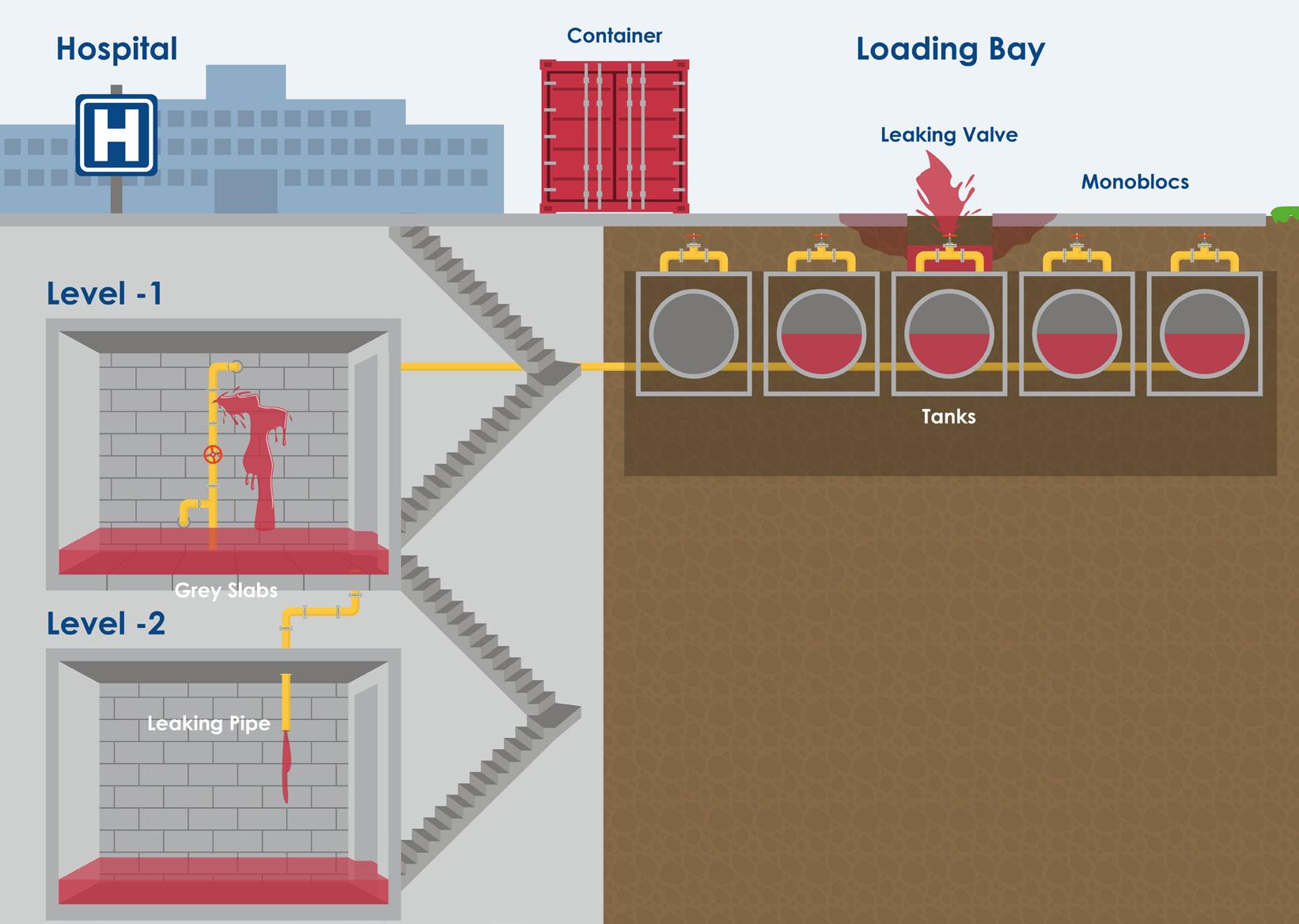
7 minute read
CASE STUDY
‘FUEL WAS WASHING OUT OF THE WALLS’
INLAND RESPONDER AWARD – HIGHLY COMMENDED
INTRODUCTION
LCM Environmental started 2022 with a substantial spill response project. Following an urgent call from the facility management company of a London-based hospital, our first spill responders attended site within the hour.
A faulty valve on one of the five underground gas oil tanks, used for the hospital back-up generators, had caused a leak that had spread across three stories. By the end of phase 1 (out of 2), the team had removed 18 tons of waste, 10 tons of gas oil and planned for ground and soil remediation. Phase 2 consisted of remedying the hospital grounds and soil from the remnants of red diesel.
