000,000 litres of water, 1,000,000 litres of hazardous waste and 9 tonnes of CO2 emissions. In addition and most crucially they also ensured that appropriate maintenance was being conducted.

GPT separator auditing stats
In truth BSEN 858 is quite explicit that emptying does not form an essential part of the 6 monthly maintenance stating “Light liquid and sludge shall be removed as required……NOTE Emptying is recommended when one half of the sludge volume or 80 % of the storage capacity of the separator is reached.”
In addition by simply emptying and cleaning the separator the essential checks to the separator’s functionality are not being undertaken. Compliant 6 monthly maintenance will require:
determining the volume of sludge, determining the volume of light liquids (oil), checks on the automatic closure device (ACD), checks on the coalescing device, checks on the warning device (alarm), checks on the sampling shaft.
A layman’s term analogy would be having a vehicle MOT. As with separator maintenance, it is a service which is required periodically to ensure your infrastructure is in good working order.
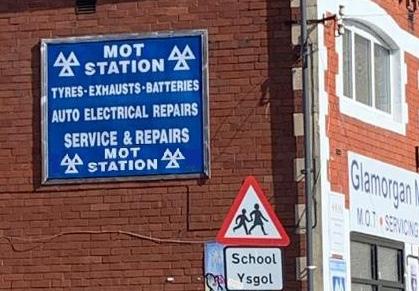
During an MOT, checks must be undertaken to test the condition and performance of certain components of your vehicle. Following the MOT you are given a report into the condition of your vehicle. You may be given a certificate stating everything is in good working order and no further action is required; or you may have issues which need additional work to be undertaken to ensure the vehicle is working properly and not likely to cause an incident.
Proper separator maintenance will be similar to this, checks will be undertaken periodically on the performance of key components. A written report should be produced and supplied to the client either confirming the system is in good working order, or, recommending additional actions needed to bring it in line with required specifications.
The current industry standard of having separators emptied every 6 months would be comparable to instead of having an MOT, having the tyres replaced and oil changed on your car every year, irrespective of their condition, without checking the functionality of the key components such as brakes, lights and steering. This would be unnecessarily expensive, environmentally unsustainable and most crucially would not test that your vehicle was working properly. In addition, if something were to go wrong you could not prove that you had conducted appropriate maintenance in a subsequent legal investigation.
