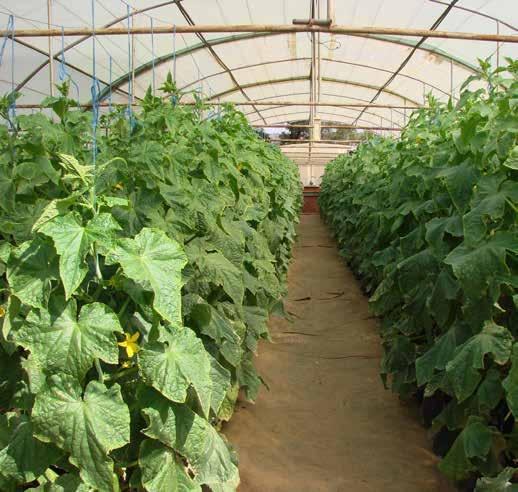
3 minute read
Commercial greenhouse cooling systems: natural ventilation compared with forced evaporative pad and fan
gr eenh ous es I sha de net I hy dr oponics I aquap onics
Commercial greenhouse cooling systems: Natural ventilation compared with forced evaporative pad and fan
Advertisement
High greenhouse temperatures are extremely detrimental to optimum plant health and growth, which obviously has a negative effect on commercial greenhouse farming yields and profitability. It therefore goes without saying that an effective greenhouse cooling system is one of the most important considerations for greenhouse growers. These solutions are either passive (natural) or forced (mechanical).
Forced Evaporative Cooling Ventilation
Pad and with Fan
Pad and fan
The pad and fan cooling system work by using exhaust fans that suck warm air out of the greenhouse creating air flow over evaporative cooling pads. This is a popular method for cooling greenhouses and can reduce temperatures significantly (between 5-10 °C depending on the relative humidity) but it has various disadvantages: 1. High energy costs. 2. Higher maintenance costs. 3. Significant temperature variance 4. Mainly effective in dryer climates. 5. Water consumption is higher in pad and fan cooling compared with high pressure fogging.
Natural , Passive Ventilation with High Pressure Fogging Natural ventilation
Natural ventilation is the result of
pressure differences created by the wind and temperature in the inside and outside of a greenhouse. It requires less energy n comparison with pad and fan cooling.
High Pressure Fogging (HPF)
If the above-mentioned natural ventilation options are not sufficient 7
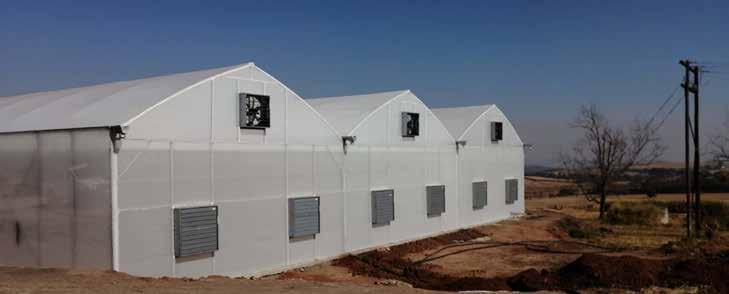
for cooling the greenhouse, they can be used in conjunction with high pressure fogging. Documented Natural ventilation is in a recent the result of pressure research paper, differences created experiments were done by the wind and on naturally temperature in the ventilated inside and outside greenhouses in of a greenhouse. Pietermaritzburg, KZN. It was found that by using HPF, the internal temperature can be reduced up to 10 °C (E. du Plessis, 2016).
In conclusion
In a comparison using a 1ha greenhouse, the following assumptions can be made: • The fans run on average for 4 hours per day throughout the entire year (this can be double in some areas depending on the climate). Water is recycled through the system and only evaporation water is counted; • The HPF runs on average 4 hours per day throughout the entire year (the system switches on and off intermittently as required throughout the day and will change during seasons); • Average electricity rate of R1, 2/kWh, and • Standard designs are assumed. The electricity expense per year for the 1ha pad and fan
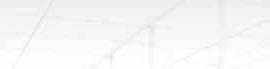

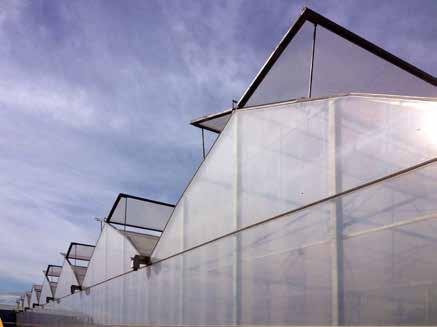
greenhouse accumulates to at least R210 000 per annum, in comparison to R 40 000 per annum for the HPF in a naturally ventilated greenhouse. The water consumption for the 1ha pad and fan greenhouse is 45 000m3/year versus the HPF system that consumes 7 500 m 3 / year. Your unique greenhouse ventilation requirements may require expert advice to guide your decision-making process. Readers may contact Bosman Van Zaal South Africa to obtain further assistance in this regard.
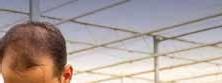


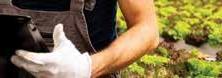