After LCM’s stellar performance on this project, the facility management client, who called us initially, has passed on multiple hospital spill response opportunities throughout the year.
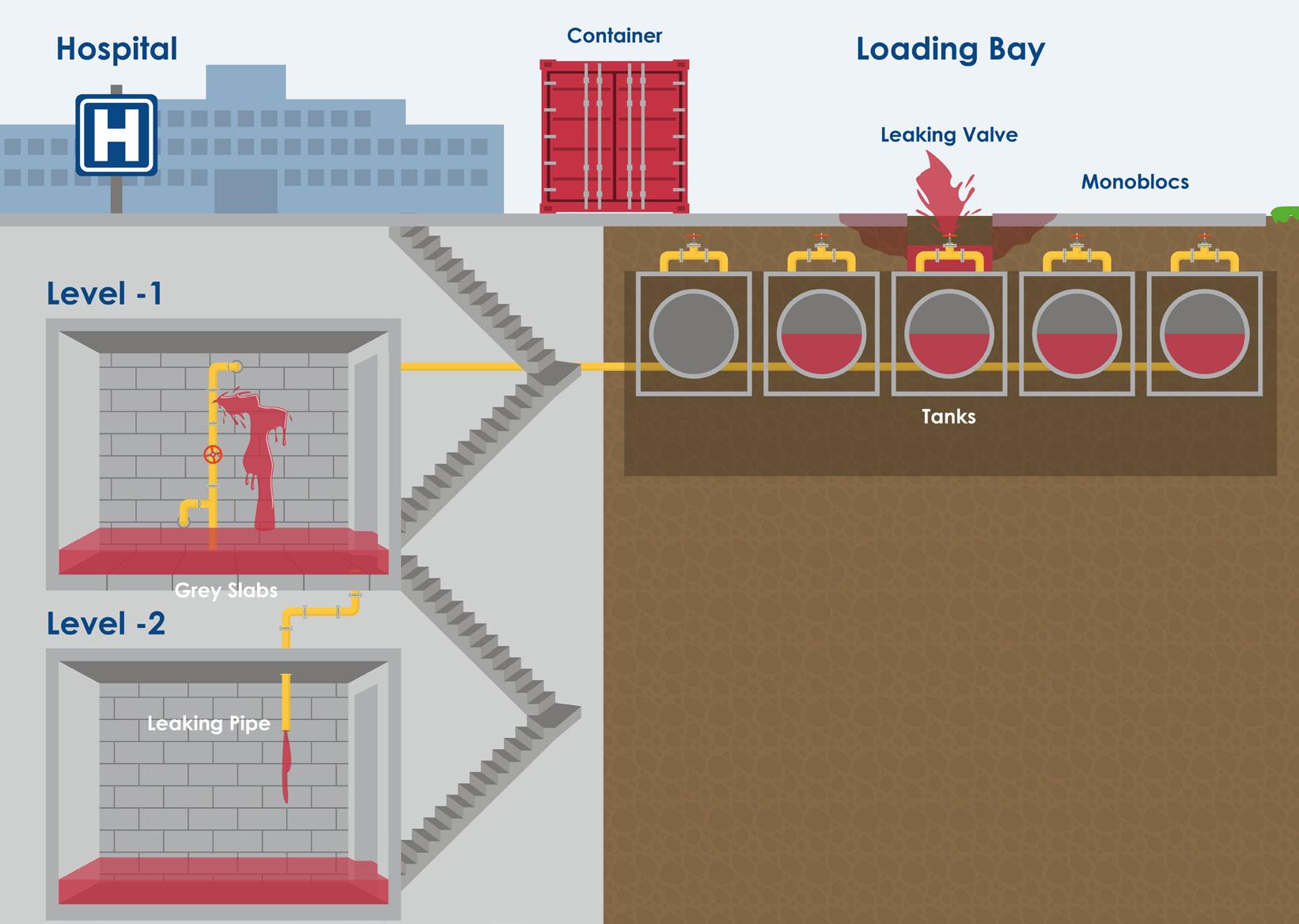
THE INCIDENT
In January 2022, LCM Environmental received a call from the facility management company of a London-based hospital regarding a major gas oil spillage occurring on their premises. The initial incident description was described as: ‘red diesel is spraying out of the walls, into two floors below the tanks!’.
The Environment Agency was informed by the client that LCM Environmental was undertaking the remediation of the spill and removal of any surface contamination on behalf of the hospital (EA Reference number: 2028706).