We have taken on board a substantial amount of new clients for separator maintenance over the last few years. Many of these were having their separators emptied every 6 months, and a concerning amount had not been undertaking any maintenance at all.
The following are all case studies of problems caused by improper maintenance being conducted, or no maintenance being conducted at all. We were called to a site which was having issues with their drainage flooding following rain fall, every time this happened they were calling a tanker out to pump out the drainage and separator to remove the flood water and allow site operations to continue. The blockage was identified as coming from the separator, and they believed the separator must be broken which was causing the flooding.
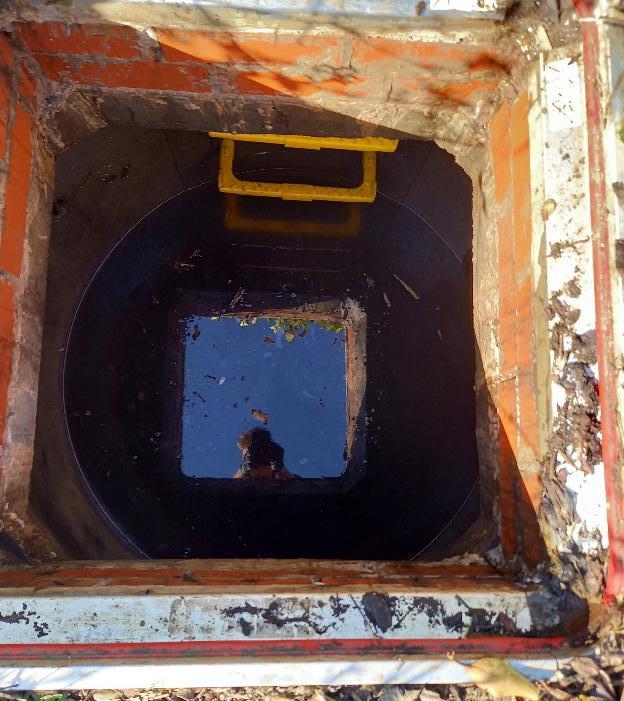
ACD highwater level ACD normal
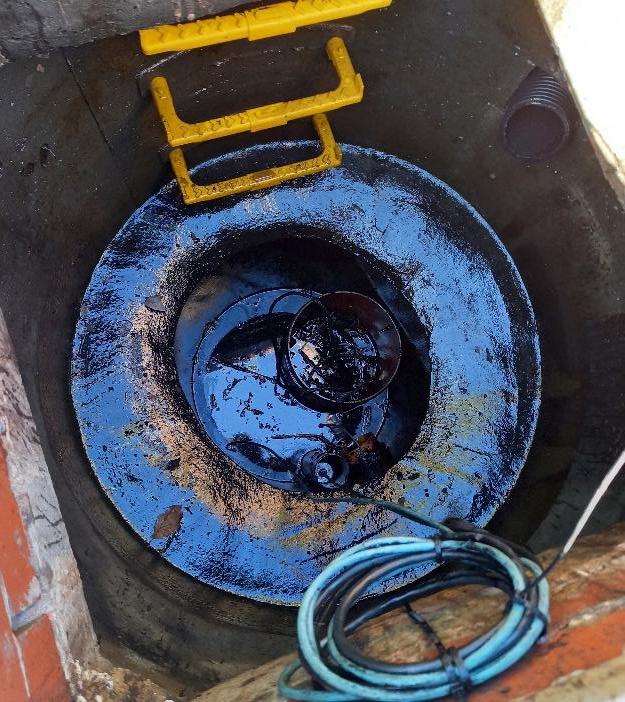
Case Study 2 – Coalescer damaged during servicing
Coalescers are often the scapegoat when separators encounter a problem. Both clients and inexperienced maintenance providers will jump straight to the assumption that the filter is blocked which is causing the system to not work properly. Sometimes, of course, there is a problem with the coalescer, but more often than not they are not what is causing the issue. It is also a regular occurrence that in When we inspected the separator we discovered that it was in full working order but that the ACD had been triggered and had not been reset. Either through negligence or lack of knowledge the inadequate maintenance had led to the tanker company getting paid for multiple call outs to remedy the problem they had caused. Costing the client a significant amount of money, disturbance to site activities and unnecessary waste and carbon creation. Left elevated water level, right correct water level following ACD reset
desperation, clients will remove the coalescer from the system to attempt to fix issues themselves. This does not solve the problem but instead means the separator will not function correctly, creating an elevated risk of pollution. In addition they may break the coalescer in the process. This then requires repairing alongside other issues, costing a significant amount more money and effort.
Left unseated coalescer housing, right coalescer housing removed with filter media missing.
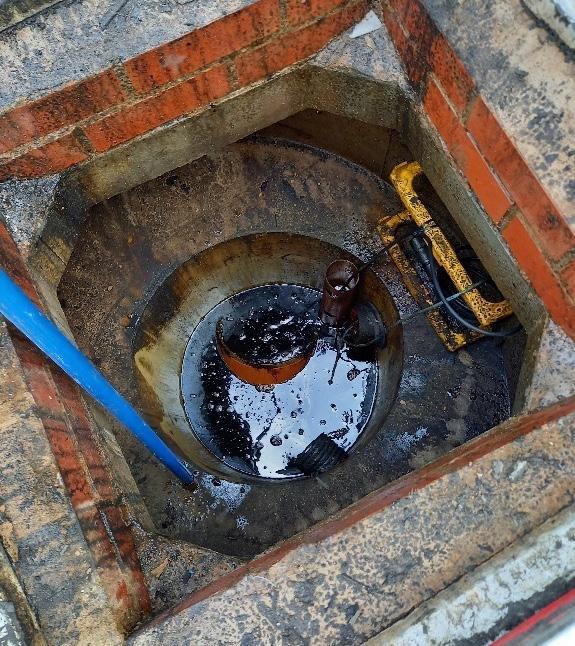
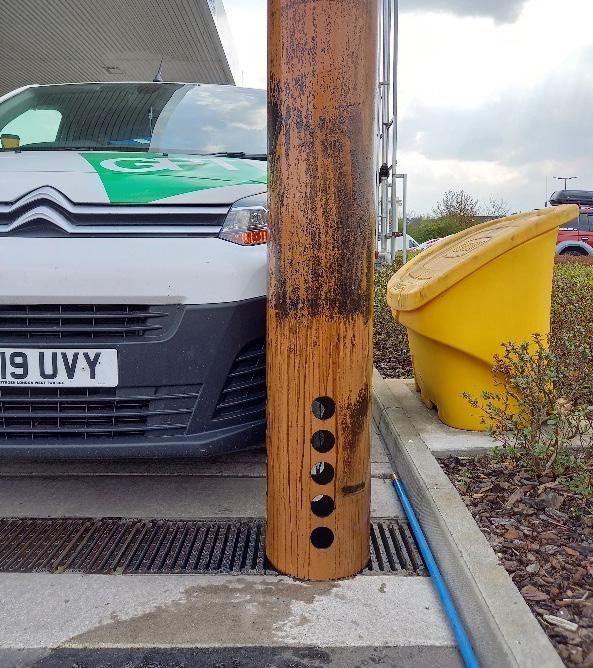
Separator alarms or “warning devices” as they are referred to in the British Standard are key to ensuring you are given advanced warning if an incident occurs and the separator has contained the spilled oil. They are also the piece of infrastructure we see problems with most often, perhaps unsurprisingly as they are electrical devices installed in drainage systems.
