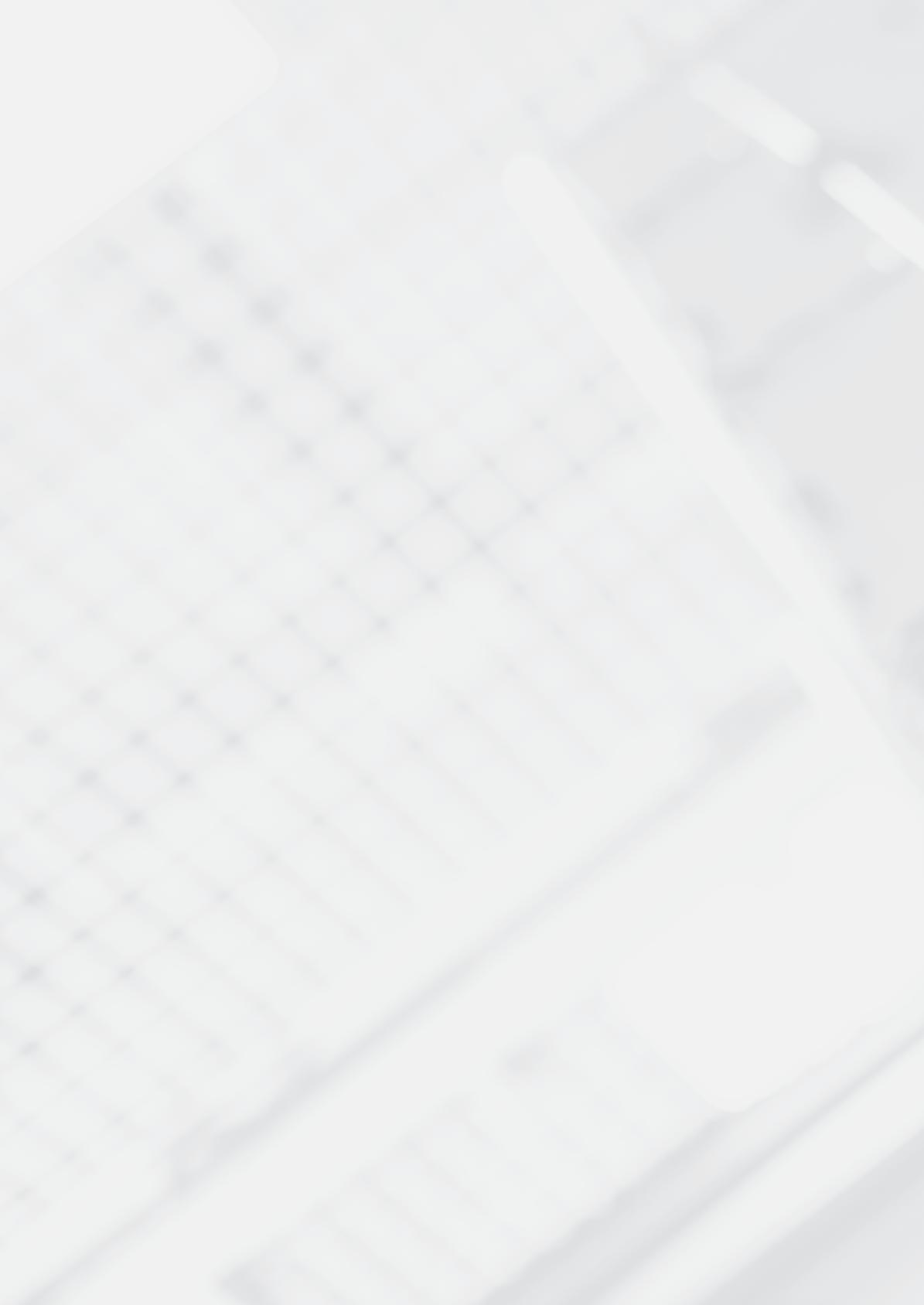
2 minute read
Developing Impact with Industry
Research Impact A key challenge and priority for the Hub is to make sure that research outputs will lead to industrial impact and, ultimately, will deliver real and lasting benefits to UK manufacturing and the UK economy.