An hour after the initial call, the LCM spill first responders were on site to evaluate the extent of the spillage. They cordoned off the area and assessed what equipment was required. The site consisted of four underground gas oil tanks (50,000L each), placed under an access road – with only one of them ‘online’ (tank #3).
The hospital generator system was on a ring main system and the gas oil within it was circulating pressurised. The spillage occurred due to a replacement valve not having a new gasket fitted correctly to the top flange of the online tank valve (tank #3). This allowed the fuel to escape once the pump was activated and the pressure built up, leading to a substantial leak. The five tank chambers were all flooded and due to the hospital site’s infrastructure, the gas oil ran into the lower service floors of the hospital (level -1 and level -2).
The project outlined was executed in two stages: spill clean-up with waste disposal, and ground and contaminated sand removal for remediation.
Figure 2 . Spill site visual. The hospital and loading bay are on the Ground level, with 5 red diesel tanks underneath. 4 of the tanks were active, one was foam-filled, only tank #3 was online. Gas oil has spread towards the two underground hospital levels through the pipework because of a faulty valve.
SCOPE OF WORKS: STAGE ONE
After receiving the initial report from LCM Environmental’s first responders, the Spill Response Project Manager immediately sent out two spill response teams, 2 jetting vac tankers and a jet washing crew. The first engineers of the LCM team on site deployed the oil-only spill socks to contain the incident from reaching any main sewers. Once on site, the site was evaluated, and a site survey video recorded (see Figure 1). The first responders then went on to strip down the faulty valve and replace the faulty gasket with a new one, to stop the spill from getting any worse whilst retaining the hospital’s critical backup infrastructure. The valve on the return line to tank #3 was opened, as well, to allow the ring main system to work as it was designed to.
All drains were covered with drain covers in the basement area to prevent the red diesel from leaving the hospital site and spreading into the water system. The LCM engineers extracted 4 tons of gas oil from the -1 floor and 6 tons from the -2 floor of the building. After the majority of red diesel was uplifted and disposed of, the jet washing crew washed down as much waste and fuel remnants as possible into the -2 level. This was done to prevent any escape of contaminated washing going into the drainage system.
On the next day, the LCM engineers applied environmentally friendly cleaning products to the slabbed area on the -1 level, the stairs, and the basement. The jet washing continued for the whole duration of the day between the -1 and -2 levels of the building – including the gully which ran the full length of the basement (-2 floor) and was full of silt and sludge. The team did a thorough clean of the areas behind the generator and the gas pumping station at the bottom of the basement.
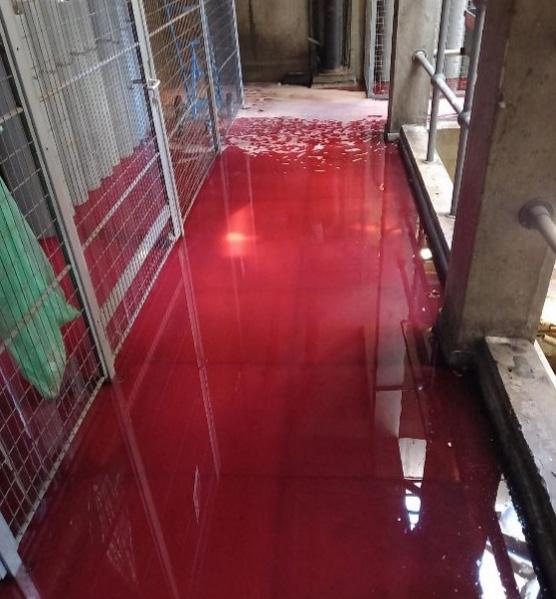
Figure 3 . Level - 1. All slabs are covered in gas oil.

Figure 4 . Basement/-2 level. Downstream pipe leaking out gas oil.