There are a lot of issues which can go wrong with separator alarms, but by far the most common issue is that they are not installed properly or they are simply turned off. BSEN 858 requires separators to be provided with a warning device, but often installers do not fit them.
This may be because they do not know what they are or how to install them, or because running power and ducting can be difficult or expensive. The photo shows an alarm which has been dumped into the separator without being connected to a power source.
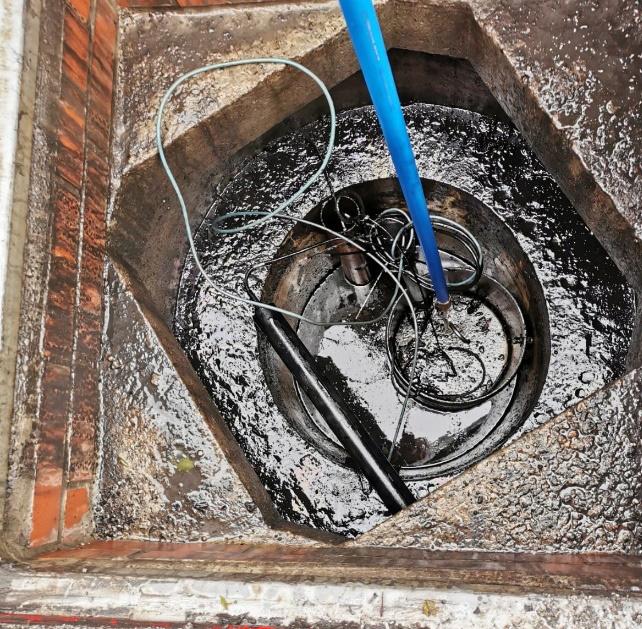
Alarm
Case study 4 - Sampling cap missing
This is a less common problem, and is one which is likely to be missed by inexperienced maintenance providers. The below photo shows the final chamber of a separator, there is some iridescence on the surface which shows a small amount of oil is present, the oil level is well below the threshold for emptying and the fact that there is some oil suggest the system is working correctly. However, the pipe on the left hand side should not be open. This is the sampling shaft and it has the top part missing. This may have been done during maintenance, or it may have been installed without it. Either way it is an issue which would allow oil to escape the system as the discharge pipe will be fed from the top instead of the bottom.