The nature of our team and its research is that we always have end use in mind, and our strong relationship with industry partners and the Catapult Centres will be critical in maximising impact and the early adoption of new technology, methods and knowledge. Long-established relationships with key partners such as Renishaw, Taylor Hobson, Rolls-Royce and DePuy continue to flourish, building on research outputs from the past few years.
Advertisement
Whilst the core research programmes are still in their early stages, significant progress has already been made in the Hub’s first year of operation in terms of developing new relationships with industry, strengthening those with our co-creating industry/catapult partners, and exploiting a number of specific opportunities to deliver early impact through new industry-driven projects. Growing relationships are being developed with companies including Hexagon Metrology, DigiSurf, Nikon, and Jaguar Land Rover, as well as many smallerscale collaborations with companies across a range of industry sectors. These new relationships will significantly extend the depth and breadth of the Hub’s impact over the coming years.
Industry led R&D
Alongside the core programme, our researchers are working on a variety of industry-led research and innovation projects. A number of new collaborations have been established in the Hub’s first year of operation. These projects cross a wide variety of industry sectors subject disciplines, and benefit from the team’s knowledge and expertise in manufacturing metrology.
Recent examples of Innovate UK funded projects include: 3-in-1 X-ray CT
(Lead partner: X-Tek Systems, plus Synopsis, Hieta Technologies, MTC and University of Huddersfield).
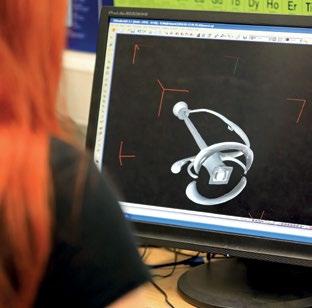
X-ray CT is the only viable method for non-destructive imaging and measurement of metallic products with surfaces that are inaccessible to conventional inspection methods, which is a common feature of AM parts. This project is aiming to develop the world’s first system (hardware and software) to integrate advanced Non-Destructive Testing (NDT), dimensional inspection and high-fidelity surface topography extraction for complete post-build inspection.
Metrology and Digital Manufacturing for Servitisation of Manufacturing Machines
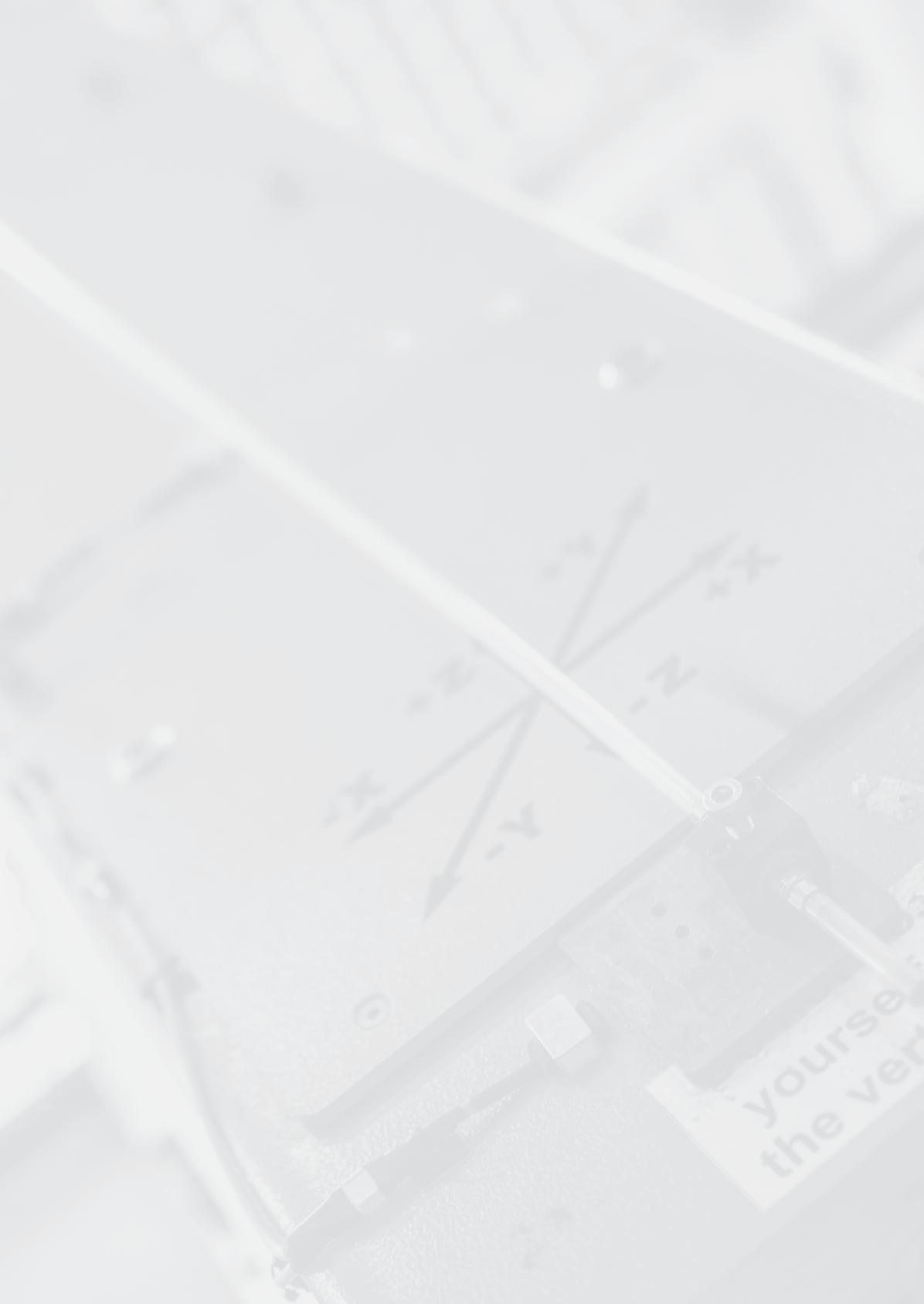
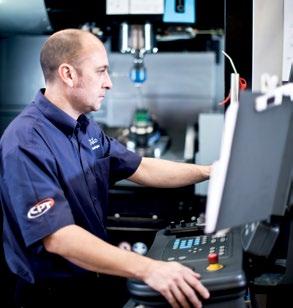
(Lead partner: Machine Tool Technologies, plus Newburgh Precision, AMRC, Cranfield University and the University of Huddersfield).
Servitisation of machine tools is a proposed new business model where a manufacturer purchases productive time available on a machine, rather than the capital asset. This project aims to develop advanced monitoring technology and analytics for both the machine and manufacturing process, with metrology and digital manufacturing being the heart of the solution. Other projects
• New technology to significantly enhance the performance of forensic ballistics systems
(Lead partner: Forensic Pathways Ltd)
• Intelligent (Internet of Things) tool holding for metal cutting machine tools
(Lead partner: Craftsman Tools Ltd)
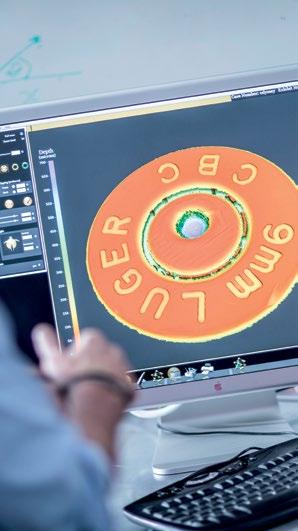