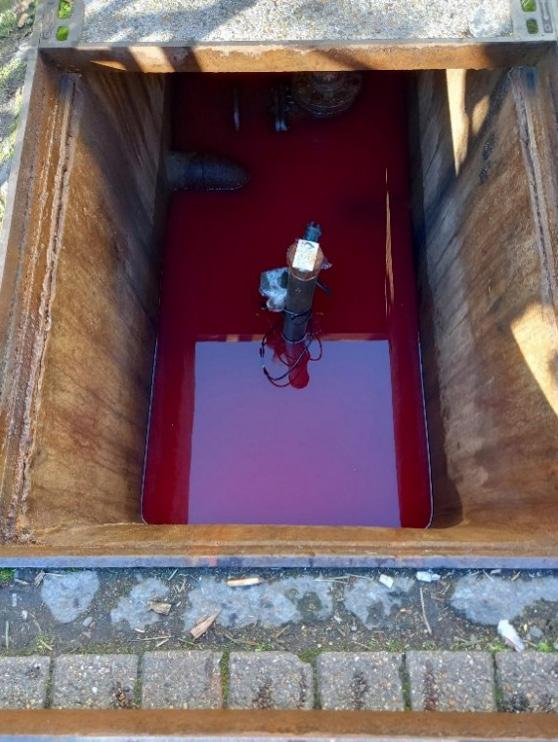
Figure 5 . Tank 3 Chamber, Filled with red diesel
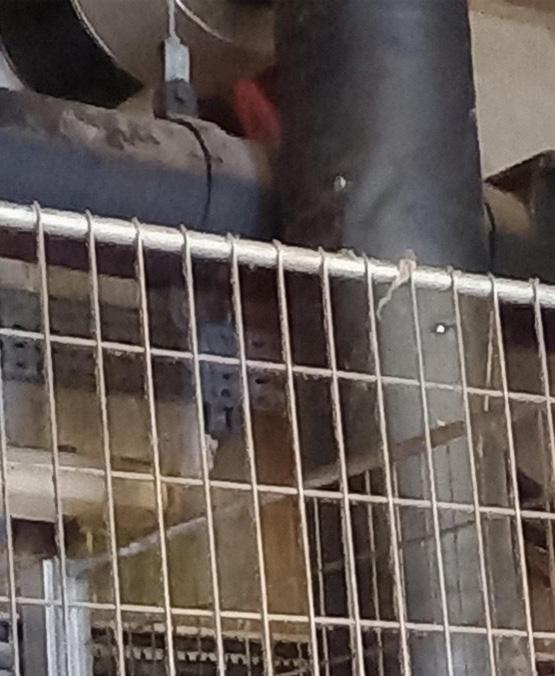
Figure 6 . Burst pipe on the -1 level. ‘Spraying out of the wall!’
SCOPE OF WORKS: STAGE TWO
Phase Two of this project included the sampling and testing the sand underneath the slabs and the monoblock area. The results of the testing indicated a high level of contamination and the area needed to be excavated. The LCM Environmental team uplifted and removed contaminated sand and concrete from under the slabs of the -1 level. Approximately 120 slabs and 10m2 of permeable block pavers were replaced in the process. There was excess gas oil leachate under the slabs that needed to be removed to prevent any further contamination.
Furthermore, the LCM spill responders had to remove approximately 6m of mono blocks from the ground floor area and sample the depth of the contamination within the soil. The LCM team sampled the sand and soil to a depth of 900mm to determine the level of contamination. Based on the results of the tests, there was a requirement to extract the contaminated soil/sand mixture and dispose of it safely. Finally, the spill responders backfilled the excavated area with clean soil/sand and replaced the 6m of new monoblocks.
When the team uplifted the slabs on the -1 level, they found a foam bed underneath the sand. The LCM engineers had to remove the foam, as the gas oil contamination had spread through it, and beyond to the base. Once the slabs, sand and foam were all removed, the team jet washed the base and apply environmentally friendly chemicals to remove any remnants of the contamination. Finally, new foam, sand and slabs were placed on the -1 level.
OUTCOME OUTCOME
LCM Environmental’s facility management client was satisfied with the speed, integrity, and expertise of the spill response team. The two-staged project was finished according to the client’s budget and time-constraint specifications.LCM Environmental’s spill response service, only being launched in September 2021, dealt professionally, rapidly, and competently with a spillage of this magnitude. This project was the tipping point for LCM’s spill response ‘trial period’ within the industry: the company proved their reliability and undeniable expertise in spillage clean-up. This resulted in further business coming to our Environmental Services Division from the same satisfied facility management client, as well as word-of-mouth reputation enhancement for LCM Environmental.The company benefited further from working with the emergency services sector, achieving fantastic number of sign ups from hospitals, police stations and fire stations for their Spill agreement. The latter, in essence, guarantees LCM Environmental are the spill responders of choice of the signed-up companies – in return, they receive discounted call-out rates, no retainer fees and 4-hour aimed response time nationwide.
Figure 7 . Level -1 slabs all cleared of gas oil. Need to be removed and the ground/ sand below them tested for further red diesel contamination.
Figure 10 . Basement level/-2 level: The leak was stopped, and all red diesel removed from site. Further concrete washing was required.