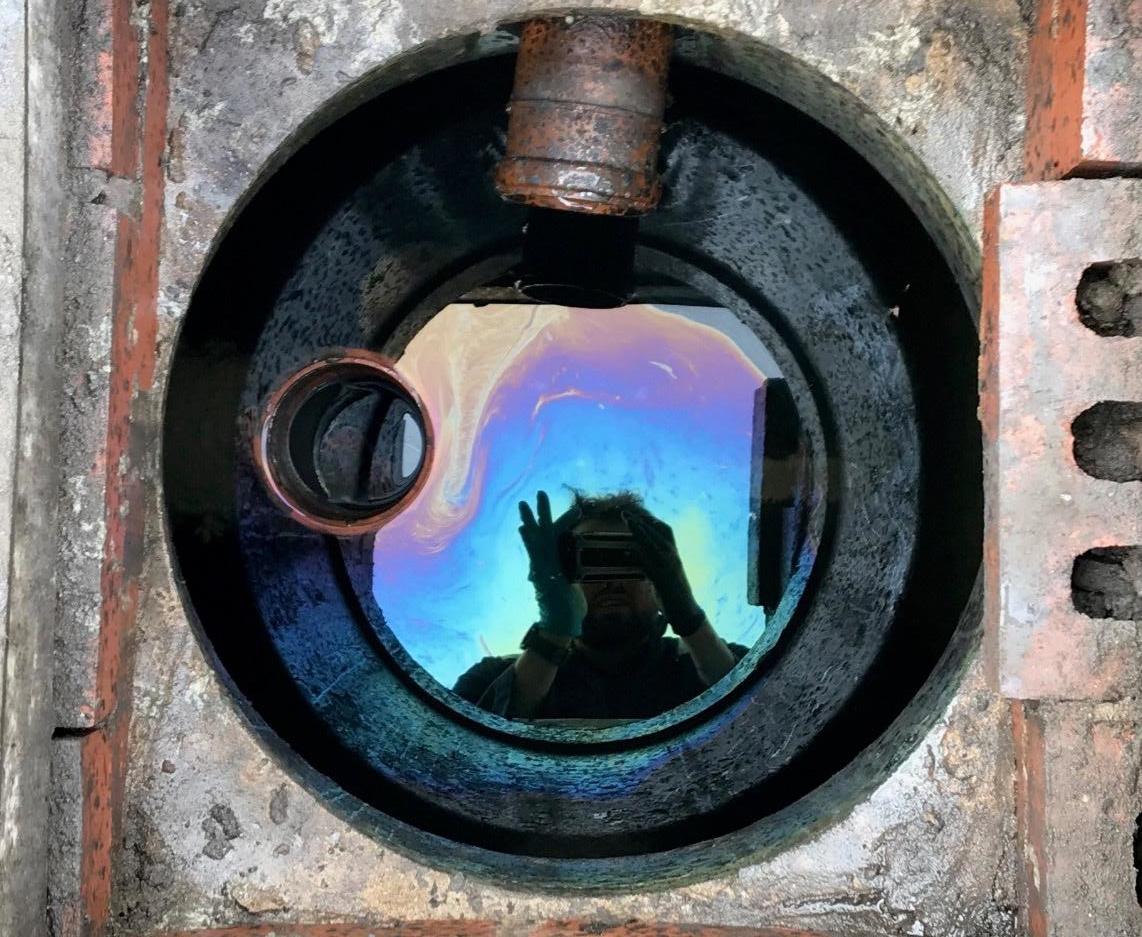
Sampling cap missing
Case study 5 - Integrity of the system broken
Some sites which have a significant amount of oils or silts entering the separator will require emptying regularly, however in many cases emptying will only be required once every 5 years as part of a general inspection. During a general inspection, as well as emptying and cleaning the system, the integrity must be assessed. This can be undertaken using a confined space entry team or by inserting a camera and recording the internal condition of the system. It is vital that during the 5 yearly general inspections the systems are not simply emptied, cleaned and recharged, but that a proper assessment is conducted. Below are photos of a separator with cracks which could only be seen once the system had been emptied and a camera inserted.
As an industry it is essential that we ensure maintenance is conducted properly, by experienced personnel. Separators are often the last line of defence, and ensuring they are adequately maintained could prevent a major environmental incident. cracked system 1 adjusted
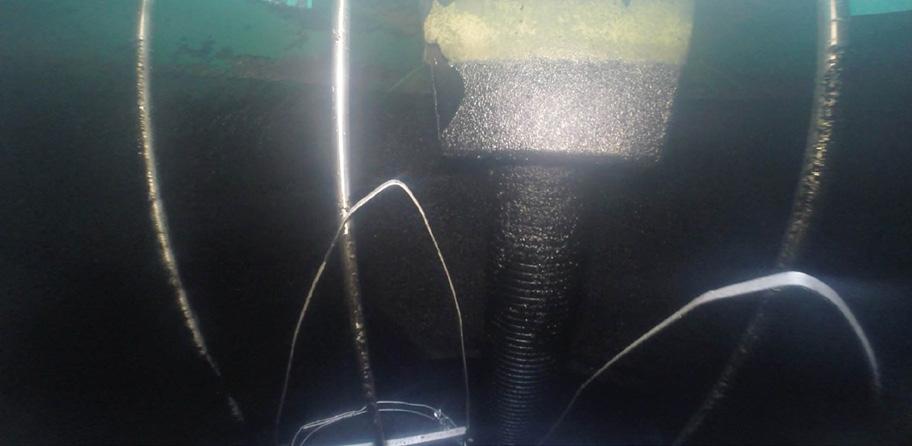
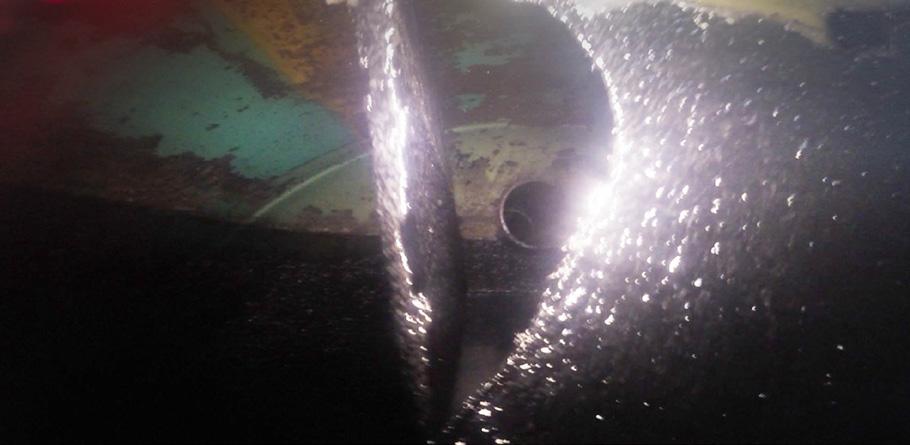
cracked system 2 adjusted
Sam Chick is the Marketing Manager at GPT Environmental Ltd who undertake separator maintenance and installations.